New 55,000 tons/year facility currently processes yard trimmings, but is gradually incorporating commercial food waste.
Craig Coker
BioCycle October 2017
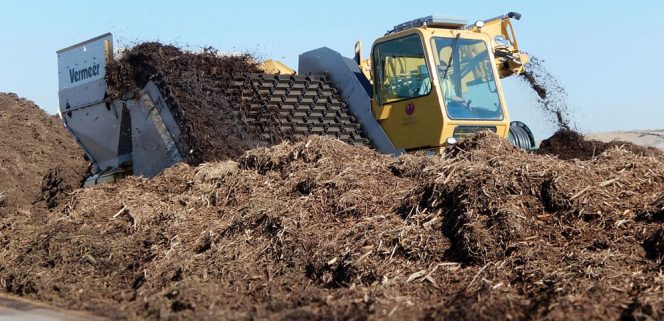
An aerated mass bed system is used for composting yard trimmings, and eventually food waste. An elevating face turner moves material 22 feet laterally on the pad in each turning event. Aeration piping is housed in a gravel bed below the concrete slab with nozzles flush with the slab surface. The aeration system can be run in all positive, all negative, or in a reversing positive-negative loop. Photo courtesy of the City of Phoenix
“We decided to include the composting facility in our new Resource Innovation Campus as we envision a robust hub for innovators building Phoenix’s circular economy and generating economic development at the Campus,” explains Stacy Hettmansperger, Operations Manager for the Phoenix Department of Public Works. “In addition to composting, a new palm fronds recycling-to-animal feed operation is opening with the City’s partner, Palm Silage. The City is actively seeking to develop partnerships with businesses to take additional items from the waste stream and create economic activity on the campus.“
Technology And Feedstocks
The TAP system, provided by Green Mountain Technologies (GMT), uses a mass bed design situated on an aerated concrete pad with computer controlled reversing positive/negative aeration. The facility utilizes a Vermeer CT1010 turner for turning the mass bed piles. Curing uses the same turned mass bed configuration but the concrete surface does not have aeration trenches. The 2.3 acres of active and curing pad concrete surface is capable of processing the Phase I throughput of 55,000 tons/year including biofilters, blowers and unloading and equipment turning areas. “While we have land, we wanted to conserve space, so we opted for a composting approach that had minimal footprint, which led us to the GMT system,” notes Hettmansperger.
While the initial commissioning is based only on yard trimmings and landscaping residuals, the City has programs in place and is gradually receiving food waste. “We have been operating a small pilot project at our 27th Ave Transfer Station since 2015, initiated by the city sponsored zero waste events in downtown Phoenix for Super Bowl XLIX,” says Hettmansperger. “For the pilot, we have been focusing on city sponsored special events and on back-of-house food waste collection at Phoenix Sky Harbor International Airport, along with the Phoenix Convention Center and material from private haulers. In August, these food waste sources slowly began to be incorporated into the composting facility commissioning process.”
To increase organics diversion to achieve the 40 percent goal, the City offers a discounted tip fee to customers that deliver clean green organics through the City’s Certified Organics Program. Participants receive the reduced tip fee if loads contain only presorted approved green waste, unbagged, less than 4-feet long, and less than 24 inches in diameter. Trash must be separated out and unloaded into designated areas.
The City collects MSW from residential accounts, with the exception of Homeowner’s Associations and multifamily units. A pilot curbside collection of yard trimmings was initiated; residents receive tan 90-gallon wheeled carts. No plastic bags or food waste are allowed in the carts. “Once the curbside green organics collection program is expanded beyond its current pilot area of the city, we will determine how to implement a residential food waste program that accounts for contamination concerns,” notes Hettmansperger.
Operations And Management
The City of Phoenix contracted with WeCare Denali Organics (formerly WeCare Organics) to operate the composting facility. Incoming feedstocks are handled in one of two ways. Self-haul customers drop off brush and yard trimmings in a designated drop-off area, which can, and does, include material in plastic bags. These are hand sorted before going through a Vermeer 6000 horizontal grinder. Larger loads of green waste, like those arriving under the Certified Organics Program, are dropped in a designated unloading zone near the Vermeer grinder, which has the capacity to store seven 30-cubic yard (cy) loads. Food waste will be handled in the same way to prepare the materials prior to placement on the aeration pad.
Ground feedstocks are moved into the primary composting area where eight to ten-foot deep piles are built with a front-end loader. “We designed the system with eight aeration zones oriented on four pads,” explains Michael Bryan-Brown, CEO of GMT. “High aeration rate is provided at the beginning of the process, delivering air at 5 cubic feet per minute/cy (cfm/cy). Aeration then steps down to match the biological activity as it moves across the aeration pad, delivering air at 4 cfm/cy in Zones 3 and 4, and at 3 cfm/cy in Zones 5 and 6 while the compost meets the Process To Further Reduce Pathogens (PFRP) requirement and finally to 2 cfm/cy in Zones 7 and 8 by the end of the aeration pad.
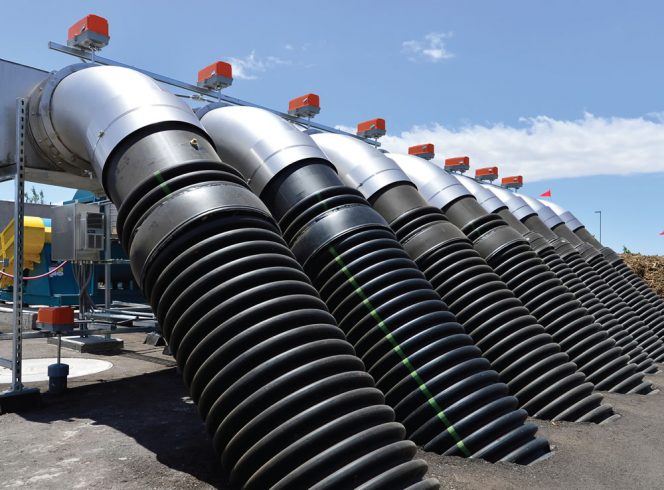
Aeration piping is housed in a gravel bed below the concrete slab with nozzles flush with the slab surface. The aeration system can be run in all positive, all negative, or in a reversing positive-negative loop. Photo courtesy of the City of Phoenix
The aeration piping is housed in a gravel bed below the concrete slab with nozzles flush with the slab surface and clean-out ports spaced along the perimeter of the aeration pad. The aeration system can be run in all positive, all negative, or in an automatic reversing positive-negative loop, using the differential between upper and lower temperature sensors in each zone. If the temperature at the bottom of a pile is high, air pressure (positive aeration) is used. If the upper part of the pile is hotter, suction pressure (negative aeration) is used. Odor management in the initial two zones is provided by 6-inch thick “biocovers” made from compost, and by a 11,750 square foot (sf) stand-alone biofilter for processing air collected by the suction blowers.
“An interesting element about designing this facility was deciding what type of aeration is best during the heat of a Phoenix summer day,” notes Bryan-Brown. “We were concerned that delivering very hot ambient air to the biofilter while in suction would overheat the biofilter and we wanted to take advantage of the cool night air to cool down pile temperatures.”
Water management is an important part of the design, given the high temperatures and arid conditions of the Phoenix area. Incoming yard trimmings only have a moisture content of about 30 percent. The site has a 50,000-gallon underground tank for the capture and storage of process water (a combination of condensate and captured rainfall runoff). The pressure blower is equipped with a misting ring using nonpotable well water to saturate the feed air with cool water, which drops process air temperatures from 122°F to 82°F. The negative aeration manifold drains to a concrete tank for condensate reuse below a Y-fitting between the blowers and the distribution piping. All the aeration supply piping is 18-inch or 24-inch diameter pipe. The Vermeer CT1010 turner is equipped with a 350 gallon/minute irrigation reel to remoisten material during turning events.
One unique aspect of operating a composting facility in a desert environment is the need for a Dust Control Plan, which is stipulated in WeCare Denali’s contract with the City of Phoenix. “Dust control is a very big issue here,” explains Chris Seney, the contractor’s operations manager. “We have had extensive training by City and [Maricopa] County staff on minimizing wheel track-out of dirt onto City streets.” The contract requires WeCare Denali to comply with the City’s air quality permit with Maricopa County Air Quality Department and to adhere to a maximum opacity of 20 percent at any time. All vehicles leaving the site must be tarped or covered. WeCare Denali is also required to have an Odor Control Plan that involves daily human and field olfactometer monitoring and immediate corrective action if a City-verified complaint is registered.
Seney, who formerly ran an 1,100 tons/day biosolids composting facility in Southern California, arrived in Phoenix in February 2017 after WeCare Denali won the contract. “I immediately had to hire 12 staff from scratch,” he says. “We were able to find qualified people by focusing on the landscape supplies, aggregates, and mining industries.” Seney has been doing extensive training of the new staff, augmented by training from the various equipment suppliers and from the staff at GMT. “Fortunately, my last composting facility was in a hot, desert environment,” he observes, “so I knew how to teach our staff my Heat Stress Plan and safety training programs.” The staff at the Phoenix facility begins work in the summer at 5:30 a.m. and stops operating equipment at 1:30 p.m. Material is accepted at the facility until 5:00 p.m. Monday through Friday and until 3:00 p.m. on Saturdays.
Compost Markets
At the end of the 45-day production cycle, the compost is screened with a Doppstadt SM 726 trommel that can do a 2-way split into compost, and overs. Residual film plastic and stones in the overs are removed with a Komptech Hurrifex.
Chris Seney is still working on the compost marketing plan, but expects to sell the products under the same brand names as other WeCare Denali contract operations — WeCare Compost®, WeCare Engineered Soils™ and WeCare Roofmix™. The City has been supporting the marketing by conducting a multiyear turfgrass study with the Departments of Public Works and Parks and Recreation. It partnered with Arizona State University to design the structure of the study and conduct the sampling and soil analysis. The Public Works Department has been providing free compost from its pilot composting area to utilize at study plots within six City parks and demonstration areas at three downtown plazas. The purpose of the study is to confirm the benefits of compost on the turf compared to traditional turf management practices. “After the first year of the study, we were really able to break down some of the institutional silos that existed between our City departments,” notes Hettmansperger. “The study has increased interest and awareness about compost across the City and how increasing green organics diversion and use of compost can develop a circular economy.”
The facility operations contract with WeCare Denali Organics went into effect in February 2017. It is a three-year contract with two optional two-year renewal periods for a total potential contract value of $16.5 million. The contract requires WeCare Denali to handle a minimum of 2,500 tons/month of organics and has a 25 percent revenue-sharing provision with the City on sales of compost and landscape products. In addition, the City gets 1,000 cy/year of compost for free, and a discounted rate on orders above 1,000 cy. For any loads above 5 percent contamination by weight, WeCare Denali can charge the City a higher per ton processing fee to account for the additional resources required to sort the material. Any loads delivered to the composting facility above 10 percent contamination by weight can be rejected. Green organics contamination is defined as “small animal waste, logs, painted or treated wood, large tree stumps and solid waste.”
The City of Phoenix originally solicited consultant proposals in June 2014 to design the facility. It elected to build the project as a combination of design-build and Construction Manager At Risk (CMAR, see sidebar). “We teamed with a local architect firm, which was valuable, as the City wants work to go to local firms,” explains Bryan-Brown. “The CMAR firm, Arrington Watkins and construction firm Brycon Construction pulled this job off in five months. They did the Value Engineering design review in mid-October 2016 and had a ribbon -cutting in mid-April 2017.”
Cooperation between designers, technology providers, contractors, and City departments is one common theme in the successful three-year journey from drawing board to start-up operations. The 27th Avenue Compost Facility is the first solid waste infrastructure project in the United States, and the first project in Arizona, to earn Envision recognition from the Institute for Sustainable Infrastructure. The Envision system rates sustainable infrastructure across the full range of environmental, social and economic impacts. The facility has also been nominated for an Arizona Forward Environmental Excellence Award in the category of Public Sector Site Development. This is an important award that has been considered the “Academy Awards” for Arizona sustainability.
Craig Coker is a Senior Editor at BioCycle and CEO of Coker Composting and Consulting (www.cokercompost.com) near Roanoke VA. He can be reached at ccoker@jgpress.com.