California renderer installs digester system to process plant’s wastewater and grease trap waste, as well as additional food residuals streams. Conditioned biogas will fuel collection trucks.
Soren Rasmussen
BioCycle October 2014
North State Rendering (NSR) in Oroville, California was seeking ways to cut operating costs, secure new waste supply contracts and improve wastewater treatment. As a renderer, the company already had permits in place to process grease trap and food waste from kitchens, restaurants and food manufacturers. Rendering those materials is expensive however, which led NSR to evaluate installation of an anaerobic digester. “For a rendering plant, biogas is a natural fit,” explains Brian Gannon of Biogas Energy, the company that supplied the AD system. “Fuel and energy are significant operational costs for the business, so investing in technology that eliminates electricity bills, slashes diesel costs and reduces natural gas usage makes sense.”
The digester system went on line in May 2014. To help finance the anaerobic digester, NSR utilized grants from the California Energy Commission’s Alternative and Renewable Fuel Vehicle Technology Program.
A flexible waste reception configuration enables the facility to process a wide variety of materials, from food and yard waste to high liquid grease trap waste. Materials received include wastewater from the rendering plant, which previously went to a storage lagoon for evaporation, 20 to 40 tons/day of grease trap waste diverted from the rendering process, and regionally sourced organic waste from prison kitchens, food processors and other generators. The facility can receive 100 to 140 tons/day of organic waste.
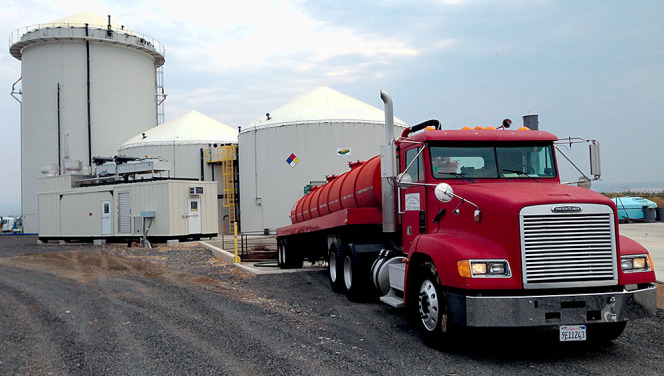
A tanker truck delivers grease trap waste from restaurants in the area to the digester facility at North State Rendering.
Materials reception equipment prepares high solids feedstocks for the digester; a grease trap reception system with an auger and screen separates out contaminants such as plastic and metals. Yard waste is limited to grass clippings (no wood or branches), and is not shredded. Food waste and grass clippings are unloaded into a hopper with an auger that moves material to a mixer that blends these materials with digestate liquids to bring the solids content to a pumpable consistency — about 10 to 15 percent solids. The mix is then pumped through a macerator and on to the digester tanks. NSR also can add dead stock to the digester during warmer months when rendering can become problematic due to extreme degradation of the material. The dead stock will be run through a grinder at the rendering plant. This has not been done yet as the need hasn’t arisen.
Anaerobic Digestion Process
From the reception area, material is pumped into two heated tanks (40 feet in diameter and 24 feet high), where the acid-forming phase of the biogas production process takes place. Next, it is pumped into the main digester tank (64-feet high). “Biogas Energy’s initial design used submersible propeller mixers inside our main digester,” notes Gannon, adding that because those mixers are inside the tank, maintenance requires lifting the equipment out to do repairs, which interrupts the digestion process. “We switched to a Landia digester mixing system, which is mounted externally, so maintenance is much easier. During commissioning, when the AD biology was at a delicate stage, we carried out some tweaks without interruption to the biogas production process.”
In addition, Landia’s (patent-pending) GasMix System is equipped with two 30-horsepower chopper pumps and a self-aspirating system that agitates the entire digester tank, preventing a crust from forming on the top level of the tank’s contents. Digested liquids are pumped to storage lagoons on site for evaporation. Solids are returned to the rendering process.
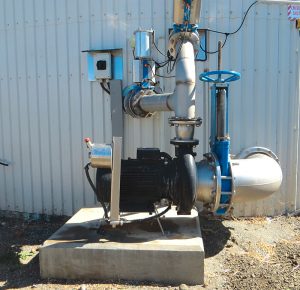
A heavy-duty chopper pump supplied by Landia recirculates feedstock through the GasMix ejector, thereby mixing the digester contents.
The 710 kW CHP engine supplied by Martin Machinery can generate enough electricity to power the entire NSR plant. While interconnections were being made, biogas generated was being fed to a boiler at the rendering plant. A gas-cleaning skid is being installed this fall to create a pipeline-quality biomethane that is then compressed in a CNG fueling station. Trucks are being converted overtime to run on the renewable fuel. The company expects to reduce diesel costs in its truck fleet by 75 percent.
“To start, NSR will run one truck 100 percent on ‘bio-CNG’, and five trucks on dual fuel (bio-CNG and diesel),” says Gannon. “The company will still need to buy diesel as needed for the dual fuel trucks.” Any surplus biogas will be fed to the boiler at the plant to reduce the need to purchase natural gas.
Soren Rasmussen is Director of Landia, Inc, the U.S. subsidiary of Landia A/S in Denmark.