Top: Below grade sparger pipes with risers are under the primary aeration floor at Napa Recycling in Napa, CA. Photo courtesy of Engineered Compost Systems (ECS)
Craig Coker and Tim O’Neill
Editor’s Note: Several years ago, BioCycle’s Senior Editor, Craig Coker, teamed up with Tim O’Neill, a compost science aficionado and president of Engineered Compost Systems, to author a two-part article on compost aeration floor fundamentals, functions and designs. Increasingly, compost manufacturers — both existing and newcomers — are opting to use aerated static piles (ASP) systems to increase throughput on the same footprint, and to improve control of odor and air emissions. This article highlights aeration floor fundamentals covered in the two-part series.
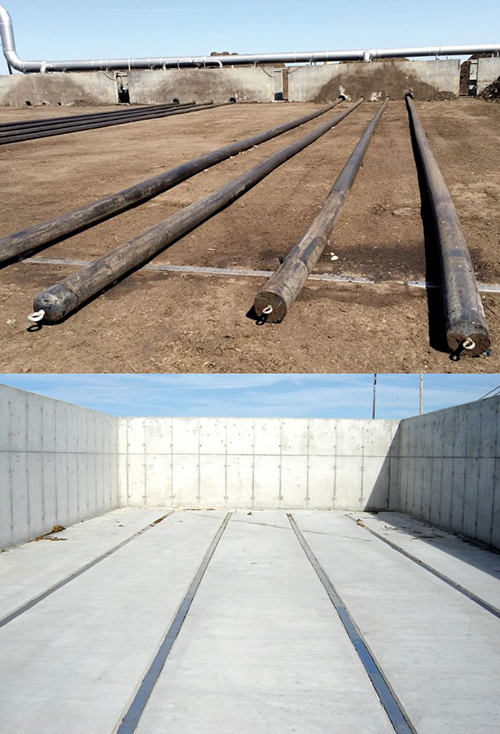
The most common type of aeration floor is a Pipe-On-Grade Sparger (top). In-floor type aeration floors (bottom) are almost always cast in concrete and provide a flat working surface.
Aeration systems for composting come in three basic types: positive, negative or reversing (which alternates between positive and negative). Positive aeration refers to a system where air is forced out of the floor into the material. Negative aeration refers to a system where air is drawn into the floor from the material. Each has its strength: positive aeration is the simplest to implement; negative aeration has the highest air emissions and leachate capture efficiencies; and reversing aeration provides the most uniform conditions throughout the depth of the pile.
There are many variations of aeration floors, but they can generally be organized into the following groups: On-Grade versus In-Floor, and Sparger versus Low Friction. By far the most common type of aeration floor is a Pipe-On-Grade (POG) Sparger. This aeration floor consists of a series of pipes with a designed series of perforations placed on top of the working surface and connected to an aeration system. These pipes are generally pulled from under the pile before it is broken down, then replaced and reconnected prior to building a new pile. A pipe is a sparger if it uses high back pressure across the orifices to overcome the pressure loss along the pipe and thus get semi-uniform air distribution along the length of the pipe.
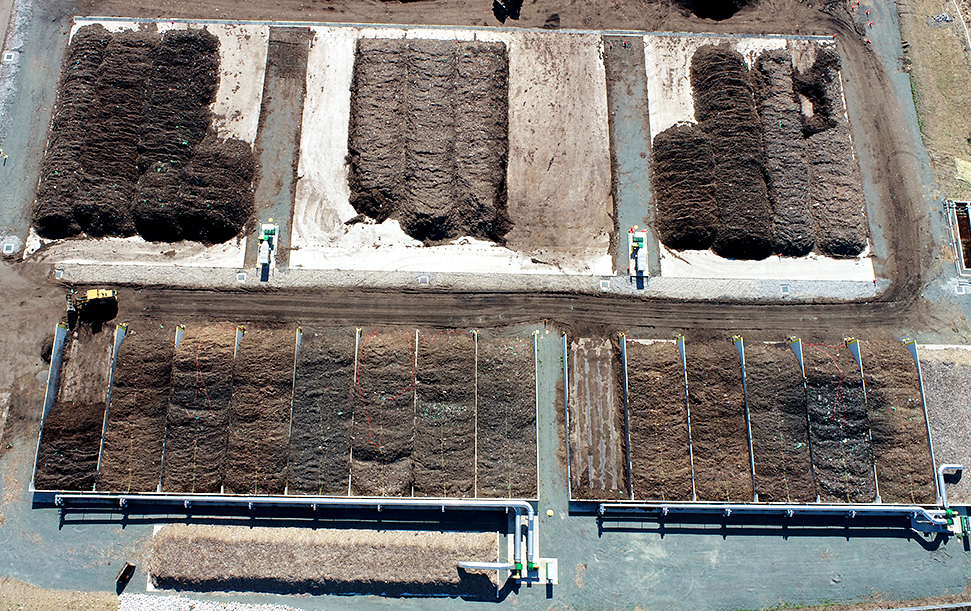
Freestate Farms in Northern Virginia uses trench style floors for primary aeration (foreground of image), and below grade sparger pipes with risers for secondary aeration (top of image). Photo courtesy of ECS
In-floor type aeration floors can be either sparger or low-friction. In either case they are almost always permanently cast in concrete and provide a flat working surface that does not interfere with the wheel loader or require regular operator intervention. An aeration floor is low-friction if it relies on a balanced low pressure design to distribute air uniformly. Low-friction aeration floors require only 25% to 50% of the fan horsepower required for the same airflow from a sparger floor, but they are somewhat more expensive to build.
Aeration Floor Performance Metrics
Five main performance metrics to consider when designing and evaluating an aeration floor include: airflow uniformity, peak aeration capability, ability to manage leachate, ease of operations and maintenance, and longevity. Each is discussed below.
Air Flow Uniformity
Airflow uniformity refers to how evenly the forced air is distributed through the pile. The metric is “maldistribution,” which assigns a percent variation of airflow across the aeration floor (example in Figure 1). While no design is perfect, one of the authors (O’Neill) has measured maldistribution in aeration floors ranging from a high of over +500% to a low of about +10%. Low maldistribution values (<+20%) more readily achieve consistent temperatures and oxygen levels throughout the pile. When air distribution is not uniform, significant areas of a pile’s biology will be inhibited by high temperatures, low oxygen, and uneven moisture levels.
Relatively uniform air distribution can be achieved using a pipe-on-grade (POG) aeration floor in modest sized piles (i.e. less than 90-feet long) by observing a few simple design rules:
- Maximum spacing between pipes should be less than two-thirds the height of the pile
- Ratio of pipe length to internal diameter should be under 150 (e.g., for a 50-foot length of aeration pipe, the internal diameter of the pipe is at least 4 inches)
- Maximum air velocity in the pipe should be less than 2,800 feet/minute
- Total combined area of all orifices are under half of the cross-sectional area of the POG pipe
Peak Aeration Capacity
Peak aeration capacity determines if, and for how long, the temperature in a newly constructed aerated static pile (ASP) can be maintained in the mesophilic temperature range. Generally, food waste/green waste composting mixes start off with low pH due to the buildup of organic acids. Mesophilic bacteria are capable of breaking down organic acids and raising the pH in acidic organic waste. Thermophilic bacteria are strongly inhibited at low pH. ASPs with low peak aeration capability tend to remain above BMP (Best Management Practice, outlined in Part I of original article) compliant temperatures for the first two to four weeks with lasting negative effects. When ASP temperatures during the first three days are controlled by sufficiently high peak aeration rates, mesophilic bacteria are able to oxidize inhibitory organic acids and raise the pH to within the efficient BMP range of 6.5 to 8. At this point aeration can be reduced and the thermophilic bacteria can take over and provide more rapid stabilization and lower odor emissions.
The peak aeration rate required to affect cooling depends largely on the amount of bioavailable carbon in the feedstocks; this tends to be highly variable. Generally feedstocks are most energetic early, but the heat output is not linear and varies somewhat randomly over time and certainly between batches. An aeration system capable of providing adequate peak aeration rates, if controlled with temperature feedback, can keep the process indicators of temperature, oxygen and pH near optimum conditions without overcooling the pile.
Leachate Management
Leachate management is an important aeration floor design consideration since these liquids are highly odorous, carry solids that can clog pipes and sumps, and, if not drained, can saturate the bottom of the piles, inhibiting the biology. The degree to which leachate must be managed depends primarily on precipitation amounts, types of feedstocks and regulations. Collecting these liquids is challenging, since water doesn’t flow under piles very predictably (compost itself forms dams and channels) and the entrained solids require regular cleaning/flushing from wherever they are captured.
All negatively aerated floors (where air is pulled through the pile into the floor) will collect leachate and condensate and require special attention to drainage design. Positively aerated floors leave most of the liquid to pool and run off of the working surface and require more auxiliary drains. However, even positively aerated in-floor systems will collect enough water and solids to be a nuisance and will eventually plug if the design doesn’t allow for cleaning or they are neglected. The bottom line is that leachate will accumulate in all aeration floors and in most applications there must to be a method to capture and control those liquids, and to have access to all below grade components to remove solids.
Operations and Maintenance
Ease of operations and maintenance is the key determinant of the aeration floor operating expenses (OPEX) and reliability. A well-designed in-floor aeration system will have much lower OPEX than a typical POG system, which requires disconnection/removal/ replacement with every batch. Some hybrid POG systems are left on the pad connected and buried in a woody layer while wheel loaders work over the top. In the authors’ experience, these systems have been prone to serious airflow distribution problems, plenum and pipe clogging, and pipe damage (often undetected for long periods of time).
In-floor aeration system maintenance includes flushing and removing solids, and occasional repair of damaged surface floor elements caused by wheel loaders. These floors need to be easily accessible for pressure washing, scooping or suctioning to remove solids. For in-floor sparger pipes, this requires access at both ends of every straight run. For in-floor aeration trenches, the trench covers themselves must be removable. Fasteners for trench covers should be stainless steel with nongalling threads so that they can be serviced over the lifetime of the facility.
Additional maintenance issues associated with a POG system include repairing pipe damaged during pile building and tear down activities, “ovalling” (misshaping) of pipes due to pile temperatures and pressures, and damage to the mechanism that connects the pipes to the aeration system. Large facilities that use POG aeration floors report needing almost one full-time operator dedicated to the repair and replacement of damaged pipe.
Longevity
Longevity is a key differentiator between an in-floor and an on-grade aeration floor. A well-designed in-floor system will last decades while POG systems have far shorter life spans.
The best choice for POG pipe material is heavy walled (DR 11 or 17) high-density polyethylene (HDPE). This material can handle high temperatures, friction, and even the occasional crushing by a wheel loader. The pipe ends should be heavily reinforced to withstand the stress of pulling pipe out from beneath a pile. The typical lifetime of an HDPE sparger pipe is 12 to 24 months. At very small facilities other pipe materials can be considered such as PVC (polyvinyl chloride), ABS (Acrylonitrile-Butadiene-Styrene) or thin walled HDPE, but these pipes should generally be considered disposable as they are not rated for the temperatures encountered and are easily fractured.
If an in-floor aeration system is going to deliver a long service life, suitable materials must be used in its construction. Buried pipe that will be exposed to elevated temperature and/or stress from above should be fused HDPE, which is tough, and not PVC, which is brittle. In addition, aeration components near the working surface need to be offset below that surface to not be damaged by wheel loaders, but not too deeply offset or they will collect material and plug more often. All metal components exposed to compost, leachate or exhaust airflows should be at least 304 stainless steel to hold up to the corrosive environment.
Craig Coker is a Senior Editor at BioCycle and principal of Coker Composting & Consulting near Roanoke, VA. Tim O’Neill is the President of Engineered Compost Systems (ECS), a compost technology provider based in Seattle, WA.