Jeff Ziegenbein
Composting facilities can utilize a variety of proactive maintenance strategies and tools to help reduce costs and increase uptime — avoiding unexpected breakdowns that can interrupt production. Leading into World War II, maintenance programs began to evolve from the less efficient and more costly reactive approach to proactive to condition-based strategies. Classic reactive programs included preventive maintenance but were primarily focused on repairing failures. This culture was one of high adrenaline as the maintenance teams were heroes for rushing in to save the day at all costs.
As maintenance techniques advanced into more proactive strategies, emergency repairs were reduced, enabling staff to adjust to simply keeping things running well and gathering monitoring data. At the Inland Empire Regional Composting Facility (IERCF) in Rancho Cucamonga near Los Angeles, California, the maintenance program has transitioned from highly reactive to one that uses a variety of proactive strategies. This has resulted in a reduction in downtime while maintaining cost containment goals.
The IERCF, which opened in 2007, is the nation’s largest fully enclosed composting facility, processing over 200,000 tons/year of biosolids, yard trimmings and wood waste, in aerated static piles. Biosolids comprise about 150,000 wet tons/year of that total. Because the facility is enclosed, the IERCF often faces more significant issues with moisture, dust and corrosion compared to outdoor facilities.
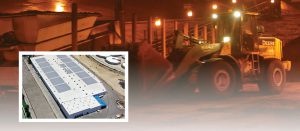
The Inland Empire Regional Composting Facility is the nation’s largest fully enclosed facility, processing over 200,000 tons/year of biosolids, yard trimmings and wood waste in aerated static piles.
For instance, feedstocks containing high nitrogen such as grass and biosolids, can produce ammonia gas while decomposing. The ammonia gas may mix with water or water vapor and become ammonium hydroxide, which is corrosive to steel and other unprotected metals. Active and finished compost products also often contain nitrates, chlorides, and sulfur compounds that can be extremely corrosive. Even microscopic amounts of these salts can draw moisture through coatings such as corrosion-resistant paints on metal structures and create osmotic blistering.
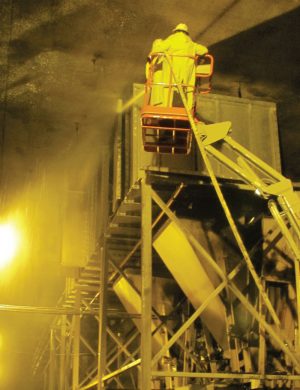
Housekeeping, such as washing down equipment, is very important due to the excessive moisture, dust and corrosion associated with compost manufacturing. Photo courtesy of Inland Empire Utilities Agency
Each facility’s maintenance program must be tailored to the conditions present at that facility. Whatever system or combination of systems chosen must be properly sized and simple to use. Keying in on the common challenges faced in the composting industry (dust, corrosion, stringy material, trash, moisture, etc.), a list of steps can be considered to help guide program development. Although maintenance can and often does occur without a plan, having one ensures that the right resources are being used at the right time and that costly surprises are minimized. And most importantly, a sound maintenance plan can improve safety and reduce injuries.
Here are eight simple steps to developing an effective maintenance program. Compost manufacturing operations, from the smallest to the largest, will benefit from taking these steps.
Step 1. Identify Assets
An asset in this context is property owned that has value. Typical assets found at a composting facility include front-end loaders, screening plants, grinders, water trucks, scales, and so on. List each asset and apply a description and a unique identification number. A notepad or an Excel spreadsheet will be fine for this step (more on maintenance software later).
One of the challenges here is to determine which components of each asset should be included as part of the asset or identified separately as a component. Typically, major parts of an asset will be listed as a component. For example, a trommel screen will be an asset. You’ve named it Screen-001. Screen-001’s engine and attached conveyors will be components of the asset. As you record information about the service and operations of the trommel screen asset, your repairs to its engine would be identified separately as part of its history.
Step 2. Criticality Analysis
Now that you have a complete list of assets, add notes that identify how critical the asset is to the organization. Consider how probable a breakdown will be and the impact. Is there redundancy, or a backup unit in place? For example, a newer front-end loader is not likely to have a serious breakdown but when it fails, inbound and outbound trucks would be sent away if there is no redundancy. In that example, the risk of failure is low but the cost is high, while the overall risk is medium. An older loader with no redundancy could raise the overall risk to critical. The matrix in Figure 1 helps rank the overall risk of failure and its impacts using a simple descriptor for each asset. This will be useful later when developing the maintenance plan. It’s important to note that if the risk includes a safety or compliance component, the overall ranking should be elevated.
Step 3. Assign A Strategy To Each Key Asset
Now that you have identified your assets, their criticality and their impact on your program if they fail, Step 3 is to assign a strategy for their maintenance.
Four primary strategies can be employed for each major asset:
- Time-based: Set a frequency for maintenance based on time such as daily or monthly
- Operation-based: Set a frequency based on use such as hours of operation
- Condition-based: Using observation, sample results or other indicators
- Run-to-fail: Allows equipment to fail
For example, you can use time-based to dictate when to grease the loader, operation-based to change the oil in its engine, condition-based to determine when to change the hydraulic fluid depending on oil analysis results, and run-to-fail on the pressure washer used to wash the loader.
Step 4. Develop A Maintenance Plan
Preventive Maintenance (PM)
A PM plan is just that — performing routine and regular maintenance tasks to lessen the likelihood of failure. These tasks are not done to correct a failure, but rather while the asset is operating normally, to allow it to continue to do so. The PM plan must take the operating environment into consideration. For example, the IERCF is an indoor facility that traps compost gases creating additional corrosion and moisture challenges, which can affect all assets. The PM plan should be tailored to address issues unique to each facility such as corrosion. Additional cleaning and painting with corrosion-resistant protectants might be necessary to mitigate the risk of failure. An outdoor facility might include steps to mitigate impacts from local weather conditions such as sun and rain.
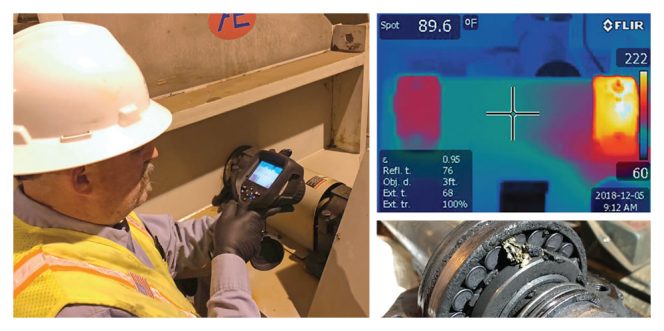
Infrared thermography uses a specialty camera (below) that displays and captures images color-coded by temperature (top, right). Users can quickly identify high temperatures on rotating equipment such as a bearing (bottom, right). Photos courtesy of Inland Empire Utilities Agency
The best place to start a PM plan is to go step-by-step through the list of assets and refer to each asset’s operation and maintenance manual. Tasks will be identified that should be performed at various frequencies. List each of those in a matrix using the four primary strategies discussed before. An example for what a front-end loader will likely require is shown in Table 1.
After listing the tasks for each asset, it will be clear which are required daily, weekly, monthly, etc. Next, procedures for those tasks along with a time estimate should be completed. For example, you observe the maintenance technician performing the daily greasing on Loader #003 and note that it takes approximately 15 minutes. Blowing out the radiator is another 15 minutes. The matrix with the asset, task lists, and time demands can be summarized providing a total time requirement to perform PM tasks for the entire facility. Those tasks can then be placed into the technician’s schedule. IERCF uses Microsoft Excel to summarize each technician’s schedule for the week. This gives all staff the ability to discuss and analyze the tasks as well as the status of each (Figure 2).
To optimize staff resources, it’s often most efficient to group tasks together by work type or location. This grouping will allow a maintenance technician to complete multiple tasks before moving on to another area or work type. At the IERCF, PM tasks are often grouped by location. For example, there are four large fan galleries so a monthly PM plan was established where a technician goes to one of the galleries and greases the motors, checks fan belt tensions, gathers bearing temperature data, and does light housekeeping.
This information helps identify the current resources to complete the PM work before each shift starts. Perhaps in the past, the maintenance crew started two hours before the operations team. That may or may not be the appropriate amount of time to service the equipment, but the data gathered from the preparation of the plan development will help clarify and allow for adjustments if needed.
Proactive Maintenance
Some maintenance tasks go beyond routine PM but can nonetheless be scheduled ahead of projected failures to avoid downtime. For example, you’ve had broken drive shafts and broken auger flails on your feed hopper augers after 14 to 15 months of normal operations. You may want to schedule an annual overhaul to avoid interrupting production. Failures during production tend to be far more disruptive and expensive, while also creating potential compliance and customer-service issues. The idea is to perform corrective action before a failure creates bigger problems.
The tasks should be added to the asset matrix and scheduled accordingly along with the anticipated time it takes to complete the task. A well-designed plan should contain several of these actions unless you are fortunate enough to have plenty of redundancy and are not concerned with surprise failures.
Predictive Maintenance (PdM)
One of the most useful strategies of maintaining equipment and minimizing the cost and impacts of failure is through noninvasive analysis of assets. PdM strategies include:
- Lube oil analysis — send oil samples to a certified lubricant testing laboratory for analysis. The report will include information about the oil’s quality, cleanliness, and changes from previous oil samples. Particulates found in the oil can often be an indicator of a failing gear or clutch, enabling a repair to be scheduled before a catastrophic and costly failure.
- Vibration analysis. Rotating equipment such as bearings can be checked easily to make sure the unit is operating properly. The vibration report will show misalignment, excess friction, and other key items that would indicate a repair or adjustment is needed before a significant failure.
- Infrared thermography. This is an easy-to-use, specialty camera that displays and captures images color-coded by temperature. The tool allows the user to quickly identify high temperatures on rotating equipment and even hot spots within compost piles.
- Ultrasound. A hand-held monitor that detects high-frequency ultrasound and converts it into audible sounds that can be heard by technicians through headphones. A common use includes leak detection and to determine when the correct amount of grease has been placed into a bearing.
These PdM tools help catch problems early to minimize the high cost of unexpected failure. Figure 3 illustrates the relationship between cost and delays when discovering failures. The earlier problems are caught, the more likely they can be remedied more efficiently.
Housekeeping
When developing a maintenance plan, it is critical to consider housekeeping. These tasks are needed to keep the assets operating well — and to keep them safe and easier to monitor and maintain. Regardless of who on staff completes them, they should be identified in the plan and appropriated resources to make sure they are completed regularly.
Housekeeping is very important at a composting facility due to the excessive moisture, dust, and corrosion associated with compost manufacturing. For example, an indoor facility like the IERCF must do periodic washdowns of all equipment to remove built up debris to avoid excessive corrosion. The washdowns may include a temporary lockout and removal of protective covers to ensure thorough cleaning. A procedure to verify the reinstallation of all protective covers must be included before returning equipment to service.
Keep it simple and practical. Remember that all maintenance programs are unique to each facility and that they do not employ all of the technologies on all of the assets. Complete the tasks recommended by the manufacturer, employ proactive and PdM where useful, and maintain a minimum standard of housekeeping. Other options can be explored with and incorporated if useful and appropriate.
Step 5. Develop A Corrective Maintenance Plan
Although it’s impossible to anticipate all the potential failures that can occur at any operation, there are some that warrant development of a plan. For example, if changing the drive motor on a trommel screen is something that happens two or three times a year, it’s useful to develop a plan and “kit” the parts needed for the repair to make future repairs more efficient. Kitting is the action of identifying and preparing all parts needed to complete a repair, so the field technician has everything needed up front.
Step 6. Develop A Spare Parts Plan
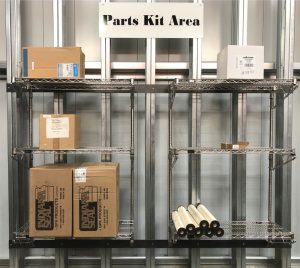
Kitting the parts needed for anticipated repairs ensures that the field technician has everything needed up front to complete the task. Photo courtesy of Inland Empire Utilities Agency
Most projects have spare parts available on-site or on the mechanic’s truck but by developing a spare parts plan, you can be far better prepared for routine repairs and many unexpected failures, saving time and money. Purchasing parts in an emergency can lead to excessive costs to rush parts procurement and shipping. Understanding your critical assets and key components along with the impacts of failure can help guide the spare parts inventory and management system. Parts must be accounted for, documented, maintained, and stored properly to ensure that they remain in good condition and everyone is aware of what is on-hand.
Step 7. Document
It’s critical to document maintenance activities. This is not only for efficiency and cost tracking, but because one of the first things an inspector from the Occupational Safety and Health Administration (OSHA) will request are the maintenance records of a piece of equipment involved in a major accident. Many companies use a computerized maintenance management system (CMMS) — a software package specifically designed to support maintenance activities. The IERCF uses SAP, which allows maintenance supervisors to schedule, track progress, track costs, and summarize maintenance activities. The system can easily accommodate IERCF’s 700 assets including its fleet consisting of: 7 front-end loaders; 2 trommel screens; 7 feed-hoppers; 23 conveyors; 1 water truck; 1 street sweeper; and miscellaneous support equipment.
These software systems are not typically expensive, but can be. If you are considering using a CMMS, it’s best to talk to a colleague who has some experience with the systems to help you determine which features are important to your organization.
Simpler methods are also effective and used in many applications successfully. For example, Microsoft Excel or Access can be great tools to track and document maintenance activities and costs. Creating a paper binder for each asset and inserting maintenance records along with manuals can also be effective. However, paper systems can get significantly cumbersome for larger operations.
In summary, maintenance activities should be carried out according to a plan and documented to allow for periodic reviews to provide opportunities for continuous improvement.
Step 8. Train Your Staff
Training is a critically important part of any successful maintenance plan. Technicians need to know how to perform maintenance and repair tasks, as well as understand how to document their work and to follow plan instructions. At minimum, they should be shown examples of what’s expected and know and understand why the data is being collected. Providing a summary of the data is very useful and assures them that the time spent documenting their actions is important.
One of the most valuable trainings that the maintenance technicians can receive is on lubrication. Proper lubrication practices can preserve equipment and reduce costs significantly. Bearings often fail from over greasing as the excess grease creates friction and blows out dust seals.
Bottom Line
Moving from an informal reactive system to a planned system may seem daunting, but the cost savings and process stability makes the undertaking well worth it. The IERCF team implemented a reliability plan — including many of the concepts discussed — and noticed continuous improvement reducing the backlog of incomplete tasks (from 200 before implementation to the current average of 74), increased schedule compliance from 33 percent to 91 percent, and increased completion of preventive maintenance tasks from 37 percent to 75 percent.
The result is a more reliable facility with a reduction in unplanned shut downs and a reduction in costs. More importantly, the program significantly improved morale by increasing the professionalism of staff and reducing the frustration of process interruptions.
Jeff Ziegenbein, Certified Maintenance Reliability Professional, is Manager of Regional Compost Operations at the Inland Empire Utilities Agency, and President of the Association of Compost Producers (ACP), the California chapter of the US Composting Council. He can be reached at jziegenb@ieua.org.