An existing manure digester, co-located with an ethanol plant, is accepting up to 200 tons/day of municipal source separated organics, food processing wastes and biosolids.
Peter Gorrie
BioCycle January 2014
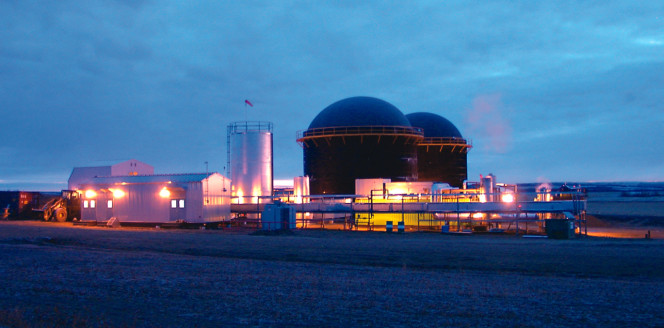
Growing Power Hairy Hill started with an anaerobic digester to process manure from an adjacent cattle feedlot. Today, the facility is receiving 200 tons/day of source separated organics from the Edmonton region. Photos courtesy of Himark BioGas Inc.
Second, it added a plant that will produce 10.5 million gallons of fuel-grade ethanol annually and boost productivity by consuming resources from, and producing them for, other parts of the operation. A grand opening was held at the facility in early December 2013.
Major digester modifications were done as part of an expansion in 2010 and 2011. The modifications were provided by the related technology company, Himark BioGas Inc., to allow the facility to accept up to 200 tons/day of municipal source separated organics, food processing wastes and biosolids from suburban municipalities and towns around Edmonton, the provincial capital of Alberta, 60 miles west. GPHH will also accept source separated organics from the city itself, which is running out of capacity at its own composting facility, says Himark general manager Trevor Nickel. “We hope they will. We could easily go to 330 or even 385 tons/day.” Since the digester’s volume doesn’t change, the amount of manure is reduced as more outside feedstock comes in. But the richer feedstock increases biogas production. GPHH started taking small amounts of SSO in 2011, and has been receiving 200 tons/day since Fall 2013.
Solid wastes are delivered by truck to the facility’s tipping floor. Liquids go into storage tanks. GPHH accepts “nearly everything” from residential organics collections, adds Nickel, noting that the digester has, from the start, been adapted to handle contaminants in the manure from the 35,000-head feedlot, including the sand, dirt and rocks. The unwanted substances sink to the bottom of the digester tank, where they are continuously removed by Himark’s patented Integrated Biomass Utilization System, or IMUS. The same device will remove the inevitable glass, rocks, nonferrous bits of metal and other heavy contaminants from the municipal wastes, improving the digester’s operation and avoiding periodic shutdowns for clean outs. Textiles, some plastics and other light contaminants are removed prior to digestion through coarse grinding and a rotary screen.
“We ran into some challenges with the lighter materials while accepting the smaller amounts of SSO,” explains Nickel. “The IMUS system does a great job with heavy contaminants, so we focussed on a solution that would limit the amount of light contaminants — film plastic and textiles especially. We installed a 4-inch minus shredder from SSI and a rotary star screen. It is very minimal and very easy to maintain equipment. We installed the equipment in the first half of 2013 and have been running full out since early fall. We’ve been very pleased at how the preprocessing functions, and it integrates very well with the IMUS equipment.”
GPHH accepts wastes in plastic bags but insists on compostable types, which shred more readily than noncompostables and, while they don’t break down easily in digestion, do so quickly afterwards. “If we identify a plastic that actually breaks down in anaerobic digestion, we can and will ask all our municipalities we service to switch to that,” Nickel adds. “Plastics are a bit of a nuisance as they don’t provide any biogas. They are relatively harmless, however, so long as they don’t appear in the finished fertilizer product, so we work to avoid that.”
Energy Production
The facility can already produce more than enough biogas to run two GE Jenbacher generators with a total capacity of 2.5 megawatts, which feed into the local electricity grid. The transmission lines can handle only about 80 percent of the maximum output and, for now, it would be too expensive to expand that capacity, Nickel notes. Some of the excess electricity goes to the ethanol plant, where, annually, 110,000 tons of non food-grade, high-starch wheat is processed into renewable fuel that’s sold to oil industry blenders. Excess biogas can also be used in the ethanol plant, replacing fossil-fuel natural gas in the boiler. Residue from the process, known as distillers’ grain, is used as cattle feed. It’s palatable and high in protein and nutrients but without the carbohydrates that cause gas and bloating. “It’s a feel-good story,” Nickel says. “The cattle really appreciate the feed.”
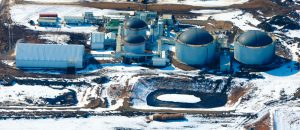
Some excess electricity generated from the biogas is used by the ethanol plant, which processes non food-grade high-starch wheat into renewable fuel sold to oil industry blenders.
The digester produces about 33,000 tons/year of dry and liquid residue. Liquids are applied on a 5,000-acre farm associated with the facility while the solids are sold to farms “a bit further afield” as a soil amendment, Nickel notes. GPHH is seeking approval from the Canadian Food Inspection Agency to market the solid portion, combined with biochar, as a home garden fertilizer.
Himark also recently installed its IMUS technology at the Western Plains Energy facility near Oakley, Kansas, where last spring, North America’s biggest anaerobic digester went into operation beside an existing ethanol plant. The facility services a cattle feedlot next to the ethanol plant and has a total digestion capacity of 17 million gallons. It began operating at the end of 2012. Methane from the digester replaces natural gas to heat the ethanol plant’s boilers.
“We hope to see others like that,” Nickel says.
Peter Gorrie is a Contributing Editor to BioCycle.