An anaerobic digestion facility that expects to be processing 100 tons/day of source separated organics by 2014 is already fueling 10 trucks daily with renewable CNG.
Nora Goldstein
BioCycle July 2013, Vol. 54, No. 7, p. 56
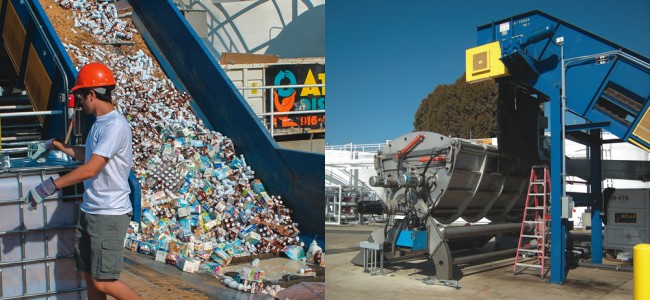
The DODA depackaging/ preprocessing system at the Sacramento BioDigester is sized for a 100 tons/day. Loads include cans of off-spec food that are tipped onto the conveyor belt of the system.
A pilot-scale APS digester was constructed at UC Davis in 2002 to determine the optimal parameters for the engineering and operation of a full-scale system to process a wide range of feedstocks, including municipal and commercial organics (including yard trimmings), food processing residuals, and agricultural waste streams such as manure and animal renderings. CleanWorld, founded in 2009 as Clean World Partners, acquired the license for the technology (Zhang is the company’s Chief Technology Advisor). In January 2011, the company was acquired by Synergex Ventures.
The first facility built under the CleanWorld banner — commissioned in March 2012 — was a commercial-scale digester installed at American River Packaging (ARP) in Sacramento. The ARP BioDigester is designed to process up to 9.5 tons/day of commercial food processing and retail food waste along with 0.5 tons of unrecyclable corrugated cardboard. About 8 tons/day of feedstocks are being processed. There are four tanks, one of which serves as storage for either effluent or excess incoming feedstocks. Two Capstone microturbines produce about 110 kW when the digester is running at capacity. CleanWorld has a net metering agreement with ARP, and supplies about one-third of the electricity used by the company. The other tanks are used for each of the three phases of the APS digester system: hydrolysis, methanogenisis and polishing.
“The hydrolysis phase breaks down the organic waste into basic nutrient components,” explains Kathryn Oliver, an environmental engineer with CleanWorld. “It can receive raw solids as high as 50 percent, but the average solids content of the incoming feedstock is about 25 percent. Retention time in the three phases — from molecule in to molecule out — is less than 30 days.” The system uses a combination of mechanical and hydraulic mixing to agitate the tanks. “Agitation is one of our biggest challenges, but also one of our greatest strengths,” she adds. “Because of the high solids content of the feedstocks, agitation can be difficult, but we’ve gained a lot of experience with hydraulic and mechanical mixing that enables the hydrolysis tank to operate at 15 percent solids.” The APS digester technology runs at thermophillic temperatures (131°F). “Dr. Zhang found that thermophillic temperatures are most efficient to digest food waste,” notes Oliver. “The thermophillic bacteria are more efficient at converting organics into methane.”
Scaling Up
In February 2011, Sacramento County issued a Request for Proposals to utilize its South Area Transfer Station (SATS), which was no longer in service. CleanWorld, along with Atlas Disposal, a Sacramento-based waste hauler, submitted a proposal and were selected to utilize the vacant site under a 20-year lease from the county. It provided an ideal location for a full-scale commercial organics anaerobic digester, and Atlas sited a fueling station immediately adjacent to the digester to utilize the renewable compressed natural gas (CNG) for its fleet. CleanWorld broke ground at the site in June 2012, first installing enough capacity to process 25 tons/day of source separated organics.
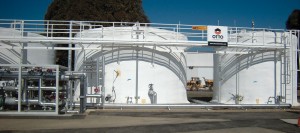
Components for the Sacramento BioDigester, including pumps, valves, liquid transfer piping, heating elements and controls, were constructed on skids and brought to the site to be connected.
Three tanks, with a total of 300,000 gallons of capacity, were constructed. A DODA depackaging/preprocessing unit was installed adjacent to the tipping area. The DODA is sized to process 100 tons/day of incoming feedstock. Packaged and unpackaged food waste is collected by local haulers from dining halls at UC Davis, grocery stores, correctional facilities and food processors. Loads have included cans of off-spec soup that are tipped onto the conveyor belt of the preprocessing system. Cans are recovered for recycling. “The landfill charges premiums to take this type of waste, so our tipping fee is very competitive,” explains Shawn Garvey, CleanWorld’s director of communications. Yard trimmings are also accepted. “Anything green grown in the last 90 days is great feedstock,” he adds. “This includes leaves and grass. We avoid branches and brush.”
All components needed for the Sacramento BioDigester were constructed on skids in California and brought to the site to be connected. Included are pumps, valves, liquid transfer piping, heating elements and controls. Digested effluent is available to use in the preprocessing system, if necessary, to achieve a solids content that is pumpable to move the incoming feedstock into the first phase of hydrolysis. The expansion includes two more tanks and one more skid to increase the capacity fourfold. “Eventually, the three tanks now in use will provide the first phase of digestion, and the two new tanks will be the second and third phases,” notes Oliver. “We will ramp up our daily throughput gradually until we reach our design capacity of 100 tons/day.
A 190 kW gas engine, supplied by 2G Cenergy, began operating in May. The engine package includes the conditioning equipment and is housed in a container. Electricity is used to power digester operations as well as the fueling station via a net metering agreement with the Sacramento Municipal Utilities District (SMUD). Heat from the engine is captured to help maintain thermophillic conditions in the digester tanks. CleanWorld opted for a gas engine instead of microturbines at this facility because of the engine efficiency. “We are getting about 28 percent electricity generation efficiency with the units at our ARP BioDigester, and about 33 percent on our new engine,” says Oliver. “However, microturbines are very easy to permit in California. Manufacturers like Capstone have units available that are certified by the California Air Resources Board (CARB) to meet air quality rules, and the interconnection is very simple. We only had to file a couple forms with SMUD to get interconnected. For the engine at the Sacramento BioDigester, it was more complicated to comply with the air quality rules for engine emissions, and more difficult to get the engine interconnected.”
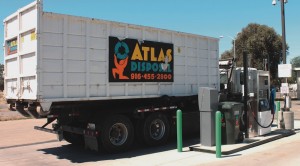
Atlas Disposal installed a BioCNG fueling station that uses biogas from the adjacent CleanWorld digester.
CleanWorld and Atlas Disposal have received a significant amount of public funding for their projects, including a $6 million grant from the California Energy Commission, $2 million in loans from CalRecycle’s Recycling Market Development Zone (RMDZ) program, and exemptions on state sales tax. Atlas Disposal received a $300,000 CEC grant to support construction of the fueling station. The digester project also will qualify for CARB’s Low Carbon Fuel Standard credit trading program, as well as other renewable fuel incentives.
The final phase of the CleanWorld “package” is the back-end of its digester system — the effluent liquids and solids that can be utilized in agriculture and other markets. CleanWorld is building a Fertilizer Production System that separates and dewaters digestate material, and an in-vessel system for the solids. “Digestate is an exceptional base for all-natural fertilizers and soil amendments,” says Garvey. “We are currently taking the effluent from the Sacramento BioDigester to a fertilizer production facility we have at UC Davis that is producing several agricultural products from the effluent. This production facility will be eventually relocated at our Sacramento site.”
Recently, CleanWorld broke ground on construction of the UC Davis Renewable Energy Anaerobic Digestion (READ) facility located at the university’s closed landfill. It is designed to process 20,000 tons/year of source separated organics from the UC Davis campus as well as other area generators. An 800 kW microturbine package will be powered by gas from both the closed landfill and the new digester and a 125 kW organic rankine cycle (ORC) generator will produce additional electricity from the waste heat not needed to maintain the digester temperature.