The newest project to come on line in North Carolina collects biogas from 5 hog farm digesters and conditions it for pipeline injection.
Craig Coker
BioCycle June 2018
Approximately 9 million hogs live on 2,217 farms in several counties in eastern North Carolina (NC), making that state second only to Iowa in terms of swine population. Hogs produce between 2.3 pounds (lbs) and 13.1 lbs/day of manure, depending on the size of the hog. Based on March 2018 U.S. Department of Agriculture data on NC hog populations and weights, this passel of pigs produces over 8.7 million tons of manure annually.
Hog manure as excreted contains about 90 percent moisture and 7 percent biodegradable (or volatile) solids. Manure from a 150-lb hog has a biogas generation potential of 4.8 cubic feet (ft3)/day. Adjusting for energy consumption for digester heating and pumping, net yield is around 3.2 ft3/day for that hog. Total swine manure biogas net yield potential in NC is around 28.8 million ft3/day, which has a potential energy value of about 18,000 million British Thermal Units per day (MMBTU/day). Given the average U.S. household consumed 250,000 BTU/day of energy in 2009 (most recent data), this renewable energy potential is greater than the total energy consumed by 70,000 households.
The vast majority of hog farms use a liquid flush system to clean manure out of the barns, so a great deal of water is used to dilute the manure down to the desired 0.5 percent solids content. This wastewater is stored outside in one of 3,300 lagoons in NC. Adding in the flush water, there is more than 52 million tons of wastewater in those lagoons, all of which is now land applied to cropland. The land application of swine manure to farm fields has not been without controversy.
Capturing the biogas yield potential of that much wastewater volume would require very large and numerous reactor tanks, so covering lagoons with high-density polyethylene (HDPE) liners has emerged as a much more cost-effective approach. That was the approach used by innovative renewable energy projects in Duplin and Yadkin Counties in NC.
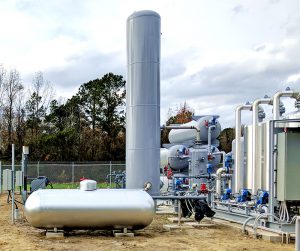
The biogas upgrading system at Optima KV consists of pressure-swing absorption to remove CO2, H2S and other constituents. Cleaned biomethane is pressurized to be sold to Duke Energy via its subsidiary, Piedmont Natural Gas. Photo courtesy of Cavanaugh
Optima KV
Optima KV is a collaborative venture between Smithfield Foods, two local swine herd farmers, engineering firm Cavanaugh Associates, and outside investors to make Renewable Natural Gas (RNG, also called biomethane). Manure is pumped from the animal barns into a HDPE-lined and covered in-ground digester at each of the five contiguous farms housing 60,000 pigs owned by the two farmers. These digesters vary in capacity from 1.7 million to 3 million gallons. In the event of operational issues with the digesters, a gravity emergency spillway will redirect the manure back to the original wastewater lagoon. The digesters are mixed with liquid recirculation pumps, which can also be used for sludge removal from the digesters. The digesters are equipped with internal baffles that help separate solids and liquids so the hydraulic residence time for the liquid fraction is about 30 days, while the solids residence time is about 90 days.
Digestate from the reactors is routed back to the farms and stored in the existing wastewater lagoons prior to land application. Odors from the land application of raw swine manure have been contentious in eastern NC and the digestate from the reactors likely has a much lower odor profile due to the anaerobic degradation of volatile fatty acids in AD, although no odor-specific evaluations have been conducted.
Each farm is outfitted with a low-power compressor that pulls the biogas from beneath the covers, filters it to remove particulates, and removes the moisture through a condenser. The preconditioned biogas is routed to a central gas clean-up facility on Smithfield Foods’ property (about 3 miles distance from the farms) through low-pressure piping. Each farm is equipped with emergency flares if there is an operational issue with the central facility.
Gas Clean-Up
The gas clean-up system (nicknamed “GUS”) consists of pressure-swing absorption to remove carbon dioxide, hydrogen sulfide and other constituents. The cleaned biomethane is pressurized to 100 lbs/square inch (psi) to be sold to Duke Energy via a subsidiary, Piedmont Natural Gas, which operates the natural gas distribution network in eastern NC. The pipeline injection standards are typically rigorous (see “Pipeline Injection of Biomethane in California” March/April 2018) and real-time gas analyzers on both sides of the interconnection monitor gas quality. Table 1 compares Optima’s gas quality to the injection specifications.
Optima KV entered into a 15-year agreement with Duke Energy to produce 80,000 MMBTUs/year of RNG. This will create about 11,000 megawatt-hours (MWh) of power produced at Duke Energy’s natural gas-fired plants in in Wayne and New Hanover Counties. The biomethane produced by the Optima KV project will partially replace the fossil-fuel natural gas consumed by those two electricity generation stations (an approach known as “directed biogas”).
Pipeline injection of biomethane can be advantageous over direct on-farm generation of electricity for sale to the grid. While injection depends on the availability of a nearby pipeline infrastructure with adequate capacity and the gas upgrading equipment can be expensive, direct sales of electricity to the grid are hampered by low purchase prices, the reality that electrical distribution systems are designed as radial networks delivering power in a unidirectional way from substations to consumers, and the need for interconnection protection systems that protect the grid from voltage fluctuations and potential short-circuit damages.
“We see directed biogas in eastern NC as having a lot of potential,” says Gus Simmons, Director of Bioenergy for Cavanaugh LLC and manager of the Optima KV project. “We built GUS with extra capacity, so we have the opportunity to connect more swine farms in the future. As biomethane can be used for any purpose currently met by fossil fuel natural gas and because Renewable Identification Numbers and state-based renewable energy credit programs do not require the specific molecules of biogas to be used by specific users, we see great opportunities for the North Carolina swine industry to export farm-based energy across the country.”
The Optima KV project began producing biomethane to injection quality specifications in November 2017 but couldn’t actually inject it until March 2018 due to delays in building the interconnecting piping as it was the first project of its kind in NC. “It was a lengthy process,” Simmons notes, “but we expect it to become much more streamlined.” The biomethane sold to Duke Energy is worth 11,200 Renewable Energy Credits (RECs) per year to the utility, helping it meet obligations under the NC Renewable Energy Portfolio Standard (see sidebar).
Loyd Ray Farms
In 2008, Duke University and Duke Energy teamed up to develop an anaerobic digestion system at Loyd Ray Farms in Yadkin County, a swine finishing facility with nearly 9,000 pigs at any given time. The system began operating in May 2011. Gus Simmons from Cavanaugh designed the system and noted, “This project was North Carolina’s first biogas system to generate renewable energy certificates (RECs) from a swine facility.”
Methane from 80,000 gallons/day of swine manure is collected in a 2-million-gallon capacity custom, in-ground, lined and covered anaerobic digester; biogas is used to turn a 65-kW Capstone microturbine with the electricity used to power farm operations. Biogas production for electricity from the covered basin is estimated to be 50,400 ft3/day. The gas is pretreated in a conditioning skid that dehumidifies and cools the gas and filters particulates larger than 5 microns. Notably, the gas does not need to be scrubbed for hydrogen sulfide (H2S) removal because the microturbine can withstand a relatively high concentration of H2S. The system also has a backup flare that is used to burn the biogas when gas production exceeds the microturbine’s capacity. Liquids from the digester are aerated and treated for ammonia and pollutants, after which the water is used for irrigation or barn flushing.
Total turnkey cost was $1.2 million (2011 dollars) and funding was received from NC cost-share, USDA cost-share, and Duke University and Duke Energy. The university and the utility contributed $700,000 in capital and are jointly responsible for operation until 2021. Duke University provided the funding as part of a three-party cost-sharing agreement with Loyd Ray Farms and Duke Energy, with the university receiving any carbon offset credits generated by the project. For the university, the AD system represents a demonstration and research project. It also serves as an educational facility for students.
Duke Energy provided funds from its research and development pool and receives all RECS achieved by the system over the life of the project. Google got on board as an investor in September 2011. Google had committed in 2007 to become carbon neutral, which included buying carbon offsets, and this project is among those the company has invested in to procure the carbon credits.
Craig Coker is a Senior Editor at BioCycle and CEO of Coker Composting & Consulting near Roanoke, VA. He can be reached at ccoker@jgpress.com.