Forest City Enterprises, one of the nation’s largest real estate developers, is investing in anaerobic digestion to reduce energy costs and ease the load on municipal infrastructure.
Nora Goldstein
BioCycle September 2013, Vol. 54, No. 9, p. 32
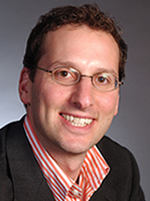
BioCycle REFOR13 Keynote Speaker Jon Ratner, Forest City Enterprises, Vice-President of Energy, Sustainability and Asset Management
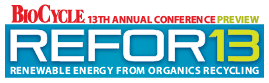
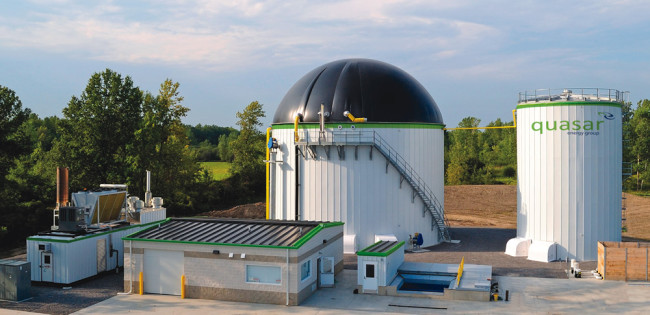
Forest City is majority owner of the anaerobic digesters built with quasar energy group. A newly constructed facility in Buffalo, New York (left) is sized to generate 765 kW/hour.
To date, Forest City has partnered with quasar on five anaerobic digestion projects — Phase I of a 1.3 MW/hour plant in Cleveland (Collinwood facility) that began operating in 2012 and Phase II currently under construction to double its capacity, two digesters in western New York State — one in Buffalo (sized at 765 kW/hour) and the other in Wheatfield (also 765 kW/hour) — and a fourth in Wooster, Ohio at the city’s wastewater treatment plant, where idle digesters are being retrofitted to quasar’s specifications. All the digesters process biosolids, food waste and FOG (fats, oils and grease). Some of the food waste received at that plant is collected from Forest City’s Tower City Center, located in downtown Cleveland.
Forest City is the majority owner of the digesters; quasar is a minority partner and also the contractor, builder and operator. The Collinwood digester is located on property owned by Forest City, however that isn’t the case with the other digesters. “We try to build on land we own, but that is not a rule,” notes Ratner. “And we plan to divert food waste when it is generated at properties we own and/or manage that are located where we have digesters, e.g., the Boulevard Mall in Buffalo.”
The investments in anaerobic digesters offset Forest City’s energy usage. “For example, the electricity generated at our digesters in western New York will be wheeled to our real estate properties in New York City, such as the Barclays Center arena in Brooklyn,” he explains. “Essentially we are making the power in the Buffalo region and selling it in Brooklyn. Our strategy is to build digester plants closer and closer to our core market areas.”
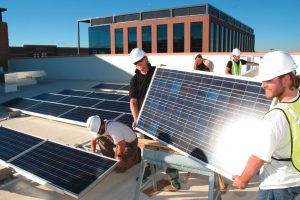
In 2012, the company’s solar developments and AD plant in Cleveland generated 6.2 MW of power. An additional 35 MW of power generation is in the pipeline.
Sustainability Vision And Commitment
Forest City was founded in 1920 by Jon Ratner’s grandfather and his great aunts and uncles. The company started out by selling building materials, but in the 1930s, evolved into real estate development. In 1960, Forest City became a publicly traded company (on the New York Stock Exchange). Its core market centers are in Boston, Dallas, Denver, Los Angeles, New York City (including Philadelphia), San Francisco and Washington, D.C., although it has assets in other markets. Recently, Forest City released its 2012 Corporate Sustainability Report, “Built On Purpose,” which states, “by reusing materials and making use of or improving existing infrastructure, we reduce the environmental impact of our developments and maximize their integration within a community.”
As Vice-President of Energy, Sustainability and Asset Management, Ratner helps lead Forest City’s Integrated Design Group, which oversees energy management and renewable energy, as well as green building and workplace designs. “As we go through the process of constructing and managing a real estate property, we want to learn from what we’ve done and continually improve with our next property,” explains Ratner. “Waste reduction and recycling, water conservation, air quality, transportation infrastructure, energy and green infrastructure are all part of the continual improvement process.”
After the recession hit in 2008, projects in Forest City’s development pipeline dwindled, Ratner and his team gave the company’s executives a proposal that suggested redirecting the skill set of people involved with new property development to work on developing renewable energy capacity, i.e., building energy-generating assets. “We made the case that the Integrated Design Group could utilize a lot of the skill sets that Forest City already had in-house to develop, permit and build these assets,” he says. “The directors supported this strategy.” According to “Built On Purpose,” the company’s renewable energy installations generated 6.2 MW of power in 2012 from five solar developments and the AD plant in Cleveland. The solar developments include Pearl City Peninsula in Hawaii, where 4,300 solar panels were installed on a 5-acre brownfield site; the installation generates 1.2 MW of energy. Ratner notes that the company has an additional 35MW of power generation in its pipeline.
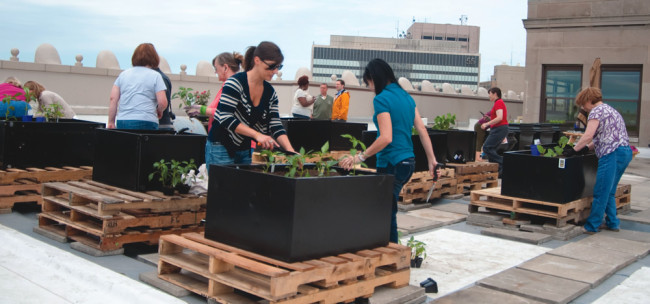
A 5,000 sq ft rooftop garden was installed on the 15th Floor of Forest City’s headquarters, located in Terminal Tower in Cleveland. Food scraps from office kitchens are composted in tumblers adjacent to the garden.
Terminal Tower is part of Tower City Center, Forest City’s 5-million sq ft mixed-use center in the heart of downtown. The retail portion of Tower City houses three levels of shops, a food court and restaurants. Recently, Forest City installed an on-site processing system developed by InSinkErator to divert food waste from the retail mall section of the Tower City complex, including the food court. Grind2Energy™ (see sidebar) is a nonsewer-based food waste recycling system that includes an InSinkErator grinder connected to a storage tank. About 1-gallon of water per minute is used to facilitate the grinding. Tower City installed the grinder in an area behind the food court; a 2,500-gallon tank is actually located two stories below in a parking space in the garage, so the slurry is piped from the grinder to the tank. A vacuum truck empties the tank as needed and hauls the slurry to the Collinwood digester.
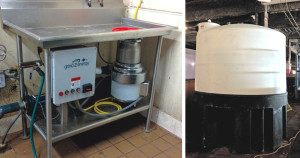
A Grind2Energy™ system was recently installed in Tower City Center, Forest City’s 5-million sq ft mixed-use complex to process food waste collected from the food court and restaurants. Food waste is sorted and ground (left); the slurry is piped to a 2,500- gallon storage tank located in the parking garage where it is stored prior to transport to the Collinwood digester.
The knowledge gained in the energy efficiency arena, combined with the experience and early success with its anaerobic digestion investments, not only reduces expenses within Forest City’s managed portfolio, but also provides an opportunity for Forest City to grow its “top line” as well. One recent example comes from a redevelopment opportunity of millions of square feet of municipally controlled entitlements in one of Forest City’s core markets. The city’s goals for this project are to be net zero waste and net zero energy by 2030 (i.e., not buying energy), be carbon positive by 2050 (i.e., selling power back to the grid) and reclaim and reuse all the water. “The city wants the first 50 percent of net zero energy achieved through energy efficiency and rooftop solar, and the next 50 percent achieved through other technologies,” he adds. “Anaerobic digestion and biofuel are included on the list of other technologies, which we have put into the proposal we submitted. The solar piece is just power. What we submitted covers water, energy and waste. And I don’t think there are a lot of other real estate developers who know what anaerobic digestion is, let alone have 5MW of capacity — this is a great differentiator for us.”
Before ending BioCycle’s interview with Jon Ratner, we asked if Forest City Enterprises is finding the technologies and know-how required to advance the sustainability of the company’s properties readily available in the marketplace today. “I would have to answer no,” he says. “While there are beneficial technologies available today, there are burdens to using them. Cost is among these burdens, but the knowledge to understand and manage them well is still a significant obstacle. We can make progress with the technologies now available, but we can’t solve the problems that exist today. My belief is that we will continue to need public investments to move us from the current paradigm to a new paradigm of sustainability. This, along with the very significant current of market demand for socially and environmentally equitable products and services is what will lead to transformative change. Part and parcel of this movement will be reinvestment in our urban cores with a focus on locally produced commodities — local food, local energy and energy generation, all leading to healthy communities — which includes jobs!”