Maine wood waste and aggregate recycler has been able to “grow with the flow” — and maintain efficiency in materials management.
Nora Goldstein
BioCycle January 2014, Vol. 55
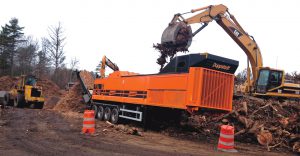
Aggregate Recycling Corporation uses the Doppstadt Kombi with a combined shredder and high speed grinder to process stumps, logs and brush.
Aggregate Recycling Corporation (ARC) in Eliot, Maine got its start in 1987 as a soil recycler, processing petroleum-contaminated soils in accordance with licenses issued by the Maine Department of Environmental Protection since 1989.
In 2002, ARC opened a wood waste and construction materials recycling facility adjacent to its existing operations. Much of the organic material received is comprised of demolition wood, green waste and other wood waste products.
Most recently, ARC opened a tipping floor to accept an even wider range of materials, adding MSW and single stream recyclables to mixed construction and demolition (C&D), concrete, brick and asphalt shingles. “We now run a transfer station to collect incoming waste streams,” explains John Doherty, CEO of ARC. “We manage a single stream recycling process, diverting the MSW to landfills and the recyclables to their various relevant processing facilities. But the organic and aggregate materials we receive get processed on site here.”
ARC has spent years building a broad network of relationships with contractors, waste transporters, landscapers, municipalities and other larger institutions, and has a steady supply of organic materials to process into various end products — raw bark, stumps and tree waste into decorative mulch and erosion control products, and demolition wood and wood pallets sold primarily as boiler fuel chips. All incoming organic materials are sorted and stockpiled according to material type. “Initially, we were putting stumps, logs and brush all in one pile, but it became obvious that they should be sorted,” notes Doherty. “This is especially true with stumps as a lot of topsoil comes in with them.”
With such a wide range of feedstocks, ARC needed a variety of equipment to perform the various reduction and sorting work necessary to add value to these waste materials. For size reduction, ARC purchased a Doppstadt DW 3060 slow-speed shredder, which worked well for processing bulky, contaminated material. A hydraulically-actuated comb enabled passage of tramp and other unshreddable material without causing damage to the machine, notes Doherty. “We also have a Doppstadt AK series high-speed grinder with an upswing hammermill design, which produces a highly consistent finished product that is ideal for mulch, animal bedding or boiler fuel.”
In August, ARC invested in a combined shredder-grinder, which had been sold primarily in Europe. The Doppstadt Kombi has a low-speed shredder on the front end, and a high-speed grinder on the back. “We had been looking at the machine for a while, but we weren’t convinced it had adequate power for the range of materials we process,” explains Doherty. “Then, in 2012, Doppstadt offered a Biopower option that adds more teeth on the cutting surface of the shredder, and a higher horsepower engine. So instead of getting a material that might be 8 to 16-inches or larger after the first pass, the shredder is producing more like 4- to 6-inch minus material before it hits the high speed grinder. The end product is very homogenous. Basically, it replaces two machines for us. We used our low-speed shredder as a trade-in, and still have the high speed grinder until we can better determine if we will need it.”
ARC is also using the new machine for its mobile grinding services. “We have a stump and brush pile processing job, and have been able to produce the end product our customer wants in a single pass,” he adds. “This definitely makes our mobile grinding more efficient, and obviously reduces our need to both maintain multiple machines and saves fuel.” ARC also has a mobile trommel screen equipped with two sizing capabilities for clients making loam products.