BioCycle September 2014
Tulare, California: Celebrating 25 Years Of Renewable Energy Generation
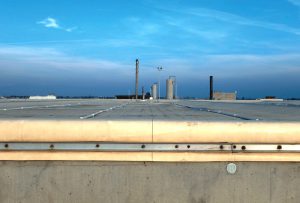
Geomembrane Technologies Inc. (GTI) installed a floating gas collection cover over the complete 4-acre surface of the Tulare, California’s digester.
The City of Tulare, located in California’s San Joaquin Valley, is home to six large-scale cheese and dairy producers. These facilities — including Nestlé Dreyer’s, Saputo Cheese, Kraft USA, and Land O’Lakes — produce large volumes of high-strength industrial wastewater, which is sent to the Tulare Waste Pollution Control Facilities for treatment. Like many municipalities, the city was challenged to meet industrial requirements at a reasonable cost while maintaining harmonious relationships with the surrounding community. Twenty-five years ago, in 1989, it selected an ADI-BVF® anaerobic digester as an efficient means of treating the wastewater to meet state regulations. To reliably collect biogas from the BVF reactor to generate electricity while also controlling odors and reducing greenhouse gas emissions, Geomembrane Technologies Inc. (GTI) installed a floating gas collection cover over the complete 4-acre surface of the city’s digester. The cover contains all the biogas generated by the reactor, thereby eliminating odors. It also is chemical- and UV-resistant to withstand the harsh environment of the digester and the California sun. Personnel are able to walk across the cover for routine operations and maintenance.
Up to 600,000 ft3 of biogas per day from the digester are collected at the wastewater treatment plant — enough biogas to generate a portion of the facility’s required power. The City of Tulare was recently recognized by receiving the Green California Leadership Award for its energy efficiency strategy, which includes the waste-to-energy initiative designed to reduce overall greenhouse gases generated in the community.
Monticello, Indiana: Mixed Organics Digester
Waste No Energy, LLC, owned by RAKR Farms in Monticello, has developed a multimillion anaerobic digestion facility that is producing 8.2 million kilowatts annually of green energy. Power is purchased by Northern Indiana Public Service Co. (NIPSCO) under a 15-year contract. The digester also produces 14 million gallons/year of fertilizer that is used by RAKR on its 5,000-acre farmstead, according to Waste No Energy President Doug Raderstorf. RAKR Farms operations include hog and cattle facilities, as well as a grain dryer. The digester, which went on line last December, processes 100 to 125 tons/day of organics, including material from grocery stores, bakeries, food processors, cheese makers, brewers and restaurants, biofuel production by-products (ethanol syrup and glycerin bottoms) and 26 tons/day of swine and cattle manure. All of the organic waste inputs are lab-tested prior to acceptance, and contracts go to prequalified suppliers. The digester plant, designed and engineered by U.S. Biogas, LLC, can produce 408,174 cubic feet/day of methane; its thermal heat output is 4.2 Mmbtu per hour.
Manure and other organics are loaded in a 1.3 million gallon digester tank, with a hydraulic retention time of 25 to 30 days, according to Duane Toenges, CEO of U.S. Biogas. The system also includes two substrate tanks holding a total of 51,240 gallons and a 20,000-gallon manure tank. “So far, the project has been very successful,” says Raderstorf. “We’ve had to deal with some surprises, but that’s all part of starting a new business in a new industry. We’ve now got all of the nuances of the operation ‘down’ the way we want them.” He adds that the biggest challenge in getting the project off the ground has been explaining the anaerobic digester concept to bankers, insurance agents, regulatory agencies and the public. “This technology has been proven over decades, so it’s just a matter of getting all the key players to understand the industry.” Because the plant is one of only two digesters in Indiana not located on confined animal feeding operations, the state had to draft and approve new regulations to cover the Waste No Energy facility, which also added time to the development process.
Pixley, California: Digester Installation At Ethanol Plant
Four years after proposing to install an anaerobic digester to replace use of natural gas in its ethanol production, Calgren Renewable Fuels of Pixley is close to seeing its plan come to fruition. The company’s 55 million-gallon-a-year ethanol plant has had to rely on piped-in natural gas to run a turbine generator capable of producing 5,800 kW of electricity necessary to make process heat and steam. With state environmental documents finally approved in late February, the company moved forward with construction of a DVO, Inc. Two-Stage Mixed Plug Flow™ anaerobic digester supplied by Andgar Corporation. Manure from the nearby Four J Dairy will be piped in. The facility is expected to start up this fall. “The project could replace up to 7,000 MBTU of natural gas a month once it’s operating,” says Lyle Schlyer, Calgren’s president. After digestion, material will be pumped into a mechanical manure separator; digested effluent will be sent back through the pipeline to Four J Farms for application to cropland.
Calgren received a $4.68 million matching grant from the California Energy Commission in May 2010 for the $10 million-plus facility. However, at the request of neighbors of the ethanol plant, Tulare County (where the ethanol plant is located) initiated CEQA (California Environmental Quality Act) proceedings to evaluate potential environmental impacts. In the end, notes Schlyer, the environmental review showed very little odor or greenhouse gas emissions from the project and construction was able to get underway.