From feedstock receiving and mixing to finished product storage, organics recycling facilities are investing in fully and partially enclosed structures.
Nora Goldstein
BioCycle June 2012, Vol. 53, No. 6, p. 30
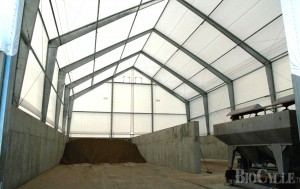
The JC-Biomethane anaerobic digester under construction near Junction City, Oregon is using a fabric structure to house its materials receiving and preprocessing operations. Supplied by Legacy Building Solutions, it incorporates structural steel beams.
lower cost per square foot, minimal foundation requirements, faster installation timelines and improved corrosion control.
The JC-Biomethane (formerly Green Lane Energy) anaerobic digestion project under construction near Junction City, Oregon was thrown a curveball toward the end of 2011 when it learned that preconsumer food waste generated by food processors would no longer be eligible for the Oregon Department of Energy’s Biomass Producer Tax Credit, forcing a change in facility design and construction plans. “Feedstock supply contracts with food processors were no longer viable without the tax credit, as that was the incentive driving producers to work with us,” says Dean Foor, Project Engineer with ECOregon, developers of the JC-Biomethane digester.
The next most available and accessible source of food waste feedstock was the postconsumer stream. With that, however, come contaminants. “Our original plan was to erect a small reception building, but our system design went from handling clean organics such as broccoli and sweet corn cannery waste to a mix of organics,” explains Foor. “The change in feedstocks required a much larger building, storage capacity, odor control and a separator to remove contaminants from the food waste.” Enclosure and odor control weren’t required by regulators, but JC-Biomethane “wants to do everything possible to be a good neighbor,” he adds.
The company opted for a 120-foot by 140-foot polyethylene fabric structure supplied by Legacy Building Solutions that incorporates structural steel beams instead of open web trusses. “The structure is a very compelling compromise between a steel building and a traditional fabric building,” says Foor. “It enables us to mount equipment from the beams, such as our air handling system. If we were only using the building for storage and not for processing inside, a more traditional fabric structure would have been fine.” The structural steel has multiple coating options, including hot dip galvanizing, red oxide primer and powder coat paint.
The building is totally enclosed, with fast-closing fabric doors for trucks to enter and leave. It will be almost 47-feet at its peak, providing adequate clearance for the trucks to tip. “This also gave us flexibility in the type of receiving equipment we could install,” he adds. The air handling system will enable multiple air changes per hour. JC-Biomethane opted for an ozone system manufactured by Oxytec Ag that is designed to destroy volatile organic compounds. It essentially uses an oxidation process where the contaminated air is oxidized with the ozone in a reaction chamber; water steam and CO2 remain after the treatment. “This technology is commonly used at German biogas plants, especially those processing feedstocks from the meat and fishing industries,” says Foor. “The primary air intakes for the odor control system will be over the feedstock receiving and digester feeding areas.”
JC-Biomethane is installing a DODA Bio Separator to remove contaminants from the food waste. In addition to the postconsumer stream, the digester will be processing manure fiber (separated fibers from a dairy farm using a flush system in the barns) and rye grass straw. “The manure fiber will provide good biological stability in the digester, and enable us to have a more aggressive feeding regime with the commercial organics and fats,” he explains. “The fibers provide a lot of surface area for bacteria in the digestion process. On the back end, we have an arrangement for the separated fibers to be taken to the Lane Forest Products composting facility, which is next door to our digester facility.” The 1.55 MW project is using the continuous-stirred reactor wet digester technology supplied by Entec biogas Gmbh. JC-Biomethane anticipates commissioning of the plant will start in late 2012.
Enclosure Within An Enclosure
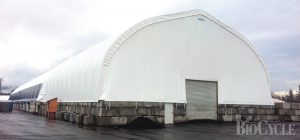
The Chemainus Composting facility on Victoria Island, British Columbia installed a BuildWorks’ MegaDome building to house its GORE Cover composting system. The block walls protect the structure from equipment operating inside.
“As part of our remediation work, we started a pilot program in 2008 using GORE covers to see if the hog fuel component of the processed and screened wood waste would be suitable for composting with the dewatered solids from our treatment plant,” says Dan Lazaro of Coast Environmental. The pilot was a success, and it was decided to start a full-scale operation.
The wood waste processing and composting operations are in an industrial park, with the closest neighbor about 1,000 to 1,300 feet away. Coast Environmental also operates a bulk receiving station for its wastewater company next door, which had been receiving odor complaints from neighbors. “We envisioned growing the composting operation, and wanted to do what would be most acceptable to the community,” recalls Lazaro. Ultimately, that led the company to erect a totally enclosed fabric structure — and compost inside using the GORE Cover System. “To our knowledge, we are the only composting operation in the world, or at least in North America, using this approach. From our vantage point, we knew we needed to have an enclosed operation, and given the materials we were composting, we decided that the GORE system provided superior worker protection, as well as VOC removal. In addition, we only need four air changes per hour, which provides a significant savings in energy usage.”
Coast Environmental already had a 10,000 sq. ft. MegaDome structure for wood waste sorting and screening. To fully enclose the composting operation, it opted to install a 70-foot by 88-foot fabric-covered MegaDome structure with a hot-dip galvanized steel arch-truss frame. Hot-dipping of the prefabricated steel coats it with a thin zinc layer, by passing the metal through a molten bath of zinc at a temperature of around 860°F, according to BuildWorks’ MegaDome literature. This serves to protect the outside, inside and all joints from the effects of corrosion. The single-woven polyethylene fabric membranes are corrosive and rot-resistant, and do not trap moisture.
Installations at composting facilities can be constructed with integrated footings and walls that are 6- to 8-feet in height to protect the building walls from the operation of loaders or turners, as well as serve as push-walls for loading equipment. The walls of the Chemainus facility are constructed of 3 rows of concrete Lock-Blocks to provide a 7.5-foot tall wall. The blocks are interlocking and connected with steel tie-plates to resist uplift forces imposed on it by the structure.
The dewatered cake and wood chips are blended in a Luck Now mixer; a loader is used to build the piles, and to occasionally turn them during the 6-week active composting and curing phases. Coast Environmental is building another MegaDome structure (80-feet wide by 250-feet long) for storage of amendment as well as finished product “as we have a pretty extended rainy season,” says Lazaro. Roughly 8,000 to 10,000 cubic yards/year of compost are produced. Recently, the Cowichan Valley Regional District (local regulatory agency) gave its approval for Chemainus Composting to expand into source separated organics and garden waste. An estimated 2,000 tons/year of food waste will be blended with 2,000 tons/year of garden waste.
Keeping It Covered
Laurelbrook Farm in East Canaan, Connecticut was facing a nutrient management issue almost 10 years ago. The dairy farm, located on 275 acres, was running out of acreage on which to spread manure. In 2006, Laurelbrook Farm began composting with the intent of creating a high quality product that could be sold and resolving the nutrient management challenges. The Connecticut Department of Environmental Protection (DEP) approved composting as the farm’s nutrient management plan, but the operation had to be covered, either by windrow covers or in a building (see “Building A Business With Nutrient Management,” November 2009).
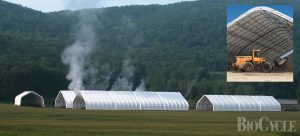
Laurelbrook Farm in East Canaan, Connecticut has four ClearSpan Fabric structures for its dairy manure composting operation and finished product storage. The two buildings used for active composting have an 18-inch wide ridge vent that runs down the center of the roof to let steam escape when windrows are being turned.
The two largest buildings — each 100-feet by 250-feet — house the active composting windrows. The Jacquiers decided not to have electricity, relying instead on the natural light and ventilation (all four buildings are open on the ends). “We selected the Backhus turner because it allows us to have the windrows close to one another in the enclosed space,” he explains. “Floor space is so expensive so we have to maximize what we have. An 18-inch wide ridge vent runs down the center of the roof so that when we turn the windrows, the steam gets out of the buildings as quickly as possible.”
Manure from the milking herd of 930 cows goes through a primary DODA separator that removes a majority of the fibers. The effluent is then run through a centrifuge supplied by Integrity Ag Systems to polish the water further by removing more nutrients and solids. “We are capturing up to 70 percent of the phosphorus from the waste stream, which is our goal,” says Jacquier. “The fibers from both processes — about 100 cubic yards/day — are brought to a 60-foot by 80-foot receiving building, where they are mixed with ‘refusal feed’ cleaned out of the mangers each morning and any waste bedding. We also can add in some sawdust and straw.”
Compost is cured in an 80-foot by 200-foot ClearSpan building, where finished material is also screened and stored. Laurelbrook Farm markets four products — a straight compost, a mulch of blended compost and wood, a topsoil and a garden soil that includes a higher percentage of compost than the topsoil blend. “We make about 14,000 cy/year of compost,” he adds, “and pretty much sell it all.”
Recently, a neighboring farm installed an anaerobic digester. Laurelbrook Farm is taking some separated solids to the digester in order to enhance gas production until off-farm substrates can be sourced.
More Storage Space
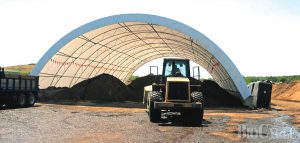
St. Louis Composting’s facility in Belleville, Missouri installed a 70- by 112-foot Accu-Steel building to store its compost-topsoil blend.
The operation has installed a number of smaller buildings (typically 20- by 30-feet) at the Valley Park location to store products such as its rain garden mix, topdressing blends and raised bed mix. But when it came to storing adequate supplies of its blended topsoil and compost, those structures weren’t large enough. Last year, St. Louis Composting installed a 70- by 112-foot Accu-Steel building for its compost-topsoil blend. “We bring in topsoil from the field, process it and then blend it with our compost to give it some organic content,” says Gavlick. “We mix the two materials with a trommel screen and then use a radial stacking conveyor to move it to the top of the stockpile. We haven’t yet filled the structure, although at one point, we probably had 5,000 to 7,000 cy in there.”
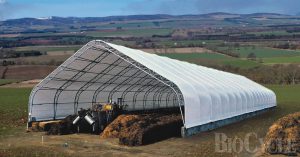
Norseman Structures feature a galvanized steel frame system coated with a corrosion barrier and an impermeable fabric cover.
Another company just entering the composting and anaerobic digestion sectors is Norseman Structures. Its buildings feature a galvanized steel frame system coated with a corrosion barrier and an impermeable fabric cover that is unaffected by ammonia gases. Liners are used to prevent corrosive gases from coming into contact with the trusses.