Tool to assess the costs and benefits of a significant capital investment takes into account economic, environmental and social criteria.
Craig Coker
BioCycle June 2018
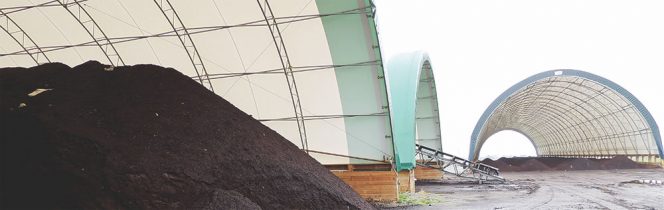
Fabric structures provide covered areas for feedstock receiving, composting and curing. Photo by Doug Pinkerton at Oregon Dairy Organics, Lancaster County, PA
Consider the following scenario: A yard trimmings composting facility in Virginia decides to begin accepting food waste, starting with very clean preconsumer streams that can simply be incorporated into the yard trimmings windrows. Then the municipality decides to consider offering a curbside collection program for postconsumer food waste, anticipating sending the collected organics to the composting facility. The facility now has to evaluate upgrades to meet the State of Virginia’s regulatory requirements for postconsumer food waste composting, which includes: “Covered areas for receiving, segregation, and grading of the waste shall be provided to segregate the waste from noncompostable components.”
Facility management confers with municipal officials to evaluate both the costs of upgrades and the benefits those investments may produce. It decides to use a cost-benefit analysis method called “Triple Bottom Line.”
Traditional CBA
A widely used method to evaluate an infrastructure investment is the Cost-Benefit Analysis (CBA), developed in Europe in the 19th century and brought to this country in 1936 by the Federal Navigation Act, which required the U.S. Army Corps of Engineers to carry out projects for the improvement of the waterway system whenever benefits outweighed costs. CBA has been widely used since then by both public and private developers to make economic decisions about entire projects, or parts of projects.
To reach a conclusion as to the desirability of a project, in this case, “Should I put up a building for composting?”, all aspects of the project, positive and negative, must be expressed in terms of a common unit; i.e., there must be a “bottom line.” The most convenient common unit is money, therefore all benefits and costs of a project should be measured in terms of their equivalent money value. For example, at a composting facility located outdoors at a dairy farm on a mountain ridgeline in western North Carolina, the winter wind blew unimpeded and the productivity of the staff declined noticeably on those cold winter days. Improving employee productivity by enclosing the facility with a structure could be easily measured in dollars.
One of the problems of CBA is quantifying benefits that are not directly expressed in terms of dollars, making the assignment of monetary values very challenging. For example, one obvious benefit of enclosing composting operations is that the risks of off-site odor episodes are greatly reduced. Clearly, that is a potential benefit to nearby sensitive receptors, but how can a monetary value be assigned to that benefit? One measure could be the avoided cost of having staff deal with complaints, or worse, an attorney’s fees for litigation defense.
Triple Bottom Line
Triple bottom line (TBL) analysis, developed in the mid-1990s as a new framework to measure sustainability performance in corporate America, uses economic, environmental and social criteria to answer the question: “Is this [project or program] a good long-term investment?” TBL analysis breaks down economic, environmental and social evaluations into criteria and subcriteria that are both qualitative and quantitative. These criteria (also known as “people, planet and profits”) can then be weighted based on local contexts and applied to project evaluations. Accounting for the impacts of each criterion over the project lifecycle is important for a complete analysis. TBL analyses can be used to compare project alternatives, as well as to decide whether to move forward on a project or not.
No universal standard method exists for calculating the TBL. Neither is there a universally accepted standard for the measures that comprise each of the three TBL categories. This can be viewed as a strength because it allows a user to adapt the general framework to the needs of different entities (governments, businesses or nonprofits), different projects or policies (infrastructure investment or educational programs), or different geographic boundaries (city, region or country).
Whether using CBA or TBL, all economic impact criteria should assess project costs and benefits over the lifetime of an investment and take into account the time value of money by discounting future revenues and costs to the present. This is done with a Net Present Value analysis (see “Economic Tool to Evaluate Organics Recycling,” December 2015
). This economic analysis can be supplemented by pertinent engineering/technical evaluations (e.g. suitability of site soils, anticipated snow load, alternative materials of construction, etc.).
The environmental criteria to be used can reflect the owners’ environmental sustainability policies as well as the more obvious criteria of air and water pollution, noise, and impacts on adjacent areas. Environmental analyses should include both on-site and off-site impacts of alternatives. The environmental criteria could also be used to evaluate alternative structures on the basis of their environmental efficiency.
The social criteria that could be evaluated include nuisance issues, workplace conditions, and public engagement. Nuisance issues would include odors, dust, visual appearance, noise, and truck traffic. Clearly, enclosures greatly reduce the potential for nuisance conditions, both off-site and on-site. Enclosures also provide a visual aesthetic, communicating better “control” over operations.
Workplace conditions would focus on employee health and safety. Public engagement criteria should address the level of interaction with the public (will the project use local construction talent and be viewed positively?) as well as public acceptance of the project. Composting facilities that take in feedstocks from commercial and industrial sources that benefit a community’s diversion goals can be viewed as an important part of the community’s infrastructure and be an economic development selling point, which can enhance public acceptance for a well designed and properly operated facility.
After data are collected for the economic, environmental and social criteria, they are ranked and then weighted according to a set of factors developed in the TBL process. Suggested weighting factors should be solicited from multiple affected parties (facility owner, site manager, operators, site neighbors, and/or other stakeholders, etc.). This process can use the Weighted Criteria Decision Matrix (see “Weighting Factors in Organics Recycling Facility Development,” January 2016).
By evaluating alternatives based on their performance with respect to individual criteria, a value for the alternative can be identified. The values for each alternative are then compared to create a rank order of their performance related to the TBL criteria as a whole. This tool is important because it treats the criteria independently, helping avoid the over influence or emphasis on specific individual criteria.
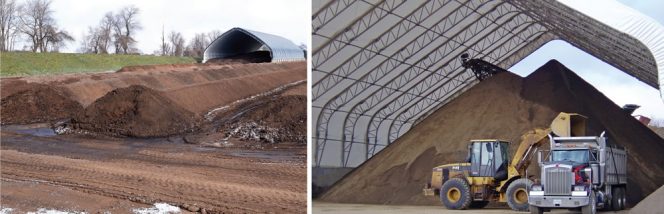
Laurel Valley Soils utilizes its ClearSpan fabric buildings primarily for compost product storage. Photos by Rick Long, Laurel Valley Farms
Case Study
“We started our composting operation to support several of the mushroom farms around us in 1979,” explains Rick Long, General Manager of Laurel Valley Soils in southeastern Pennsylvania. “We have three buildings on-site that we use primarily for product storage — a steel-roofed structure and two Clear-Span fabric buildings. We need to have lights on in the steel building for our workers to see, but in the fabric buildings, so much ambient light comes through that we don’t need lights on. So we save money on electricity, and we improve the safety of our operations.”
Long adds that Laurel Valley Soils had to replace the roof on its steel building once, “and we have already noticed corrosion that will require another replacement in 10 years. But we got 16 years of life out of one of the fabric building’s shells that just was replaced.”
The TBL can be calculated as follows:
• Economic benefit: Reduced energy cost and less frequent roof replacement
• Social benefit: Improved worker safety
• Environmental benefit: Reduced storm water runoff and improved storm water runoff quality — significant benefits given Laurel Valley Soils’ location in the Chesapeake Bay watershed.
“The Pennsylvania Department of Environmental Protection encouraged us to enclose some of our operations because of the Bay’s water quality problems,” recalls Long. “We wanted to help improve runoff quality, so we actually capture the water that comes off the roofs of our buildings to reuse it in the composting process.” He also notes it will be relatively easy to extend the ClearSpan fabric buildings in the future to enclose the composting operations should that be required or advantageous.
Craig Coker is a Senior Editor at BioCycle and CEO of Coker Composting & Consulting near Roanoke, VA. He can be reached at ccoker@jgpress.com.