Top: Active composting takes place in 12 aerated vessels (aeration piping in center of photo), each with capacity of 2 tons/day. Photos courtesy of Mississippi Topsoils.
Nora Goldstein
Mississippi Topsoils in Cold Spring, Minnesota began composting residuals from a local poultry processor in 1998. The founders, Brad Matuska and Mathias Miller, invested about $500,000 to install a NaturTech in-vessel system on a 5-acre site. The system has 12 composting vessels made from modified steel roll-off containers, each with capacity of 2 tons/day. Three biofilters treat the process air from the vessels.
Over two decades later, the same system is in place, processing about 3,000 tons/year of poultry solids from Pilgrim’s Pride (which previously had been land applied) with an equivalent amount of ground forestry mulch. Miller’s son, Dean, is now co-owner of the company. “The in-vessel system is designed to be foolproof and maintenance proof,” notes Darian Richardson, Mississippi Topsoils’ General Manager. “The equipment has had a fair amount of wear and tear, and some replacement parts, but it is all working well.”
The facility is permitted by the Minnesota Pollution Control Agency to process 9,360 tons of poultry residuals and wood mulch annually, but has maintained a steady flow closer to 5,500 to 6,000 tons/year for many years. “Pilgrim’s Pride’s process requires that a certain amount of the residuals be retained in its wastewater treatment system to keep the biology stable,” explains Richardson. “It is in a nice healthy balance and we expect the amount we receive continuing to be about the same.”
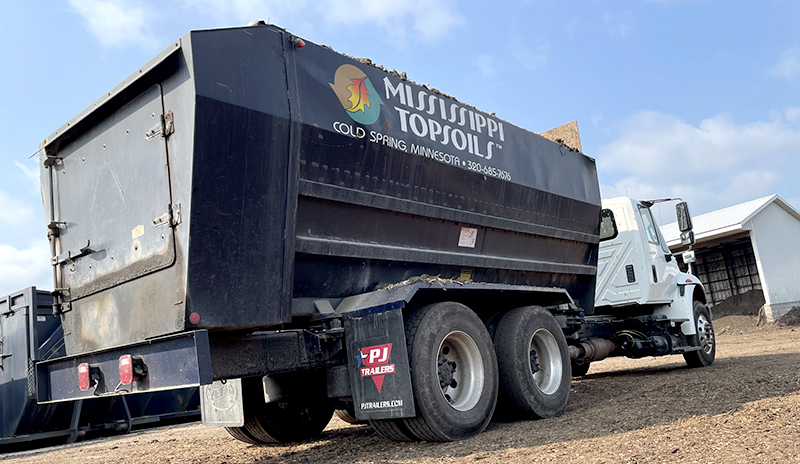
Amendments are placed in a truck-mounted horizontal mixer that goes to Pilgrim’s Pride — located next door — to collect the solids.
Amendments are placed in a truck-mounted horizontal mixer, which is driven to Pilgrim’s Pride — located right next door — to collect the solids several times per day. Forestry wood chips, along with overs from the screening process, are used as amendments.
A BioCycle profile of Mississippi Topsoils in 2015 noted that an early challenge was achieving the right carbon-to-nitrogen ratio. “While there’s a ton of immediately available, soluble nitrogen in the poultry solids, there wasn’t a lot of carbon immediately available in the wood waste, even the sawdust,” Matuska explained in the article. “Much of that carbon is locked up in cellulose and lignin in the wood material — inaccessible to the microbial action of composting because it’s buried inside. We learned we had to run the aeration system at a higher than normal volume of air so we could blow off some of the excess nitrogen, to bring it into balance.”
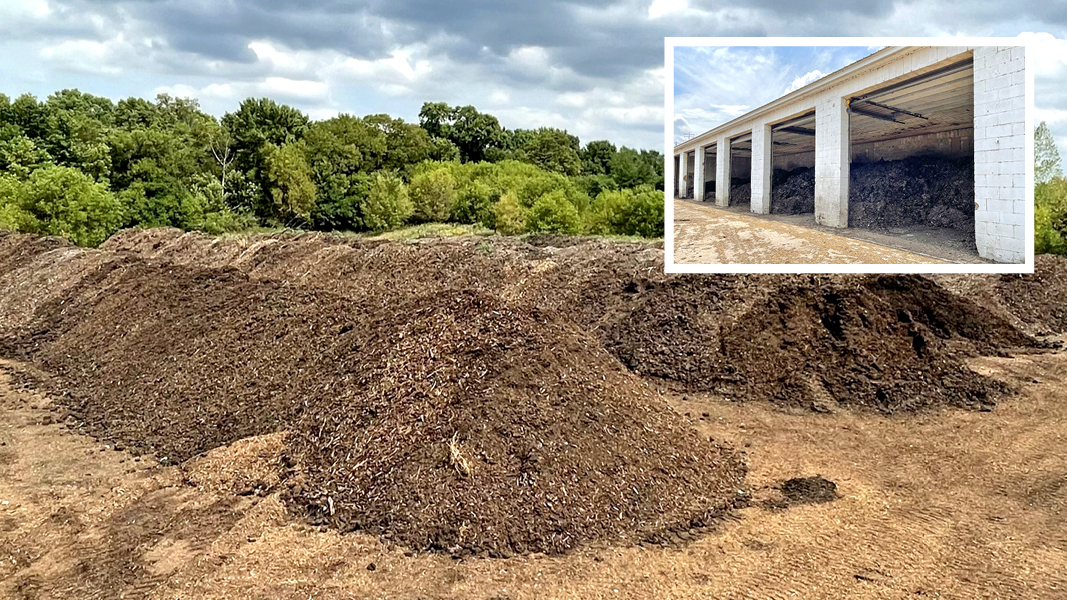
After 2 to 3 weeks in the vessels, the curing phase begins in a concrete building (inset) for about six weeks, followed by outdoor windrow composting for 8 to 10 months of final curing.
The entire process of converting the poultry solids to compost takes about a year. It starts with two to three weeks of in-vessel composting under aeration, which is controlled by continuous temperature monitoring. After the in-vessel composting phase, the curing phase begins in a 30- by 100-foot concrete building for about six weeks. Then the material is piled in outdoor windrows about 200 feet long and 15 feet wide, for 8 to 10 months of final curing. Loaders are used for moving materials and windrow construction and management.
Bagging Blends
An early lesson for Matuska and Miller was that even if you make great compost, people don’t “fall over themselves to buy it,” said Matuska in 2015. “We all need to be better at the sales and marketing side. We found out quickly that, in order to grow the business, we couldn’t continue as a retailer, but needed to become more of a manufacturer.”
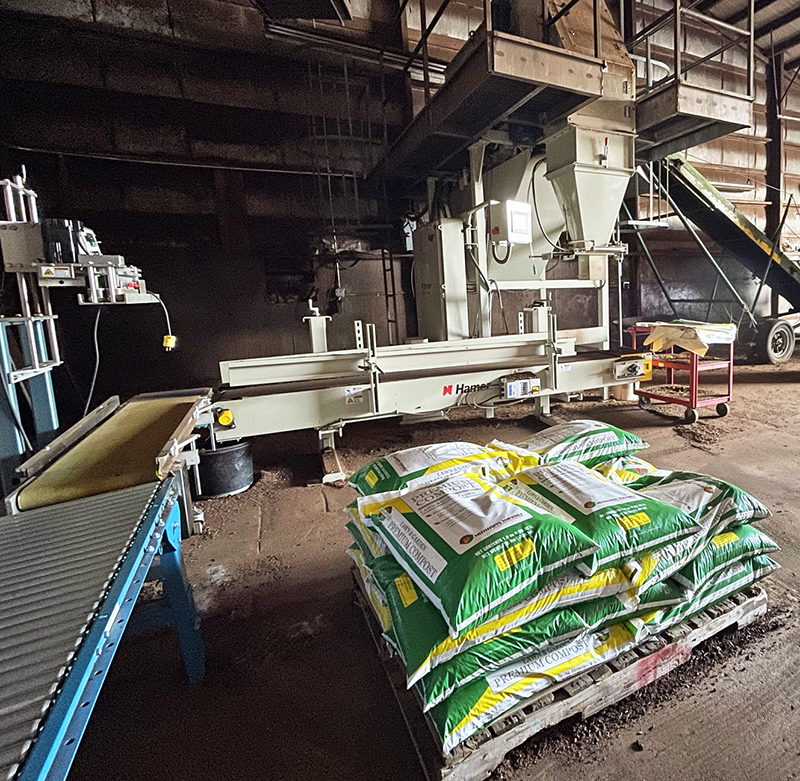
The current bagging line is comprised of a semi-automatic dosing machine and sealer. It is being upgraded to a more automated form-fill-seal system.
Today, Mississippi Topsoils’ Soil Essentials® Premium Soil Products line includes straight compost, a topsoil-compost blend, and a potting soil — available wholesale in bulk and in bags. The company also makes a cow manure compost, processing 160 tons annually in an indoor aerated static pile. Its products, used by certified organic growers, are sold at independent garden centers and greenhouses, as well as through nursery and landscape supply wholesalers.
“The material we get from Pilgrim’s Pride is quite consistent, and our customers appreciate consistency,” notes Richardson. “They know that year after year the products they are buying from us will behave the same way. That is what builds customer loyalty. We’ve been approached about accepting different feedstocks for composting over the years but typically decline. It would have to be quite an impressive, consistent product to make a change that would be as consistent as what we have now.”
Mississippi Topsoils’ customer base has been expanding, with more nurseries requesting customized blends for what they are growing, and more retail customers discovering gardening during the pandemic who are in need of quality soil products. A loader is used to make the planting soil and potting mix blends; about 120 cubic yards of products are blended at a time.
Bagging is done by hand using equipment from Hamer-Fischbein, a Minnesota-based company. The line includes a semi-automatic dosing machine and sealer. Mississippi Topsoils has been hampered by the speed of the bagging line — with customer demand outpacing the capacity to fill the bags. “We’re upgrading to a more automated form-fill-seal system that does the dosing and sealing, and the bags come from roll stock,” says Maija Eickhoff, who recently joined Mississippi Topsoils as the Operations Coordinator. “In the future, we will incorporate robotic palletizers.” The line is rated to fill 32 bags/minute, but the speed will be impacted by the blends going into the bags.