City of Raleigh is equipped to better utilize available acreage to process greater volumes of yard trimmings into high value compost.
Niki Vala and Nora Goldstein
BioCycle December 2017
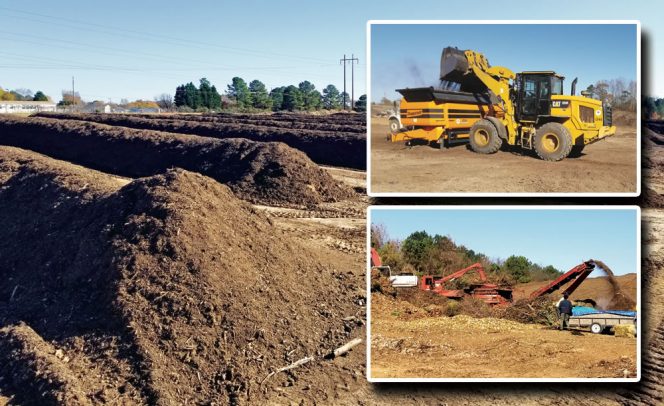
The City of Raleigh’s yard trimmings composting site uses a Morbark tub grinder (top inset) to size reduce incoming materials to a uniform size. Last year, it procured a Doppstadt trommel screen (bottom inset), which “relieved the final pinch point” that would occur when compost was ready to sell.
The site opened in the 1990s when North Carolina passed a regulation banning green waste from landfills. For much of the time since then, the composting facility served as a place to bring the diverted yard trimmings; a minimal amount of processing was done to compost the material. In 2014, however, the city decided to invest more in managing the composting process, and purchased a BACKHUS 21.55 turner. John Ennis, Operations and Compliance Supervisor, was brought on in late 2016 to run the site and improve overall materials management. “When I got here we were only using about 12 acres of our permitted 70, so we have been ramping up quite a bit since then,” Ennis explains. “We average about 40,000 tons of intake annually, but that could be increased dramatically when we have our processes ready for it. Daily tonnage varies with the seasons. During the City’s bulk leaf collection in the fall, we may receive 400 tons/day or more.”
Composting Operation
The facility owns a Morbark 1300b tub grinder and a Morbark 3800 horizontal grinder for reducing incoming materials to a uniform size. Ennis has found that the ideal particle size for the operation is between 5 to 8 inches on the larger woody materials. “This size allows for longer oxygen infiltration without added turning,” he explains.
The consistency of source material helps make each day’s intake fairly predictable, but Ennis notes that the team is still working through the best ratios of carbon and nitrogen to generate maximum yields of compost. “We’re still a fairly new team and are developing our best practices for blending,” he says. “We have plenty of space to inventory material so it allows us the flexibility to stockpile brush until we get more nitrogen on our rows, for example. Our goal is to create the right blend with the proper ratios of carbon to nitrogen. Our ratio runs on the lower end of the spectrum, and in return our composting process isn’t quite as fast as it would be with a more ideal ratio.” The site’s ability to add significant amounts of water to the windrows is limited, which also slows the composting process, which takes upwards of 6 to 8 months, Ennis adds.
In late 2016, a new Doppstadt SM 617 trommel screen was procured, relieving the final pinch point in the operation that would occur when compost was ready to sell. “The Doppstadt had about 25 hours on it when I got here, and we still had the older machine that it replaced on site,” Ennis explains. “The old trommel is probably twice the size of the Doppstadt and generates half as much output. And the new unit is easy to maintain, from the swing-out engine to the hydraulic controls.” Compost is screened to a half-inch minus, and used primarily by city departments and residents.
Positioned For Growth
The City of Raleigh composting facility has been steadily increasing material flow by about 10 percent annually, in part due to the booming housing market in the immediate area. But expansion of operations on the facility’s acreage is also a result of a decision to begin composting material that has been stockpiled on the site. “In the last couple of years, as the compost yard has grown its intake, the process of building and turning windrows had not kept up,” notes Ennis. “As a result, material was simply being stored on the site, even though we have a maximum windrow capacity of over 300,000 yards of actively composting materials.”
Market demand exists for the finished compost, he adds. “The city itself would take more if we could make it. We have a lot of outside customers coming to pick up product that want more. Now that we have proper equipment, we will be able to make mulch and soil blends, too. Creating high-value products, rather than just seeing these materials as an afterthought, will allow us to meet current demand and generate more volume for the future.”
Niki Vala is the Marketing Coordinator for Ecoverse.