Connecticut composter transitions to solar-powered aerated static piles to expand composting capacity and improve process control.
Dan Emerson
BioCycle November 2015
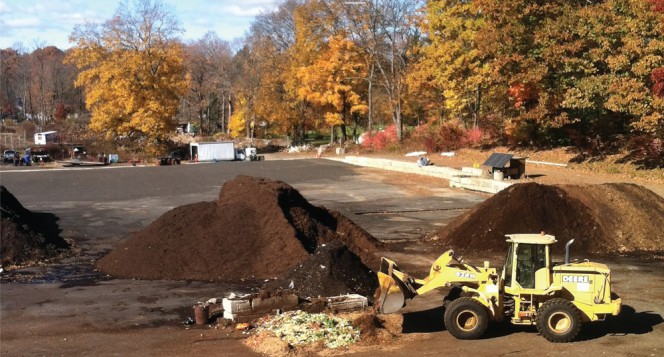
Food scraps are unloaded on a bed of horse manure to absorb liquids. Carbon is then added in the form of wood chips, leaves and/or additional manure and the materials are mixed with a front-end loader.
New England Compost in Danbury, Connecticut was founded in 2001 by Jeff Demers, a landscape professional, who initially focused on mulch production. He began composting yard trimmings in 2003. “Over the next few years the demand for our compost outpaced our soil products and eventually our mulch products,” recalls Demers. More recently, when the State of Connecticut’s organics diversion law took effect in January 2014, the company expanded into food scraps collection and composting.
Very few of the company’s food waste clients are required to participate in a diversion program as a result of the first phase of the Connecticut law going into effect. The law covers generators producing 104 tons/year or more of food waste and located within 20 miles of a processing facility (composting or anaerobic digestion). In 2020, the threshold drops to 52 tons/year. “About eight percent of my customers are covered by the new law,” says Demers. “In terms of developing food waste clients, I have more success signing up schools and institutions that want to do composting, as opposed to being required to do it. We also have clients who are source separating because they know they will have to do it by some point, and they want to get a good head start, to make it easier when they have to do it. The new law is helping our food waste business grow. We’ve found the key is providing good service and open communication.”
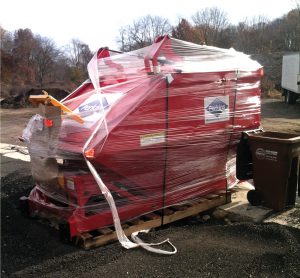
New England Compost purchased a
SAT 6 Collection Unit with 6 cubic yards of capacity from Perkins Manufacturing. The unit, which includes a tote lifter, is being installed on a 20-foot flat bed truck. Photo by Jeff Demers
New England Compost uses 32-gallon, wheeled totes made by Cascade Engineering for food scraps collection. Demers started out using a 16-foot box truck with a lift gate and swapping out clean totes for full ones. “That has become impractical with our growing customer base,” he explains. “We just purchased a SAT 6 Satellite Collection Unit with 6 cubic yards capacity from Perkins Manufacturing, which includes a tote lifter. I’m installing it on a 20-foot flat bed truck. The unit takes up approximately 10 feet, which leaves 10 feet available for extra totes, a water tank and a pressure washer. We will start using the SAT 6 in mid-November.”
The collection route started out with a half-dozen local private schools, with new customers being added gradually. Some generators use compostable cart liners, although Demers does not supply them. This past summer, New England Compost also began accepting organics under a pilot project from five area supermarkets — two Shop-Rite stores in Norwalk and Stamford (material is delivered to Demers’ facility), and three Adams Hometown Market stores in Watertown, Terryville and Thomaston. Adams plans to add three more of its stores to the pilot this fall. Demers also will be adding Danbury Hospital as a client. The most distant food waste pick up is about 25 miles away from his facility.
In August, New England Compost succeeded another vendor as the composter for the Town of Bridgewater’s residential food scraps (which is transitioning from curbside collection to a drop-off program), and also expects to start processing organics from the Town of Ridgefield, which is launching a residential food scraps drop-off program in mid-November. The residential food scraps programs have been initiated by the towns in collaboration with the Housatonic Resources Recovery Authority (HRRA), a regional waste management and recycling authority serving 11 municipalities in western Connecticut. Demers provided a dump truck full of compost for HRRA’s annual spring compost giveaway this year. “He’s been very generous offering us compost back as part of the program,” says HRRA Executive Director Jen Iannucci. “The residents loved it.”
For now, he makes several cold calls per week to drum up new business. “New England Compost is a smaller operator than the other food scraps haulers and composters in the region, which is an advantage in dealing with some clients,” explains Demers. “We are more hands-on, easier to contact and most of all, they’re supporting a Connecticut-based business. Many of the generators, from grocery stores to the many private schools we collect from, like knowing where their food waste goes, and how it’s composted, and the fact that they are supporting the local economy. In addition, some clients like dealing with one company for collection and composting, so if there is a tote or contamination issue, they can call us or we can contact them directly, as opposed to having a garbage hauler bring it to our or their attention.”
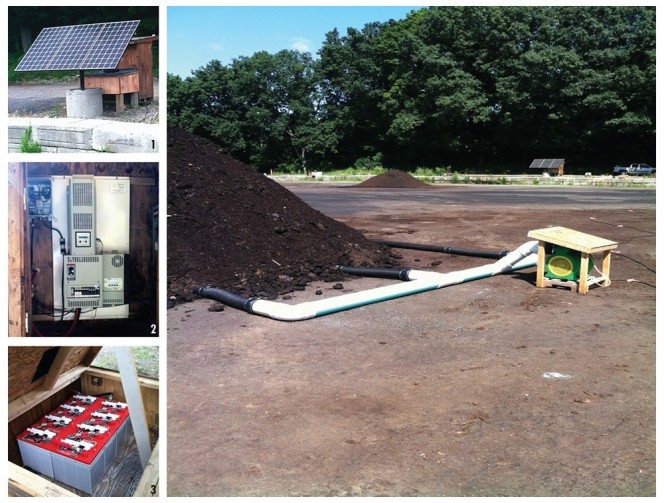
A 1.5 horsepower blower is hooked up to aeration pipes (above). The blower is powered by solar components, supplied by Apollo Solar, that include 3 LG 275-watt monocrystalline panels (1), a prewired panel (2) and eight 6-volt deep cycle batteries (3) housed in a box that can accommodate additional batteries as the ASP system is expanded. Photos by Jeff Demers
Solar-Powered ASP
New England Compost currently handles about 10 to 12 tons/week of food waste. Overall, the facility is permitted to receive 5,000 cubic yards annually of organics. “I’m growing the business at a moderate pace to adapt and stay ahead of growing demand we have for collecting more food waste,” he says. In addition to food scraps, Demers composts horse manure containing wood shavings, and leaves and other yard trimmings dropped off by local landscapers.
The composting site has a surface paved with “road millings” (ground asphalt) to receive the food waste. A layer of horse manure is spread first to absorb any liquids from the food waste that is unloaded over it. After visual inspection for contamination, carbon is added in the form of wood chips, leaves, and/or additional horse manure and the materials are mixed with a front-end loader. “I compare my mixing method to layering a cake,” notes Demers.
As part of the expansion into food scraps, New England Compost switched from using windrows turned by a front-end loader to solar-powered aerated static piles (ASP). “Switching to the ASP system allows more space for composting as it occupies a smaller footprint,” he adds. “It also allows us to stockpile other materials that we use to make different soil blends, whereas before, space was limited and we’d have to purchase materials on an as needed basis.”
The 240-volt, 60 hz system currently consists of eight 6-volt, deep-cycle golf cart batteries, and three 275 watt monocrystalline photovoltaic (PV) panels. Designed by Apollo Solar in Bethel, Connecticut, it can power one 1.5 horsepower (hp) blower, explains Demers, who has invested about $15,000 in the new technology. “I will be switching soon to six 315 watt monocrystalline PV panels and should be able to run two 1.5 hp blowers without increasing the existing battery bank. To run a third blower, which this ASP system can do, I will need another six 315 watt PV panels and have to double my battery bank.”
Turning piles with a front-end loader required about nine to ten months to produce finished compost. Demers has cut that to three or four months using the solar system. Adding aeration, rather than using the turning method, makes it easier to keep the composting process active and improve process control, he adds. The aeration system is programmed to run one minute for every 19 minutes off or three minutes per hour. Once incoming feedstocks are mixed, the material is placed on perforated pipes for passive aeration until there is enough accumulated to start the aeration (it takes about three weeks to build out a pile).
“By not turning the compost as often I’m also reducing fuel consumption and wear and tear on equipment, so it’s a ‘win-win,’” says Demers. “With the new system, it’s been a learning process. Active composting is approximately 30 days and curing is another 30 days, but I like to cure longer, typically around 90 to 120 days. I’m making a high quality compost and that requires time. It’s like making a fine wine — the longer it ages the better it gets.”
Finished compost is screened to three-eighth inch with a McCloskey 512R trommel. Due to the facility’s location, compost is sold primarily on a wholesale basis although Demers is exploring options to enter the retail market. New England Compost’s primary end users are gardeners and higher end landscape companies. “They prefer our compost over a primarily leaf dominated compost, which is very prominent in our area,” adds Demers. “The main applications are for amending soils because we have such poor soil conditions here. Some companies also use it to top-dress lawns.”
Dan Emerson is a Contributing Editor to BioCycle.