Energy efficiency, codigestion and new CHP units have the Victor Valley Regional Water Reclamation Facility in California more than 90 percent of the way to energy net zero.
Nancy Andrews and Logan Olds
BioCycle December 2015
The Victor Valley Water Reclamation Authority’s (VVWRA) regional water reclamation facility (WRF) in Victorville, California began operating in 1981 and treats 12.5 million gallons per day (mgd) of wastewater for the growing High Desert region of southern California. After more than 30 years of service, the WRF was experiencing critical operational challenges. Delayed maintenance had resulted in more than 80 water quality violations and $800,000 in fines. VVWRA’s 2008 National Pollutant Discharge Elimination System (NPDES) permit further lowered the regulatory bar by decreasing the total nitrogen limit to 10.3 milligrams/liter (mg/L) and ammonia-nitrogen to 0.54 mg/L. Because of these stringent limitations, VVWRA’s functional facility capacity was reduced from 18.0 to 13.8 mgd.
In addition, VVWRA’s natural gas and energy consumption was significant given the size of the facility and its level of treatment. It lacked biogas conditioning equipment to lower hydrogen sulfide and siloxane levels and avoid excessive engine-driven blower maintenance. As a result, biogas was being flared and VVWRA was purchasing natural gas at a cost of more than $40,000/month to replace wasted digester gas. Electrical costs were also a concern, totaling nearly $800,000/year amidst rising electrical rates in California.
New Solutions For Old Problems
In 2008, VVWRA began planning secondary treatment optimization and expansion for the WRF to comply with nitrogen permit limitations and increase capacity. VVWRA leaders recognized that these regulatory-focused initiatives also provided an opportunity to incorporate facility features to reduce future energy costs and eliminate natural gas purchases. In addition to nutrient removal, the expansion project included plans to decommission the facility’s three smallest digesters, leaving concrete and steel on site and unused — but still available and capable of producing enough biogas to meet the plant’s energy demands if integrated with an imported organic feedstocks program. Thus the concept for the Waste to Energy project via increased codigestion was born, and VVWRA management established energy neutrality as a utility-wide goal.
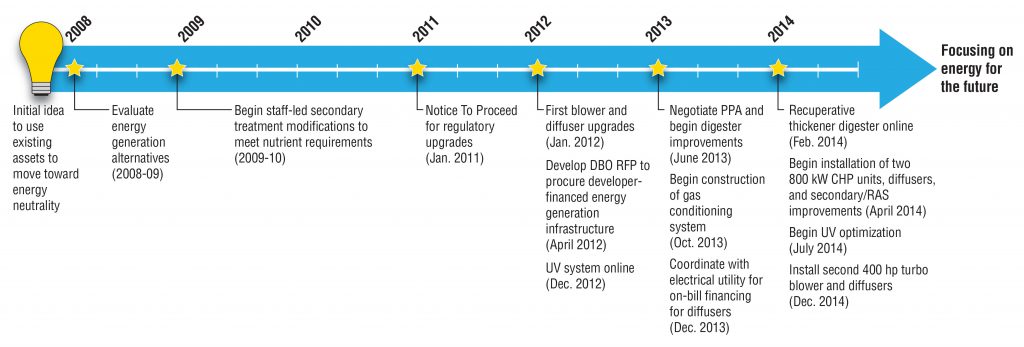
Figure 1. Improvement steps timeline
Figure 1 shows steps taken from 2008 to the present. Staff-led improvements to secondary treatment processes began in 2009, addressing instrumentation for monitoring, repair of aeration diffuser equipment for improved efficiency, and structural enhancements such as internal recycle pumps for added reliability. These steps improved the WRF’s operational efficiency and reduced energy consumption, while also improving effluent quality and expanding plant capacity.
As these measures were underway, VVWRA conducted a facilities evaluation to identify upcoming capital and repair and rehabilitation (R&R) projects likely to occur, in what sequence they would occur, and how measures to improve energy efficiency and generate energy could be incorporated into each project. As a result, the first of two 400-horsepower (hp) high-efficiency turbo blowers was installed as part of the plant’s 2012 energy improvements project.
Variable-frequency drives (VFDs) were also added to return activated sludge (RAS) pumps, eliminating use of six out of ten secondary pumps and two RAS pump stations. These improvements have achieved dual benefits by reducing VVWRA’s required operations and maintenance (O&M) man-hours each year from 1,600 to 640 and WRF energy consumption from 190 kW to 75 kW.
For the ultraviolet (UV) disinfection system, bioassay data were used to demonstrate it was overperforming under normal flow conditions and UV transmittance ranges. The system was optimized in 2012 through staging of lamp modules and installation of more efficient lamps. Facility staff also focused on improving filtered effluent quality to minimize the required UV dose. These modifications reduced site-wide electrical use by 5 percent, saving $8,000 each month.
Securing Creative Financing
VVWRA’s bonding capacity was stretched thin with $200 million committed to concurrent upgrades for the WRF and interceptor system. Bond financing to help the utility achieve its goal of energy neutrality would have resulted in $15 million to $20 million in additional costs incurred by the capital project and significant impacts to ratepayers. VVWRA sought a private technology provider capable of financing the remaining WRF improvements. In 2012, a request for proposals (RFP) was developed for installation of the energy production facilities, structured to require minimal upfront investment from VVWRA.
Knowing the project would result in energy savings, VVWRA took advantage of a power purchase agreement (PPA)/lease arrangement through which the selected contractor would develop and own the energy infrastructure and recoup its investment via contracted sales of energy. The RFP for the PPA arrangement also covered installation of the second high-efficiency aeration blower, allowing payments for these capital upgrades to be built into monthly electrical payments for the PPA.
In April 2013, VVWRA entered into a 20-year PPA with Anaergia, Inc. Biogas that previously had been flared now generates electricity used on-site, reducing VVWRA’s dependency on energy from local utilities. Anaergia designed, built and will own the renewable energy system, with no capital cost to VVWRA.
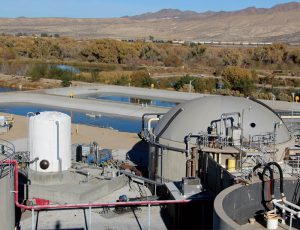
The Omnivore™ recuperative digestion system was installed in one of the WRF’s decommissioned digesters, increasing capacity for higher quantities of off-site organics. Photo courtesy of Victor Valley Water Reclamation Authority
The PPA also created additional opportunities for public-private partnerships. In 2013, VVWRA worked with Anaergia on a pilot project to install the company’s Omnivore™ recuperative digestion system in one of the WRF’s small decommissioned digesters. Anaergia had received a $2 million grant for the pilot from the California Energy Commission. The system increase loading capacity, produces more gas with existing tank infrastructure, and incorporates efficient hydraulic mixing with low energy demand. The process also decouples hydraulic residence time from solids residence time, keeping solids in the digester longer and allowing for greater solids destruction and increased biogas production. The Omnivore system went on line in February 2014. A Tecon double-membrane gas holder was also installed.
Codigestion
Codigestion was recognized as a central feature of the WRF’s energy neutrality program and an opportunity to derive economic value from underutilized digestion tanks. Beginning in 2011, VVWRA’s facility became California’s first wastewater treatment plant to receive preprocessed food waste screened and slurried off-site by a major commercial solid waste company. This experimental “walk before you run” approach helped bring VVWRA staff up to speed on a new operation prior to designing and operating a permanent facility.
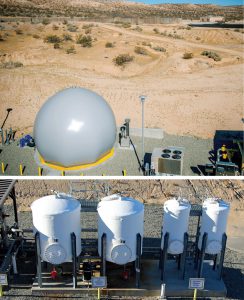
New biogas-related equipment includes a Tecon double-membrane gas holder (top) and gas conditioning (bottom) sized for double the normal biogas flow at that time. Photo courtesy of Victor Valley Water Reclamation Authority
To prepare for future large-scale codigestion, an unused dissolved air flotation thickener (DAFT) unit was converted to a fats, oils and grease (FOG) receiving and pump station in early 2014. The new receiving station began accepting imported FOG, waste from local pet food processor ADM, and other feedstock from local businesses. Codigestion of these new resources more than doubled biogas production from 200,000 cubic feet/day (ft3/d) to 500,000 ft3/d.
Modifications using the Omnivore system also increased the digester’s capacity to receive higher quantities of off-site organic waste streams. Codigestion trials with the modified digester started in June 2014.
Gas conditioning was installed in late 2013 as part of a larger regulatory upgrade to the facility. Conditioning equipment was sized for double the normal biogas flow at that time, given VVWRA’s plans for increased codigestion. These projects eliminated the need to purchase natural gas, saving VVWRA $40,000/month. All of the WRF’s operating digesters are used for codigestion.
Anaergia has invested $10 million to design and build the renewable energy system (including installation of the Omnivore system). That investment includes two 2G Cenergy 800-kilowatt internal combustion engines procured in 2014.
Achieving Net Zero
At current gas production levels, the WRF could be generating 1.3 megawatts (MW). Currently, the plant is using an average of 1.1 MW, indicating that the system could potentially generate 0.2 MW of energy more than it uses. By summer 2016, the facility is projected to export up to 25 percent of the energy it generates to Southern California Edison (SCE) at $0.12/kWh. VVWRA also has the foundational infrastructure in place to create new ways to use surplus biogas with limited future investment. For example, VVWRA has considered exporting compressed biogas to offset a local industry’s use of propane.
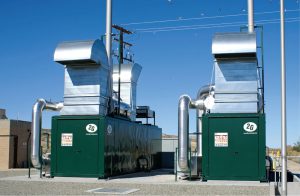
Two 2G Cenergy 800 kW internal combustion engines were procured in 2014. Currently the WRF uses an average of 1.1 MW of the power produced. Photo courtesy of Victor Valley Water Reclamation Authority
Among the lessons learned over the years is that coordination with the electrical utility is critical. Electricity produced on site has increased to 27,000 kWh/day, accounting for 93 percent of the electricity consumed by the WRF. However, SCE requires a minimum grid purchase of 80 kW at all times to avoid potential to back feed to the grid, creating a barrier to achieve complete energy neutrality in the near term. In addition, newer engines are very sensitive to power quality, and the VVWRA engines have experienced outages due to inconsistent grid power voltage.
The plant’s improved processes have reduced operating issues and related costs and operations staff have a facility they are proud to operate. Less manpower is needed for facility O&M, allowing staff to focus more time on further improving the process efficiency of other areas of the plant, including the UV and cogeneration systems. These improvements are gaining recognition: the National Association of Clean Water Agencies awarded VVWRA a 2015 National Environmental Achievement Award in the Operations & Environmental Performance category.
Less than 10 years after facing more than 80 water quality violations and nearly $1 million in regulatory fines, the VVWRA WRF has been named the second-best plant of its size in the state of California for two consecutive years, and is on its way to being one of the nation’s first completely energy-neutral wastewater treatment facilities. With final infrastructure now installed, the WRF has largely eliminated its dependency on outside power sources and creates more biogas than it uses.
Nancy Adams is a Supervising Engineer at Brown and Caldwell. Logan Olds is General Manager of the Victor Valley Wastewater Reclamation Authority. This article is excerpted from a Case Study about the Victor Valley Water Reclamation Authority’s energy neutrality initiatives, prepared for the Water Environment Research Federation.