Dry anaerobic digestion facility in Luxembourg successfully treats mixed yard and food waste collected in compostable plastic bags.
Christian Garaffa and Klaus Gröll
BioCycle October 2013, Vol. 54, No. 10, p. 40
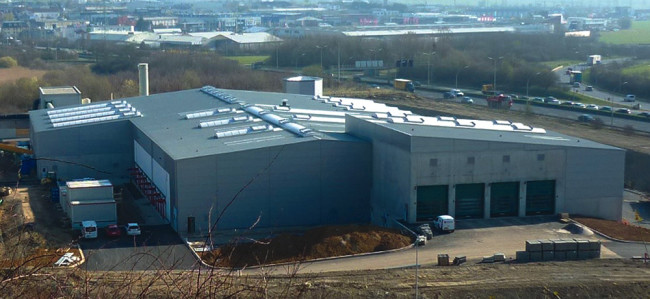
Preprocessing, anaerobic digestion and composting operations are enclosed at the Syndicat Minett-Kompost facility.
Dry technologies started gaining a significant market share in Europe in the 1990s with plug flow systems that operate with “shovelable” or solid substrates with total solids (TS) content ranging between 20 and 40 percent. Dry fermenters are less sensitive to sedimentation issues and handle substrates with larger particle size compared to wet AD systems (between 1.5 and 3-inches). They can treat garden waste or mixtures of garden and food waste. The different structure and higher TS content of the feedstocks require a different approach to pretreatment — typically particle size reduction and screening — compared to wet systems. It has a high viscosity and moves via plug flow inside the digester. With input substrates having TS greater than 60 percent, part of the liquid digestate or process water is recirculated and added to the incoming material to reduce the TS to bewteen 20 and 40 percent. Dry plug flow technologies include Kompogas, Dranco (OWS), Valorga and Strabag (formerly Linde).
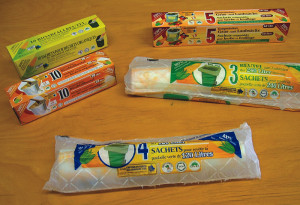
The waste authority introduced compostable bags made from Mater-Bi resin for residential food waste collection to help maintain a high participation rate.
Minett-Kompost
The dry plug flow AD and composting facility in Mondercange, Luxembourg is managed by Syndicat Minett-Kompost, the public authority responsible for waste management in the 21 municipalities in the southern part of Luxembourg (185,000 residents). In 2011, Minett-Kompost added an AD plant to its existing 20,000 tons/year (tpy) composting facility in Mondercange. The AD technology was supplied by Strabag Umweltanlagen GmbH. The new plant, which treats mixed green and food waste, has a capacity of 30,000 tpy, including the pretreatment and post composting stages. The green waste stream for AD includes grass clippings, weeds, etc. Other yard waste — primarily tree and shrub cuttings with a high proportion of wood — goes directly to the composting operation. Capacity of the digester is 25,000 tpy. In the winter months, when municipal green waste production is low, up to 4,000 tpy of energy crops (silage) can also be used.
The Syndicat Minett-Kompost also manages collection of biowaste in the 21 municipalities. In 1999, the authority introduced specifically labeled compostable bags made of Mater-Bi resin for residential food waste collection to keep a high participation rate in the scheme and a good quality of the material collected. Food waste bags and liners of different capacity (from 2.5 to 64 gallons), along with 15-gallon yard waste bags, are distributed in different local supermarkets. Certified compostable food service ware items, listed on the waste authority’s website, are accepted in the collection container (Bio-bin). In addition, the Syndicat Minett-Kompost organizes an annual event using compostable food service ware and promoting use of compostable plastic bags.
Materials Processing
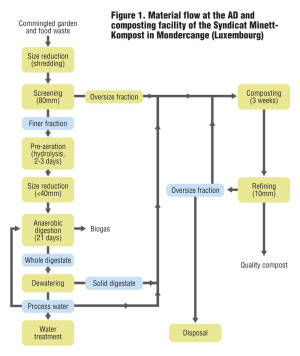
Figure 1. Material flow at the AD and composting facility of the Syndicat Minett-Kompost in Mondercange (Luxembourg)
The finer fraction goes through a hydrolysis stage under aerobic conditions for 2 to 3 days at temperatures ranging from 95°F to 115°F. The aeration buffers and homogenizes the substrate thus avoiding build-up of lower molecular weight organic acids that can inhibit start-up of the fermentation process. It also promotes breakdown of the lignocellulosic fraction, making it more readily available for microorganisms in the subsequent fermentation phase. In addition, the fragments of compostable plastic bags start breaking down during this phase.
After hydrolysis, a second size reduction to less than 1.5-inches takes place and then the prepared substrate is fed into the digester by a screw conveyor. Fermentation occurs at 106°F (mesophilic) at 25 percent TS content with an average hydraulic retention time of 21 days. The horizontal plug flow digester is equipped with seven transverse agitators preventing formation of a floating layer or sediments on the bottom (Figure 2). The agitators also facilitate release of the biogas.
Digestate is discharged from the reactor by an extraction system and dewatered to 40 percent TS content by a screw press. The pressed liquid still has around 15 to 20 percent TS content. It is sent to a decanting unit to lower the level to under 8 percent TS. After decanting, it is stored and used either for recirculation in the digester or for moisture control in the composting process. The excess liquid is sent to a wastewater treatment system.
Pressed digestate is mixed with the oversize fraction (> 3 inches) from the pretreatment stage and moved with front end loaders to tunnel composting for three weeks with one turning cycle for quality compost production. The stabilized compost is screened for refining and stored for curing. During this aerobic phase, breakdown of any possible remains of compostable plastic bags is completed.
Christian Garaffa is Marketing Manager, Source Separation and Recycling, for Novamont S.p.A. Klaus Gröll is Managing Director of IGLux s.à r.l., an independent consultancy, engineering and research company in Europe specializing in sustainable waste management, including anaerobic digestion as well as composting of biowaste (k.groell@iglux.lu).