Kevin Anderson and Stan Slaughter
Missouri Organic Recycling, Inc. (MOR) in Kansas City, Missouri, started out as a yard trimmings composting facility in 1992, processing grass and leaves from municipalities, residents and commercial sources. Founded by the Anderson family, the company decided to expand by collecting and composting food waste and construction and demolition (C&D) debris. Approval was received from the Missouri Department of Natural Resources (MODNR) to conduct a two-year pilot project with a local bagged salad preparation facility; the pilot began in December 2001.
The pilot was successful, and MOR was permitted to accept food production residuals as well as pre and postconsumer wastes in 2004. In 2005, we received a $50,000 grant from MODNR’s Environmental Improvement and Energy Resources Authority (EIERA) to purchase a 2,800-gallon capacity tanker truck to collect wastewater from MOR’s food processing customers. (See “Food Waste Composting Takes Hold In Missouri” (August 2009) for the early history.) The fleet of collection vehicles expanded, as did the types of food waste accepted and customers serviced — including commercial and institutional generators and more food manufacturers. Examples of the latter include 10 tons/day of hot tea grounds, semi-trucks full of dog food, starch, and spices. The company also accepts virtually all types of paper — including wax-coated labels, waxy wet-strength cardboard boxes, colored paper and milk cartons — as well as certified compostable liners and foodservice ware.
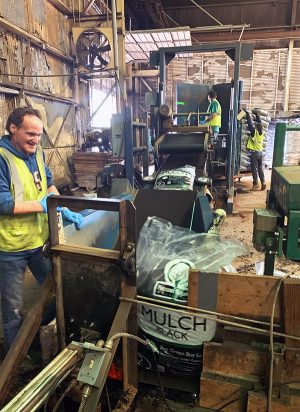
A bagging line at Missouri Organic turns out about 750,000 bags of soil and mulch per year.
Currently, MOR processes about 17,000 tons/year of food waste and about 85,000 tons of green waste (340,000 cubic yards (cy)). Wood waste is processed into mulch, and MOR also has a contract with the city of Kansas City to process all green waste for the city departments as well as residents. The composting facility is on 20 acres. MOR has five locations, some used for retail sales and green waste drop-off. Equipment includes John Deere loaders and skid steers, a Frontier compost turner, Hogzilla tub grinders and Peterson horizontal grinders, and screens supplied by Power Screen and Doppstadt.
Average annual compost production is 75,000 cy/year. MOR sells a lot of custom soil blends, e.g., for bioretention applications, roof tops, garden soils, and a biochar/compost mix. A bagging line at the facility turns out about 750,000 bags of soil and mulch per year.
Contaminant Removal Via Depackaging
Over the years, MOR has added more trucks to its collection fleet and is up to about 350 food waste customers. The contaminating materials in those loads consisted mostly of noncompostable bags, bottles, plastic wrap, and plastic serviceware. All those materials were placed in the windrows and screened out at the end of the process. While our compost looked good, we were uncomfortable with having the contaminants go through the hot composting process. We also ended up with an overs pile that had enormous amounts of plastic that could not be screened out or reused in the process.
We tried using wind sifters/screeners to remove contamination but never had a lot of luck with them. They slow the screening process way down. In general, we were spending a lot of time and money cleaning our waste stream, and started looking for better ways to do this. Our search included depackaging systems to remove contaminants at the front end of the process.
We visited several sites around the country to observe depackagers in operation, evaluated operational features and costs and settled on the Tiger from Ecoverse. MOR received a significant grant from the local solid waste district to fund just under half of the costs of the project. Additional infrastructure work involved installing a 2-inch water line and 3-phase electrical power to be integrated into the project. The depackager and staging area are inside a steel building.
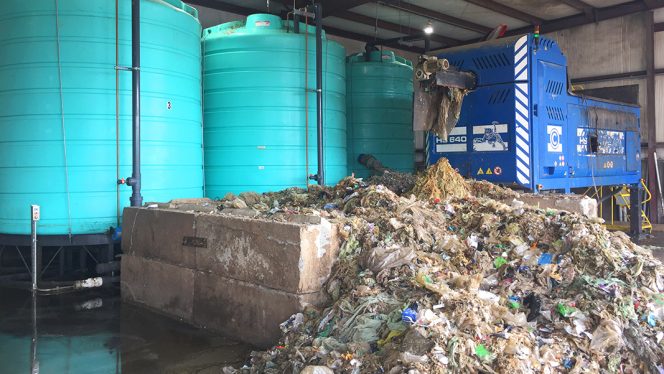
Three large vertical tanks with 29,000 gallons of total capacity were installed to store the food waste slurry coming out of the depackager. Rejected material is mixed with dry shredded pallets and sold to a cement kiln nearby as refuse-derived fuel.
MOR settled on the Tiger because of its vertical design. This helps to keep small hard plastic pieces from falling through the screens like in the horizontal mills. It also creates a tornado effect that moves the plastic out of the mill. The unit is in a very compact space; its integrated design did not require added conveyers and augers.
Managing The Slurry
MOR designed and contracted the system itself and uses its repair and maintenance staff to keep it running. The depackager came online in the fall of 2018. It immediately removed 14% of the food waste stream as contamination. The rejected material is mixed with dry shredded pallets and sold to a cement kiln nearby as refuse derived fuel. This meant that our disposal service was rated as “zero waste to landfill,” which provided extra value to our clients. The Tiger’s ability to depackage steel and aluminum canned foods gave us more tipping fees and recycled cans to sell.
Originally, the food slurry coming out of the Tiger emptied into a pit for loaders to take to the windrows. Ground, aged yard trimmings were formed into two small rows and the slurry placed in the middle. The windrow turner made three passes to mix the material and form the windrows. We were trying to keep the moisture of the slurry under 70% so the food could be scooped and moved with a loader and then blended with yard trimmings. We quickly discovered, however, that the process was not as simple as we had hoped in the beginning. As a result, MOR had to make a significant investment after the fact to handle the slurry, which was a bit unexpected.
Three large vertical tanks with 29,000 gallons of total capacity were installed inside the building. The Tiger’s output was diverted from the pit and run through a 4-foot diameter radial pump to the storage tanks. A 40,000-gallon potable water tank was installed just outside the building to accept and store spoiled liquids (juices, beer dregs, etc.), which replace water needed to slurry the food. In front of the building, the asphalt pad was expanded by 50 feet on two sides and a custom-built Meyers 42-yard mixer was wired and plumbed in place away from the building. A 4-inch line from the slurry tanks to the mixer was buried deep and protected from heavy traffic.
Two large piles of bulking agent are maintained at the edge of the pad. One is ground, aged yard trimmings and the other is woody fines from our mulch operation. This configuration allows one operator to pump in the slurry and load the right blend of browns in the mixer. After 6 to 8 minutes of mixing, the material empties onto a 180 degrees radial stack conveyor that moves the material away from the mixer. It falls in an arc onto the composting pad, eventually creating a pile with 3,000 cy of material. Each batch coming out of the mixer is about 40 cy.
Before switching to pumping the food waste into the mixer, the blend going into the windrows was very inconsistent. We couldn’t control the amount of slurry in the mix. This new process is very easy to track. The slurry is dosed into the mixer at about 1,000 gallons/40 cy batch.
The Tiger itself is designed to have more moisture to keep the screens clean, and the throughput higher. Adjusting the liquid feed can be done with a turn of a knob, which is helpful when we are processing feedstocks that are drier like paper or compostable serviceware and spices. We run between 65% and 83% moisture in the slurry.
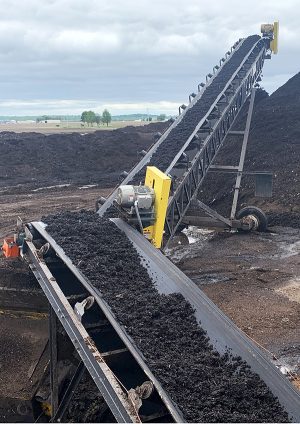
Blended feedstocks empty onto a 180 degree radial stack conveyor. The material falls in an arc onto the composting pad.
Missouri Organic is in the midst of changing its composting system to have material remain in static piles for a longer period of time. The newly made pile of 3,000 cy that comes off of the radial stacker will sit for a week before being moved to another static pile, where it will remain for about two weeks. Next, that 3,000 cy pile will be broken down and moved into 3 smaller windrows for turning; this process is expected to take 3 weeks, and then the compost will be screened. Depending on demand for the compost, the product could sit for 3 months or 3 weeks for curing. Most likely we are looking at a total active composting process of 6 weeks with curing of 3 weeks to 3 months.
Depackaging Performance
MOR is still learning about the limitations of the depackager but has discovered that nothing larger than 1-gallon containers are optimal. The rated throughput capacity of the Tiger is 15 tons/hour, but the most we’ve seen is 12 tons/hour, with an average of about 7 tons/hour. Heavy, wet “old” food waste slows the process. Lots of cardboard can also slow it down, whereas plastic bottles, aluminum, tin and steel cans go fast as they process cleanly and quickly. The auger is cleaned about once a month.
Gauging the level of contamination that remains in the food waste is difficult to determine, but we estimate it is well under 2% and has been very easy to screen out. Some smaller pieces remain in the slurry. But because the total contamination is down the finished compost is much cleaner than before. We have had no issues with the pumps due to the remaining contamination.
Although our food waste collections from schools, businesses and restaurants are way down due to the virus, industrial sources are increasing so we’ve not had a major change in our operation during the pandemic.
Kevin Anderson is owner and vice president of sales and marketing at Missouri Organic Recycling (MOR). Stan Slaughter is an education and garden specialist at MOR.