The recycling industry has created well over 1 million jobs and is projected to add another million as recycling levels continue to divert more and more material to industry and agriculture.
Neil Seldman
BioCycle July 2012, Vol. 53, No. 7, p. 22
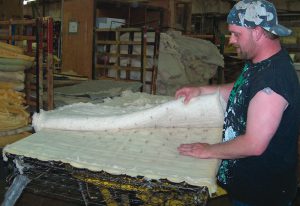
A mattress recycling and refurbishing plant in Bridgeport, Connecticut that opened in June will process 100,000 mattresses/year and employ 20 workers.
In Bridgeport, Connecticut a mattress recycling and refurbishing enterprise started up in late June. Twenty workers will process 100,000 mattresses and box springs annually. This will reduce transfer station and landfill costs, while making good end products available to consumers at pennies on the dollar compared to new mattresses from formal retail stores. The plant is owned by the Greater Bridgeport Community Development Corporation, which used a $100,000 Community Development Block Grant (CDBG) to leverage additional capital.
An array of refurbishing operations in Eugene, Oregon — including mattresses, automobiles, appliances, computers and furniture — sell through 11 outlet stores run by Saint Vincent de Paul (SVDP). It is estimated these operations have helped lower the cost of living in Eugene by 3 percent. SVDP’s total operations employ over 400 workers at living wages plus health insurance. SVDP also manufacturers products made from window glass and fire starters made from old crayons. Since the great recession of 2008, SVDP has hired over 100 new workers and raised wages.
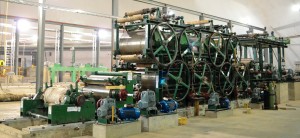
A small paper mill that uses recycled high grade paper and recycled cotton is under construction in Reading, Pennsylvania. The plant will create 100 jobs at $14/hour.
In Alachua County, Florida, a 40-acre Resource Recovery Park has been created for recycling and composting companies. Similarly, an industrial park for these types of companies is being developed in Austin, Texas. Austin just released an extraordinary business plan for resource recovery that will guide the city to 90 percent diversion of discarded materials by 2020. The report will save cities seeking to replicate these goals hundreds of thousands of dollars in consulting fees.
Urban Agriculture
In Poughkeepsie, New York, the city is providing 4 acres to Greenway, Inc., a composting company, which will create the foundation for an intensive urban agriculture sector. Urban agriculture is essential for sustainable cities. David Crockett, director of the Office of Sustainability in Chattanooga, reports that if just 10 percent of the food eaten in the city were grown in the city, it would make a $1 billion impact on the local economy.
In Atlanta, urban agriculture is making considerable progress. Biponica, Inc. has produced two grow facilities at Park Department outdoor centers which grow fish using algae and duck weed as feed, and vegetables from the nutrients in fish excretions. Elemental Impact has established the downtown Zero Waste Zone to segregate organic waste for composting. This also makes it easier to recycle nonorganic discarded materials. Elemental Impact is also working with the city’s airport, the busiest in the U.S., to capture back of the house and concourse organic waste, as well as the plastic packages used to deliver food to the facility. Elemental Impact is now working closely with the National Restaurant Association to establish these zones in many U.S. cities.
Reuse And Niche Recycling
Also in Atlanta, the faith-based organization Charitable Connections has recently expanded the Fuller Center, its restore that distributes used and new building materials to low-income customers. Charitable Connections also has established a recycled paint enterprise, as well as attracted an electronic scrap recycling company and a textile recycling company to the community.
In Berkeley, California, Urban Ore has served as a model for large and small reuse stores all over the world. The privately owned enterprise started in 1979 at the tipping face of the old Berkeley landfill, and recovered its first round of tools and equipment from the landfill itself. Incorporated as a Subchapter S corporation in 1980, Urban Ore is open 360 days a year, 10 hours a day. Conducting business under the motto “to end the age of waste,” Urban Ore’s staff diverts used building materials and other products from landfills and transfer stations by sorting, cleaning, organizing and selling products to individual customers and other reuse stores in the San Francisco Bay Area. It recovers reusable goods by scavenging under contracts from municipally-owned transfer stations in Berkeley and El Cerrito.
In 1999, Urban Ore had to rewrite Berkeley’s zoning law to be able to move across town onto the property it subsequently bought. With the cooperation of the Planning Department and the blessing of the City Council at the time, a new category of conservation business that can occupy Mixed Use/Light Industrial properties “as of right” was created. That designation is Materials Recovery Enterprise.
The enterprise now has 38 workers and grosses over $2.6 million annually. Recovered materials that cannot be sold are recycled. Urban Ore sends to landfill less than 2 percent of the 7,000 to 8,000 tons of materials and products that come its way each year. It was able to purchase most of its 3.2-acre facility in West Berkeley in 2009, with loans from the Small Business Administration, a local bank, and the Alameda County Source Reduction and Recycling Board. The company has a design service that has helped around 30 private industry and local governments in the U.S. and other countries to develop transfer stations that maximize recovery from businesses, haulers and individuals. Learn more at urbanore.com.
Neil Seldman is President of the Institute for Local Self-Reliance in Washington, DC.