Technology to produce food waste slurry key to project implementation — and helps generators comply with California organics recycling mandates.
Craig Coker
BioCycle January 2017
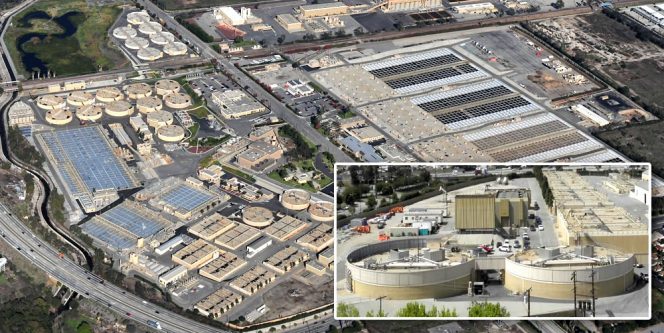
The Sanitation Districts’ JWPCP in Carson (CA) treats an average of 280 million gallons/day of wastewater. One of the two anaerobic digestion tanks above has been used for codigestion, with the second serving as the control.
Photos courtesy of Los Angeles County Sanitation Districts
The Sanitation Districts, a regional agency, is a confederation of 25 independent special districts working cooperatively under a Joint Administration Agreement. It was created under state law to serve the wastewater treatment and solid waste management needs of about 5.6 million people in Los Angeles County. The service area covers approximately 850 square miles and encompasses 78 cities and unincorporated territory within the county.
The wastewater system includes approximately 1,400 miles of sewers, 49 active pumping stations, and 11 wastewater treatment plants (also known as Water Resource Recovery Facilities, or WRRFs). A portion of the biosolids from the 11 WRRFs are shipped to the Sanitation Districts’ Tulare Lake Compost in Kings County to produce Class A EQ compost, and the rest are managed through 6 contracts, mainly through composting.
The solid waste system includes two operating sanitary landfills, three landfill energy recovery facilities, three materials recovery/transfer facilities, and two refuse-to-energy facilities. Between the wastewater and solid waste system facilities, approximately 120 megawatts (MW) of renewable electricity are produced. Yard trimmings that are not reused as alternative daily cover at landfills are composted elsewhere in Southern California.
Joint Plant Codigestion Studies
The Sanitation Districts’ flagship WRRF is the Joint Water Pollution Control Plant (JWPCP), located in Carson. The plant treats an average of 280 million gallons/day (mgd) of wastewater from a service area of 3.5 million people. Sewage sludge from the primary and secondary activated sludge treatment system is anaerobically digested in 24 completely stirred tank reactors, each containing 3.7 million gallons. The reactors operate at 96°F (35°C) and have a hydraulic retention time of 18 days. The digesters produce about 5,000 standard cubic feet per minute (scfm) of biogas, some of which is used to keep the reactors mixed and heated. The remainder is scrubbed to remove particulates, dried to remove moisture and then compressed and chilled to serve as fuel for three gas turbines and one steam turbine-generator. The 20 MW of power generated from this combined-cycle power plant is used to meet all of the JWPCP’s electrical needs. A public CNG refueling station is located within JWPCP.
As a result of the passage of AB 341 in 2011, a feasibility study of codigestion of food scraps with sewage sludge was conducted at JWPCP. The study concluded that the concept had technical merit, although economic merit was questionable. The main advantages were that the digesters existed and energy recovery from biogas was already an operating practice. The unknowns were the impact of the food wastes on digester performance and on digestate quality, the materials handling considerations managing a solid waste within a WRRF, and the economics of codigestion.
In 2012, the Sanitation Districts started several laboratory bench tests, adding slurried food waste from a private contractor (see below) at a rate of 10 percent by volume. The slurried waste contained approximately 14 percent total solids, 92 percent volatile solids and chemical oxygen demand (COD) of 225,000 milligrams per liter (mg/l). Biogas production in the bench reactors increased by 112 percent. This led to a decision by the Sanitation Districts to develop a demonstration project at JWPCP to explore larger-scale implementation issues and economics. The objectives of the demonstration project were: to assist member cities with food waste diversion efforts, determine the impact of full-scale food waste codigestion on WRRF operations, evaluate the performance and economic considerations, and to decide whether to expand the codigestion program to other Sanitation Districts’ WRRFs.
Collaboration With Waste Management
In 2008, Waste Management (WM), recognizing growing interest in food waste diversion, decided to investigate how it could develop new technological solutions for processing food waste streams in addition to traditional composting. In 2009, it developed a large-scale (>75 tons/day) pilot program for diverting food waste to anaerobic digesters. After discussions with several municipalities, WM began bench-scale testing a processed food waste material for codigestion at the Orange County Sanitation District in 2011, followed by pilot-scale testing at the Victor Valley Wastewater Reclamation Authority. In 2012, it began negotiations with the Sanitation Districts to pilot test its system at JWPCP.
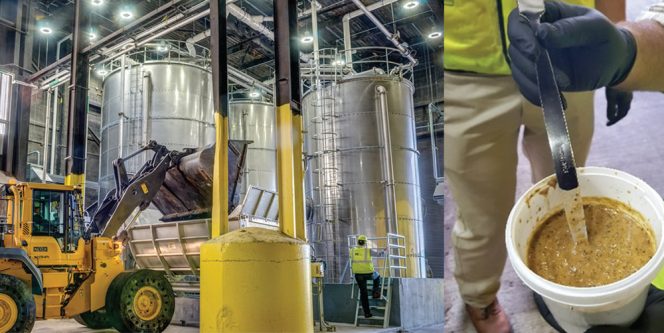
Waste Management has been using its patented CORe® processing system (above) to supply the JWPCP with an “engineered” slurry (right) produced from food waste. Photos courtesy of Waste Management
Recognizing the CORe program could produce a suitable feedstock for the JWPCP digesters, the Sanitation Districts and WM entered into an agreement for a two-year demonstration project where WM would deliver, by truck, 84 tons/day (200,000 gallons) of a food waste slurry. The project began in February 2014. The EBS slurry is delivered in 5,000 gallon tankers, with 4 to 5 trucks per day delivering 20,000 to 25,000 gallons/day. The slurry is unloaded into sealed storage tanks with recirculators that operate several minutes each hour to maintain the slurry suspension. WM pays a tipping fee of about $10/ton to help cover a portion of the codigestion project’s implementation costs.
JWPCP designated one of the 24 AD reactors as the designated test reactor. The slurry is injected into the test reactor at a rate of 9 percent of the liquid volume and 30 percent of the solids volume. The EBS slurry, which is made from food waste from commercial sources and some expired soda products, contains about 250,000 mg/l COD, has a volatile solids content of 91 percent and has very little contamination (see Table 1), notes Myers. Specifications for codigestion feedstocks are still evolving and have both regulatory considerations, like heavy metals content, and digestibility considerations, like COD content. “Our original plan was to design the CORe processing technology to handle up to 10 percent contamination by weight,” he adds, “but we found these early-stage opportunities to be somewhat unique, so we are tailoring our EBS slurry product to meet the needs of each partner. Someday, we hope to see more uniform food waste specifications for codigestion at WRRFs.”
Renewable Natural Gas Production
Increases in biogas production mirror those observed in the bench-scale testing. “Adding 84 tons/day of EBS is producing an additional 100,000 cubic feet/day of biogas, which is capable of producing an additional 200 kW of electricity,” explains David Czerniak, a Senior Engineer with the Sanitation District’s Energy Recovery Engineering Section. “As the WRRF is self-reliant, we are turning to our CNG refueling station to explore renewable natural gas (RNG) vehicle fuel from the biogas. The 84 tons/day of EBS we are taking now is capable of producing 1,200 gasoline gallon equivalents (GGE) of RNG. The CNG station could take up to 400 cubic feet per minute (cfm) of RNG, which would mean digesting 125 tons/day of diverted food waste.”
The Sanitation Districts has applied to the California Energy Commission (CEC) for a grant to develop a biogas conditioning system to make RNG for direct RNG fueling at the existing CNG refueling station on the property. The project will consist of installing a conditioning system to purify the biogas and associated delivery piping to produce 760,000 GGE of RNG per year, with an estimated revenue of $2 million annually based on current market conditions. The project cost is estimated to be $5.4 million. A CEC grant, if received, would fund up to $2.5 million of the project.
The Sanitation Districts is also in discussions with Southern California Gas about using the cleaned biogas from additional food waste digestion for biomethane injection into the natural gas distribution grid. “Our research suggests that a biomethane injection project could take up to 1,040 cfm of RNG, which would come from about 375 additional tons/day of diverted food waste through our digesters,” says Czernkiak. “We are also considering a demonstration using the Grind2Energy technology from Emerson, bringing the slurry produced by that system directly into our sludge wet well upstream of the digesters. As a test, we are getting about 4,000 gallons/week, which is too small of an amount to have much effect on our biogas production.”
Demonstration projects, by their very nature, identify issues that need to be addressed and resolved as part of facility planning. There were a few start-up issues involving EBS storage and handling that were worked out. One issue was that summertime hydrogen sulfide (H2S) levels in the test reactor peaked at 1,800 mg/l, where normal H2S levels were 200 mg/l. WM added vinegar to the EBS to reduce the pH, which has improved the H2S levels, along with more rapid turnover of the contents of the storage tanks. Another initial concern was reactor mixing. The JWPCP digesters have gas mixers; compressed biogas is forced down hollow-tube lances to the bottom of the reactor, where the gas bubbles up and mixes the tank contents. JWPCP staff was uncertain whether the higher solids loading from the food waste in the test reactor would stifle efficient mixing, but that has not been the case to date.
The WRRF’s AD reactors are cleaned every 8 to 9 years, which takes about 6 months. The staff is planning to move the test reactor to another digester so they can take the first one out of service for some overdue cleaning. This will answer the question of what impact the food waste has on digester volume capacity.
Craig Coker is a Senior Editor at BioCycle and CEO of Coker Organics Recycling (www.cokercompost.com) near Roanoke VA. He can be reached at ccoker@jgpress.com.