Partnership between the City of Wooster, Ohio and an anaerobic digester developer to retrofit WWTP solids handling is already yielding positive results.
Marsha Johnston
BioCycle December 2014
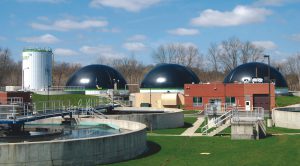
Retrofits to three anaerobic digesters (domed structures below) at the Wooster WWTP included adding a steel ring to each tank to increase volume by 100,000 gallons/tank, and to add mixers and heat exchangers.
In early 2013, the City of Wooster (pop.~ 26,300) in northeastern Ohio found itself in a bind: Despite having spent $25 million in 2007 to upgrade its wastewater treatment plant processes, its discharges were not compliant with environmental regulations. The plant has a designed daily flow capacity of 7.5 million gallons/day (mgd); daily flow is actually 3.5 mgd. “The process upgrades were supposed to reduce the amount of solids and save on power consumption,” explains Kevin Givins, Wooster’s utilities manager. “The project ended in 2007, but by 2011 we were under findings and orders from Ohio EPA to investigate the issues and fix them.” Notably, the plant was not in compliance for suspended solids, ammonia, and Biochemical Oxygen Demand (BOD). In fact, the Ohio EPA told the city it needed to reduce the solids in its effluent into the Killbuck Creek almost immediately after the 2007 upgrades to the plant were completed.
The 2007 project did not upgrade any of the plant’s anaerobic digesters, two of which were built in the 1940s, two in the 1960s and one in 1980. “We would have been looking at another $5 million to fix the digesters,” adds Givins, “but after we spent $25 million, there wasn’t a lot left over to do additional projects.”
The City of Wooster issued a Request for Proposals in 2013 to upgrade the solids handling portions of its WWTP. It received two proposals — one from quasar energy group and one from a joint venture between Agri-Sludge and Swedish Biogas. Quasar energy group, based in Cleveland, Ohio, proposed a public-private partnership where it would pay for the upgrades to the treatment plant’s solids handling, and Wooster would pay a tipping fee to quasar to process the solids as well as purchase electricity generated by the anaerobic digesters.
The city awarded the 20-year contract to quasar to retrofit, operate and monitor the plant’s anaerobic digesters, as well as manage the biosolids. All upgrades had to fit within the existing footprint of the WWTP. The contract marked the first time that quasar, which began in 2006 as Schmack Bioenergy, would retrofit an existing plant, notes Clemens Halene, chief operating officer, although it had done work on municipal facilities in Akron and North Ridgeville, Ohio previously. Quasar already had an AD plant, along with a laboratory and engineering facility, at Ohio State University’s Ohio Agricultural Research and Development Center (OARDC) campus located in Wooster.
Under the Wooster contract, quasar provided approximately 90 percent of the capital for the $7.1 million project, while the city spent $1.5 million. Due to the need to meet compliance deadlines, quasar had only 14 weeks to retrofit the three digesters, build the biomass (hydrolysis) tank and a building and receiving station, and install a 1,100 kW Caterpillar generator. The city was responsible for making the required wet stream improvements to manage the ammonia and BOD levels (at a cost of about $4 million). The city’s project also included installing a septage receiving station, which it hadn’t been able to do previously because of challenges managing its own solids.
Facility Retrofits
Quasar’s responsibilities at the WWTP start with receiving the primary and waste activated stream from primary treatment, which is operated by the city. “The solids are pumped from the settling tanks and we take it from there,” explains Halene. “We are responsible for the digestion, effluent solution and energy solution to provide electricity back to the plant.”
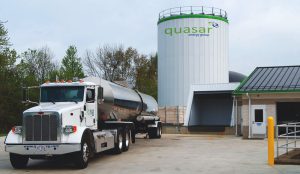
A biomass equalization tank is used to mix the treatment plant solids with other substrates, such as food waste, prior to loading into the digesters.
Three of the WWTP’s existing digesters were expanded by adding a steel ring to each tank (increasing volume by 100,000 gallons/tank). Mixers and heat exchangers were installed. “We could have built all new tanks, but it was easier to upgrade them to 2014 standards, with increased size and higher sides,” he notes. “We put new gas storage shells on top, which provides tremendous biogas storage.” To avoid service disruption during the 14-week construction period, quasar installed a temporary gravity belt thickener to increase the solids content from 1.5 to 8 percent, and transported the thickened slurry to its digester on the OARDC campus, 1.5 miles away. “It required five tanker truck trips a day,” says Halene. “After digestion, we would bring the material back to the treatment plant’s lagoons.”
Incoming WWTP solids arrive at 1.5 to 2 percent solids; a gravity belt thickener raises the solids content to 8 percent. Quasar built a biomass equalization tank to macerate, mix and store feedstocks prior to anaerobic digestion. Using the tank helps to control odors from incoming feedstocks. In addition to the WWTP solids, quasar sources food waste and other organics streams, both locally and from the Cleveland and Columbus areas. “We get the tipping fees for that material,” adds Halene. “The City of Wooster also can source feedstocks and in turn, it receives a percentage of the tipping fee for what it brokers. Our goal is to source all additional organics from a 10 to 20 mile radius of Wooster.”
The streams are pumped into the biomass tank, mixed for three days and pumped into one of the three digester tanks, where they remain for between 18 to 30 days. The new system can handle up to 14 percent solids versus only 2 percent previously. The city’s solids utilize about one-third the capacity of the retrofitted digesters, with the remaining two-thirds available for additional feedstocks, especially those with higher energy content.
Energy Production, Nutrient Recovery
Biogas from the digesters is fed to a 1,100 kW CHP unit on site that converts it to electricity; the plant uses 600 kW and 500 kW is sold to the grid. “Wooster is exporting almost the same amount of electricity it is consuming,” notes Halene. Taking the Wooster plant off grid is saving the city between $300,000 and $400,000 a year, as the plant’s electric bill has been chopped from over $32,000 a month to just over $300, according to Givens. Quasar is planning to install a biogas upgrade system in the next 12 months to be able to sell renewable CNG vehicle fuel.
The increase in plant capacity has also opened the door for Wooster to accommodate more industry. Daisy brand dairy products, based in Garland, Texas, is building a new dairy processing plant in Wooster, closer to East Coast markets. “Because we were in violation of our permit, we wouldn’t have been able to take a significant industrial load if we didn’t deal with some of the issues,” explains Givins. “I would venture to say that, if not for quasar, we would not have gotten the Daisy project, and that they would probably have located somewhere else.”
Quasar has a proprietary full-scale nutrient resource recovery system at the wastewater treatment plant that operated for about three months on a testing basis. The company is scaling nutrient recovery back over the winter months, and plans to go into full-scale operation of the equipment in 2015. “Essentially, our process treats the digested effluent by recovering the nutrients — primarily nitrogen,” says Halene. Nutrient removal enables the treated wastewater to be discharged into the nearby creek. Currently, the effluent is stored in lagoons. Quasar’s goal is to dewater digested effluent to 25 percent solids and recover nutrients from the 75 percent liquid stream. Biosolids are used on reclamation sites or land applied on farms.
The City of Wooster is excited about the changes at its wastewater treatment plant. “There was a lot of concern in the community as to what was going on, with numerous articles in the paper that didn’t shed a positive light on us,” notes Givins. “But that’s all turned around now, the facility is in compliance, and the plant is off the grid, generating more power than we can use.”
Marsha Johnston is a Contributing writer to BioCycle.