Norm-E-Lane Dairy in Wisconsin installed an anaerobic digester in 2007, and “outgrew” it several years later, prompting expansion and a new engine.
Nora Goldstein
BioCycle March/April 2016
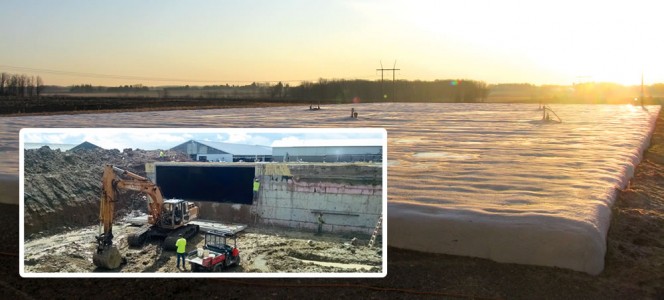
Norm-E-Lane Dairy expanded its DVO Two-Stage Mixed Plug Flow™ digester in 2014, increasing capacity from 1.42 million gallons to 1.96 million gallons. Construction of 70-foot digester extension (inset). Photos courtesy of Norm-E-Lane Dairy
In 2007, Norm-E-Lane installed a DVO, Inc. patented Two-Stage Mixed Plug Flow™ anaerobic digester sized to process 1.42 million gallons of manure. “We looked at a couple other anaerobic digesters on farms in Wisconsin and were interested in the bedding product made from the separated solids,” recalls Josh Meissner, grandson of the dairy’s founders, who owns and operates the dairy with his father, uncle and cousin. “And we determined we could pump the digested effluent to the field versus having to haul it. Those were the initial factors that led to our decision to install the digester. And as we got going, we learned about the odor reduction benefits and recovery of the excess heat from the engine.”
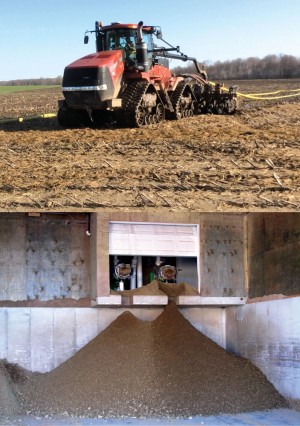
The dairy’s initial interests in installing an AD system were the ability to pump digested effluent to farm fields for application (top), and the bedding product made from the separated solids (bottom). Photos courtesy of Norm-E-Lane Dairy
Along with the digester, the farm installed a 600 kW Guascor engine. Norm-E-Lane has a power purchase agreement (PPA) with Dairyland Power Cooperative. “All the power we produce goes back on the grid,” notes Meissner, “and we buy power back per our PPA. Heat recovered from the engine is used to heat the digester and some of our other buildings.”
The original DVO digester was sized for 2,000 cows. But as the dairy improved efficiencies in the milking parlor, it was able to add more cows. “It ended up being 400 more cows,” he says. “We were adding too much manure too quickly to the digester, and it wasn’t operating properly. As a result, we faced a choice to either expand the digester or shut it down.”
The Meissners selected expansion and worked with DVO, Inc. and W.W. Williams, an industrial distribution company, in 2014 to assist. The digester was shut down, emptied, and a 70-foot extension was put on, increasing the capacity from 1.42 million gallons to 1.96 million gallons, or about 38 percent. That is equivalent to 33 gallons/cow/day — 25 gallons of manure plus 8 gallons of wash water. (Dry, non-milking cows provide about 16 gal/day.) Capacity is based on a 21-day retention time in the anaerobic digester. The expanded facility went on line in the fall of 2014.
Engine Replacement
The original engine installed in 2007 ran well for the first 3.5 to 4 years, but then started to show signs of age, notes Meissner. “We had a 95 percent run time for the first few years, but the biogas is hard on components,” he says. “We did repairs and replaced parts but by about year 5, the cost-effectiveness to continue doing repairs wasn’t there so we decided to take the engine off line. We went about 1.5 years without an engine, instead feeding the biogas to a boiler which in turn heated the digester.”
In need of a replacement engine, DVO suggested that Norm-E-Lane install a combined heat and power (CHP) unit made by MTU Onsite Energy. W.W. Williams had just begun distributing the engine in parts of the U.S. and Mexico, targeting the anaerobic digestion market. “MTU guarantees 42 percent electrical efficiency of the engine,” explains Tom Drake, Manager of the firm’s Gas Power Systems Group. “MTU supplies the engine and the control package, and our team supplies the balance of the CHP plant, including heat recovery and gas cleaning and conditioning.”
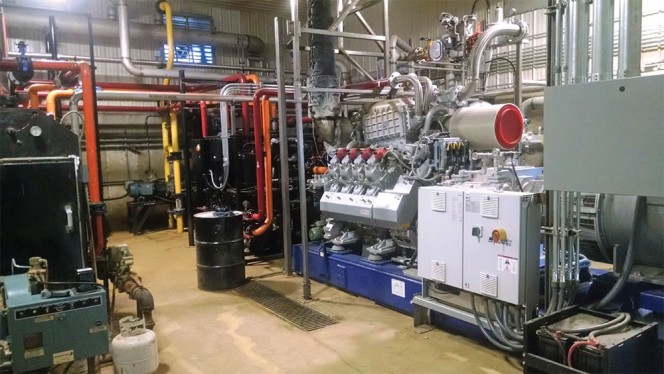
As part of the expansion, Norm-E-Lane installed a combined heat-and-power unit made by MTU Onsite Energy. The engine is rated at 763 kW, but is limited to producing 600 kW per the dairy’s power purchase agreement. Photo courtesy of W.W. Williams
The new engine and components had to fit into the footprint occupied by the previous unit. Stainless steel was used as much as possible to extend the life of components. “Our other CHP system didn’t include hydrogen sulfide and moisture removal, which we now have,” notes Meissner. “Preconditioning is part of the MTU system.”
One feature of the agreement with W.W. Williams is that by the end of year eight, to cut down on labor hours for maintenance and downtime of the engine, MTU switches out the existing engine with one that has been remanufactured by MTU. “The replacement engine is reconditioned and under warranty to be equivalent to a new engine,” explains Drake. “So instead of doing a complete engine rebuild in the eighth year of the agreement, which requires taking it off-line for about a month, the switch can be done in about a week-and-a-half.”
Norm-E-Lane secured grant funding from Wisconsin’s Focus on Energy Program to cover some of the capital costs of the original digester as well as the expansion. “Our recent Focus on Energy funding was $500,000,” says Meissner.