To mitigate exposure, composting facility operators are modifying feedstock recipes and increasing use of plant bioassays of finished compost. Part II
Craig Coker
BioCycle August 2013, Vol. 54, No. 8, p. 21
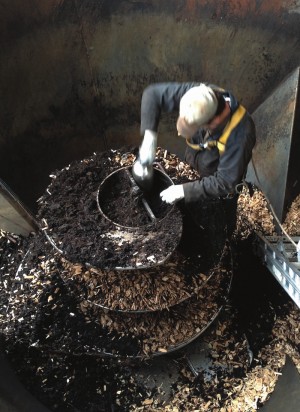
ing of its mixer, a Green Mountain Compost operator had to remove compost affected by a persistent herbicide.
Persistent herbicides have been a problem for composting facilities in several countries since 2000, when yard trimmings compost produced by the City of Spokane, Washington was found to be contaminated with clopyralid. Compost contamination problems have cropped up in 13 states since 2000, most recently in Vermont and Kentucky, as well as in the United Kingdom and New Zealand.
The four main persistent herbicides of concern are clopyralid (sold as Confront, Stinger, and other brands), picloram (sold as Tordon or Grazon), aminopyralid (sold as Milestone, ForeFront, and other brands) and aminocyclopyrachlor (sold as Imprelis, Streamline, and other brand names). These herbicides are designed to be persistent and systemic in their action against broadleaf weeds. They are registered for use on right-of-ways (including roadsides, electric utility lines, railroads, etc.), industrial sites, natural areas, and pastures and grazed areas around these sites. They can end up in composting facilities that take in grass clippings, hay, straw and manures from herbivorous animals that have grazed in pastures or eaten hay or grains containing persistent herbicides. These herbicides are known to survive the composting process and end up in the final product, where they can exert phytotoxic effects on plants in concentrations as low as 1 part per billion (the equivalent of 1 inch in 15,782.8 miles) for aminopyralid and 10 parts per billion (ppb) for clopyralid.
Unlike shorter-lived herbicides such as glyphosphate (sold under several brand names, most notably, Round-Up), persistent herbicides are persistent in soils at very low levels for a very long time. The U.S. EPA’s Office of Pesticide Programs found that one persistent herbicide, aminopyralid, applied to soil at a concentration of 5,240 ppb, photodegraded with a half-life of 72.2 days on silt loam soil maintained at 25°C and irradiated with light to simulate 28 days of summer sunlight at a latitude of 40°N (EPA, 2005). Under those conditions, it would take over 866 days (over 2 years, 4 months) to photodegrade in soil below the phytotoxic threshold of 1 ppb. Degradation in soils by microbial metabolism was found to be much slower, with half-lives of as much as 533.2 days. What data does exist show wide variability in product half-lives in soils.
It has been widely believed that most nonpersistent herbicides and pesticides are degraded by the aerobic high-temperature environment of a well-run composting facility. Persistent herbicides, however, have been shown to be resistant to composting, but very little is understood about the mechanics or the extent of degradation in a composting pile. In a recent study, Ohio State University found that 42 to 53 percent of aminocyclopyrachlor and 30 percent of the clopyralid were still present after 178 days of composting, and that concentrations of the persistent herbicides in the finished compost were at levels that would require dilution of the compost at a 50:1 level to prevent growth effects (Michel, 2012).
Composting facilities that take in food scraps are not immune to the potential problems of persistent herbicides. These herbicides have been found in food scraps and in 2012, EPA established allowable tolerance levels for clopyralid in foods at 50 ppb in apples, 5,000 ppb in Brassica plants (bok choy, broccoli, brussel sprouts, cabbage, etc.), and 3,000 ppb in rapeseed and Teff cereal grains (EPA, 2012).
Managing Risk Of Exposure
Despite publication of a position paper by the US Composting Council that calls for a ban on these herbicides from the market to limit potential damage to composting facilities (USCC, 2013), the reality is that this class of herbicides will continue to remain on the market (although use of some, such as aminopyralid, may be restricted). Therefore, composting facilities accepting feedstocks that might have persistent herbicide contamination should adopt risk management measures to minimize potential problems. The extent of appropriate risk management measures is a function of product markets. A composter producing compost for alternative daily cover at landfills would have a higher risk tolerance than one making compost for community gardens. The elements of risk management that composters should consider are: feedstock acceptance, recipe management, recipe amendment, and product bioassay and augmentation.
Feedstock Acceptance: A feedstock acceptance protocol is always the best line of defense to protect compost product quality. Refusing to accept a feedstock that can impair product quality is always 100 percent effective, but that option is not always a good one. “We like using horse manure and bedding in our recipes, as it has a good C:N ratio and it helps us balance dry and wet feedstocks,” says Dan Goossen, General Manager of Green Mountain Compost, the Vermont composter with recent persistent herbicide problems (see Part 1 of this series, “Unraveling The Maze of Persistent Herbicides In Compost,” June 2013). “We’ve stopped taking horse manure and bedding until there is a reliable testing method for these herbicides. We’re hopeful the industry and EPA can come up with a simplified yes/no method for herbicide presence.”
A good feedstock acceptance protocol also includes the ability to trace a feedstock back to its source in the event of a quality control problem, but that is difficult in modern agriculture and food distribution. “When our contamination problem surfaced in June 2012, we began storing samples of feedstocks in the freezer so we could go back and test them,” notes Goossen, “We got lucky that we were able to identify one of the sources of the aminopyralid-contaminated hay.” However, tracing sales and handling of commodities like hay sold to horse farms is rarely so well-defined according to Tom Creech, a hay dealer who also owns the composting facility that makes Thoroughbred Landscape Products in Lexington, Kentucky. “When I sell hay for feed and bedding to the horse farms and track stables here, I buy it from a dealer in one state, who gets it from a grower in another state. I sell it to a distributor, who sells it to the horse tracks. So, when our composting facility gets the muck from the tracks for composting, if there is a contamination problem, we’d have to go through five levels of distribution to find out if that farmer used Milestone.” Both Creech and Goossen expressed concern that farmers will not be forthcoming about their usage of persistent herbicides if they think that their sales to horse farms will be affected.
Creech’s composting facility, which composts only horse manure and bedding, had a persistent herbicide contamination problem in 2012. “I sold some of our compost to a greenhouse tomato growing operation in another state that killed his entire crop,” explains Creech. “I had to replace all that compost for free, but at least that grower is still buying from me. My real worry now is that I have no confidence that the horse manure compost I sell is contamination-free.”
Recipe Management: Another element of a good risk management program is recipe management. Recipe algebra is using the mathematics of good recipe formulation to limit the amount of a feedstock added to a composting mix. This is more frequently used when heavy metals are an issue, but the procedure is the same for persistent herbicides. “Clopyralid and aminopyralid have some decay in composting,” notes Goossen, “but we don’t know the exact rates yet. So when we resume taking in horse manure and bedding, I will assume no decay in my recipe algebra and aim for a clopyralid concentration below 10 ppb and an aminopyralid concentration below 1 ppb.”
Recipe algebra is done in the same manner as accounting for carbon content, nitrogen content, or moisture content in the feedstocks, as shown in Table 1.
Recipe Amendment: Recipe amendment can be another component of a good risk management program. Goossen found that when he mixed a high-carbon wood ash with the soil in his bioassay growing pots, an amendment rate of about 20 percent on a volumetric basis resulted in growth response as good as in the control pots after 4 to 5 weeks. “I was a little leery of this idea at first, but it works amazingly well,” he says. “The resulting soil pH is above 7.5 but our compost runs a little high on pH to begin with.” He has not tried the wood ash amendment in his composting operation yet, but this author has used wood ash amendment in a paper sludge composting facility, with a similar result of elevated pH.
“Adding a high-carbon wood ash would be like treating the material with activated carbon,” explains John Jachetta, Ph.D., the (now-retired) Regulatory Sciences and Government Affairs Leader for Dow AgroSciences, LLC, manufacturer of aminopyralid. “Activated carbon irreversibly partitions certain chemicals into the carbon matrix, which is why it is used in some drinking water treatment applications. This approach could potentially be very effective in composting.” The balance point between adding enough wood ash to bind up the persistent herbicide and adding too much and producing compost with an elevated pH is not yet known. A high-carbon amendment like biochar may offer similar potential.
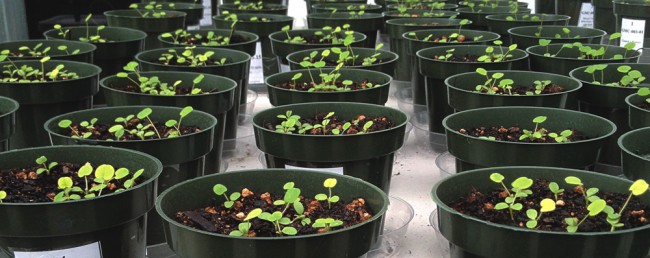
Plant bioassays, essentially growth trials, are the best and most cost-effective method of testing incoming feedstocks and finished compost for presence of persistent herbicides.
The persistent herbicide problem is not going to go away as EPA has signaled that it does not intend to force removal of these products from the market because of their effectiveness in controlling invasive and noxious weeds in pastures and rangeland. (As noted in Part I, an agreement was reached between Dow AgroSciences, the U.S. EPA and the Vermont Agency of Agriculture, Food and Markets to restrict use of Milestone on pastures in the Northeast, as well as placed restrictions on where hay grown in areas treated with Milestone can be distributed.) The impact of this problem on the financial viability of future composting facilities seeking capital funding is unclear at present, as investors will want to know what management practices are in place to prevent a repeat of the expensive settlements incurred by the Chittenden Solid Waste Management District in Williston, Vermont on behalf of GMC, which it owns and operates. Another unintended consequence is the adverse impact on improving the environmental sustainability practices at horse farms that wish to divert manure to commercial composting facilities as those facilities shy away from accepting the manure and bedding.
However, with a good risk management program in place, composters can accept limited amounts of some of these feedstocks without risk of compromising product quality.
Craig Coker is a Contributing Editor to BioCycle and a Principal in the firm Coker Composting & Consulting (www.coker compost.com), near Roanoke VA. He can be reached at cscoker@verizon.net.
References
Michel, F.C., et al., “Persistence of Imprelis During Composting”, presented at U.S. Composting Council Annual Conference, January 2012, Austin TX
U.S. Environmental Protection Agency, “Environmental Fate and Ecological Risk Assessment for the Registration of Aminopyralid”, Office of Prevention, Pesticides and Toxic Substances, May 2005.
U.S. Environmental Protection Agency, “Clopyralid; Pesticide Tolerances”, Federal Register, Vol. 77, No. 182, p. 58045, Sept. 19, 2012.
U.S. Composting Council, Position Paper on Persistent Herbicides, April 2013.