Mobile wood grinding fleet, qualification as a preapproved cleanup contractor
and reliable outlets for processed debris are keys to success.
Dan Emerson
BioCycle August 2014
The weeklong winter storm that hit the south and East Coast last February was a record-setting event. The state of South Carolina lost 11 percent of its timber, with North Carolina and some East Coast states sustaining similar levels of tree damage. As the lead contractor in the post-storm cleanup effort, South Carolina-based Southern Disaster Recovery also achieved some impressive stats, processing about 2.5 million cubic yards of green and wood waste, and doing more than $40 million in FEMA (Federal Emergency Management Agency)-approved ice storm cleanup.
Further to the north, Supreme Industries in Connecticut and Savage Forest Enterprise in Maine are also quite busy doing storm cleanup. This article takes a closer look at each company’s storm debris recovery and processing practices.
Southern Disaster Recovery
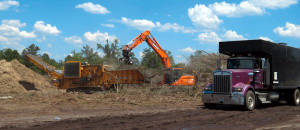
Southern Disaster Recovery offloads storm debris at a Collection Operations and Debris Management site (left) during a 2014 ice storm in South Carolina. Mobile processing equipment includes a CBI horizontal grinder (right). Photo courtesy of SDR
In 2011, entrepreneurs Al McClaren, Kevin Boucher and Mark Ells founded Southern Disaster Recovery (SDR), located in Greer, South Carolina, to specialize in post-storm, tree cleanup work. McClaren had been working for another debris removal company cleaning up after an October ice storm on the East Coast when he met Connecticut-based Supreme Industries owner Kevin Boucher. “I was considering starting my own company, and I knew Kevin had been getting into the debris business,” explains McClaren.
He and Boucher partnered with fellow clean-up contractor Mark Ells, owner of Greenville, South Carolina-based Greenworks Recycling, to form SDR. The company’s size — more than 200 employees and an extensive network of subcontractors — enables it to simultaneously handle multiple storm cleanup projects, according to McClaren.
To set up debris management sites in advance of storm events, SDR works with county or municipal officials to find suitable locations, adds McClaren. If the site will be used to clean up after a hurricane or tornado, the company may install liners to contain any hazardous household waste that might be included in the cleanup.
Local governments’ readiness to deal with storm events varies greatly, he says. When Congress passed the Hurricane Sandy Relief Act, it stipulated ‘extra’ reimbursement to have disaster recovery plans in place. “Although FEMA has directed county governments to ‘precontract’ with qualified cleanup contractors and have debris management plans in place, most of the counties in any state don’t have those,” notes McClaren. “I’ve been meeting with county reps to try to get them to do that.”
In cleaning up after storm events “we only deal with what FEMA will allow,” he continues. That means cleaning up tree and green waste only on public property, as well as material private property owners have “brought to the curb. We don’t deal with telephone poles; the utility companies handle those.”
SDR has been successful in complying with FEMA requirements. “So far, nothing has been rejected (for reimbursement),” explains McClaren. “We pride ourselves on sticking to the letter of the law. Some guys will go on private property and grab a pile of trees to haul off. But federal contractors are not allowed to do private work at the same time as public cleanup projects.”
Supreme Industries
One of the most experienced storm cleanup contractors in the U.S. is Connecticut-based Supreme Industries, one of the three founders of SDR. Kevin Boucher, president of Supreme, started the company about 35 years ago as a residential land-clearing business, and transitioned into right-of-way clearing work for utility companies engaged in infrastructure improvement. Over the past 15 years, Supreme has been involved in large-scale cleanups following hurricanes in Florida, Louisiana and Texas, and helped remove tree debris after ice storms in Connecticut.
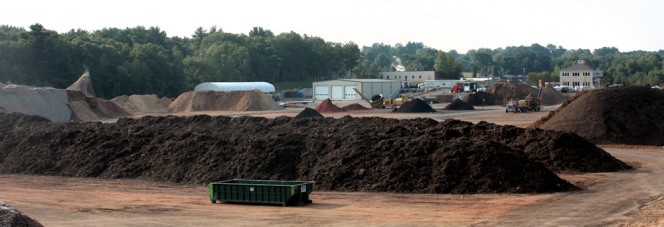
Supreme Industries operates a wood recycling and windrow composting facility at its yard in Southington, Connecticut. Photo courtesy of Supreme Industries
Supreme operates two facilities: its primary base in Harwington, Connecticut, and a second location opened about two years ago in Southington. Depending on the distance and timing of a storm cleanup job, Supreme has a network of subcontractors who will haul its equipment to areas where storm cleanup is taking place. Supreme’s fleet of storm cleanup equipment (all made by CBI) includes three tub grinders, four horizontal grinders and three “whole tree” chippers. “We’ve found horizontal grinders to be the ‘most productive’ gear when Supreme is clearing storm debris,” notes Boucher. The company also has a fleet of bulldozers, pay loaders and excavators.
When processing storm-related debris at a site, Supreme’s workers divide it into piles of brush, “stem wood” and logs. Tree stumps also go in a separate pile, and are broken up to remove dirt. “We grind the three categories of material at different times,” he explains. “The end result is that some of it goes into mulch, some is used for biomass fuel and some is screened and sorted for use in composting. So, we have multiple uses for the product after grinding is completed.”
There are differences in storm cleanup work, depending on whether the damage has been done by high winds versus an ice storm, notes Boucher. “Wind events typically blow things over, so there are more uprooted, whole trees and fewer (separated) tree limbs. Conversely, ice-related storms create an abundance of tree limb debris that we refer to as ‘leaners’ and ‘hangers’ on the project sites.”
The logistics of getting heavy equipment to disaster recovery sites also involves planning routes based on compliance with local roadway weight restrictions. In states such as Ohio, Maine and South Carolina, where Supreme does a lot of work year-round, “we have a pretty good system for mobilizing equipment,” he adds. “When we anticipate a storm hitting, we check with state Departments of Transportation (DOT) agencies and they tell us what routes we can take, based on weight restrictions and width of vehicles and equipment. We can’t take a heavy, wide piece of equipment and drive to South Carolina without knowing from the DOT that the routes we are going to take will accept the width and weight of the equipment we’re moving.” After a disaster, Supreme brings its smaller equipment in first to make sure roads are accessible, and heavier gear follows a few days later. The vehicles at storm recovery sites typically have window stickers designating them as FEMA disaster recovery contractors.
Boucher notes there are a number of smaller contractors around the U.S. who “chase storms,” while companies like Supreme have prepositioned subcontractors and prior relationships with local governments and therefore are “typically on the top of the list” when it comes time to hire. After major storms, “we hire a lot of subcontractors, so its typically a 24-7 operation for the first couple of weeks, getting everything organized and set up and pointed in the right direction,” he says.
How does Supreme typically “vet” those seeking to be hired as subcontractors? “There will typically be a staging yard set up by the local community or state, and we set up a small, emergency trailer so people can come in and introduce themselves,” explains Boucher. “We make sure their insurance is up to date and they have the proper equipment. After you’ve been in business for a few years, you start seeing the same people (at storm sites) and know who performs best.”
Supreme seeks local markets for processed wood and green waste. The company has a “network” of 25 walking floor tractor-trailers to transport ground material to buyers, typically within a 50 to 100-mile radius of where it was created. “It’s the most economical way to move material,” says Boucher.
For disaster recovery contractors, dealing with the FEMA bureaucracy can be challenging. After 15 years of doing storm cleanup work, “we’ve learned you have to be really ‘good’ with FEMA paperwork to get reimbursed,” he adds.
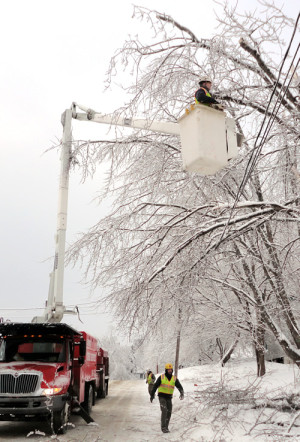
After storms, Savage Forest Enterprise helps reopen tree-blocked roads and remove limbs that might impair utility lines.
Photo courtesy of Savage Forest Enterprise
Savage Forest Enterprise
Smaller contractors, like Mount Desert Island, Maine-based Savage Forest Enterprise, also have a role to play in storm debris cleanup. The tree-care firm provides services to the Acadia and Mount Desert Island areas, and also acts as a cleanup contractor after storms. The nine-employee firm processes over 7,000 cubic yards/year of wood and green waste at its 10-acre site, according to owner Tom Savage.
Trees in the area are damaged both by summer wind and thunderstorms and by winter ice storms. Surprisingly, much of the damage caused by ice coating trees doesn’t show up until the following summer, when storm winds hit, explains Savage. Many trees survive winter ice storms and don’t show stress until they take on their spring “leaf load” and are hit by summer storms. “We have a lot of deciduous trees, so there is a lot of splitting and cracking,” he says.
After storms, Savage Forest Enterprise does a lot of work to help reopen tree-blocked roads and remove limbs that might impair utility lines. The company chips the wood waste on-site; about two-thirds of the processed debris is given away to local residents and governments, as wood chips and mulch. The mobile equipment used includes a Vermeer HG200 horizontal grinder and a Vermeer BC1500 brush chipper.
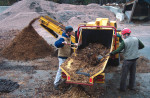
Savage Forest Enterprise uses a Vermeer HG200 horizontal grinder as well as a brush chipper. Photo courtesy of Savage Forest Enterprise
After material is processed it is moved to a temporary staging area to be held until being given away or sold for use as biomass in energy plants around the state. However, using real estate just to hold wood “can sometimes not be profitable,” explains Savage, and the fact that when wood waste is stored outdoors, “the quality can go down.” The biggest user of the biomass is the Verso Paper Corp. mill in Bucksport, Maine. Selling storm biomass is “not necessarily profitable in itself,” Savage notes. “It has to be a submarket for our primary service, which is the removal of storm debris.”
Dan Emerson is a Contributing Editor to BioCycle.