Best management practices adopted by wastewater treatment plant anaerobic digester operators are applicable to farm, industrial and source separated organics codigestion facilities.
Timothy G. Shea and Todd O. Williams
BioCycle December 2012, Vol. 53, No. 12, p. 50
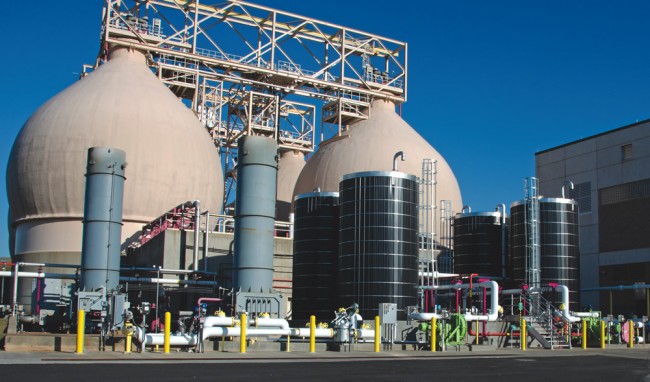
A treatment plant built receiving tanks for each source of industrial wastes (above). Generators rent the tanks and are responsible for delivering substrates on a timely basis to allow continuous feeding.
The first principles of anaerobic digestion are: 1) Know what is being added to the digester at all times; 2) Treat the addition of every new substrate with the same caution used in digester start-up operations; and 3) Have a contingency plan in place in case of problems. These principles, developed in municipal WWTP practice, are applicable to all digesters — with one major exception. Municipal sludges are relatively consistent from one facility to the next, whereas the newer applications involve feedstocks that are often quite variable. In either setting, digester start-ups are not something to be taken lightly and no assumptions should be made that one organic waste will behave the same as the next one.
The start-up approach should first consider the following rules for waste characterization:
• Each waste should be characterized for its physical, chemical and biological attributes, its availability (time of day and quantity) at the door of the treatment facility, and how it has to be stored at the treatment site for delivery at a relatively constant rate to the anaerobic digester(s).
• The waste characterization should be designed with representative samples to avoid receiving a material that will exert a toxic or inhibitory effect on the digestion process, result in chronic or acute foam formation, cause unintentional struvite or vivianite precipitation, impart ammonia toxicity, or result in an interrupted rather than continuous or semicontinuous feed rate.
Feedstock testing depends on the origin of the wastes. Many sources do not wish to reveal the content, however the integrity of a treatment process may be at stake so the digester owner interested in handling the material has to establish a screening analysis that is consistent with the waste source to protect its assets. In addition to the standard suite of tests for oil and grease and nutrient and micronutrient contents, a biochemical methane potential (BMP) test should be conducted. The initial testing may be costly but a sick digester is far more costly to remediate. The toxicity can take a number of forms, but usually will result in inhibition of complete digestion, leaving residual feedstock in the digested biosolids (in the case of WWTP codigestion). One example is grease in the digested sludge, observed in a large municipal plant where the problem turned out to be inadequate nutrient content for the carbon loading.
The bottom line is that it is better to not accept a problematic waste stream than to have a stuck or damaged digester. Waste characterization can provide the safety net that is needed.
Supporting Infrastructure Needs
The authors suggest that the challenges associated with codigestion projects can be managed if best management practices (BMPs) followed for municipal digester start-up are used with the new feedstocks as well. This is because the start-up protocols are safety-driven, proven and thorough, especially when conducted in accordance with industry guidelines such as found in the Manual of Practice No. 16 (1987) of the Water Pollution Control Federation (now the Water Environment Federation). Following the BMPs will identify and eliminate these types of conditions:
• Malfunctioning digester pumping, heating, mixing, gas pressure relief and emergency overflow systems.
• Loading the digesters at organic loading rates exceeding the capacity of the seed sludge inventory to process new organic substrates. Seed sludge is the initial charge of biologically active material needed to start active fermentation in a digester. To avoid overloading the seed sludge, the operator must know the inventory of seed sludge at all times, and pace loading of new substrates to the inventory in hand.
• Inoperative pressure relief valves, emergency overflow conduits and other safety equipment.
• Lack of a contingency plan to allow diversion of feed from the digester in event of a malfunction.
Operators need to ensure that sampling and monitoring programs are in place to verify conditions, starting with the temperature, pH and the concentrations of total and volatile solids, alkalinity and volatile fatty acids in the digester.
An additional need for today’s codigestion applications is for facilities to receive, store, blend, preheat and transfer the blended feed stream to the digester. One approach is to provide receiving tanks for each source of industrial wastes. In this manner, each industry can rent its receiving facility and meet its responsibility to deliver the waste on a timely basis to allow continuous feeding.
To also maintain optimum digester operations, facilities need to ensure there is an adequate gas and condensate collection system, biogas utilization capacity and emergency outlet and pressure relief systems that can function with low density sludges. A low density sludge has a build-up of gas bubbles in the liquid that reduces the density of the liquid to less than the 1.0 to 1.05 gram/cc density of the digesting sludge. In some cases the density can be as low as 0.5 gram/cc. A sludge at this density requires twice the height of a liquid having a density of 1 gram/cc to activate a pressure relief valve. If that height cannot be developed with the low density liquid, this safety device will not work. The liquid in a foaming digester can easily be as low as 0.5 gram/cc.
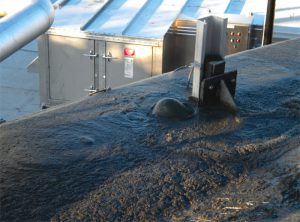
Foam is a frothy digesting sludge in which gas hold-up occurs, causing volume expansion. A rapid rise in foam formation can result in ejection of foam from the digester (above).
Foam Formation And Volume Expansion
Foam, as differentiated from scum, is a frothy digesting sludge in which gas hold-up occurs, causing volume expansion. The density of sludge varies with its dissolved gas and bubble content. A feed sludge containing 5 percent total solids will have a density of up to 1.05 grams/cc, but a frothy sludge could have a specific gravity as low as 0.5 gram/cc. Foam generation results in an expansion in volume that can occur gradually or rapidly, depending on the cause. Examples of factors that can cause foam formation include the following:
• Decrease in gas pressure: A lowering of the gas pressure in the plenum above the digesting sludge will reduce the amount of gas that can be dissolved in the sludge, increasing the rate of bubble formation and release. There is no optimum pressure or range; instead, it is a change in pressure that is important. For example, there is a sudden release of gas from a bottle of champagne when it is opened, as the pressure in the bottle decreases to equilibrium with the atmosphere. That change in a digester can create a large volume of foam.
• Feeding with the temperature below the mesophilic range: The biological processes for conversion of volatile solids to VFAs, and VFAs to methane (CH4) and carbon dioxide (CO2), are temperature dependent. When a digester is fed sludge while operating at less than the mesophilic temperature range (94° to 980F), assimilation of the biodegradable matter in that sludge is slowed, allowing products of partial decomposition to accumulate. However as the temperature rises to the level of optimal activity, the production of gas is accelerated. The holdup of that gas in the sludge reduces its density, causing the formation of foam because of the rapid release of the gas.
• Intermittent feeding and mixing: Rapid changes also can result in foam formation because of the differences in concentration, density and/or temperature of the feed. As a result digester feeding cycles as frequently as hourly or 30 minutes with continuous mixing are now used commonly.
• Feeding FOG: A continuous feed strategy becomes even more important when substrates such as fats, oil and grease (FOG) wastes are added to a sludge digester because these materials are assimilated rapidly with the attendant rapid formation of digester gas.
• Excessive mixing at a high turnover rate: This practice can also result in foam formation, especially with the pumped hydraulic jet mixing systems that are used in the new digesters. An excessive mixing energy input can be alleviated with variable frequency drives to slow the rate of mixing energy input.
Any one or combination of these events can result in the rapid formation of foam. Digester foaming at moderate levels is common, is often chronic or sustained in nature, and is usually accommodated by such practices as the installation of foam suppression sprays, surface mixing systems, surface foam-breaking systems, pressure relief valves and overflow outlets that allow removal of liquid from the surface rather than at the depth. Provision of a scum nozzle and a gasholder cover system that under normal conditions can handle transient foam production events with the storage capacity is also useful.
Conversely, a rapid-rise foam event is not considered normal foaming. It is a transient event with a rapid rate of increase in the volume of the digesting sludge followed by a longer period of decreasing volume (Figure 1). The rapid expansion will result in ejection of a frothy sludge from the digester by whatever portal is at hand, until the excess volume is expelled. The rapid expansion usually results in the immediate shutdown of the feed to the problem digester, and the eventual abatement of the volume expansion. With a rapid shutdown of feed, the overflow will typically cease within a day.
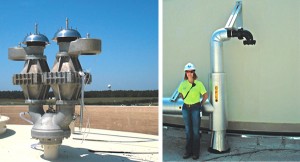
Safeguards used to minimize the effects of rapid rise foam formation include pressure relief valves (left) and emergency outlets (right).
Under extreme conditions the rate of formation of foam can result in an outflow volumetric flow rate as much as 10 times greater than the inflow volumetric flow rate. Once the event is recognized and the feed shut down, the foam formation will gradually abate. In one such event at a municipal sludge digester undergoing start-up, foam production could not be measured because it was not confined to a pipe or an easily defined vessel, but the impact of gas holdup was obvious as the frothy digesting sludge erupted past the gasholder cover and flowed over the wall of the digester. With the digester feed shutoff, the flow of frothy sludge past the cover soon relieved the pressure in the digester, reducing the gas holdup and density of the remaining digesting sludge and abating the foaming event. The records show that the entire process took place within the span of a day, including the period of rapid rise in volume of digesting sludge followed by the longer period of declining sludge volume.
Safeguards used to minimize the effects of rapid rise foam formation include pressure relief valves, emergency overflows, foam suppression sprays, increased head space in the gas plenum and rapid transfer piping to lower the liquid level. Note that some of the safeguards above are nonfunctional at reduced liquid density.
In summary, operation of a digester with multiple substrates presents some unique challenges. It is important to recognize these challenges from the onset. The foremost of these is the potential for foam formation. Foam management begins with the start-up procedure used as each new substrate is added. Start-up is a time of transition, and transitions are the most critical periods for foam formation that can generate gas holdup.
Timothy Shea, Ph.D. PE, BCEE is a Technology Fellow with CH2MHILL in Chantilly, Virginia. Todd Williams, PE, BCEE is Residuals Resource Recovery Technology Leader with CH2MHILL in Richmond, Virginia.
Reference
“Anaerobic Sludge Digestion”. Manual of Practice No. 16. Water Pollution Control Federation. Second Edition. 1987.