Two horizontal digesters and an in-vessel composting system enabled the City of Augsburg, Germany to expand processing capacity and include food waste.
Robin Szmidt
BioCycle March/April 20152
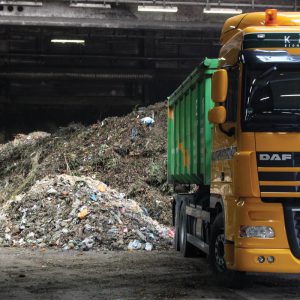
The Augsburg facility processes household biowaste, including yard trimmings commingled with food waste, along with landscape waste. Residents are allowed to use biodegradable bags and paper wraps to contain the biowaste.
Photo by Robin Szmidt
About an hour’s drive west of Munich in southern Germany, the City of Augsburg had been served by an indoor composting facility since 1994. It was operated by Abfallverwertung Augsburg (AVA), three quarters of which was initially owned by the City of Augsburg and the districts of Aichach-Friedberg and Augsburg. Until recently, the remaining quarter was owned by a private company but as of 2015, the facility is under full public ownership.
The enclosed composting operation utilized a travelling bucket-type turner (Wendelin Komposting from Bühler). However, it could only handle yard trimmings and was limited in its potential to be adapted to an input stream including food waste. Overall the facility was a substantial net energy consumer. In 2012, the AVA Supervisory Board passed a resolution to modernize the site for the future by building a new facility for both anaerobic digestion and composting. The decision was driven by the need to receive wetter materials and reduce energy consumption — or better still, produce energy.
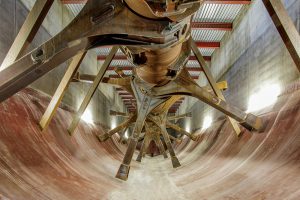
The horizontal plug flow digesters, about 115-feet in length, have a longitudinal paddle shaft that slowly rotates. Material traverses the digesters over a typical 21-day retention time.
Thöni Industriebetriebe GmbH©
Because of site limitations, the new facility had to be built within the existing footprint of the old composting site with a minimum break in service, and was expected to use as much of the existing facility as possible. All of the old technology was stripped out and the buildings remodelled to optimize process flow and meet engineering requirements of a combined AD and composting process. At the same time the new site had to allow for future expansion and increases in tonnage. The contract for redevelopment of the site and the AD and composting technologies was awarded to Thöni Industriebetriebe GmbH for the installation of a thermophilic plug flow “dry” digester and in- vessel composting (IVC) system.
Construction of the new facility started in February 2013 while the composting unit was still receiving waste. Composting operations and construction continued in parallel until May 2014 and then there was a four-month break in waste reception. Commissioning of the AD plant started at the beginning of October and by December 2014 the site was in full operation once again.
Facility Operations
The process flow is illustrated in Figure 1. Yard trimmings and comingled food waste come from the City of Augsburg and the districts of Augsburg and Aichach-Friedberg. They can be mixed with landscape waste, which is delivered by private traders and parks maintenance teams to the site. The materials are first treated in the digesters before composting and therefore undergo a two-step hygienization process — first in the thermophilic AD and second in the enclosed composting operation. The site is licensed to take up to 61,000 tons/year. The facility uses a double Thöni TTV horizontal plug flow digester configuration in which two digesters are structurally linked but are operated totally independently. Each unit has an active volume capacity of 1,650 cubic meters (58,000 cubic feet). The process operates in the thermophilic range, maximizing process rate, hygiene and biogas yield.
Incoming biowaste is shredded, followed by separation into fine and coarse fractions using a linked star screen. The coarse fraction (> 80 mm; about 3 inches) mainly consists of plastic films, which although discouraged, are still a significant issue. This fraction is delivered to the neighboring waste incineration plant for combustion. In turn, the incinerator provides heat for the AD and composting site. The incinerator receives garbage and material otherwise unsuitable for reprocessing or recycling.
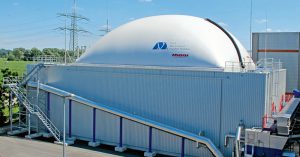
All of the biogas generated is first collected in a gas storage unit located on the load-bearing roof of the digesters.Photo courtesy Thöni Industriebetriebe GmbH©
The fine fraction (< 80 mm) is passed through a magnetic separator and conveyed to fully automated Thöni storage/feeders (3 x 200 cubic meters). Packaged food waste is not accepted at the plant so there is no need for a separate depackaging line. Overall, the pretreatment equipment is kept deliberately simple to maximize throughput and minimize stoppage time.
The computer control system links to a series of load cells and level sensors to monitor the availability of input material in the feed train so that the AD system can be continuously charged 24/7 every day of the year. The feeders dose the digestible material into a premixer where it is blended with press water produced by the Thöni screw presses at the discharge end of the digesters. This high-solids viscous mix with a dry solids content of about 39 percent is then force-fed into the digester using hydraulic pumps. Each has a longitudinal paddle shaft that slowly rotates. This ensures the digestion process is gentle without end-to-end mixing so that the biochemical digestion steps can take place sequentially as the mass moves slowly from the input to the outlet end.
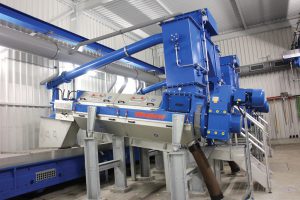
Material is discharged from the digesters and separated into a liquid and a solid fraction by screw presses (two per digester). A portion of the liquid fraction is recirculated as inoculum to the input end of the digesters.
Photo by Robin Szmidt
The digesters, which are located outside, are large static vessels, approximately 115 feet in length that sit on a steel base within an insulated concrete cradle. The entire digester is then insulated and clad to match local buildings as required by planners. This design allows heat distribution and monitoring systems to be installed in the cradle zone below the digester body, guaranteeing a frost-free area without the need of a separate building. The internal area of the digester incorporates floor- and cross-heating zones linked to the computer-controlled heating system. This maintains the thermophilic process at around 54 °C (129.2°F), accelerating bioconversion on the one hand while hygienically treating the biological waste within the digesters on the other.
Material that has traversed the digester over a typical 21-day retention time is then discharged and separated into a liquid and a solid fraction by screw presses (two per digester). This is a one-step process that quickly establishes aerobic conditions for solids ready for composting. A portion of the liquid fraction is recirculated as inoculum to the input end of the digesters while the remainder is directed to intermediate storage tanks before use as agricultural high-quality liquid fertilizer.
The solid digestate fraction after pressing is transported using an automated auger system and top-loaded into closed Thöni intensive composting modules with positive floor ventilation. This ensures a rapid switchover to a 7-day aerobic post-digestion composting phase. The nearly finished compost is then moved by loader to in-building aerated bunkers for an additional 7 days. Material is then screened using a 12 mm (half-inch) trommel, one of the few remaining pieces of equipment from the old facility. The finished compost is sold for agriculture and gardening and landscaping applications, meeting the general European Union standards and the higher German “Rottegrad” standard with the highest grade, level 5, routinely achieved.
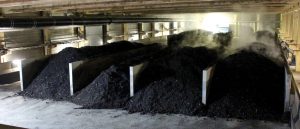
The solid digestate fraction first goes to a 7-day post-digestion composting phase, and then is moved to in-building aerated bunkers (above) for an additional 7 days of curing.
Photo by Robin Szmidt
Biogas Utilization
All of the biogas generated in the digesters is first collected in a gas storage unit located on the load-bearing roof of the digesters. Since being commissioned in the fall of 2013, biogas produced by the AD facility has been upgraded to natural gas standard using a Pentair membrane plant. This is a key component regarding site environmental impact and was specified with a zero tolerance of methane emissions/maximum methane recovery. The gas upgrader is also operated by AVA, and feeds into the gas network of Stadtwerke Augsburg, the public utility company.
Almost as soon as the AD facility came on line, available input material began to increase and the design capacity was very quickly reached. The Augsburg team believes that this is due to the high profile of the new facility together with the introduction of “bioenergy waste bins” in the district of Augsburg, which had a much greater impact on quantity of waste than was forecast. The bioenergy bins —240 liter (63 gallon) wheeled carts — were distributed to households. A marketing and information campaign was conducted that included leaflets and local advertising, etc. This included instructions about what materials are, and are not, accepted in the program. Householders can wrap food waste but not use plastic bags. Paper wraps and biodegradable bags are accepted.
The bins, serviced weekly or biweekly depending on time of year, had not previously been available to all households and a considerable proportion of biodegradable waste had simply been in the general residual waste stream. Aichach-Friedberg will also introduce the new bins during 2015. In 2014, only one year after commissioning, AVA decided to build a third digester, increasing throughput of the AD plant to about 74,000 tons/year. This additional unit will come on line as soon as possible in 2015.
Overall, the new facility at Augsburg is a real example of integration of waste, resources, energy and products. For example, the heat requirement of the thermophilic digesters is met by using reject heat from the neighboring waste incineration plant. Conversely the AD and composting site also enables emissions of greenhouse gases (GHG) to be significantly reduced by separately collecting specific exhaust airflows in the facility for direction either to the incinerator as combustion air, particularly “dirty” air potentially contaminated with trace ammonia or methane, or to the biofilter. GHG emissions are also minimized by retrieving and liquefying the separated carbon dioxide stream.
The integrated exhaust air system of the AD and composting facility is a hugely important element of this overall concept. By managing and linking the entire exhaust air system with that of the incinerator, the volume of exhaust air has been significantly reduced, thereby halving the area of the existing biofilter and reducing electricity usage accordingly. The incinerator itself generates both electricity, which is directed to the grid, and heat for distribution via a local area network, including the AD facility. Overall, the AD and composting project has improved the throughput of the site, improved product quality and generated energy while at the same time reducing the footprint per ton and the carbon footprint of the whole operation.
Robin Szmidt is founder and director of Target Renewables Ltd., a unique UK-based consultancy for the anaerobic digestion sector, specializing in integration to the compost sector. He has worked on a number of international projects with major European AD suppliers and comes from a product use background in agriculture and horticulture with a PhD in compost microbiology.