BioCycle December 2012, Vol. 53, No. 12, p. 14
Cincinnati, Ohio: Composting On Urban Brownfield
In late July, former software entrepreneur Grant Gibson opened a new business in Cincinnati with an unusual distinction: It may be the first, large-scale composting operation located within the boundaries of a major U.S. city. Compost Cincy’s 12-acre operation is located on a 30-acre, former brownfield site in a manufacturing area seven miles north of downtown Cincinnati. Gibson decided to pursue his longtime interest in renewable resources in the fall of 2011, and focused on composting, as it seemed to be the “green” business offering the most opportunity. A friend introduced him to officials from Castellini Companies, one of the largest produce distributors in the United States. It was a timely introduction; Castellini had been disposing of large amounts of waste in landfills, but “was looking to become more sustainable,” Gibson recalls. Castellini became Compost Cincy’s first customer, which provided a source of “significant revenue right out of the gate.”
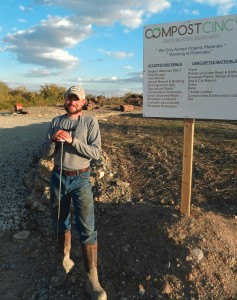
Grant Gibson’s large-scale composting operation is located on a former brownfield site in a manufacturing area seven miles north of downtown Cincinnati.
A roughly 4-acre clay pad provides the base for the composting operation, which consists of six windrows, each roughly 300 feet long. As material is received, it is immediately processed and mixed with the proper amount of bulking agents. “We have the tree service companies dump the chips in a pile near the food waste, which makes it easy for us to mix,” explains Gibson. Depending on air temperatures, and the moisture and oxygen content of the material, it is turned from four to six times during each 75-day cycle, to maintain internal temperatures in the 120° to 160°F range. Equipment includes a rubber tire loader, skid steers, a dump truck and an older Eagle windrow turner that Gibson acquired second-hand.
Most of the finished compost is sold to local soil and mulch outlets and consumers. The compost is also being used in urban agriculture. Gibson gives credit to the city of Cincinnati’s Office of Environmental Quality and Office of Economic Development “who have been big advocates in convincing other departments and the Ohio EPA to endorse what we’re doing.” With the three-employee operation continuing to grow, Gibson would like to be processing a total of 300 to 500 tons of organics daily within the next couple of years. Eventually, he plans to add a complete food depackaging line at the site, to divert as much noncompostable material as possible into the recycling stream.
Sunbury, Pennsylvania: Rolling Out A Supermarket Composting Program
Weis Markets, with 163 stores in the mid-Atlantic region, announced it has signed a contract with American Biosoils & Compost, based in Skippack, Pennsylvania, to expand a composting program to 50 stores next year. This follows a year-long pilot at eight stores, says Patti Olenick, Weis’ sustainability manager. In addition, starting in early 2013, the chain intends to sell at retail the compost it generates in what Olenick describes as a “closed loop” process. Weis stores generate, on average, about 1.5 tons/week of organic waste. The composting program is diverting material from produce, bakery, floral and other departments.
Weis Markets also recently joined the U.S. EPA’s Food Recovery Challenge. Participants are asked to take three steps: Conduct an assessment of their current practices; Set a goal for reducing the amount of food waste being thrown out; and Commit to a more sustainable approach by tracking their efforts across three food diversion actions areas: prevention, donation and composting (see “Sustainable Food Management In Action,” March 2012). If participants don’t have food diversion data, EPA helps them develop measurement and tracking programs. “We like EPA programs because they give us guidance and a standard of measurement so it’s easy to document our efforts,” explains Olenick. “The Food Recovery Challenge is another tool in our toolbox.” Weis plans to use the tools to help it measure the amount of unsold food being donated and otherwise diverted from landfills. The Weis Markets “organics-to composting-to-Weis brand compost” initiative will be featured in an upcoming issue of BioCycle.
Queens, New York: Correction: Composting At St. John’s University
In the November 2012 issue of BioCycle, we reported on a student-built and operated composting system at St. John’s University in the borough of Queens in New York City. The article reported that the university diverts two tons/semester of food and coffee grounds. That quantity is not correct. St. John’s diverts an average of 1,600 lbs/week of kitchen trimmings (fruits, vegetables and some starches) along with 400 lbs/week of coffee grounds — for a total of 1 ton/week, or about 12 tons/semester.
Columbia, Missouri: Ramping Up Food Waste Composting
In 1991, the City of Columbia opened a yard trimmings composting operation on a 15-acre site. In 1999, it began receiving wiener casings from a Kraft Foods facility in Columbia that makes more than one billion hot dogs a year. The plant produces 32 tons/week of wiener casings, which are primarily cellulose. The city combines the casings with the yard trimmings in a 50/50 mixture, turning and watering the windrows periodically. The process takes four to six months to make finished compost. And in early 2011, Columbia obtained approval from the Missouri Department of Natural Resources to compost food waste. It began receiving loads in the fall of 2011.
Columbia offers food waste collection to commercial generators, and is currently servicing three Walmart stores, a Sam’s Club, a Hy-Vee store and a State Farm office. All food waste is accepted for collection as long as it is free of packaging and other contaminants, says Cynthia Mitchell with the city’s solid waste department. Commercial generators subscribe to the service and receive containers owned by the city; food waste is collected weekly in a sealed refuse truck. The city recently applied for a grant to purchase a truck designed for food waste collection.
Jamaica, Vermont: Compost Helps Repair Tropical Storm Irene Damage
A slope stabilization demonstration using a seeded compost blanket, along with compost filter socks for sediment and storm water control, is underway in the town of Jamaica, Vermont. The demonstration site consists of a slide on an embankment approximately 6,000 sq.ft. in size with 1:1 slopes and exposed glacial till soils. The slope damage was a result of Tropical Storm Irene in August 2011. To stabilize the slope, about a 2-inch thick compost blanket was applied using a blower truck. The compost, which was mixed with grass seed as it was applied, was made from horse manure, yard trimmings and wood chips. About 60 cubic yards were used. FEMA had declined to pay for the slope reconstruction. Ultimately, a $7,000 grant from Green Mountain Coffee Roasters covered most of the costs, according to an article in the Brattleboro Reformer.
Okahumpka, Florida: Compost Earns Biobased Product Label
C&C Peat Company, located in Okahumpka, has earned the USDA Certified Biobased Product Label for its Regular AA Compost. The Biobased Product Label verifies that the product’s amount of renewable biobased ingredients meets or exceeds the prescribed USDA standards. Biobased products are goods composed in whole or in significant part of agricultural, forestry or marine materials. Ongoing lab testing and monitoring by the USDA assures the label standards are maintained. Compost, in the Mulch and Compost Materials category, must have a minimum biobased content of 95 percent.
C&C Peat is a family-owned and operated horticultural business established in 1981 to sell potting soil and other soil amendments. “We started producing compost in the early 2000s, and amped up production and quality when we built a new facility in 2007,” says Michael Wolfe, C&C Peat’s Division Manager. “However, we had far more capacity than a market for our compost products, so we sought out government bids such as Department of Transportation projects. We found out very quickly that being certified as biobased opened a lot more doors than not having the certificate, so we went through the process to become certified.”
Several different compost products are produced at C&C Peat’s Okahumpka facility, located 40 miles northwest of Orlando. All of its products meet the Florida Department of Environmental Protection Class AA requirements. “Our most popular product is our “Regular” grade, which is a three-quarter-inch minus material that we produce primarily for our potting mixes, but also as a soil amendment,” says Wolfe. C&C Peat’s Class AA compost is sold in Florida. The chief feedstock is horse bedding from thoroughbred racing stables located in central Florida. Shavings in the bedding are typically pine. The Okahumpka facility has the capacity to compost 150,000 cubic yards/year of bedding. The complete process takes 120 days.
Lexington, Kentucky: Residential Food Waste Pilot
In February 2011, the Lexington-Fayette Urban County Government (LFUCG) began a small residential food waste collection pilot, offering the service to about 400 households in a neighborhood of Lexington. About 40 households signed up for the program. Residents can place all household food waste, including soiled paper, in their yard trimmings carts. The pilot requires that food waste be either bagged or wrapped prior to placement in the carts, which are serviced weekly. Compostable bags and products, including ASTM 6400, ASTM 6868 and ASTM D5338 certified plates, cups and silverware, are allowed. Kitchen food waste containers were made available to participating households. Businesses and several schools located in the targeted neighborhood are eligible for the pilot. LFUCG contracted with Bluegrass PRIDE, a nonprofit organization that provides environmental resources and information to schools, community groups, local governments and citizens in Central Kentucky, to do the outreach and education, including offering training to homeowners and the businesses.
“We did a community waste audit in 2009 and found that 23 percent of what was being landfilled is organic waste,” says Esther Moberly, Recycling Program Specialist in the city’s Division of Waste Management. “That includes grass, leaves, food waste and other organics. About 82,800 tons/year of waste are being landfilled.” The City of Lexington composting facility is only permitted to receive a small amount of food waste, Moberly adds. The site would need to be expanded if the volume of food waste diverted increased. The pilot is continuing, and LFUCG is considering increasing the number of households serviced.
West Chicago, Illinois: Growing With Mulch Production
Kramer Tree Specialists in West Chicago has been offering residential and commercial tree care and maintenance in the Chicago region for more than 35 years. When the state of Illinois passed a landfill ban in 1990, it decided to expand into mulch production. “Most of our original source material was the organic waste we generated from our tree care services,” says Tim Peters, manager of mulch operations. “But now we take in 50 loads a day from a number of streams, including municipal brush and leaf collection, landscaping companies, land clearing projects and even some clean wood waste and pallets.” Kramer Tree produces three mulch products: high-quality special blended mulch, red/brown/black dyed mulch, and leaf mulch.
The leaves are reduced in a tub grinder to produce the leaf mulch, which is used by Kramer’s landscape customers. Light brush and clean demolition debris are also processed through the tub grinder, and allowed to cure briefly after the first reduction. “Upon order, we then regrind that mulch before passing it through our coloring trommel to create our red, brown and black dyed mulch products,” notes Peters. Kramer Tree had been processing the largest wood waste that comes in with the tub grinder. “The big material we get, mostly from land clearing but occasionally from our tree service or from landscapers, can be upwards of 8 to 10 inches in diameter, which can be murder on a high-speed grinder,” he adds. In addition to wear and tear, it burns up large quantities of fuel, upwards of 40 gallons/hour.
The company opted for a Doppstadt DW slow-speed shredder. “The 32 rpm shaft reduces with high-torque rather than high-speed, so the wear and tear, as well as the fuel consumption, drop dramatically,” explains Peters. The shredder has been consuming about 10 gallons/hour of fuel and has a throughput rate of 200 cubic yards/hour. While the chip size is larger than what is produced by a tub grinder, the company views that as an advantage, he adds. “We’re doing two passes anyway, so there’s no reason our first pass needs to produce a finished size equal to our final product. And because the reduction from the DW shredder is larger, the piles don’t get as compact, which means they don’t cook as much and you eliminate the risk of high temperature and combustion.”
New Orleans, Louisiana: Gulf Saver Bags Help Gulf Coast With Compost
Following the BP oil spill almost two years ago, BioCycle reported on a project utilizing canvas Gulf Saver Bags filled with a compost blend, inoculated with hydrocarbon-eating microbes and planted with native marsh grasses to both clean up and rebuild the fragile wetland ecosystem. The initial project was a partnership between the nonprofit Restore the Earth Foundation and the Coalition to Restore Coastal Louisiana (CRLC). Recently, Restore the Earth published a cost-benefit analysis comparing the results of planting Spartina A. (smooth cordgrass), in the Gulf Saver bags versus traditional bare root plug planting. According to that analysis, the bags cost less per acre to deploy ($31,750 versus $37,850), plants demonstrated almost double the survivability rate, and the need to replant was five to ten times less (only required once versus multiple times required of bare root plantings).
Where the Mississippi River meets the Gulf of Mexico, Gulf Saver Bags planted with black mangrove continue to be deployed in hopes of stabilizing barrier islands before they disappear. “It has actually worked out fairly well,” says Shane Granier, chief biologist and project manager with the Louisiana Department of Wildlife and Fisheries. “From an observational standpoint it seems like those plants take off faster than if you were to plant them bare root in native soil.” Because the young plants are susceptible to both cold snaps and the very erosion that mature plants will mitigate, getting a jumpstart in the Gulf Saver Bags can be critical. But the bags are susceptible to wave energy and tidal forces, particularly before the mangrove roots have established themselves through the burlap and into the native soils. “Wooden stakes, working with tidal zones and adjusting the thickness of the burlap material have all shown promise of dealing with this challenge,” notes Granier.