An institutional and commercial organics collection program in Eureka, California, diverted 760 tons of food waste in a year-long trial.
Marsha Johnston
BioCycle June 2014
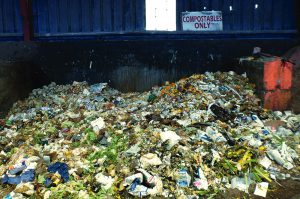
Commercial organics collected by Recology were unloaded in a bunker at the Humboldt Waste Management Authority’s transfer station for transport to a composting facility about 150 miles away. Photos courtesy of Juliette Bohn
Beginning in October 2012, and running for a little over a year in northern California’s Humboldt County, the Food Waste to Watts pilot diverted food waste from 50 commercial participants in the City of Eureka and 9,000 students and staff at nearby Humboldt State University (HSU). Funded by an EPA Climate Showcase Communities grant designed to help communities develop replicable programs that measurably reduce greenhouse gas (GHG) emissions, the pilot diverted over 760 tons of food waste, 200 tons of dry wall/wood, and reduced 680 tons of GHG emissions. In addition, HSU achieved 85 percent of its organic waste diversion potential, and received an Energy Efficiency and Sustainability Best Practices award from the Cal State University system for implementation of a campus-wide program.
At BioCycle’s 14th Annual Conference on Renewable Energy From Organics Recycling in San Diego in April (BioCycle REFOR14 WEST), Juliette P. Bohn, project manager for OurEvolution Energy and Engineering, described the trial-and-error process of establishing an organics diversion program from scratch while relying on public agency support and navigating local politics.
The pilot was named Food Waste to Watts to demonstrate the ultimate goal of developing an anaerobic digester (AD) to produce energy from diverted organic waste. “Even though we were not producing renewable energy in this first phase, we wanted the logo to reflect the longer term vision,” says Bohn, who was a project manager with Humboldt Waste Management Authority (HWMA) at the time. “The idea was to have the material flowing by the time the digester was constructed; we chose to compost it as an interim step in order to build organic waste diversion capacity and collect data that would be used for the full program roll-out.”
At the outset, both the Eureka City Council and HWMA were quite enthusiastic about the project. The City of Eureka passed a resolution supporting development of the AD facility and offered a site. Over time, however, the political will started to shift. Most notably, the HWMA executive director who envisioned the project and hired Bohn, retired in December 2011. “Political change happened throughout the project,” notes Bohn. “There was a near complete turnover of the Eureka City Council and HWMA Board of Directors. Additionally, HWMA hired a new executive director in November 2012.”
Launching The Pilot
Preparatory work on the pilot started in 2011. The EPA grant was awarded that summer, and HWMA contracted with Environmental Science Associates (ESA) to help develop the program and provide initial source separation training.
The pilot’s first participant was HSU, which wanted to start diversion in the Fall 2011 semester. Bohn’s team therefore had to set up its diversion procedures on campus before a site was procured to take the food waste. “In the beginning, we sent the separated food waste to the landfill,” Bohn explains. “This temporary arrangement allowed the pilot team to measure and audit the diverted waste, and the HSU Waste Reduction & Resource Awareness Program (WRRAP) students to monitor the collection bins and create signs and other outreach materials designed to educate students and staff about the new program in an effort to reduce contamination.” HSU was the sole pilot participant from the fall of 2011 until October 2012, although the entire pilot had to be suspended from May through July of 2012 when HWMA’s local transfer site was shut down.
As HSU got started, Bohn learned that the local composting site it had planned to use had declared bankruptcy. After scouring nearby cities, the team could not find an alternative site that met the basic regulatory and logistical requirements for composting food waste. As an interim solution, Patrick Owen, HWMA’s operations manager, suggested hauling the material to the nearest permitted food waste composting facility — Cold Creek Compost, 153 miles away. “We visited the Cold Creek site, confirmed regulatory approval, and began investigating the types of trailers that could handle wet food waste, the types of long-haul trucks used in our area, the kinds of bins they could carry, and how much weight we could put in the bins,” Bohn recalls. The team determined that material from commercial facilities would be collected using traditional garbage trucks with slight modifications to prevent leakage.
With such a distant composter, the Food Waste to Watts pilot still needed a local site to receive organic materials, remove large contaminants, and scoop the organic waste with front-end loaders into 40-cubic-yard leak-proof roll-off containers for transport. By March, 2012, a “bunker” was set up at an HWMA transfer station, and the HWMA team began processing HSU’s food waste for the first time. “The bunker consisted of huge concrete blocks set at a 90-degree angle to the push wall of the transfer station tip floor,” says Bohn. HSU’s Plant Operations staff collected campus food waste in 96-gallon wheeled carts that were aggregated into an on-site 15-yard roll-off container, which Arcata Garbage Company hauled once a week to the HWMA transfer site. Once a week, HWMA shipped two 40-yard roll-off containers to Cold Creek Compost. The HWMA team also began preparations to expand the pilot program into the Eureka commercial sector.
But in May 2012, the Humboldt County Department of Health and Human Services shut down the pilot project by closing the food waste receiving and transfer operation. It turned out that the facility’s Transfer Processing Report, an official document that details what a waste transfer station can do, did not include food waste. Using state environmental guidelines and the existing permit, Bohn’s team drafted amendments to the report and paid a fee to have the Local Enforcement Agency (LEA) review them. The first draft was rejected, whereupon the pilot team began meeting with the agency to better understand its concerns and work out solutions. “We were able to negotiate the terms of operation for our liquids management plan, by storing sawdust next to the bunker to absorb any liquids, and committed to comply with the existing a 48-hour solid waste removal frequency,” explains Bohn. “It was painful to be shut down, but it was ultimately a good capacity-building and outreach experience, and the LEA now has more familiarity with food waste diversion.” By August 2012, the team received regulatory approval to restart the pilot program — just in time for HSU’s Fall semester.
Round Two
With Food Waste to Watts reestablished at HSU in the fall of 2012, Bohn’s team and her private sector partners, Environmental Science Associates and Recology, the exclusive waste hauler in Eureka, again turned attention to the collection logistics and recruitment of commercial participants. It was decided to use 96-gallon wheeled carts for organics collection, allowing Recology to use the same truck for all sites (multiple carts were used for larger participants) and reduced wear and tear on the garbage truck lift arms. For each business licensed to handle food in Eureka, Recology noted the current garbage bin size and pick up frequency. The team then used that data to estimate the volume of organic waste that could be diverted as well as how many 96-gallon carts would be needed for each potential participant. “Then we knocked on every single door,” Bohn says. “We wanted participants who would be really excited about diverting organic waste.”
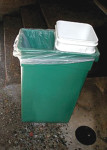
Pilot participants were given smaller containers with a garbage bin insert for indoor use, and 96-gallon carts to store mixed organics until collection.
To divert as much organic material as possible, pre and postconsumer food waste, food-soiled paper, waxed cardboard, milk cartons, bathroom towels, composting facility-approved bioplastics (i.e., straws, cups, utensils and coffee cup lids), floral waste, bones and shells were accepted. “We said, ‘If it was ever alive, you should put it in the organics bin,’” Bohn notes. “This made participation easy and maximized the organic waste diversion from landfills. Further, Cold Creek’s willingness to experiment with, and accept a wide range of materials was key to the success of the program. If Cold Creek found that some of the materials such as bioplastics did not break down in the first compost cycle, they would simply recompost them with the next cycle until they were gone.” Participants had a choice of using either no bags, or compostable bags in the collection program. “Most participants liked the idea of not buying bags and really took to washing out the internal collection bins in the commercial sinks,” she adds.
The pilot team also helped participants reorganize their kitchens. “Sometimes their recycling bins were overflowing onto the floor; restaurants use the big #10 cans and big plastic jugs of oil, so we made the biggest bin recycling, put in green slim-jims for food waste and replaced the big ‘black hole’ garbage bins with fewer, smaller bins,” Bohn explains. “Their overall diversion increased as a result.”
To monitor participation, the pilot team used a “lid-flipping” strategy, regularly opening bins of a quarter to a third of participants and showing staff the contaminants they found. By the end of the program, Bohn says, only two or three participants still had organic waste bins that were “pretty” contaminated.
Despite the pilot’s success, the newly installed decision makers at the Eureka City Council and HWMA would not approve the estimated five to six percent increase in waste hauling rates to make the program permanent, and the pilot ended at the end of 2013. “A project of this magnitude needs to be supported by a formal vision, such as the City of San Jose’s ‘Green Vision’, in order to survive the political pendulum,” Bohn concludes. Ironically, she adds, the 75 percent diversion of commercial waste from landfills required by California law by 2020 cannot be achieved without diverting organic waste.
Marsha Johnston is a free-lance writer with Earth Steward Associates in Arlington, Virginia.