Top: Packaged food waste (inset top, left), Reinford Farms (center), raw manure (inset bottom, right). Photos by Nora Goldstein and aerial courtesy of Commonwealth Media Services
Nora Goldstein
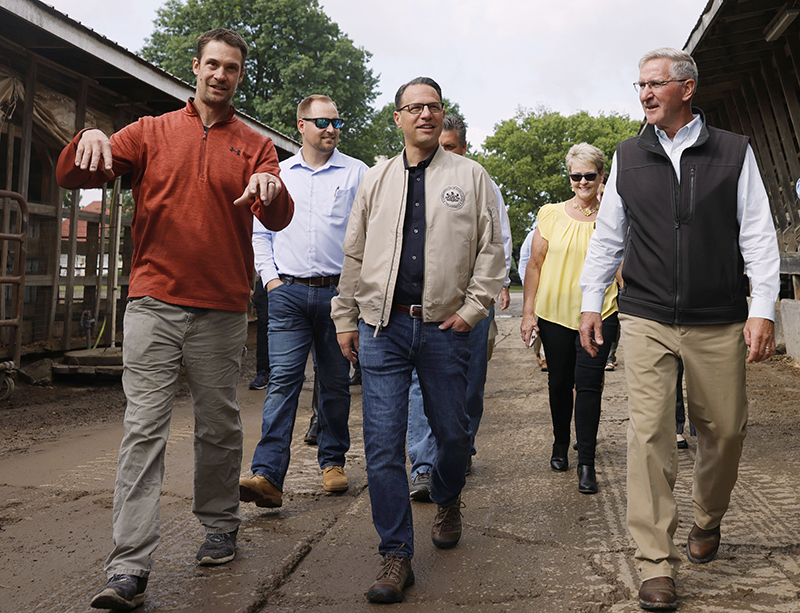
Brett Reinford (left) with Pennsylvania Governor Josh Shapiro (center) and Secretary of Agriculture Russell Redding (right) during a recent tour of Reinford Farms. Photo courtesy Commonwealth Media Services
Reinford Farms in Mifflintown, Pennsylvania began receiving food waste to add to its dairy manure digester in 2008. The farm, which currently milks about 750 cows, installed a 526,000-gallon complete-mix anaerobic digester in 2008 that was supplied by RCM (now known as Martin Construction Resources (MCR)). “That digester was not sized to take food waste,” says Brett Reinford, the farm’s business manager. “But as soon as the digester was built, we received a call asking if we could take food waste. We said yes, and within a year, we had maxed out the digester’s capacity.”
The food waste — mostly produce from Sam’s Clubs and Walmart stores in the region — was emptied into a holding pit and then loaded into a grinder. “My dad took a forage chopper and revamped it to suit our needs,” he explains. “The food waste was ground for 30 to 45 minutes and then added to a concrete gravity-fed influent tank where it was mixed with manure.”
As Reinford Farms started to pick up more food waste clients, it began exploring the option of adding a second digester. “We wanted to be confident we had the food waste flow before we made the investment,” says Reinford. The second digester — also purchased from MCR — began operating at the end of 2019. It is about three times the size of the first (1.5 million gallons). Earlier in 2019, the original digester caught fire, blowing its top off. It was an old-style design with the mixer motors mounted on the cover. Methane was escaping from the cover and sparks from the motor ignited the methane. The motors for the mixers are now submersed in the manure of the original digester as well as the new one.
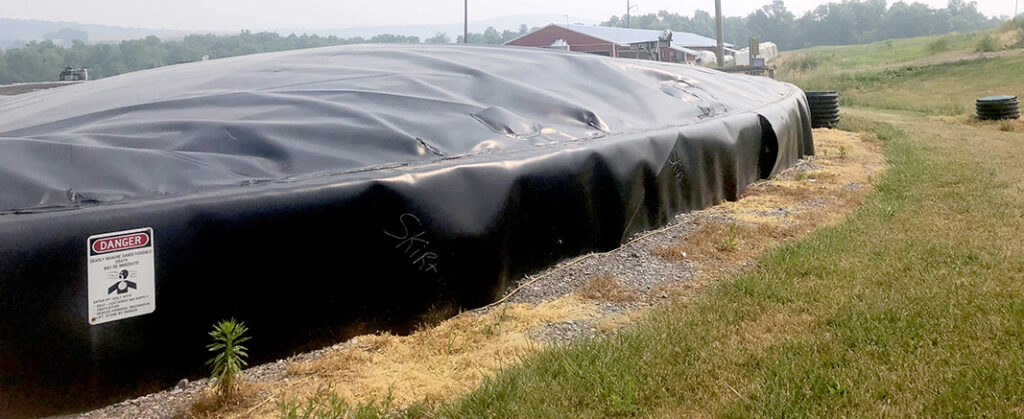
The second digester installed at Reinford Farms, with capacity of 1.5 million gallons, began operating in 2019.
Several other modifications were made when building the new digester. A 50,000-gallon tank to hold food waste was installed to better control the amount being added to each digester. “We had no way to balance that previously when the food waste was being mixed with the manure in the influent tank,” he adds. “We also installed new mixers and pumps that are more equipped to deal with the thickness of the food waste in the digester. When the cover came off our original digester, we saw about 50% solids, when it should have been more in the 10% to 12% range. We believe some of the grains and minerals that we were feeding the cows settled to the bottom. We were not able to suspend the sand-like grit that was found because we did not have reliable mixers.”
Food Waste Flow
Over the years, as it was receiving food waste, Reinford Farms saw an increase in the amount of contamination building up in the digester and the storage lagoon. “We decided to clean up the food waste we were getting and started looking at depackaging equipment in 2015,” notes Reinford. “We purchased a Scott Equipment Turbo Separator in 2017.”
The Reinfords built a 5,600 sq. ft. warehouse that serves as its food waste receiving and storage facility. It also houses the depackager. Most of the food waste received is in packaging; only liquid food waste arriving in tanker trucks is unloaded directly into the food waste storage tank. “We have modified a couple things on the depackager since we acquired it,” he says. “And we’ve learned that how we run the machine is a big factor — if we run it aggressively, we end up with some contamination in the slurry.” The screen on the depackager is three-eighth inch; the original screen size was three-quarter inch. The smaller screen size significantly helps with contaminant removal.
Corrugated boxes are unloaded and recycled, along with other recyclables that can be recovered after going through the depackager. Since 2017, Reinford Farms recycled 400 tons of aluminum. Waxed corrugated is baled and sold to a company that makes fireplace logs. Revenues from sale of recyclables since 2017 is about $500,000.
Over time, most of the grocery store produce Reinford Farms had been receiving was being diverted to animal feed. Currently, around 90% of what is depackaged are liquid or semi-liquid products. “The liquid stream has the highest margin from both a tipping fee and a biogas generation perspective,” explains Reinford. “The liquid stream is expensive to take to a landfill, so most generators are willing to pay the tipping fee we charge. Digesters are a perfect fit for liquid and semi-liquid feedstocks. A bonus for us they don’t add solids that can fill up our digester. In terms of biogas production, we process a lot of sugary drinks.”
The farm hauls about 80% of the material coming into the depackaging facility. In many cases, its trailers are parked at the generators’ operations. It works with food waste brokers that notify Reinford when loads need to be picked up. Almost all incoming food waste loads are contracted through the brokers, eliminating the need for someone on staff to source feedstocks. The farm’s “food waste shed” is in eastern Pennsylvania and northern Maryland.
The depackaging facility operates 24/7 to keep up with incoming feedstock. In 2022, Reinford Farms processed 35,000 tons of packaged food waste. Nonrecyclable packaging residuals comprise about 12% of the total volume of food waste received; the typical residuals’ rate at food waste depackaging facilities is 30% or more, says Reinford. The farm plans to apply for a permit to expand the square footage of the receiving building.
The farm beta tested Scott Equipment’s new mechanical screening system (Cleansweep), designed to remove contamination that remains in the food waste slurry. “It was impressive with the liquid products that we get a ton of,” notes Reinford. “For example, we received 120 loads of water bottles. The labels on the bottles shred during depackaging and are in the slurry. The Cleansweep was very effective at removing that contamination.”
Digester Operations, Biogas
The farm has two million gallons of available digester capacity, and typically operates on a 30-day retention cycle. That cycle can be increased to 50 days if more capacity is needed to process materials. Roughly 125 to 150 tons/day of food waste and manure from 750 cows are fed into the digesters — roughly two-thirds food waste and one-third manure. “We do not accept grease and fat in order to maintain an optimum pH level in the digester,” explains Reinford.
The two digesters produce about 360,000 cu.ft./day of biogas. The farm has a 499 kW MAN combined heat and power engine and needs to purchase a second engine as it is having to flare a lot of the biogas. When BioCycle featured Reinford Farms in October 2020, it was selling the power to PPL Utilities for 6 cents/kW, which was about half of what the utility had been paying. Now, the rate is 14.5 cents/kW because PPL has raised the rates it charges its customers. Renewable Energy Credits are sold for 2 cents/credit.
Reinford Farms was hoping 2023 would be the year that the U.S. Environmental Protection Agency would activate the electric RINs (eRINs) pathway in the Renewable Fuel Standard (RFS) as part of the 2023-2025 RFS rules updates. The eRINs are credits created by utilizing electricity generated from biogas to charge electric vehicles. EPA released the final ‘SET’ rules on June 21 and did not include the e-RIN pathway. “It is was a disappointing ruling,” says Reinford. “It’s a major setback for anyone that is considering installing digesters and for those trying to maintain the financial viability of their existing ones.”
Digested manure passes through a solids separator with a 1 millimeter (mm) screen. The solids are used for bedding the cows, and the effluent is piped to a 2.5-million-gallon lagoon. “We are building a new covered lagoon, which will store about 10 million gallons,” says Reinford. “We produce about 40,000 gallons/day of effluent, and are permitted to spread 20 million gallons/year on the 1,400 acres we farm. We’ve been seeing a lot less trash in the lagoon since we tweaked the depackaging process.”
In 2022, Reinford Farms did not have to purchase any synthetic fertilizer, a cost savings of $300 per every 6,000 gallons of effluent applied. The value is usually around $200/6,000 gallons. In addition to having less odor than undigested manure, the liquid is much easier to land apply because the solids have been broken down during digestion.
Research is being conducted at the farm on the benefits of mixing switchgrass with the bedding that ultimately ends up in the digester to boost biogas generation and establish a more balanced pH. Results are not yet available.
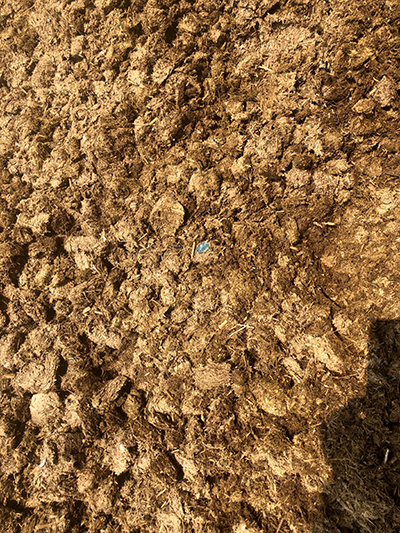
Even after passing through a 1 mm screen, some plastic contamination is still visible in the digested solids.
Even after passing through a 1 mm screen, some contamination is still visible in the digested solids. The Reinfords are assessing the benefits of producing a biochar from the solids, and then adding the char into the digester. “We are starting a study with Penn State University soon with some biochar that we have,” says Reinford. “The hope is that it increases gas production and generally helps with the health of the digester. There is evidence on a small scale that says it does. My other thought is if we install a biochar system on our farm and char our solids, that would effectively eliminate all the plastic fragments that escape our depack. Then we could use the char as a solid amendment in our fields. I think it would solve one of the most glaring issues with a depackager — the microplastics. It’s just a theory but I think it would work well. The downside is that digested manure solids are a very good bedding with very little bacteria. We are just not sure how to get the plastic out. We would have to buy sawdust to use as bedding, which is a tradeoff monetarily, but the plan is to make up for it by having higher value end products to sell.”