Craig Coker
BioCycle September 2016
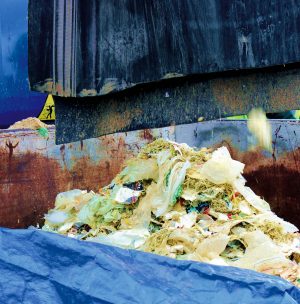
Depackaging commingled food scraps — density is code and force can act as switch to separate packaging. Photo by Nate Clark
Contaminant removal invariably requires some materials be separated from other materials. In its simplest form, separation is a binary process, splitting a feed material into two components. These components could be called the extract (or that which you are trying to recover) and the reject (that which you do not want). The objective of a binary materials separator is to split a feed material into two different components by exploiting some difference in the material’s properties.
The “Code”
Separation of materials requires identifying the appropriate characteristic by which separation can be done — or what material property will you exploit to achieve separation. This could be called the “code,” or signal, to tell a machine how to separate materials (Vesilind, 1984). For example, magnetic attraction is the code for optimizing separation of nails and screws from ground-up wooden pallets. For depackaging, density is often selected as the code for separation. The key separation codes of all recyclables for processing fall into several categories: size, weight, density, hardness, magnetism, electrical conductivity, and light refraction.
The ability of a machine to identify a property’s characteristic and to perform some function, actively or passively, on that material as a result of that information could be called “switching,” or separating the material according to that characteristic. For example, separating colored glass from clear glass uses transparency as the separation code (i.e. transparent vs. variable opaqueness), and uses percent light transmittance as the switch. The glass cullet pieces pass by a photocell. Colored cullet interrupts the photocell light beam, so the code activates an electromagnet that operates a gate directing the colored cullet in one direction. Clear cullet doesn’t break the photocell beam, so the gate remains closed. Another example would be a trommel screen, which uses particle size as the code and screen mesh as the switch, allowing smaller particles to fall through and larger particles to be retained.
Processing and separation systems for organics tend to be either dry or wet systems. Dry systems include depackaging, grinding, shredding, extrusion, screening, magnetic removal, centrifugation, and air entrainment. Wet systems include pulping, filtration, cyclonic classification, flotation and settling. Both dry and wet separation systems rely on this concept of codes and switches.
Table 1 summarizes some of the codes and switches used for binary separation of materials in solid waste and in organics processing.
Separation Efficiency
Separation systems are not infallible; the separation of woody overs from compost will always have some woody material in the screened compost pile. Performance of a separation system is defined by its efficiency, which is a combined parameter that takes into account the capture efficiencies of both the extraction and rejection functions. The metrics used to evaluate separation efficiency are recovery and purity. Recovery is simply the percent recovered (or not recovered) from the entire waste stream feed (percent compost fines captured/not captured vs. percent not captured/captured). Purity is the percentage of the desired recovered material in the total recovered waste stream (i.e. percent screened compost in the finished compost pile); purity can also be expressed as the converse (i.e. percent overs in the finished compost pile).
Most organics recycling separation processes require the separation of one material from a mixture of many materials. This process has one input, the feedstock, and two outputs, the extract (recovered material) and the reject (the remaining material). In materials recovery facilities, a sequence of binary separation steps occurs in series, with each reject stream becoming more homogenous with each step.
Consider a device, such as a star screen, that separates incoming compost into three streams — one is a reject stream of overs and the other two are extract streams that meet certain property characteristics (in this case, size). These are called polynary separators. The performance of a polynary separator can also be described by recovery, purity and efficiency.
Role Of Preprocessing
Efficiencies in mechanical separation can be enhanced with preprocessing to reduce particle sizes. Lenz Enterprises owns and operates a composting facility that processes source separated organics (SSO) — including residential streams — in Stanwood, Washington. It runs incoming loads through a Komptech Crambo slow-speed shredder followed by a conveyor-based sorting line and a magnetic separator. Lenz is able to remove 70 to 80 percent of the contaminants from the commingled residential SSO. The SSO separation codes/switches are: size/shredder screen size, appearance/manual separation, and magnetism/magnetic attraction.
Another example is at the Langage Farm in Plymouth, England, which codigests food scraps with dairy manures. To open the packaging and remove contaminants, Langage Farms opted for a multistage approach, starting with an Atritor rotating drum equipped with paddles that break open the bags. Material passing through the drum screens goes through an Untha shredder for particle size reduction.
A fair amount of plastic, as well as bone, grit, eggshells and glass, end up in the fraction passing through the Atritor. The farm equipped each digester tank with a surface skimmer to remove floating contaminants (plastic, styrofoam, cork, etc.) and a curved scraping arm installed at the bottom of the tank that moves heavy particles to the wall of the tank and pushes them into a sump hole. Collected material is pumped up to a grit separation tank on the roof of the digester; heavy particles fall out, and the liquid is returned to the digester. For this AD system, the separation codes/switches are: hardness/tearing force (debagging), size/screen mesh (screen and shredder), and density/flotation or gravity.
Another consideration is where to place separation equipment in the process train of an organics or conventional recycling facility. The relationships between recovery, purity, and efficiency can drive equipment sizing decisions, quality of downstream processes, quality of recovered materials and overall system efficiencies. For example, a common question in composting is deciding on screening overs out before curing, after curing but before product storage, or after product storage and just before going to market. While the most overs will likely be recovered after active composting (potentially reducing the quantities of fresh bulking agent that must be acquired), the higher moisture content of fresh compost will inhibit screening efficiency, and downstream curing and product storage are at risk of process inhibition due to decreased pile porosity. Screening overs out right before going to market means curing and product storage process footprints must be larger, which, on smaller sites, can be an issue.
Craig Coker is a Senior Editor at BioCycle and a Principal in the firm Coker Composting & Consulting (www.cokercompost.com), near Roanoke VA. He can be reached at cscoker@jgpress.com.
References
Vesilind, P.A., “Basic Principles of Materials Separation,” Proceedings, 16th Mid-Atlantic Industrial Waste Conference, Penn State, June 1984.