Experiencing odors and complaints at its AD operations, quasar energy group spent 10 months dissecting the situation and coming up with a suite of solutions.
Marsha W. Johnston
BioCycle March/April 2017
In a comprehensive initiative to bring the challenge of odors to heel, Cleveland,
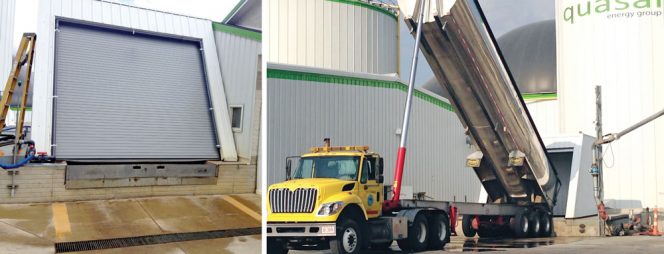
Hoppers where incoming organics are unloaded are kept under negative air to draw in any fugitive odors. An odor neutralizing atomizer system was installed around the perimeter of the hopper threshold (gray tubing, photo on left). Photo courtesy of quasar energy group
“Before our evaluation and odor plan, over all of our eight plants studied, we have had several hundred odor complaints since the first one was built,” notes Scott Nally, quasar’s Chief Operating Officer and former Director of the Ohio Environmental Protection Agency (Ohio EPA). “Since we implemented the plan and its changes in the latter part of summer 2016, we have had only a handful.” Nally acknowledges that the biggest test of the innovations will come in the warm months of 2017, but says the warm weather last October was a good test.
Odor Inventory, Characterization
The first step in the evaluation process was to identify and characterize the odors. Beginning in February 2016, in close cooperation with the Ohio EPA’s Technology Compliance and Assistance Group, quasar began identifying every possible odor its plants could emit, the typical source and the best way to quash it. Taking in over 100 different waste materials, including animal and human waste, quasar knew that each has a different potential odor. “Protein-based waste tends to have an ammonia odor from nitrogen, while human waste tends to create a sulfurous, rotten-egg smell,” explains Nally. “We surveyed all of the different waste streams from a chemical standpoint to identify odor mitigation technologies.”
The second step was to study quasar’s physical facilities and stages of the AD process to see where odors might be arising. Odors were characterized as high, medium or low “emitters.” The rankings were applied, for example, to liquid and solid receiving areas, the digester pressure release mechanism, biofilters and flares.
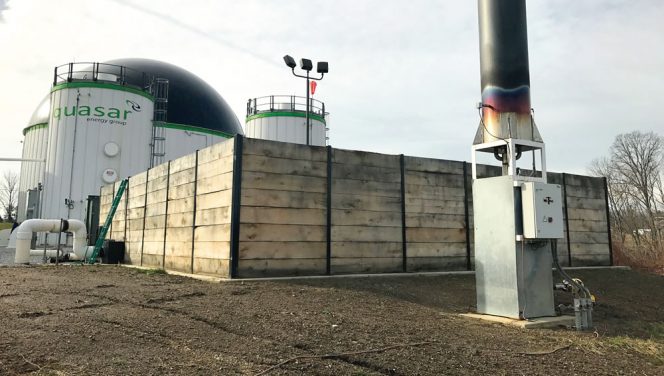
Quasar energy group took a critical look at its biofilters, including the media, sizing and contact time as odorous air passes through. The new biofilter at its Wooster (Ohio) AD plant is four times the size of the original. Photo courtesy of quasar energy group
Just as valuable, he adds, the Ohio EPA group provided quasar a wider perspective on odor causes and solutions. “They brought ideas to the table, from all kinds of industries, for example, what’s working at oil and gas operations, and at industrial facilities making mothballs.” Jointly, quasar and the Ohio EPA group began mixing and matching mitigation solutions. The company used one of its AD plants with an on-site lab as a research and development facility to test tools such as a small oxidizer. “Once we found the right pieces and parts, we retrofitted all of our AD plants with the technologies,” notes Nally.
Odor Management
Once the analysis was complete, quasar began matching up technologies based on the material being digested and the locations where odors are emitted. For example, at the receiving area for solid human or animal by-products, a truck pulls up, and the material drops into a hopper. The hoppers and liquid receiving areas are now kept under negative air to draw in any fugitive odors. The company also mounted diffusers and put an odor neutralizer around the perimeter of the hopper threshold. Neutralizers, explains Nally, are similar to the air fresheners that people use in their bathroom. An important finding of the study, he adds, was that neutralizers work, but masking agents, such as orange or cherry scents, do not.
Quasar examined different types of biofilters and biofilter reactors, oxidizers, and various engineering solutions, such as ways an odor could be completely self-contained. “Obviously, we can’t block off a pressure release valve, but we looked at our process flow diagram and shored up wherever we could contain it,” he notes.
Containing odors also meant taking a critical look at the facilities’ biofilters, including the biofilter media, sizing and contact time as the odorous air passes through the biofilter for treatment. The company added more areas where biofilters would be used to treat odors, such as the feedstock hopper and any kind of dewatering area, explains Nally. Because of the greater air volumes coming in and the complexity of quasar’s waste streams, the company determined that the 15- to 30-second contact time and biofilter size it had been using were insufficient. “We needed at minimum one minute of contact,” he says, noting that the new biofilter at its Wooster (Ohio) plant is four times the size of the original. “We had to add substantial capacities to biofilters at all AD plants. We had to increase the size for more contact time and then increase it again for the greater cubic feet [of air] running through them.”
Further, quasar established a biofilter maintenance regime, writing up a set of standard operating procedures (see sidebar). “There is a maintenance component with biofilters,” continues Nally. “Running air through them dries them out, [so] we measure moisture content to make sure they still have biota. The biofilters have to stay moist, particularly in the summer.” To address short-circuiting — when cracks or crevices form in the media and allow odorous air to escape before being treated — operators need to fluff the bed and replace parts of it periodically. “We do partial clean outs, which help with the biofilters’ efficacy,” he says. “And wood chips, which many AD installations use as a biofilter medium, can become a compost pile in the summer and create their own odor.”
To also address short-circuiting in the biofilter beds — and improve structural integrity — quasar designed and is patenting a biofilter utilizing a filter sock design (rows of multiple fabric tubes filled with media). According to quasar, the new biofilter design maintains a target minimum of contact time of 45 seconds for odor treatment.
Odor Coordinator
Finally, to solve what is often a mystery when odor complaints arrive, quasar hired a full-time odor coordinator to monitor all 8 of its plants and a hotline. Nicole Lappin, a self-employed private investigator (PI) with a Class B PI license from the U.S. Department of Homeland Security and a former airline passenger service representative, applied for the job the same day she heard about it. Investigating workers comp cases and doing background checks, “I developed a detective mentality and ability to approach topics in a factual, nonemotional way,” explains Lappin. “And my years in the airline industry with passengers taught me to listen and respond in a timely manner. I think these are essential qualities for an odor coordinator.”
Nally agrees on the importance of keeping emotion out of the complaint process: “Obviously when someone’s having a cookout, it can be emotional, but you really have to be able to dissect the event.” Soon after Lappin was hired last summer, her value was proven, adds Nally, by providing quasar knowledge of odor incidents that occurred when the plant was not receiving any materials. “At one of our plants, we kept getting calls from residents complaining about odors at the same times, sunrise and sunset,” she recalls. Lappin recorded the location, date, time of the odor, its description and duration, and weather conditions.
“She has tools at all of the plants to assist her, including cameras, sensors, pumps, and pressure gauges,”explains Nally, “enabling her to see what is happening at a given plant at any given time. Once we were able to get the specifics of the complaint, we could pin it down in our gas curve, and really use science and direct factual information to see what was causing the issue.”
Quasar discovered that odor events are often weather and time dependent. “The domes are black, so during the day when sun is on them, they have a particular pressure,” he notes. “When the sun goes down, the pressure changes on the dome, and it would flip the overpressure valve and there was a release of biogas.” The same phenomenon would happen at sunrise. Even though the valve only released for a couple of seconds, Lappin put the pieces together and the company figured out a fix: ramping up the engine or flare just prior to a release to prerelieve the system of any biogas. “When you have someone on staff directly connected to odor in their title, he or she will follow up on every piece and run it to ground,” continues Nally, adding that the public really appreciates the ‘closed loop piece’, that we’re doing something about it.”
For her part, Lappin believes having the same person answer the hotline builds trust with the community. “It’s important for people to know that if they call, they will get me on the other end of the line, and they won’t have to repeat their experience to multiple representatives,” she says. “And that once it is completed, I will follow up with the residents on any of our findings.”
In each of the communities where quasar has an AD plant, it publicized the hotline through its website, the local wastewater treatment facility, business organizations and Chambers of Commerce. The company also sent email blasts to neighbors, particularly any that had historically complained of odors.
Marsha W. Johnston is a Contributing Editor at BioCycle and an Editor at Earth Steward Associates in Arlington, VA (mwjohnston1@gmail.com).