Companies, often in tandem with universities, are developing phosphorus and ammonia recovery systems that can be paired with anaerobic digesters.
Dan Emerson
BioCycle September 2015
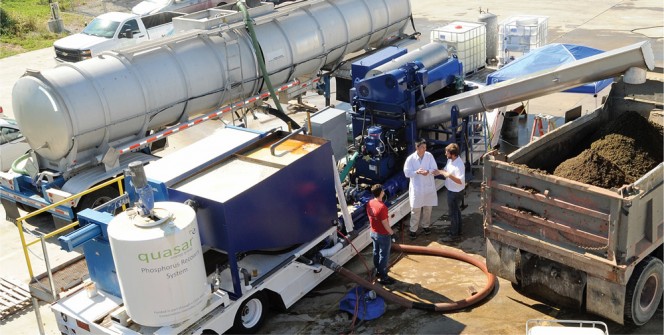
The quasar energy group’s Phosphorus Recovery System was evaluated by The Ohio State University and found to recover phosphorus (P) at an efficiency rate of about 99.57 percent. Photo courtesy of quasar energy group
Brownhaven Farm in New Bremen, Ohio, is located in the Grand Lake St. Mary’s watershed, where phosphorus is the primary nutrient contributing to toxic, blue-green algal blooms in Lake Erie, Grand Lake and other Ohio waters. Grand Lake has been subject to a state water contamination advisory every year since 2009, due to unsafe levels of algae toxins. The Brownhaven Farm dairy has 265 milking cows that produce eight tons/day of manure, according to owner Lou Brown.
In late July, Cleveland, Ohio-based quasar energy group successfully demonstrated a new system at the Brownhaven Farm that removes phosphorus from agricultural waste. In the on-farm demonstration, quasar’s Phosphorus Recovery System (PRS) recovered phosphorus from manure at an efficiency rate of approximately 99.57 percent, according to The Ohio State University (OSU) professor Dr. Yebo Li. The system separated the Brownhaven Dairy farm’s manure into a phosphorus-rich solid and water containing less than 0.5 mg/L (milligram/liter). The solids can be shipped off the farm for use on phosphorus-deficient farmland, and the liquid, which contains nitrogen and potassium, can be used to irrigate crops or returned to the manure lagoon.
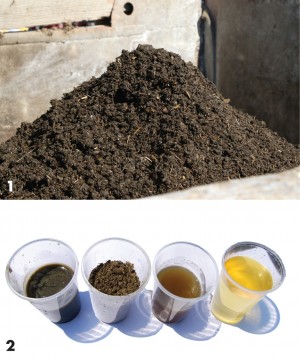
Separated solids with high P levels (1). Samples (2) after each stage of the P recovery process (from left to right): slurry; solids after dewatering; liquids after dewatering; and final low P liquid product. Photos courtesy of quasar energy group
The PRS operates as follows: Manure is pumped into the system, and the solids are separated using a centrifuge. The separated solids (25% solids) contain about 90 to 95 percent of the manure phosphorus, according to quasar. These are conveyed to a storage unit. Liquids drain into a collection tank directly below the centrifuge. Liquid hydrated lime (Ca(OH)2) is pumped directly into the tank and mixed with the liquids. This mixture is brought to a target pH of at least 10.5 to facilitate coagulation and precipitation of remaining solids not captured by the solid separator. Another pump then sends this material to a lime-mixing tank where it is further mixed to achieve a uniform pH. The material overflows into a lime-settling tank; precipitated solids settle to the bottom of the tank and clarified liquids exit through a top outlet. Settled solids and liquids are pumped out of the bottom of the lime settling tank and into a filter. Filtered liquid has a phosphorus content of < 1 mg/L and can be used for irrigation. Separated lime solids (lime cake) are blended with collected solids from the centrifuge and can be transported out of the distressed watershed.
The PRS is designed to work independently or in tandem with an anaerobic digester. Quasar developed the technology with a U.S. Department of Agriculture (USDA) Natural Resources Conservation Services (NRCS) Conservation Innovation Grant, which provided $1 million to help fund the demonstration, according to quasar President Mel Kurtz. (Quasar matched the NRCS grant with $1 million.) When farmers use the new system to remove phosphorus from agricultural waste to address watershed runoff, “phosphorus, which has been the dominant concern in the marketplace, is no longer a detriment to the agricultural community,” Kurtz points out.
Liquid separated from the manure can be used in the place of chemical fertilizer, since it has the necessary levels of potassium and nitrogen. “It’s an ideal solution for farms where years of over application of phosphorus has led to a surplus in the soil,” he adds. The technology also can be employed by municipal wastewater treatment plants, which also are a major contributor of phosphorus into the watershed, Kurtz continues. He cites the most recent U.S. Geological Survey finding that, in the Lake Erie watershed, agricultural runoff was the source of 37 percent of phosphorus in the watershed, while wastewater plants added 46 percent.
While the PRS is commercially available, quasar is working on reducing its cost — currently about $600,000 — and improving performance, according to quasar. The fact that the unit is mobile — it’s mounted on a trailer — makes it feasible for multiple farms to utilize one unit.
Kurtz expects that the next generation of the quasar system will be able to process 150 to 300 gallons/minute. Most dairy farms in Brownhaven’s size range have lagoons holding 800,000 to 3 million gallons of manure. Public concern about the problem of agricultural runoff polluting the watershed has been on the increase in recent years, Kurtz points out: “For the first time, farms have been shut down by judges for nutrient mismanagement.”
Brownhaven Farm and a group of neighboring farmers are considering the economic feasibility of buying a quasar system on a cooperative basis. The group is seeking input from OSU’s agricultural scientists to find out the value of the phosphorus by-product generated by processing the manure, the economics of transporting it to potential users, and related issues, according to Brown.
Ammonia And Phosphorus Capture
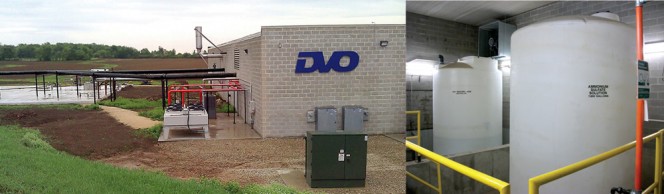
Dallman’s East River Dairy has an anaerobic digester (left) and nutrient recovery system supplied by DVO, Inc. Sulfuric acid (contained in vessel on right) is used to create ammonia sulfate, which is used to make liquid ammonium sulfate fertilizer. Photos courtesy of DVO, Inc.
At Dallmann’s East River Dairy in Brillion, Wisconsin, a patented nutrient recovery system codeveloped by Chilton, Wisconsin-based DVO, Inc., and Washington State University (WSU), is being used to capture most of the ammonia nitrogen present in the farm waste, greatly reduce ammonia emissions from lagoon storage, and eliminate harmful pathogens such as e-coli. The Ammonia Recovery (AR) system works in tandem with the farm’s anaerobic digester, DVO’s Two-Stage Mixed Plug Flow™ system, which began operating in early 2013. DVO (which holds the patent) and WSU developed the system specifically to remove nitrogen from manure. Digestate is first processed nonchemically by “conditioning” it to release the ammonia, which is then captured using a custom ammonia stripper — turning it into a stable commercial fertilizer.
Farms can either sell this fertilizer or use it themselves to offset commercial nitrogen purchases. The AR step removes up to 80 percent of the nitrogen in the form of ammonia, according to Doug VanOrnum, DVO’s VP of Technology and Strategy. At the Dallmann dairy, manure produced by the dairy herd is scraped from four barns into a flume that transfers the manure to a reception pit, where it is agitated prior to entering the anaerobic digester. After processing by the digester, the slurry’s ammonia content is captured and converted in the stripping tower to ammonium sulfate (a form of nitrogen). The Dallmans sell the ammonia sulfate fertilizer in liquid form to a local cooperative. It can also be added back into the digestate slurry for crop application on-site.
The AR system also can eliminate most ammonia emissions from farmers’ storage lagoons. “This is the first practical technology solution to do that,” notes VanOrnum.
Regarding return on investment, DVO estimates the payback period typically ranges from three to seven years. “It is either revenue neutral or revenue positive, especially when the waste being treated has a high ammonia content,” he adds. The system installed at the Dallman farm was set up as a research and development site for DVO. AR has also been installed at five other farms in the U.S. — two at dairies in Washington State and one in Wisconsin, one on a poultry farm in Ohio, and another at Bio Town Ag in Reynolds, Indiana. Bio Town Ag’s anaerobic digester handles about 80 percent off-site feedstocks, in addition to manure.
DVO also recently introduced a phosphorus recovery system that is paired with its anaerobic digester. The unit — which captures 75 to 95 percent of the phosphorus in the solids fraction — was successfully commissioned at a large dairy farm in the Pacific Northwest, as well as two other locations. The system employs an organic polymer to capture the “P-rich” solids, which can be dried to a high level and sold off-site for its fertilizer value. “Depending on the solids concentration in the digestate, the recovery cost is only one- to two–tenths of a cent per gallon treated,” says VanOrnum.
Dan Emerson is a Contributing Editor to BioCycle.