Nora Goldstein
Prince William County, Virginia’s Balls Ford Road Compost Facility in Manassas has been processing yard trimmings, garden debris, and leaves from the surrounding community since 1994. In 2015, the county awarded a 20-year contract to Freestate Farms, LLC to run its Balls Ford facility.
As part of the contract, Freestate Farms would finance, build, and operate an advanced composting facility that improved the county’s ability to process yard trimmings and added the ability to compost new food waste streams. Prior to the new facility, the site composted about 30,000 tons/year of yard trimmings and some preconsumer vegetative food waste. Material was ground, placed in 20-foot high windrows that were turned with an excavator and front-end loaders, and then finished by trommel screening. Because some jurisdictions in the region that tip at the facility allow residents to put yard trimmings in plastic bags, it was difficult to produce a consistent, high quality product.
Construction of a 14-bunker aerated static pile composting system got underway in earnest in the beginning of 2019. The system, designed by Engineered Compost Systems (ECS), also includes a “mass bed” aerated curing pad. “At the end of November 2019, we stopped accepting commercial loads at Balls Ford and redirected them to the county’s landfill, where we set up a temporary composting operation,” explains Douglas Ross, CEO of Freestate Farms. “That helped facilitate construction logistics and progress while ensuring that we could continue to serve the local community.”
In mid-August, the first bay of the new composting facility was loaded and material is now being redirected back to Balls Ford. “With the completion of Phase One construction, our capacity is now roughly 80,000 tons/year, with one-quarter of that capacity allocated to food waste,” says Ross. “This will allow us to almost triple tipping capacity and compost production, while also providing a new location for food waste processing in the region.”
Preprocessing And Composting
Incoming food waste and yard trimmings are unloaded in a partially enclosed tipping/preprocessing building adjacent to the bays. After removing obvious contaminants, materials are put into a stationary Crambo (Komptech) shredder that opens bags of organic material and feeds a 3- to 4-person picking line. The line, supplied by Sparta Manufacturing, is equipped with magnets, suction tubes, and sorting containers. “We chose equipment that would let us effectively and efficiently process a wide variety of inputs,” notes Ross. “Residential yard trimmings and food waste frequently arrive in plastic bags and sometimes contain noncompostable materials. We wanted a process that would let us remove these items at the front end rather than continuing to try to screen out at the back end.” From the pick line, material goes into a large tub mixer (from ECS) that blends various inputs and adds leachate for moisture. The resulting mix is then placed into the bunkers.
From the bunkers to a finished product, the total retention time will be about 40 to 45 days, with potentially another 30 to 45 days of curing. Material remains in the bunkers for 15 to 18 days, on the aeration pad for the next 20 to 30 days, and then cures in windrows on a dirt pad prior to final screening. The bunkers are designed for positive and negative aeration, while the mass beds provide positive aeration only. “This allows us to closely control the temperature for ideal decomposition while also minimizing any odors,” explains Ross. “In fact, the bunker process is most frequently using negative aeration and that air is deodorized through a biofilter before being released.”
Originally, Freestate was going to achieve PFRP (Process to Further Reduce Pathogens) in the bunkers, but then decided it would use leachate, which is being collected in a leachate pond during the bunker and mass bed steps, to add moisture to the bunkers during active composting. This enables the site to be more environmentally friendly because it reduces overall water use as well as leachate disposal. As a result, PFRP (55°C for a minimum of 3 days) will be achieved while the compost is in the mass beds.
ECS used 3 different types of concrete aeration floors at the Balls Ford Road facility, each specialized for its purpose: a low pressure trench style floor for reversing high aeration rate primary composting bunkers; a low pressure suspended floor for the biofilters that scrub the exhaust air from the bunkers; and a sparger type floor for the positive aeration mass bed used for secondary composting. All of the floors are designed to minimize fan power consumption. “These designs dramatically lessen the amount of energy needed to operate composting system,” says Ross. “It was important to us that we create a facility that would create high quality compost while also minimizing the region’s and our own environmental footprint. The result is this state-of-the-art system and the best management practice processing techniques that we are employing.”
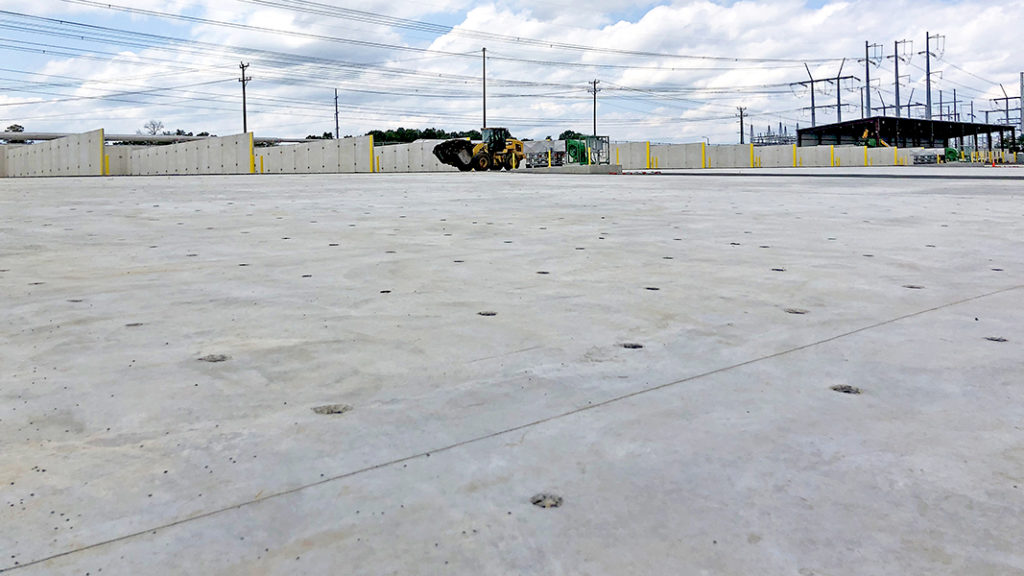
Newly built sparger type floor for the positive aeration mass bed used for secondary composting (foreground). Active composting bunkers and preprocessing building (on far right) are in the background.
Ramping Up, and Looking to the Future
Freestate Farms has begun marketing its new food waste processing capacity to local generators, waste brokers, and public agencies after having first operated the new system with its existing yard trimmings and preconsumer vegetative food waste feedstock. “We expect to receive at least 20,000 tons/year across the full spectrum of food waste — institutional and food manufacturing, commercial and residential,” notes Ross. “Our Balls Ford facility includes a county ‘convenience’ center where residents self-haul their recyclables and trash. This area will now include a food waste drop-off, which is a great way to help grow community awareness and participation.”
Local generators have asked to tip loads containing certified compostable products at the new facility, and Freestate will try processing a few loads with these materials and then run the screened overs through the sorting line. “This will let us see how well various compostable products break down and what steps we can take in our process to also convert them into high quality compost,” he adds.
Freestate Farms has a variety of markets for end product sales in its local metropolitan region, which includes northern Virginia, Washington, D.C., and nearby Maryland. One end market that is top-of-mind for Ross is storm water management, where compost can be used in engineered soils for green infrastructure as well as compost blankets and socks. “Using compost in these projects can help jurisdictions meet their Total Maximum Daily Load Allowances, which were created to preserve and improve water quality,” notes Ross. “I’m excited that we can be part of improving the quality of the Chesapeake Bay watershed.”
Looking forward, Freestate’s agreement with Prince William County also includes Phase II project development, under which Freestate will further expand the facility’s processing capacity, with a particular focus on managing food waste. While the details are not yet public, the facility will also include renewable energy generation and an integrated indoor organic food production system. “We are very lucky to have such good partners in Prince William County and the Solid Waste Division in particular,” adds Ross. “They have been great to work with through contracting and Phase I development, and we are excited to build upon this foundation and move on to Phase II development in the months ahead.”