The Muscatine Organics Recycling Center (MORC) processes packaged and unpackaged food waste streams, such as meat tubes being fed into the Scott Turbo Separator (above). Operators have fun with the MORC’s “out of this world” connection to the Mork & Mindy television sitcom.
Nora Goldstein
Jon Koch, Director of the City of Muscatine, Iowa Water & Resource Recovery Facility (WRRF), recalls that his path to increasing codigestion of food waste at the WRRF began in 2011 when he wanted to stop flaring so much of the biogas produced by the facility’s anaerobic digesters. “We run boilers with the biogas and flare the rest,” explains Koch. “In the summer, we were flaring gobs and gobs of gas. It seemed like an enormous amount to me, but when we looked at options for utilizing it, we were told it wasn’t enough to entertain other options. So I decided to explore how we could make more biogas.”
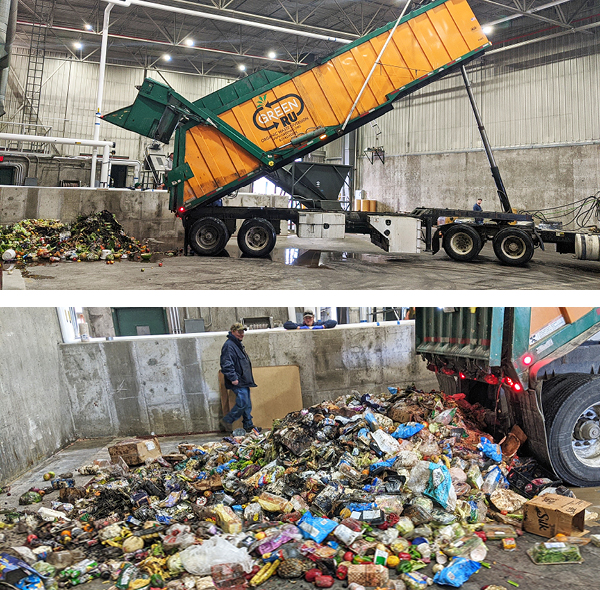
Preconsumer food waste from area grocery stores is tipped onto the floor of the MORC and then put into the depackager using a front-end loader. Photos courtesy of City of Muscatine
The 5.5 million gallon/day treatment plant had been receiving some fats, oils and grease (FOG). Koch began researching availability of other high strength organic wastes and learned that the region had minimal existing capacity to process source separated food waste streams, including both liquids and solids. “We recognized early on that for an investment in food waste receiving and processing to pencil out, two factors are critical,” he says. “First, there must be a really stable source of material from multiple sources available. We have that, with no service of this kind for a very large radius around Muscatine. Second, the organics processing had to pay for itself in tipping fees without being dependent on the sale of the biogas created, so the project could carry on even if energy prices tanked.”
Eight years in, Koch acknowledges that the transition to a full-fledged WRRF with capacity to receive and process food waste and an initial intention to produce renewable natural gas (RNG) has been slow, partially due to bids coming in over budget several times. “But then several fortuitous events lowered our costs,” he explains. “The city’s old recycling center at the transfer station two blocks away, which stopped being used when the city switched to single-stream recycling nine years ago, became available. We were able to convert it much more cheaply into a food waste preprocessing facility — the Muscatine Organics Recycling Center (MORC) — than building a new structure. Further, it had better features than what we would have built, with 40-foot ceilings, and 3 truck docks for unloading. The second event was our ability to repurpose old tanks at the plant for food waste receiving and mixing, versus having to build new ones. The last upgrade, which is underway, is converting an existing center mix square digester into a two-stage continuous plug flow system supplied by DVO, Inc. This gives us capacity to increase the amount of food waste that can be accepted — and thus increase biogas production to tap energy markets.”
Depackaging Capacity
The MORC has a Scott Equipment T42 Turbo Separator designed to process 10 to 20 tons/hour of packaged preconsumer food waste. Packaged and sometimes loose loads of products that need size reduction from food manufacturers are tipped at the facility; the fee is $40/ton. “Area food manufacturers include Nestle Purina, Kraft/Heinz, Conagra and West Liberty Foods, so we are getting everything from dog food to ketchup to sausages,” says Koch. “We also receive source separated loads of preconsumer food waste from six HyVee grocery stores in the region, two of which are in town. We hope to include more local grocers, schools and restaurants in the future once we have increased digester capacity and when things get back to some normalcy where we can go in and do some promotion and training.”
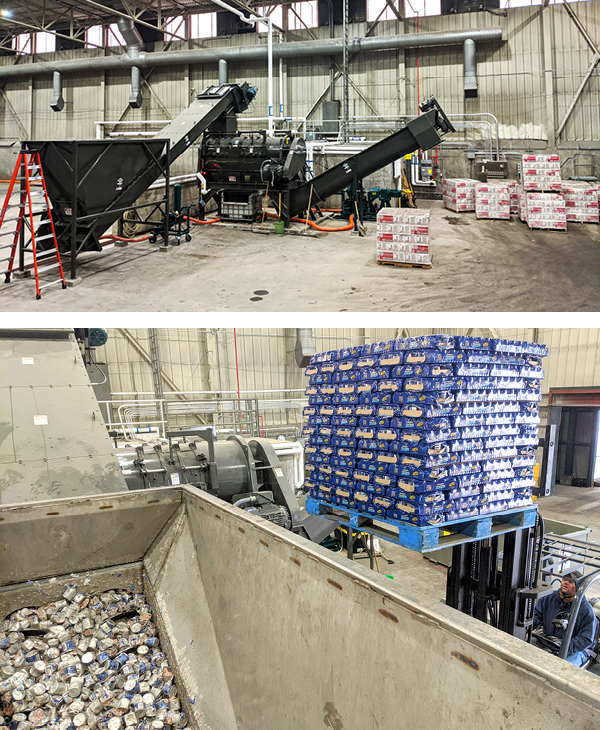
Nonedible packaged food products and beverages are emptied into the feed hopper of the Scott Equipment T42 Turbo Separator with capacity to process 10 to 20 tons/hour. The slurry passes through a one-eighth-inch screen before being transported to the WRRF.
Because the MORC receives source separated organics not mixed with municipal solid waste, the Iowa Department of Natural Resources did not require Muscatine to apply for a solid waste permit to operate the organics recycling facility. The MORC was officially opened in May 2020, after testing the equipment in April 2020. About 1,600 tons of material were received and processed in 2020; Koch anticipates that will increase to 4,000 to 5,000 tons in 2021. “Our goal is to hit $400,000 to $500,000 in tip fee revenues this year, which includes unpackaged solid and liquid waste received at the WRRF, where we charge $0.10/gallon,” he says.
The T42 has a perforated plate with a 1-inch screen on the bottom where the slurried food waste is discharged. That enables contaminants, such as creamer tabs, the plastic pieces used to close bags of bread and rolls, and other smaller items to pass through. To further screen the material, a tote was cut in half and a bowed perforated plate one-eighth-inch holes was inserted on top. Material falls onto the perforated plate, and an operator squeegees the solids so that the liquid falls through. “It’s working okay, but it requires a staff person, so I’m not thrilled,” adds Koch. “We are evaluating an industrial screening system to put on line with the digesters that would screen the wastewater solids before they are pumped to the storage lagoon.”
High Strength Waste Receiving
The WRRF has two complete mix, mesophilic anaerobic digesters with floating covers that have close to 1 million gallons of capacity combined. The square digester being retrofitted will add about 500,000 gallons of additional AD capacity. The plant has two 35,000-gallon blend tanks that had been used to mix primary and waste-activated sludge to feed to the digester tanks. Muscatine had stopped using the tanks, which were still connected to the digester complex. It was determined these would work well for receiving, mixing and feeding food waste streams to the digesters. One tank has been retrofitted; the second will get retrofitted as part of the square digester upgrade.
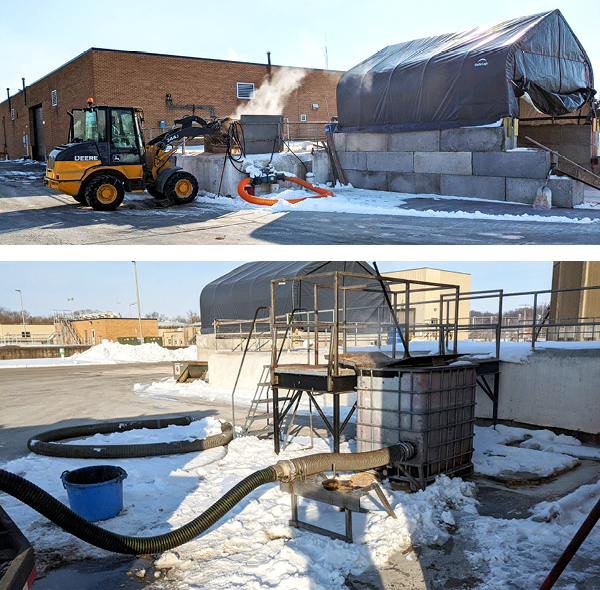
Unpackaged solid food waste is loaded into the top of the high strength waste blend tank (top). Dirty FOG is pumped into a tote that has a bar screen to remove trash (above).
The retrofit involved cutting a hatch into the top of the tank to receive loads of high strength waste (HSW). Trucks unload solid unpackaged food waste into a storage bay next to the HSW receiving tank and the material is dumped directly into the hatch using an end loader. A Vaughan Chopper Pump pulls material out of the tank and recirculates it directly back into the tank through the Vaughan jet nozzle mixer system. The second tank will use the same set up.
FOG pumped from restaurant traps has to be screened to remove items like gloves, hairnets, silverware and other nonorganic items before being added to the tanks. In another stroke of ingenuity, Koch and his team installed a bar screen with half-inch gaps that sits diagonally inside the tote. The bottom behind the screen was cut open to allow material to fall through into a trench that was created when the cement driveway was poured for incoming trucks. Trucks hook on to the side of the tote, which is low to the ground so the contents can gravity flow out the back of their tankers. The trench “weaves and meanders” into the side of the building where a pipe transports the trap waste into the storage tank. “It was a $30,000 solution for what would have been a million dollar project,” notes Koch. “Haulers have to rake their own trash off the screen.”
Liquid from MORC goes directly into the tank at another location, not through the tote screen. About 35,000 to 40,000 gallons/day of HSW, including the slurry from the MORC, can be fed into the digester,” he adds. “Liquid waste haulers call and schedule to come in because we only have so much storage capacity in the blend tank.”
Retention time in the digesters is at least 20 days. About 6 million gallons/year of biosolids are produced, which are land applied on between 460 and 650 acres of farmland near the WRRF. Biosolids are pumped out to lagoons, dewatered, and in the fall, when the soybeans are harvested and before the corn is planted, the material is land applied using a dragline that slices them into the soil.
Next Steps
Capital costs for Phase I — the MORC and retrofit of the HSW tank —were $3.0 million. Phase II, the upgrade of the square digester and retrofitting the second HSW tank, is about a $1.5 million project. “Phase III will be our biogas utilization system with a yet unknown function and cost,” says Koch. “Between 4 and 6 million scf of biogas are produced now, and our hope is to at least double that when the new digester comes on line. We had been moving in the direction of RNG, but with the new Administration and the prospects for activation of the e-RIN pathway of the Renewable Fuel Standard looking like it may come to fruition, we are considering generating electricity instead of RNG.”
The City of Muscatine is currently evaluating microgrid technology to store power for emergency use at the WRRF and sell all remaining power back to the grid. “We can purchase power for less than what we would sell it for with the eRIN in place, but acting as a microgrid can smooth demand charges and protect us from power outages,” he adds.
Recently, Stanley Consultants, the city’s engineer, received the American Council of Engineering Companies of Iowa’s Engineering Excellence Award in the Water/Wastewater Category for the Muscatine codigestion project. The submission, which received a Grand Prize along with the Grand Conceptor Award, was titled “Converting Organic Waste Into ‘Liquid Gold.'”