When effectively implemented, adopting lean manufacturing principles can help improve quality, bring efficiency to production and delivery times, and lower associated costs.
Matt Eul
BioCycle May/June 2019
Composting is a manufacturing process. To capitalize on the growing number of opportunities for compost in the marketplace, producers need to adopt manufacturing processes that are streamlined. “Having spent a significant amount of time visiting customers throughout the world, I believe there are many similarities between the composting industry and other types of manufacturing,” explains Ted Dirkx, applications specialist for recycling and forestry at Vermeer Corporation. “Producing an end product, whether it’s compost or equipment, a manufacturer needs to have a systematic process in place that is efficient and effective at achieving a quality product. To do this, companies need to continue to reevaluate processes to reduce redundancies that can impact the quality of the end product or add additional time or expense.”
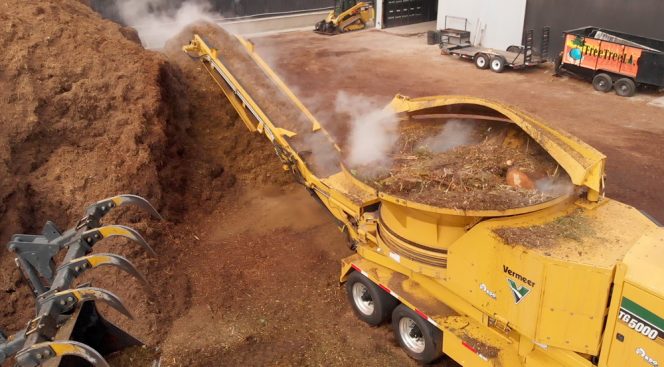
Tweaking the layout of an operation so processing takes place toward the front of the yard (above), and incoming material is unloaded in the back of the yard, reduces the number of times material has to be handled. Photo courtesy of Vermeer Corporation
For more than 20 years, Vermeer has incorporated “Lean Manufacturing” principles to help improve the company’s processes. Dirkx says the most straightforward definition of lean manufacturing is the relentless pursuit of waste elimination. When effectively implemented, adopting lean manufacturing principles can help improve quality, bring efficiency to production and delivery times, and lower associated costs.
“At the end of the day, lean manufacturing is the ability to identify and eliminate waste in the production process,” he says. “I have visited a lot of growing composting companies that are focused on adding people and wheel loaders to keep up with demand instead of looking for ways to improve the setup of their operation. Making a few adjustments to the layout of their operation or adding more application-specific equipment, like a compost turner, can reduce the amount of time they spend moving or flipping material, which can help reduce labor costs, as well as have a positive impact on the quality of their end product.”
Lean Manufacturing Principles
To implement a lean manufacturing process, several basic principles need to be adopted:
• Change in culture — too often companies will adopt the “this has always been the way we do things” attitude. To successfully implement lean manufacturing principles, everyone from management to hourly employees need to be open to change and feel like they have an equal voice in the process.
• Customer-focused
• Growth strategy
• Journey, not a destination
“There are many, many books and trained experts around the world that can help an organization implement lean manufacturing processes,” notes Dirkx. “However, lean manufacturing is only successfully implemented if everyone in an organization is on board with uncovering and subscribing to these production methods to meet the needs of customers. And, it has to be an ongoing process — as customers’ needs change, a company has to be able to adapt.”
Getting Started
The process starts with identifying waste. Company management needs to understand how their employees perform their jobs. Their
work can usually be divided into three categories:
• Value-added work: Includes the manufacturing steps required to transform material into an end product that customers are willing to pay for.
• Non-value added work: Actions that do not effectively contribute to producing an end product, creates waste or consumes resources. Customers typically aren’t willing to pay for non-value added work either. Examples include excessively moving material or producing product that doesn’t sell.
• Necessary non-value added work (i.e., chores): Activities necessary to run the business either to meet regulatory requirements or manage finances and people, as well as maintain machinery and the facility.
According to Dirkx, most companies only spend around 5 percent of their time doing direct value-added work, and another 5 percent on necessary non-value tasks. “The vast majority of employees’ time is spent doing non-value added work so there is a tremendous amount of opportunity for a company when waste is eliminated,” he explains. “Even the most efficient operations still only spend around 15 percent of their time performing value-added and necessary non-value added work. Lost time is easy to overlook but can range from inefficiencies caused by not having a formalized process in place, which can result in miscommunications, not having everything ready to run when people show up in the morning, or underutilizing each individual’s unique skill set. Realistically, it’s impossible to eliminate 100 percent of non-value added work. The real goal is shrinking the time frame to get from point ‘A’ to point ‘B’ without sacrificing quality.”
Identifying Waste
Transportation is one of the main forms of waste that Dirkx sees at composting facilities: “Many composting companies accept material at the front of their yards. As it’s processed, the material moves toward the back of the facility until it is ready to sell. It is then moved back up to the front of the facility. Tweaking the layout of an operation so material is processed toward the front of the yard and asking customers to dump in the back can help reduce the number of times material has to be handled.”
He adds that an effective way to control waste is by setting established visual cues for employees. “Just like the lines in a parking lot give drivers a visual reference, composting companies should establish ways to let their team know what’s expected of them using visuals and standardized operating procedures, Dirkx explains. “It is also helpful to remove any unnecessary items on the jobsite.”
For example, at Vermeer, work areas only have the tools required for that certain part of the equipment assembly and each tool has an assigned place to be returned to when a task is completed. “Simple steps like this help maintain overall efficiencies, because each station only has exactly what is needed to perform the work and it’s easier to identify tools,” he says.
Since Vermeer Corporation first implemented lean manufacturing in 1997, it has held more than 2,700 continuous improvement events, reduced the number of forklifts used at its facility by 33 percent. “Before 1997, a certain machine took on average 52 days and required around 80 hours of direct labor to produce from raw steel to the finished machine,” notes Dirkx. “With the help of lean manufacturing principles, the same machine on the same line now takes around 2.5 days to manufacture. This example just shows what’s possible with lean manufacturing.”
Matt Eul is Senior Product Marketing Specialist in Vermeer’s Recycling, Forestry, Pipeline & Specialty Excavation division.