Mitigating fire hazards and resource utilization offer two good reasons to harvest diseased lodgepole and ponderosa pine trees from the forests of the West.
Dan Sullivan
BioCycle July 2012, Vol. 53, No. 7, p. 28
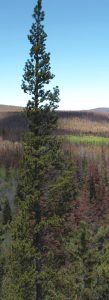
Colorado’s current mountain pine beetle epidemic is poised to kill 90 percent of the state’s lodgepole pine trees while leaving the region highly vulnerable to forest fires.
The mountain pine beetle (MPB), Dendroctonus ponderosae, is a species of bark beetle native to the forests of western North America. These insects inhabit ponderosa, lodgepole, Scotch and limber pines, preying on trees under stress from poor siting, fire damage or other injury, root disease, overcrowding or old age. The MPB normally plays a critical role in the forest ecosystem, culling weaker trees and catalyzing new growth. But uncharacteristically hot and dry summers in recent years, coupled with mild winters and overcrowded mature stands, particularly of lodgepole pines, have instead catalyzed an epidemic. Those who make a living out of the forest have a limited time to harvest the damaged trees before they become useless and settle to the forest floor, thus presenting a major fire hazard.
“We have 7,000 acres of our own that we thinned, and we saved a ton of fiber,” says Steve Marks, owner of Marks Lumber in Clancy, Montana. This was accomplished by both harvesting some trees before they were ravaged and by mitigating damage to the trees left standing. Marks explains: “If the trees had space around them, the bugs didn’t bother them as much. We had 10 percent or less mortality. But where they were closed in — the lodgepoles in particular — they took a big hit.” By Marks’s estimation, unmanaged stands in Montana have suffered a loss of between 50 and 100 percent since the epidemic began there in late 2005. “The folks who didn’t do anything now have nothing but a huge liability,” he adds. “There’s so much beetle-killed timber on the ground that it could cost hundreds of dollars per acre just to get it cleaned up, depending on the species.”
The MPB has a hard black exoskeleton (outer covering) and measures between one-eighth and one-quarter inch long. They lay eggs under the bark and introduce blue stain fungus into the sapwood, effectively preventing the flow of pitch, a primary defense mechanism trees have against infestation. Water and nutrient flow are also blocked, and a besieged tree typically dies within a few weeks (it usually takes about year for the needles to turn from green to orange). The beetles then move on to another tree. “After a tree dies, two things happen,” says Marks. “Initially, there is a heavy loading of fuels from the dead pine needles that are still on the tree. When the needles drop to the forest floor [where they present less of a fire hazard], the trees are still standing. Then the trees start breaking off and loading fuel back up again.”
Without some sort of subsidy, says Marks, it just doesn’t make economic sense to deal with the dead trees that have been standing for more than a couple of years. “When harvesting you can’t drop them like green trees; with ponderosa pines, we will have a 70-foot-tall tree break into three or four pieces and come down right on top of the feller bunchers. There is minimal activity in the export market for low-grade dimensional lumber, but the ponderosa pine has deteriorated so rapidly it has no lumber value, and as for hog fuel we are 250 miles away from any conversion facility. The costs are so high for logging and grinding it that it is just not economically feasible unless someone subsidizes it.”
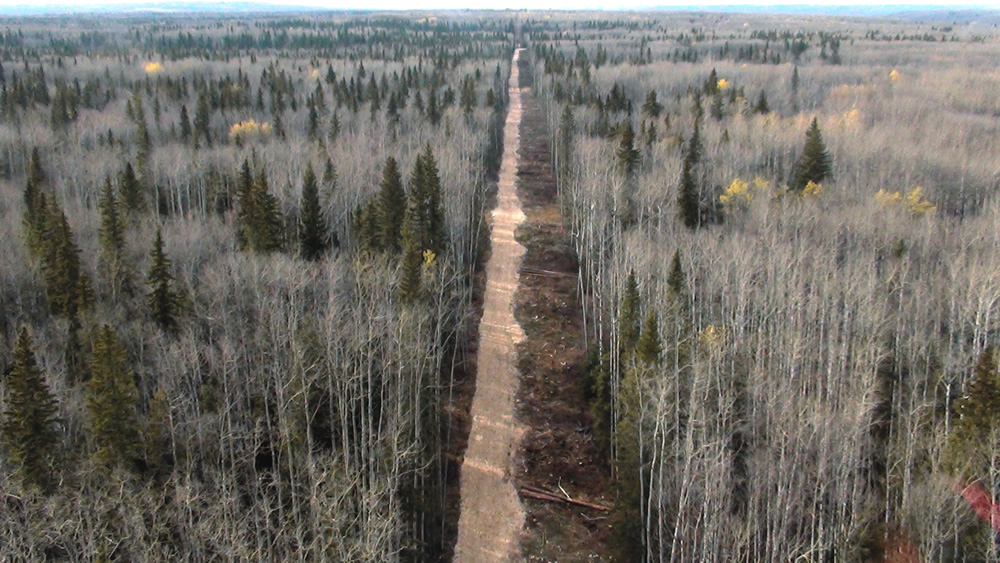
Triple G Construction in Alberta, Canada, utilizes ground wood chips to stabilize temporary roads built for oil and gas exploration.
Lodgepole pine trees don’t rot as quickly as ponderosa so remain salvageable for a few more years. Earlier on in the epidemic, which Marks observes has tapered off as evidenced by the lack of healthy green pines turning the telltale orange, the preferred method of harvest was to get into an infected area with mechanical equipment. For Mark’s Lumber, that included a feller buncher, a grapple skidder, stroke delimbers and a Rotochopper B66 horizontal grinder. The chipped trees were then sent 275 miles for use as boiler fuel at a food production facility.
Biomass Energy
Government subsidies help bridge the cost gap between removing the diseased wood and its diminished market value. “Without market value, government subsidies do help with harvest costs,” says Julie Kies, Montana Department of Natural Resources and Conservation Biomass Utilization Program Manager. Subsidies can also help support the enhancement of wood and biomass markets and forest business practices that sustain a more diverse and resilient forest product/biomass industry. “There is a lot of interest and burgeoning opportunities for a mini industry developing around biomass in Montana,” she adds. “…Biomass fuel suppliers have invested in equipment to improve fuel quality and efficiency of delivery. There used to be only two engineering firms in the state developing wood biomass energy projects; now we have at least nine. A total of 14 public schools and hospitals burn biomass for heat, and some portion of that wood is beetle-killed. In total, these facilities are consuming about 6,500 bone dry tons/year of biomass.”
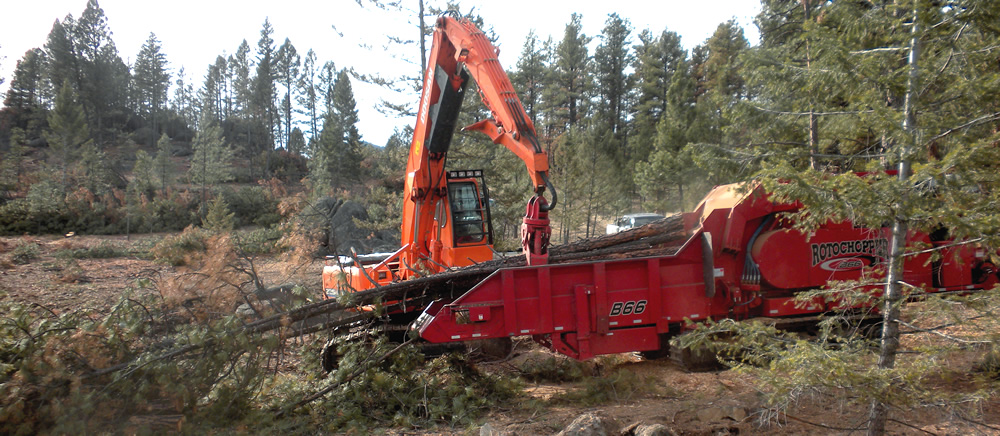
Marks Lumber in Clancy, Montana, utilized a Rotochopper B66 horizontal grinder to process beetle-killed pine trees into chips for boiler fuel.
Kies concedes that 6,500 dry tons is a small volume, particularly considering the near 1 million tons of chips and hog fuel that were purchased annually by the Smurfit-Stone Container pulp mill in Frenchtown, Montana, before it closed in 2009. “This leaves smaller mills seeking outlets for their milling residue, and everyone seeking outlets for logging residues and small-diameter logs from hazardous fuel reduction treatments and precommercial thinnings, not to mention sawlogs,” says Kies, adding that many mills in Montana have been burning their own mill residues for on-site heat/energy production since the 1980s.
She also references several companies developing innovative uses for the biomass. Blue Marble Biomaterials, for example, is extracting high-value compounds from organic wastes, including beetle-killed wood, for the food, flavoring and fragrance industries. Algae AquaCulture Technologies, located at Stoltze Land and Lumber mill in Columbia Falls, Montana, is using beetle killed wood as a feedstock for producing energy, soil amendments and food crops (see “Greenhouse Packs A Power Punch, July 2011). “The Stoltze mill is expanding its biomass-fired combined heat and power system to provide electricity to neighboring renewable energy markets,” says Kies. Blue Dog Furniture, a custom manufacturer, is using beetle-killed blue-stain wood in its products. And Western Montana was selected as a pilot region for the Northwest Advanced Renewables Alliance initiative to build a supply chain for jet fuel from forest biomass. “In Montana, the supply source would definitely include beetle-killed trees,” she adds.
One challenge for waste-biomass-to-energy projects to the north in British Columbia, suggests Mike Jennings, president of Northland Chipper Sales in Langley, is that electricity is inexpensive. “All the electric power comes from hydro,” he says. “It’s cheap and it’s green and tough to compete with.” Jennings adds that a number of pulp mills like to get beetle killed wood chips from central BC where the weather is dryer, making for fuel with a lower moisture content that performs better in their boilers. “They use it to displace natural gas,” he explains.
Beetles Know No Borders
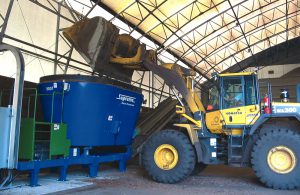
Processed wood waste and biosolids from the cities of Kelowna and Vernon, British Columbia, are loaded into a Supreme Enviro-Processor 900 batch mixer for composting.
In British Columbia, contractor Andy Bouchard grinds wood waste — including beetle-killed wood, segregated clean construction (“white”) wood, pallets and limbs and branches — for the cities of Kelowna and Vernon and at 16 other regional landfills. He uses a 6800 CBI Track Grinder, which stays put in Kelowna, and a pair of Diamond Z 1260s, which make the rounds at the other landfills as needed. “It could be a week or it could be a month,” says Bouchard. “It all depends on how much material comes in.” Segregating the wood for processing is done by staff at each landfill. While fee structures vary, there are some constants. “If it’s clean wood, then there is less of a tipping fee,” he adds. “If it’s dirty, they pay more per ton.”
He processes about 120,000 cubic yards/year of wood waste for Kelowna, about 60 percent of which is cocomposted with about 30,000 wet metric tons/year of biosolids at a composting facility jointly owned by the cities of Kelowna and Vernon. “The rest of the wood chips are shipped to a local mill for cogeneration of power,” says Gordon Light, city of Kelowna Organics Supervisor. “We trade the material shipped to the mill for hog fuel from the mill.” The hog fuel is also composted with the biosolids. Light and Bouchard estimate that about 5 to 10 percent of the woody feedstock processed in Kelowna is beetle-killed pine.
The biosolids and wood waste (ground to a specification of 90 percent passing a three-quarter-inch sieve) are mixed with smaller amounts of water and ash using two Supreme Enviro-Processor 900 batch mixers. Materials are composted on two 88-foot by 610-foot pads designed by Engineered Compost Systems (ECS). Each pad contains built-in trenches with perforated stainless steel covers that allow for both positive and negative aeration. Initial stage composting is 21 days; secondary stage composting on another section of the aerated pad is about 24 days. Finished compost is screened with a McCloskey trommel to half-inch and placed in rows for final curing. It is sold under the brand name, Ogogrow, a popular landscape, nursery and garden product that in 2011 netted $614,000 in revenues.
Another market for the recovered wood is remediation of oil-contaminated mud left behind by oil and gas exploration taking place in the past decade. Bouchard and his stepson, third-generation logger Del Kohnke, figured out that by mixing wood chips with the contaminated mud into a composting pile, the hydrocarbons break down.
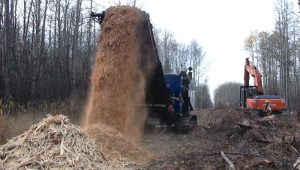
Triple G Construction utilizes a pair of Peterson Pacific 4710B grinders to process wood waste in the forest.
About 600 miles to the north, operating out of Grand Prairie, Alberta, Triple G Construction, which has made a side business by managing MPB damage, also found a niche market in gas and oil exploration. The company uses the chips to provide a navigable base for temporary roads. “This product is good for muddy sensitive sites and makes for a safer work area,” says owner/supervisor Gervin Antypowich, adding that he uses a pair of Peterson Pacific 4710Bs equipped with 1-, 2-, 4- and 6-inch screens to grind the wood. The company also markets sawdust mixed with fractured 1-inch long strands of the beetle-killed wood for mixing with liquids drained off of sumps. This provides safer transportation to landfills.
Fighting Fires With Forest Management
In Ft. Collins, Colorado, Morgan Timber Products manufactures a wide range of products, including fencing, posts, poles, specialty lumber, landscape mulch, livestock bedding and biomass. “We try to use every size and shape that comes out of the forest in some market or another,” says Karen Morgan, who owns and operates the company with her husband Mark. That includes harvesting and utilizing beetle-killed wood. “People love the tongue and groove paneling with the blue stain,” she says.
At the time BioCycle contacted Morgan Timber Products, one of the largest wildfires in Colorado history, the High Park Fire, had already consumed 53,000 acres and was raging right outside Ft. Collins. (By press time, the fire had burned 87,000 acres and destroyed 259 homes.) The Morgans, who have helped manage a number of wildfires over the 38 years they have been in business, feel that much of the destruction could have been prevented through more active forest management. “The Forest Service wanted to hire harvesters to cut the fire line on the High Park Fire, so they allowed us to remove our TimberPro Harvester and our Morbark 3 Wheel Shear from within the fire area to help build line,” explains Karen Morgan. “The reason our machines were not burned was because we had been working on a private landowner’s 400 acre property doing mountain pine beetle mitigation work for quite awhile. We make a habit of parking equipment in the middle of the most-open area. It did do what it was supposed to, which was to drop the fire from a crown to a ground fire, thereby slowing the progress.”
Seated in Idaho Springs, Colorado (about 30 mile miles west of Denver), Clear Creek County rents out a Vermeer BC600XL Brush Chipper for $125 per eight hours logged onto the machine in order to encourage residents to practice fire mitigation around their property. “It can handle up to a 6-inch-diameter branch, says Michelle Harrison-Lipe of the Clear Creek County Transfer Station/Recycling Center. “Basically, they limb the tree and utilize the logs or let people come get the logs. The chipper is just basically to let people deal with the slash.” The program is hugely popular, she adds. “We have a lot of dead trees, and if people are cutting down trees at their house and have a lot of tree branches, they often prefer to just chip them right on their property as opposed to bringing them here.”
The cost to residents who do bring slash to the transfer station is typically $8/cubic yard (cy), although it is currently free to county residents until the end of September. The slash is loaded into a Maxigrind, which processes the material into varying size chips, depending on the end use. The majority goes to the Alpine Waste & Recycling composting facility about 30 miles away. “To date, we’ve taken about 1,000 cubic yards there,” says Harrison-Lipe, adding that not all of it is beetle-killed pine.
Forty miles northwest of Idaho Springs, more than 70 percent of the pine trees within the 23,000-acre Fraser Experimental Forest (surrounding the town of Fraser) has already succumbed to the mountain pine beetle. In order to turn a problem (fire hazard) into a solution (wood chips for biomass and other experimental uses), researchers moved in with a Bandit Model 990XP 12-inch drum chipper. “You see all these acres of dead material and this huge short-term supply,” says U.S. Forest Service biochemist and researcher Chuck Rose. “The question is, what can we do with it?”
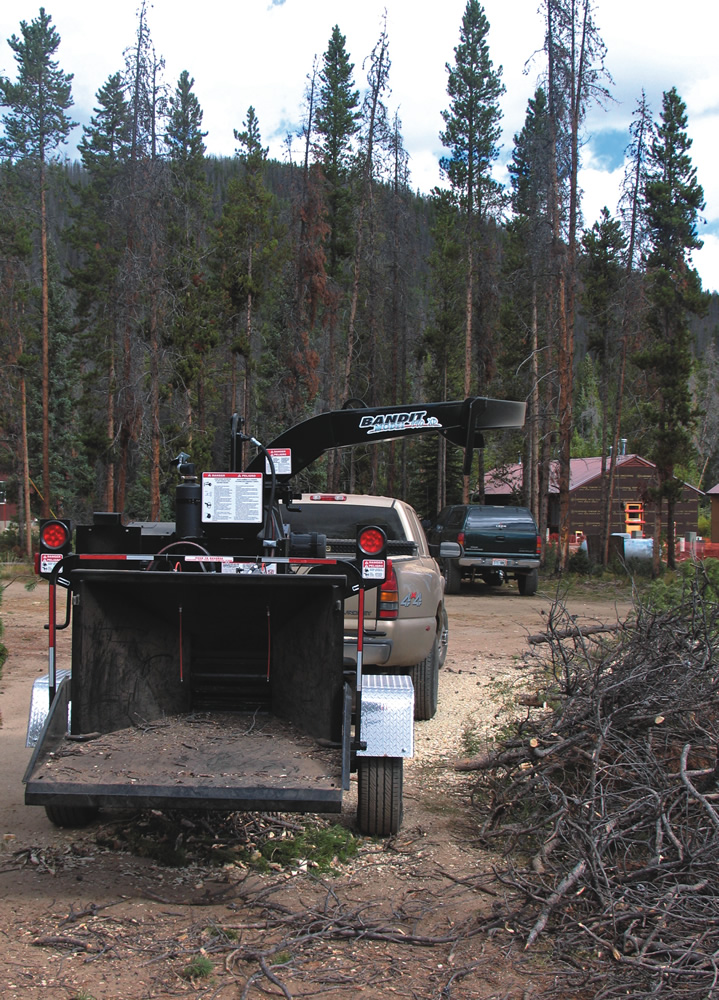
Researchers at the Fraser Experimental Forest in north central Colorado use a Bandit Model 990XP chipper to process beetle killed wood for a number of exploratory uses.
Collaborating with scientists at the Rocky Mountain Research Station in Ft. Collins and building on a 70-year history of pioneering investigation, Rose and his team are looking at how the blue stain might alter the chemical composition of the wood, thereby making it a more, or perhaps less, useful product. Part of their investigation involves sending the chips to Biochar Engineering Corporation (BEC) in Golden, Colorado, where pyrolysis units cook the chips into biochar, which can be used as a soil amendment to retain water, lower the soil’s bulk density, enhance absorption of ammonium, reduce erosion and aid in carbon sequestration. Rose says the Bandit Model 990XP, which can process logs up to 14 inches in diameter, has proven an ideal tool for the job. “The guys at BEC said our chips are their favorite feedstock to process so far.” Some of the biochar is returned to the Fraser Experimental Forest, where it assists with restoration work.