BioCycle December 2016
Kerman, California: Mid Valley Disposal Opens New Composting Facility
Mid Valley Disposal (MVD), headquartered in Kerman, services the Central Valley in California. The open house for its new food scraps and yard trimmings facility was held in mid-December. “This is the first facility in the Central Valley for diverting large volumes of food scraps in order to meet California’s organic diversion mandates,” notes Ivette Rodriquez, MVD’s recycling director. MVD received a $3 million CalRecycle grant from the state’s Greenhouse Gas Reduction Fund and must meet the GHG emission reductions required by the San Joaquin Valley Air Pollution Control District. Mid Valley Disposal’s new facility, located at MVD’s existing materials recovery facility and transfer station in Kerman, is designed to process 60,000 tons/year of pre and postconsumer food scraps and yard trimmings collected from the company’s existing routes in Fresno County and nearby communities. MVD is using Sustainable Generation’s SG Mega™ System with GORE® Covers. “We selected this process because it had already been precertified by the San Joaquin Valley Air Pollution Control District for VOC emission reductions,” adds Rodriguez.Mid Valley Disposal’s new facility features 16 bunkers, including 12 covered aerated static piles (164 ft. length x 27 ft. width x 12 ft. height each). Organics will be composted for 8 weeks in 3 phases: 4 weeks in Phase 1 covered; 2 weeks in Phase 2 covered; and 2 weeks in Phase 3 uncovered. The composting pad has in-floor aeration with a leachate collection system. MVD purchased a Vermeer horizontal grinder to process yard trimmings and food scraps before putting them under the GORE covers. A pilot project was conducted with Sustainable Generation to gain knowledge and experience with the end-to-end organics recycling process — from customer education and food scraps collection through marketing the finished compost. “The pilot ran for 7 heaps of compost at 450 cubic yards per heap for one year,” she notes.
MVD is establishing a protocol — working with other composting facilities utilizing the GORE cover technology — to determine what compostable bioplastic products can be processed successfully. To help manage contamination in incoming food scraps, a MVD recycling coordinator visits businesses regularly and when contamination is found a meeting is scheduled with the owner or manager to plan additional source separation training. “We also go back and check that the contamination is removed and corrected,” explains Rodriguez. “As for the processing site dealing with contamination, it will be prescreened to take out large contaminants before grinding them to our feedstock size.” Target markets for finished compost include agricultural application, customized fertilizer, site improvements, and storm water management and erosion control projects.
Queens Borough, New York: St. John’s University Expands Diversion With Pulper
St. John’s is a large private university in the Queens Borough of New York City with about 20,000 undergraduate and graduate students. Since 2012, student workers have been diverting preconsumer food waste to an on-site O2 Compost aerated static pile three bin system. Historically, the preconsumer diversion amounts to about 3,000 pounds per week. Wanting to expand the program to include postconsumer food waste, Tom Goldsmith, Director of Environmental and Energy Conservation at St. John’s, started shopping around for a grinder or macerator to reduce the volume of the food scraps going into the aerated bins. “I was getting quotes for new machines at over $50,000 each,” notes Goldsmith. “As luck would have it, I stumbled upon a 800 pound/hour Somat Remote Waste Pulping System Model SPC-50 on eBay. As it turns out this pulper had been picked up by a kitchen equipment resupplier from a grammar school in the New York City suburbs and was being offered for $6,000.”
Once the unit was set up, St. John’s student workers began a campaign to engage the larger student body in the dining hall to “Scrape their plate for compost.” “I expect St. John’s will be able to double its diversion quantities to recover 9,000 pounds/week of pre and postconsumer food waste,” says Goldsmith. “We estimate that is 90 percent of all campus food waste.” When mixing the pulped food waste as feedstock, he is testing an increase in the amount of bulking agent (wood chips) from a ratio of about 50:50 for nonpulped food to adjusted ratios of 60:40 to 65:35 bulking agent for pulped food waste. For a look at SJU’s operation, check out their SJU YouTube at http://bit.ly/sju_soils.
Charlottesville, Virginia: How2Compost Label Launched
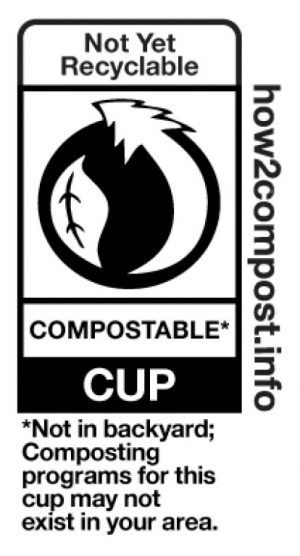
Sustainable Packaging Coalition’s How2Compost label features information to assure consumers packaging is certified compostable.
How2Compost is an extension of SPC’s successful How2Recycle program. Like the How2Recycle label, the How2Compost label is a next generation labeling system that brings harmonization and precision to recovery claims on packaging and is designed in accordance with the Federal Trade Commission’s guidance over environmental marketing claims. Companies can choose to become a member of How2Compost in order to feature the label on their BPI-certified packaging.