Nora Goldstein
The Foodbank, Inc. in Dayton, Ohio, an affiliate of Feeding America, services a 3-county area that includes Montgomery, Greene and Preble counties. Each year, Food Research and Action Center (FRAC) releases a study called How Hungry is America?, which provides data on food hardship — the inability to afford enough food — nationally, for every state, the District of Columbia, and 108 Metropolitan Statistical Areas (MSAs) across the country. In 2019, Dayton ranked 42nd among 108 MSAs across the country with 1 in 6 households struggling with food hardship.
More broadly, 32.7% of the population for whom poverty status is determined in Dayton (42,400 out of 130,000 people) live below the poverty line (2019 data), more than double the national average of 13.1%. “A lot of industry in Dayton has fallen away, including a big General Motors plant, and people with high paying jobs lost their income,” explains James Hoffer, Garden & Compost Manager at The Foodbank, Inc. in Dayton. “They have had to rely on our Foodbank.” The situation has worsened due to the COVID-19 pandemic.
Food rescue from more than 80 retailer partners accounted for 3.5 million pounds of food distributed by The Foodbank in 2019. “Our spoilage rates are incredibly low,” wrote Emily Gallion, The Foodbank’s Grants & Advocacy Manager and Caitlyn McIntosh, Development Manager, in the organization’s newsletter in February 2020. “Last year, we only lost about 1% of the food we acquired. However, considering that we distributed over 16 million pounds of food in 2019, even 1% can make a significant impact. Meanwhile, we were also buying compost for our urban garden and paying to remove food waste from our property.”
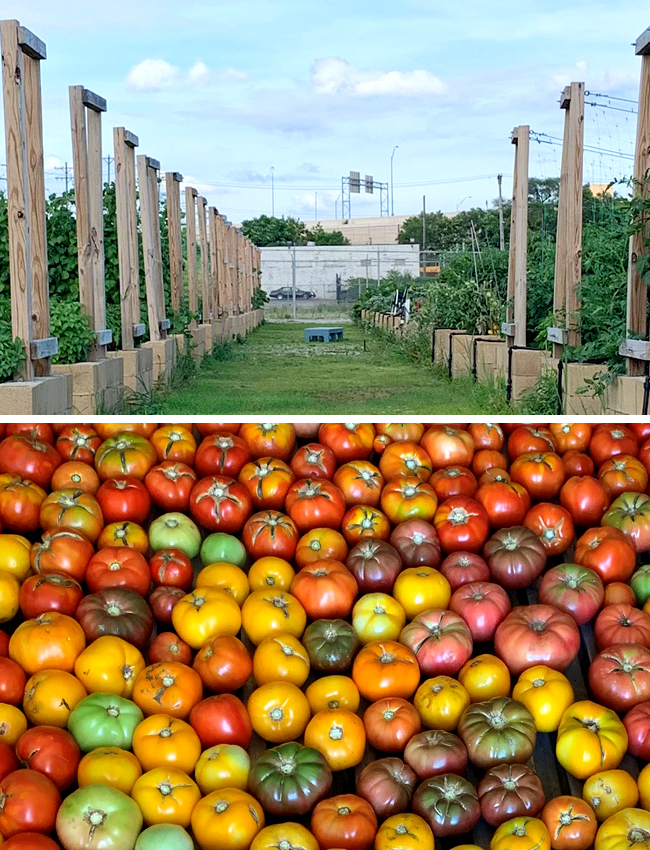
The 3-acre urban garden at The Foodbank, Inc. produces 8,000 lbs/year of produce for distribution. Photos courtesy of The Foodbank, Inc.
The Foodbank has about 500 to 600 lbs/day of spoilage (about 80 to 100 tons/year). It is located in a warehouse adjacent to center city Dayton on an old, 8.5 acre-industrial site, most of it paved. “We considered building a 3-bin composting system but due to our urban location and having neighbors close by, we had concerns about our ability to control odors and rodents,” says Hoffer, who started as a volunteer at The Foodbank in 2015 prior to joining the staff in 2017. “And we definitely had a need for the compost — 3 of those paved acres are home to the raised bed urban garden, which grows about 8,000 lbs/year of produce.”
On-Site Composting
Hoffer researched on-site composting options via the Internet, as well as visited sites with in-vessel units. These included Shenandoah National Park (Green Mountain Technologies Earth Flow with a cart tipper), Akron/Canton Zoo (Big Hanna), and Ohio University (Wright Environmental Services, Inc. in-vessel system). The Foodbank zeroed in on the self-contained Earth Flow in-vessel composter — similar to the one at Shenandoah National Park — with capacity to process 1,200 lbs/day of total feedstock, including food waste.
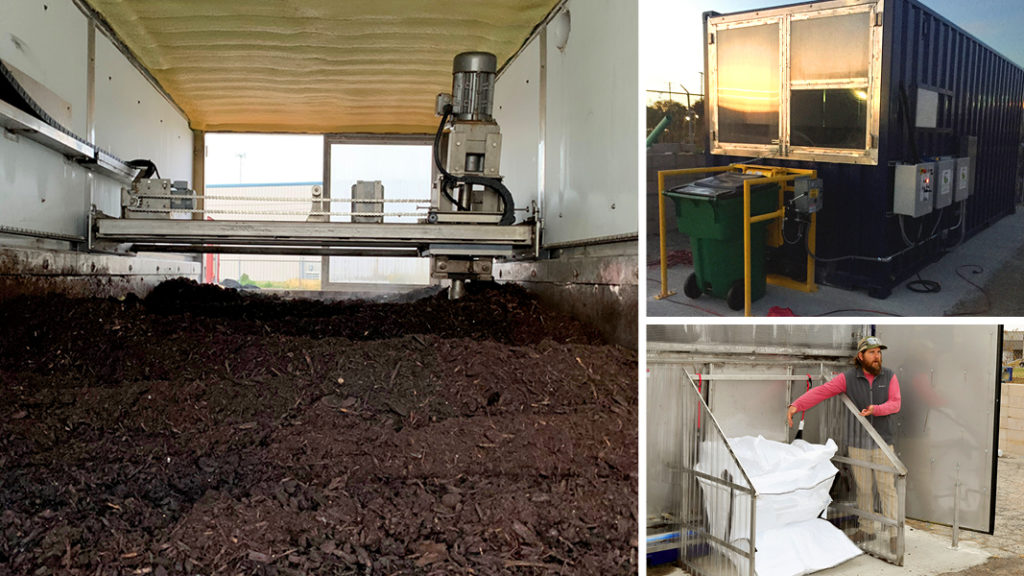
An auger mounted inside the Earth Flow in-vessel composter (above) mixes and helps aerate material. Cart tipper attachment to load the vessel (top right) and 1 cy bags (below right) to receive the compost as it discharges are shown.
The Ohio EPA has grants available through its Recycling and Litter Prevention Program. In 2018, The Foodbank applied for a $95,000 grant, which it received. “The grant covered about 70% of the cost of the Earth Flow, and then we received a 30% match from the Kroger Zero Hunger Zero Waste Foundation, as well as a donation from a private funder,” notes Hoffer. “We added a cart tipper on the loading end and an automated discharge unit on the output end. We also needed to install a pad for the composting vessel and upgrade the electric service. The site, which is adjacent to the urban garden, was already fenced in. A 100-foot access road was built. With everything, we have about $150,000 in the complete project.”
Composting got underway on November 1, 2019. The Foodbank has a Class 2 composting permit from Ohio EPA, which allows it to accept all food types of food waste, yard trimmings, agricultural waste, paper and cardboard, and compostable containers that meet ASTM D6400 or D6868 compostability standards, including those displaying the Biodegradable Products Institute’s “Compostable Logo.” The Class 2 permit requires facilities to register, obtain a license to operate and establish financial assurance. The permit also allows The Foodbank to accept food waste from off-site sources.
“The maximum amount that The Foodbank puts in is about 600 lbs/day, as there is not spoilage on a daily basis,” explains Hoffer. “Since COVID-19, less food is going to waste because demand is higher and we are distributing more at a faster rate. The Foodbank is centrally located in the greater Dayton metro area, which makes it convenient to come here and drop off food scraps. We are setting up a bucket exchange program where people and organizations make a donation to ‘purchase’ a 5-gallon bucket, and we will accept the food scraps twice a week.”
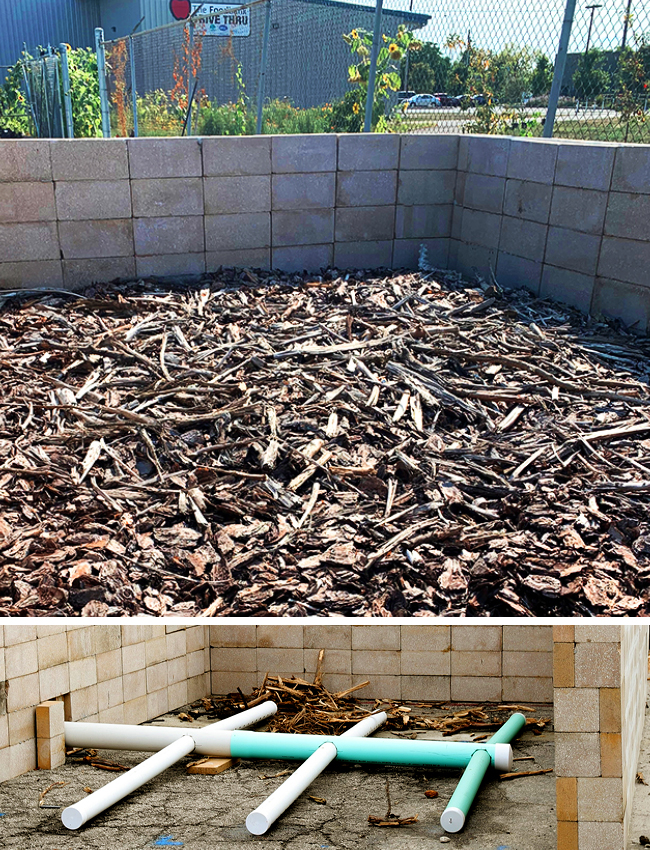
A biofilter built with pine bark nuggets treats the process air coming from the in-vessel composter.
Montgomery County, where Dayton is located, has a yard trimmings recycling program and delivers, free of charge, shredded leaves and wood chips, to the composting operation. Food waste, collected in wheeled carts, is tipped into the in-vessel composter. The shredded leaves and wood chips are added, and the feedstocks are mixed by the auger in the Earth Flow, which is built in a modified, intermodal shipping container (8-ft wide by 20-ft long). There is a stainless steel floor with holes that sits above aeration pipes on the bottom of the container. Air is forced up through the mass (10 minute on/off aeration cycles) and is pulled out by an exhaust blower into a biofilter comprised of pine bark nuggets that is adjacent to the composter. The exhaust blower runs continuously.
Material remains in the Earth Flow for 14 to 21 days, achieving temperatures to meet PFRP requirements (55°C for 3 consecutive days). The compost is cured for about 30 days, currently in 1-cubic yard (cy) construction bags (typically used by homeowners for construction debris). “The compost discharges into the bags, which we have been moving with a forklift that we also use in The Foodbank’s warehouse,” says Hoffer. “This is a temporary set up. We just poured concrete for bays where we will do the curing, and store the compost. The covered, open-sided structure, which costs about $20,000, will have solar panels on the roof that will produce some of the electricity for the in-vessel composter.” The Foodbank also procured a small front-end loader tractor to assist with operations.
Finished compost, which will be stored over the winter, is used in the urban garden. Future plans include distributing a portion of the compost through an extensive network of community gardens and urban farms.
Food Waste Collection, Depackaging
Wheeled carts approved by the American Institute of Bakers — a food safety certifier — are used for food waste collection inside the warehouse. Volunteers do the collection, and any necessary depackaging of donated food wrapped in film plastic or in sealed plastic bags. “My biggest concern when we were considering composting on-site was contamination from the packaging, and how to efficiently remove it,” notes Hoffer. “We rely heavily on volunteers — we have about 7,000 to 10,000 annually — and they were tasked with the separation. As it turns out, that is the most popular and fun volunteer activity, in part because they know that although they were not able to help get this food to people, the compost is used to grow more food.”
Since the Earth Flow started operating last November, 53,000 lbs of food waste have been composted. “Using the in-vessel machine at a foodbank was not something we had seen before, so our project serves as a ‘proof of concept’ to demonstrate how to compost in a parking lot in an urban setting,” he adds. “We got the composter in part based on other community needs, including an urban location to process food scraps as well as a source of compost for those who grow food in the city and donate produce to The Foodbank to distribute. I had to sell the Board of Directors on the viability of the project — the cost savings to The Foodbank’s operation, as well as the ability to accept outside food scraps.”
The cost savings are already apparent, continues Hoffer: “In the past 6 months, we have more than paid for the electricity costs for the next 3 years. The Foodbank was spending $15,000/year for food waste disposal, in addition to trash hauling. We’ve been able to reduce the frequency of our trash collection service — and are saving about $10,000/year in what we had been spending on compost for the urban garden. Repurposing inedible food into something that feeds people is not as difficult as people may imagine.”