Top: Rejects from a food waste preprocessing/depackaging operation in northern California.
Jim Miller and Craig Coker
Preprocessing/depackaging systems are fairly simple in concept, using the “switch” to act on the “code” of the incoming waste stream. There are two outputs, as noted in Part I of this article series: the extract, or recovered organics, which can be further processed by anaerobic digestion (AD) and/or composting, and the rejects, which are film plastic, HDPE (high density polyethylene), PET (polyethylene terephthalate), PP (polypropylene), cardboard, paperboard, aluminum, and steel. Frozen foods can easily end up in the reject stream (and have damaged separator paddles in one installation), so thawing the frozen foods first demands extra labor and space.
As no preprocessing system is 100% efficient, small pieces of packaging will end up in the recovered organics. But it’s possible to reduce contaminants to less than 2% through proper source separation, presorting, and screening. One operator in the Midwest installed a density separator downstream of the depackager to try to remove additional contaminants and found that when they processed Snickers® Ice Cream Bars, the peanuts ended up rejected by the density separator.
For waste streams that have high percentages of recyclable content, preprocessing systems may be designed to recover the recyclable materials. Optional wash tanks are available for facilities that wish to clean and bale conventional recyclables for sale, but that leads to a wastewater management issue (see infrastructure considerations below). Several operators of depackagers reported having to open cardboard boxes of packaged foods by hand so that the cardboard would remain clean enough to recycle (i.e. not smeared with food).
Much of the reject stream becomes a mix of film plastic, food-soiled cardboard and paper, and smaller pieces of HDPE, PET, PP, and metals. Where materials recovery is not practical or feasible, facilities load this mix into an open-top dumpster for transport to a landfill; for others, the mix can be baled and shipped to a mass-burn waste-to-energy plant for incineration. Missouri Organics Recycling in Kansas City (MO) blends the reject mix with dry shredded pallets as a “refuse-derived fuel” for a nearby cement kiln. One of the authors got a quote from a mass-burn plant to take baled rejects from a proposed preprocessing system at a tip fee of $95/ton, plus 150-mile one-way transport.
Infrastructure Considerations
Most versions of preprocessing/depackaging equipment are designed to be used in enclosed spaces, although the Hermitage Wastewater Treatment Plant in Hermitage, Pennsylvania, has its preprocessing system outdoors (food waste slurry is codigested with biosolids at the plant). Enclosures can be pre-engineered metal buildings on concrete slabs. Considerations should be given to corrosion to mild steel due to the potential for high humidity inside a building. Two coats of an industrial epoxy paint should suffice, provided there is a proactive preventive maintenance program to recoat nicks in the paint as they occur. Another option is using galvanized steel, as it can be a more cost-effective finish than painting, and reduces the construction schedule. As discussed in Part I, there are ways to formulate concrete slabs to hold up against the low pH nature of preprocessed food wastes and the high abrasion potential of materials handling.
Anaerobic digestion installations using preprocessors are usually set up to handle the extract from the preprocessing system as a slurry, but composting facilities might need to invest in liquids handling infrastructure. Missouri Organics Recyclers installed three 29,000-gallon polyethylene slurry tanks to receive the extract from its Tiger depackager. A transfer pump and 4-inch line are used to convey the food waste slurry into a stationary mechanical mixer where it is blended with ground yard and woody waste prior to composting.
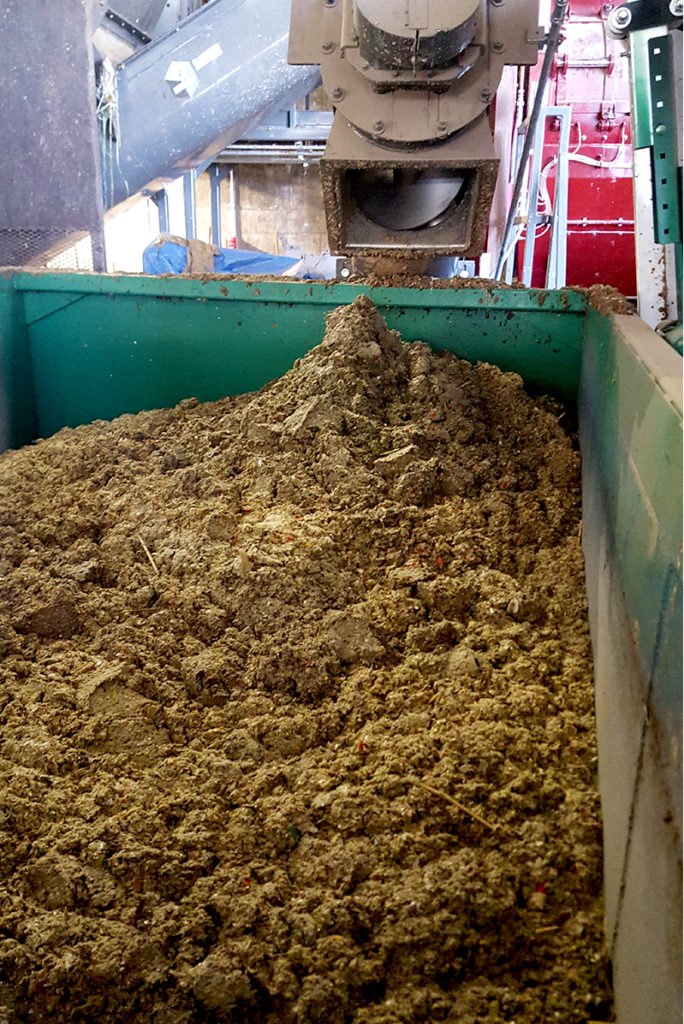
Output from a Scott Equipment depackager prior to anaerobic digestion in a dry fermentation system. Photos courtesy of Jim Miller
Preprocessing equipment usually has large horsepower motors and is normally configured to need three-phase, 460-volt power. That is not usually an issue when preprocessors are located at wastewater treatment plants or AD facilities, but can be a problem at composting or farm AD facilities — particularly those in more rural areas served by rural electrical cooperatives rather than mainstream utility companies. One author received a quote from a cooperative of $200/linear foot for extending three-phase power from the road to the facility. The equipment that would have needed the power would have been located approximately 1,700 feet from the road.
Access to water is also an infrastructure consideration. Several operators have commented that the systems work better with more water rather than less, but there is a trade-off against higher transportation costs for moving slurried organics. As with power, available supplies of water are not usually an issue in more urban installations (except in drought-stricken parts of the western U.S.) but can be in more rural areas. Missouri Organics Recycling came up with a clever idea of installing a 40,000-gallon potable water tank outside the depackaging building to accept and store spoiled liquids, (juices, beer dregs, etc.), which replaces the water needed to slurry the food.
Several operators have noted the need to use water for equipment cleaning. Again, this is usually straightforward if the preprocessing/depackaging site has access to a municipal sewer, but it can be an issue in more rural areas. Several preprocessing operations use washwater as process water. St. Louis Composting’s facility in Belleview, Illinois, was diverting washwater to a storm water management pond but it led to regulatory challenges, so the company was forced to relocate its depackager to a repurposed urban warehouse with access to the sewer line. In addition, it may not be possible to directly discharge washdown and/or process water to the sewer without an industrial pretreatment system to reduce pollutants and biochemical oxygen demand (BOD) through removal of total suspended solids (TSS) and possibly nutrients like nitrogen and phosphorus, and to obtain a discharge permit from the wastewater treatment plant.
Operational Considerations
Preprocessing systems can expand the capabilities of organics recyclers. “Our depackager allows us to diversify the types of materials we could accept at our facility and to offer new services,” notes Will Kelley, Resource Manager for Napa Recycling in Napa, California (CA). “It has increased our customer base from Napa County to the [larger] region and ensures a consistent clean feedstock for composting.”
One common theme the authors have heard from those operating preprocessing/depackaging systems is the constant need for cleaning. “While we are pleased with how our preprocessing system operates, the simple reality is that preprocessing food wastes is very messy, and we spend a lot of time keeping equipment and processing areas clean,” says Hillary Gans at ReThink Waste in San Carlos (CA), who runs an Anaergia OREX preprocessing system for the South Bayside Waste Management Authority. “This equipment requires precleaning or the maintenance work can get a bit nasty.”
While these systems are effective in reducing contamination in composting and digestion feedstocks, they are not a single solution. “Doing load checks is the most important thing,” adds Kelley. “We do not accept any glass and if a hauler consistently brings in glass, then we will not allow them to dump. Our drivers do a load check on each container they pick up. This is the most beneficial because we can stop the problem at the source before it arrives at our facility. The machine is only one part of a successful operation. Having a solids receiving and preprocessing area to manage organics from receiving through processing is very important.”
In summary, as the interest in diversion of food waste from landfill disposal grows, installation of preprocessing systems will increase. Depending on the waste stream and downstream processing options, system design and capability can vary significantly. An efficient and effective food waste preprocessing system will deliver quality feedstock that is appropriately tailored for a specific AD process or composting.
Jim Miller is CEO of J.R. Miller & Associates, a consulting engineering firm in Brea, CA. He can be reached at jrmiller@jrma.com. Craig Coker is a Senior Editor at BioCycle CONNECT and a Principal at Coker Composting and Consulting near Roanoke VA. He can be reached at ccoker@jgpress.com