Threemile Canyon Farms in Boardman, Oregon is the state’s largest dairy farm, housed on 93,000-acres of farmland. The complex includes 3 dairies. In 2012, Threemile Canyon Farms installed an anaerobic digestion system to treat manure from 33,000 dairy cows. Biogas was being used to generate electricity for farm operations. More recently, Threemile Canyon partnered with Equilibrium Capital to invest in converting its methane digester from generating electricity to producing renewable natural gas (RNG). According to Iogen, the $55 million project began injecting RNG into the grid in July 2019; the RNG is being used as transportation fuel in California. Iogen provided the project with a structured 10-year RNG offtake agreement that “provides an investment-grade floor price for RNG with market upside sharing, and is managing all fuel compliance activities, including generating and monetizing D3 RINs under the federal Renewable Fuel Standard and LCFS Credits under the California Low Carbon Fuel Standard program,” stated the company in a press release.
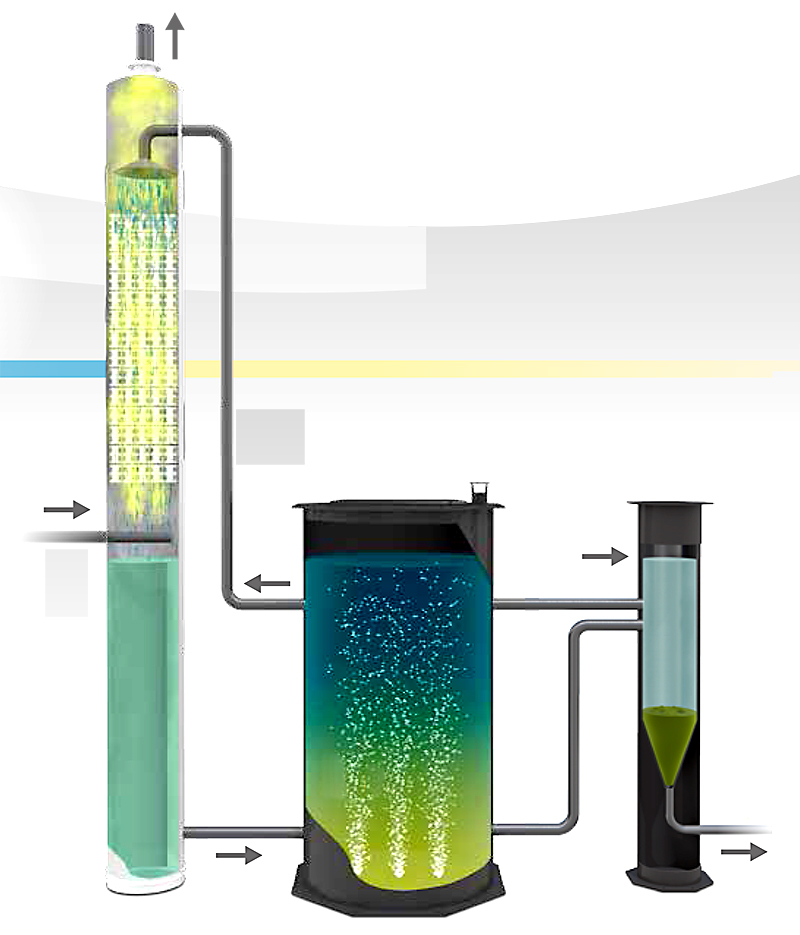
THIOPAQ®, a biogas desulfurization technology developed by Paques, removes hydrogen sulfide. Diagram courtesy of Paques Environmental Technologies
The first step in the conditioning system installed to clean the biogas features the THIOPAQ® process, a biogas desulfurization technology developed by Paques to remove hydrogen sulfide (H2S). “The THIOPAQ® is a chemical scrubber with a biological component,” explains Andrew Delgado, Paques’ Project Team Leader. “H2S is first absorbed with an alkaline solution in a scrubber tower. A bioreactor containing Thiobacillus bacteria simultaneously reduces the H2S to elemental sulfur while regenerating the alkalinity.” The desulfurized gas exits at the top of the scrubber tower where it is further treated in an amine process supplied by Wartsila to remove carbon dioxide. Drying and compression steps complete the gas upgrading process before it is injected into a pipeline.
Delgado adds that the scrubbing process works just like a caustic scrubber that achieves very high removal rates (>99.5%). The difference with the THIOPAQ® process is that it biologically regenerates the alkalinity thereby significantly reducing operating costs. The sulfur is converted to safe, odorless biological sulfur, which is removed from the process as a slurry, and is ultimately used as a soil amendment.
Threemile Canyon Farms received the Innovation Center for U.S. Dairy’s 2020 Outstanding Dairy Farm Sustainability Award, judged by an independent panel of dairy and conservation experts who consider innovation, scalability and replicability when choosing winners. The farm uses the digested solids for cow bedding, and the liquid effluent to irrigate its crops. “We grow about 300,000 tons of potatoes each year, which are processed at a local manufacturing plant,” notes the farm’s website. “Any processing waste, such as ‘peels and culls’, is returned to the farm and recycled as feed for our dairy cows.”