Nora Goldstein
The Town of Bennington, Vermont built an IPS agitated bay facility in 1992 at its wastewater treatment plant (WWTP) to compost biosolids with yard trimmings. The 4-bay Bennington Compost Facility utilizes equipment supplied by BDP Industries. By 2010, biosolids production had decreased to the point where only two of the four bays were being utilized. Based on this, and a relatively low tipping fee, the town made the decision to haul its biosolids to the Hoosac Water Quality District Compost Facility in Williamstown, Massachusetts, about 15 miles from Bennington.
“We dewatered the solids and loaded them into a 40-cubic yard (cy) roll-off container and took them to the Hoosac Water District’s aerated static pile composting operation at the treatment plant,” explains Jon D’Amour, Chief Operator of the Bennington WWTP. “The town contracted for so many wet tons/year to be processed. It was working very well.”
About three years ago, the WWTP began an upgrade to the facility, including its two primary digesters and a secondary one. (Biogas is utilized to heat the digesters.) A contractor was doing the digester upgrades, but the WWTP was responsible for cleaning them out. “We dewatered as much as we could, which increased the amount we were bringing to the Hoosac facility,” says D’Amour. “The next step was to dewater and put sludge into the secondary digester while screens were being added to the primary ones. Without screens, a lot of rags got into the digesters, which became a challenge when cleaning them out. The Hoosac Water District began refusing our loads due to the rags.”
Unfortunately, the contractor fell behind on the upgrades, and the WWTP had to hold sludge in its primary clarifier, which was causing washouts. It had a backlog of about 4,000 cy of sludge. To manage the growing volume, Bennington began sending material in tractor-trailer loads to a wastewater treatment plant in New York State. “The pH of the material was high and it was killing the biology in the facility’s treatment system, so we had to find another option,” adds D’Amour. “We attempted to thicken it so it could go to the only landfill in Vermont, but our material was rejected. We were running out of options, and needed to do something quickly. The economics favored composting. That’s when we began to evaluate restarting the agitated bay composting system.”
Restarting The In-Vessel Composter
That was in mid-August 2019. D’Amour contacted BDP Industries to request assistance to restart the facility within 2 weeks. BDP manufactured the compost agitator, the major piece of equipment used in the facility. “Bennington had been proficient maintaining the facility and equipment during its dormant period,” explains Rich Nicoletti, BDP’s compost systems manager. “It was basically ready to restart with the exception of the biofilter and process control system. The biofilter media needed to be replaced and the process control system required a major upgrade of components that no longer functioned.”
The WWTP replaced the media with fresh wood chips and BDP assisted with developing an alternate operational method that included installing timers on the aeration fans and manually monitoring temperatures to assure compliance with pathogen reduction requirements. The Bennington Compost Facility officially went back into service at the end of August 2019. It processes about 30 cubic yards/day of blended feedstock (6 days/week) — or 5 to 7 wet tons/day of biosolids depending on cake solids. Double-ground brush is used for amendment.
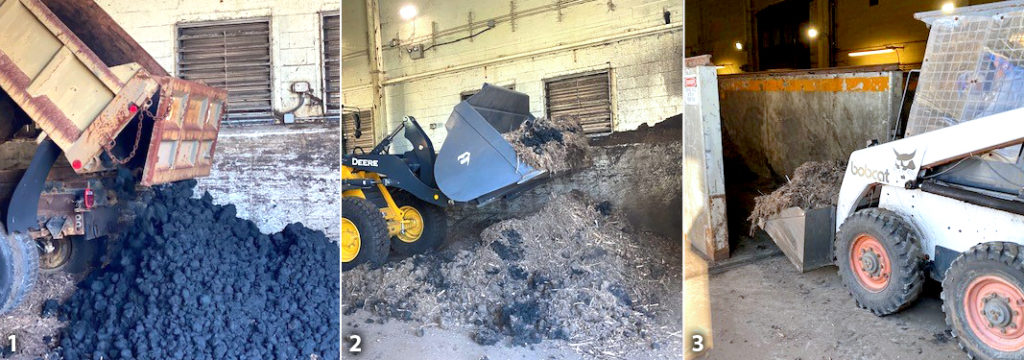
Dewatered solids (1) are mixed with ground brush and finished compost (2) and loaded into a bay for composting (3). Photos by Jon D’Amour
“It just so happened that around the time we were restarting the facility, the town was being required to manage a large brush pile it has,” notes D’Amour. “Particle size is 1- to 2-inches, with some larger pieces and some fines. When we were first operating the facility in the 1990s, we had a mechanical mixer, but sold that when we stopped composting. Now, we mix feedstocks with a bucket loader. Biosolids are fairly wet — about 18.5% to 20% solids. Our recipe is 4 cy of biosolids, 8 cy of wood chips and 8 cy of unscreened, finished compost.”
The bays are 180-feet in length, divided into 5 aeration zones. Each new “plug” into the bay takes up about 12- to 16-feet. Material spends a minimum of 14 days at or above 55°C to meet EPA Part 503 pathogen and vector attraction reduction requirements (PFRP). Curing is done in the bays as well, utilizing the excess capacity from lower sludge production. After compost is discharged, it is put in a storage bin. Samples are sent out for testing to be sure the compost is stable and meets Class A exceptional quality requirements.
The Bennington highway department blends the finished compost with topsoil. It screens the mix, which is used along roadways. No compost screening is done at the wastewater treatment plant. The highway department utilizes all of the compost produced.
Testing Aeration In Negative Mode
The original IPS composting technology utilized in Bennington is designed to operate in a positive aeration mode, with air forced up through the mass via perforated pipes set in stones on the floor of the bays. Building air is captured and treated through a biofilter. “Positive aeration effectively pushes off moisture and all volatiles that come with composting, including ammonia,” notes Nicoletti. “The ventilation system is effective at sucking up the building air and pushing it to the biofilter. But positive aeration corrodes the building faster, and can expose workers to ammonia when they go inside the building. These are all reasons for switching to negative aeration.”
BDP ran a pilot in a portion of a bay at another facility with its partner company, BacTee Systems, Inc., utilizing BacTee’s composting aeration floor technology. The next step was to do a full-scale trial in an entire bay. The Town of Bennington agreed to dedicate a bay for the research. BDP and BacTee developed a retrofit plan to install the aeration floor in the dedicated bay. “The typical floor in our bays is pipe and stone, which makes it challenging for the agitator to scrape the floor without upending the pipes,” adds Nicoletti. “The agitator tends to pack material on the floor, so the ability to scrape the floor when using negative aeration is critical.”
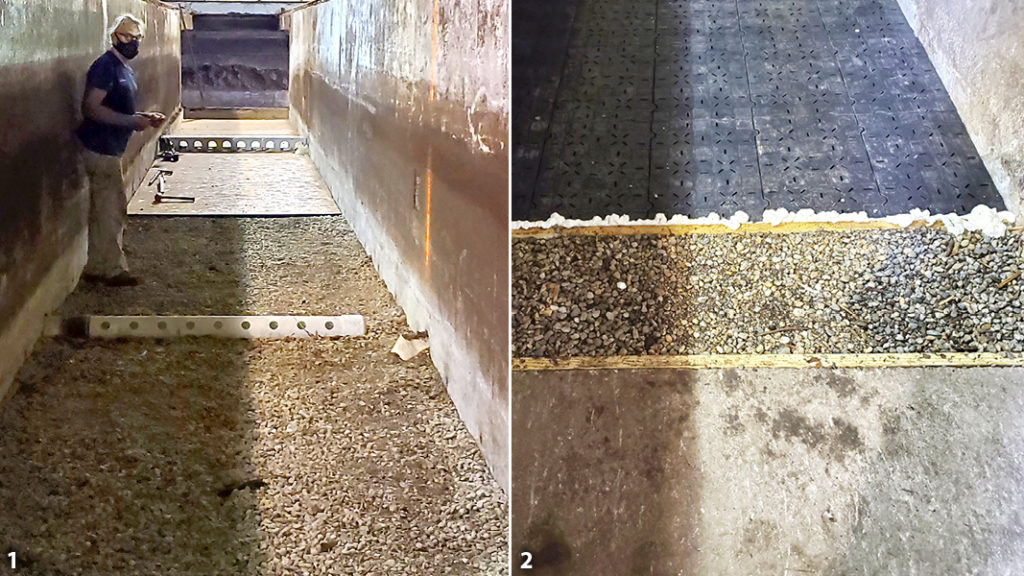
(1) Original bay floor with perforated pipes set in stones. (2) Installation of BacTee Systems composting aeration floor technology. Photos courtesy of BDP Industries
Retrofits started in August 2020, which included installing the BacTee floor in the research bay. BDP installed valves on the blowers in each of the research bay’s 5 zones (A-E) to allow the zone to be easily switched from positive to negative aeration. It started in September with the last 2 zones in the bay (D and E) in negative mode. “The dryer the material is, the easier it is for negative aeration,” explains Nicoletti. “In early October, we switched the valve in C, the middle zone, to negative aeration, and decided to give it about a month to see how it goes. We didn’t have any issues so are now connecting the discharge from Zone C to the suction of Zone B such that we are moving the heat from Zone C into Zone B to aid in achieving PFRP temperatures during the winter months. Ultimately, the plan is to recover heat from Zones C, D and E and pipe it into Zones A and B during the winter.
“The next step in the study, if all goes well and we feel confident we can run Zones A and B in negative mode, would be to do the opposite in the summer months — to take the wet, ammonia laden process air from negatively operated Zones A and B and pipe it to the suction side of positively operated Zones D and E, hopefully assisting in keeping moisture in the compost to keep it active as well as using the compost as a type of biofilter to scrub the ammonia and other gases.”
BDP is taking this opportunity to do some trials with the agitator for the next generation of its machines. “The goal is to lower the energy draw by optimizing the direction of the drum and conveyor rotation such that they work better together,” he says. “We also will test adding scrapers on the agitator to plow the BacTee floor.” BDP plans to publish a paper on the findings of the research trial in mid-2021.