Sixty percent of Muntons’ supply chain carbon footprint is attributed to artificial fertilizer used by its barley growers. The solution? Convert its liquid malt waste into biofertilizer.
Richard Crowhurst
BioCycle June 2018
Muntons, a supplier of “Great British Malt,” installed a mesophilic Up-flow Anaerobic Sludge Blanket system to treat its liquid malt waste. Photo courtesy of Muntons and HRS Heat ExchangersMuntons Malted Ingredients Inc., based in Chicago, is known to the U.S. food industry as the supplier of “Great British Malt.” Its products are used in the brewing and baking trades, as well as in breakfast cereals, confectionery and a wide range of other food products. What is less well known is that Muntons’ parent company in the United Kingdom is now a leader in sustainable production. Since early 2016, Muntons has been operating a “closed-loop” system which turns liquid malt waste into a high quality biofertilizer at its anaerobic digestion plant in Stowmarket in the east of England.
The basis of the system is a $7.5 million, 499 kW on-site anaerobic digestion (AD) plant that generates 14 percent of the site’s electricity. The reactor is a mesophilic Up-flow Anaerobic Sludge Blanket (UASB) system. Since its commissioning, the system has treated almost 33 million gallons of effluent, saving the company more than $3.35 million in electricity and waste disposal costs, and reduced carbon emissions by 800 tons of CO2e.
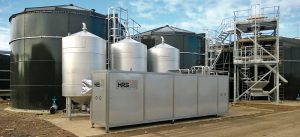
A 3-tank pasteurization system with tube-in-tube heat exchangers facilitates final treatment of the digestate, used as a biofertilizer. Photos courtesy of Muntons and HRS Heat Exchangers
Project Origin, Operations
Muntons first became interested in AD after analysis showed that 60 percent of the carbon footprint of its supply chain came from the artificial fertilizer used by its barley growers. The company realized that if a portion of the liquid waste it produces could be treated through AD, it could produce a high quality fertilizer for its farmers to use — significantly reducing its carbon footprint. The digestate product is high in organic matter and acts as a soil conditioner.
Digestate from the UASB system is blended with low chemical oxygen demand (COD) effluent before being treated with Dissolved Air Flotation in Muntons’ existing activated (aerobic) sludge plant. This stabilizes the digestate and removes further COD, nitrates and phosphorus, prior to the effluent being discharged to local waterways in accordance with an environmental permit. The remaining sludge is pasteurized in a 3-tank unit supplied by HRS Heat Exchangers, before the digestate product’s distribution to the growers.
The 3-tank system operates as follows: While one tank is being filled, the second holds the sludge at 158°F, at the same time as the third tank is being emptied. Each process lasts one hour. Waste cooling water from the CHP engine is used to heat the material in corrugated tube-in-tube heat exchangers, which is more efficient than heating an entire tank of digestate. HRS has also incorporated an energy recovery section into the process, whereby heat from the hotter (pasteurized) sludge is transferred to the colder (unpasteurized) sludge. This significantly reduces overall energy consumption of the pasteurization system. Every batch of digestate can be traced back to the feedstock from which it was produced.
Digestate Analyses
Once pasteurized, the biofertilizer can be supplied for application either as a liquid for soil injection or a dewatered solid for spreading. The material has a dry solids value of 30 percent; the liquid is typically 1 to 2 percent dry solids. Table 1 provides a typical analysis of the digestate. While the product currently is used on local land from which the company sources its malting barley, Muntons is interested in developing a wider market. It is working with the University of Lincoln on a project to document the composition and effectiveness of the biofertilizer. Initial results with lettuces grown with the digestate demonstrate quality and growth benefits over artificial fertilizers of similar nutrient concentration. A paper on the research (by Lincoln University and Crop Intellect) entitled, “Efficacy of Muntons digestate for its potential to be used in agriculture,” will be published soon.
A further collaboration with University College London showed that the digestate yields a type of bacteria that produces an antibiotic that kills multi drug resistant E. coli bacteria. Antibiotic bacteria were identified through a national scheme in the UK called Swab & Send — an initiative to look for new antibiotics in unusual locations.
Because Muntons’ plant uses a combination of both anaerobic and aerobic processes, under current UK Environment Agency rules, the resulting combined sludge cannot be certified as meeting the UK standards for compost and digestate. These standards, known as PAS110, provide a guarantee to users that the finished product meets certain quality parameters that make it exempt from further waste legislation, and can be applied to fields as a fertilizer. However, the Muntons’ process includes a pasteurization step and the resulting material is treated in accordance with the requirements of the PAS110 standard for anaerobic digestate, based on conventional Hazard Analysis Critical Control Points (HACCP) principles. This helps to assure local farmers that the final biofertilizer contains no ergot (a fungal disease of rye and other cereals) or plant pathogen contaminants.
Muntons plans to install a smaller anaerobic digester tank to ensure all of its sludge is treated anaerobically before final pasteurization and centrifugation. This satisfies both PAS110 and End of Waste requirements and will allow the nutrient-rich fertilizer to be sold back to farmers growing cereals. “We want our biofertilizer to compete in the agricultural market with the likes of PAS110 digestate and other biosolids that have undergone pasteurization,” explains Muntons’ environmental manager “Even though we are considered low risk and all our feedstock is from traceable, food grade grains, we felt that pasteurizing our material was the best way to help us get End of Waste Certification.”
The more than $3.5 million in savings as a result of installing the AD and pasteurization systems are split approximately equally between disposal costs and energy purchase. Muntons’ production plant is able to run at full capacity continually without the need for external waste disposal. “For Muntons, this whole project has been about maximizing efficiency,” explains Matt Hale, International Sales and Marketing Director at HRS. “Although they have an abundance of heat, they still wanted to recapture what they could and our heat exchangers provide 40 percent heat regeneration.”
Based in the United Kingdom, Richard Crowhurst is a freelance writer specializing in renewable energy, environmental and agricultural topics.