Top: About half of the loads of food scraps coming to the Shakopee Mdewakanton Sioux Community (SMSC) Organics Recycling Facility from residential, commercial and institutional generators arrives in certified compostable bags, and about half is loose.
Nora Goldstein
The Shakopee Mdewakanton Sioux Community (SMSC) opened its Organics Recycling Facility (ORF) in Prior Lake, Minnesota, in 2011, accepting source separated organics (SSO) — including food scraps, certified compostable products, food processing residuals, yard trimmings, wood and horse manure — from the Tribal community and surrounding jurisdictions. SMSC had previously operated a smaller yard trimmings composting site for its own materials.
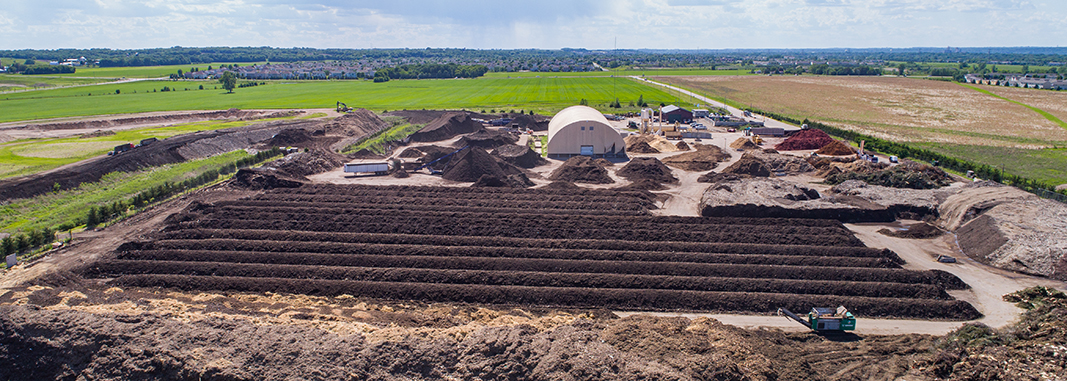
The windrow composting facility opened in 2011. Plans are underway to transition to an aerated static pile composting system at a new location.
Initially, the ORF was mainly taking in preconsumer material from grocery stores and food manufacturers. Then it began receiving postconsumer food scraps from many sources, including the nearby Mystic Lake Casino Hotel and Little Six Casino (both owned and operated by the SMSC), as well as from several school districts, restaurants and businesses. That is when the facility began receiving compostable foodservice ware products.
Due to its close proximity to the Twin Cities, the SMSC also anticipated it would be receiving food scraps from haulers servicing the metro area. “We currently take in about 12,000 tons/year of food scraps and compostable products,” notes Erin Skelly, the ORF’s Environmental & Compliance Tech. “Only about 10% to 20% of that comes from the SMSC’s gaming enterprises and convention center. The rest comes from the greater Twin Cities region. We also have a contract with Hennepin County to compost back-of-house SSO from its commercial food scraps collection program.”
Once it began taking in postconsumer material, contamination went up significantly. “The most contaminated postconsumer material we’ve been seeing comes from school lunchrooms,” adds Skelly. The haulers that bring material to the ORF are responsible for training generators about source separation practices, signage and other outreach and education initiatives. “In the future, we would like to collect the SSO ourselves, which would provide the ability for us to get cleaner materials,” she says.
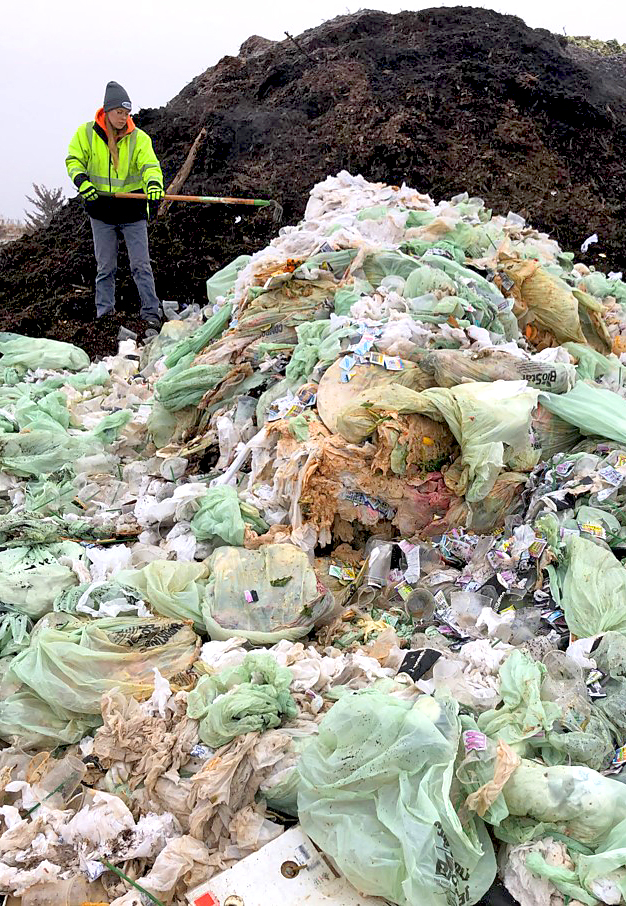
Load inspectors tear open compostable bags containing food scraps to assess the level of contamination.
Load Inspections
Before taking on a new hauler, a meeting is required to review inspection and acceptance procedures; haulers also are given a tour of the composting facility. Incoming loads of commercial, institutional and residential food scraps (the ORF gets residential curbside from one city) are inspected for contamination. Roughly half of food scraps from these generators arrives in compostable bags, and the other half is loose. After a truck tips a load, a front-end loader bucket spreads out the material into a flat layer to facilitate the inspection. The SMSC sets a 5% contamination threshold (by volume) on tipped loads. “The inspection takes about 15 to 20 minutes,” says Skelly. “We tear the compostable bags with a hook so we can quickly inspect what is inside. If the load is over 5% contamination, it is rejected and the SMSC charges $250 to reload the truck, which then goes to the landfill that is about 15 minutes away. With contaminated packer truck loads, the hauler has to arrange for a roll-off truck to come to pick up the rejected load. Estimating the percent of contamination is part art and part science. We are trained in what 5% looks like, and there is not a lot of in between — it’s either 5% or less, or significantly over.”
All feedback to generators is provided via the haulers. Load feedback includes descriptions of the contamination and photos. The SMSC has an online account for each hauler bringing material to the ORF. Load inspection photos and sources of the loads are kept on file in the account. “This provides a record of progress and helps identify recurring issues,” she explains. “We also give positive feedback, e.g., send a photo of a clean load.”
Skelly estimates she spends about 10 hours/week on load inspections and contamination follow-up. Products that are similar in appearance to certified compostable products (i.e., lookalikes) are “a huge problem,” she adds. “We’ve heard from some haulers that their food service customers don’t want the hassle of separating the food scraps from the foodservice ware and packaging, so they opt to switch to using compostable products. This can lead to confusion and the inclusion of the lookalikes.”
Shredding And Composting
About 70,000 tons/year of material are composted at the ORF. All incoming food scraps and yard trimmings are processed in a Komptech Crambo 5000 with 8-inch and 12-inch screens, and a magnet. The shredder essentially rips open any compostable bags. The size-reduced contents are mixed using a bucket loader with ground yard trimmings and wood, and put into windrows that are 10-feet tall and 20-feet wide. The piles are turned with a Komptech X67 once a week during the active phase of composting, which is about 70 days. Turning frequency and/or composting time may increase if the operators notice slower disintegration of compostable products in the windrows. Moisture is added to windrows periodically via a drip line that lies on top of the row and slowly infiltrates over the course of 24 hours.
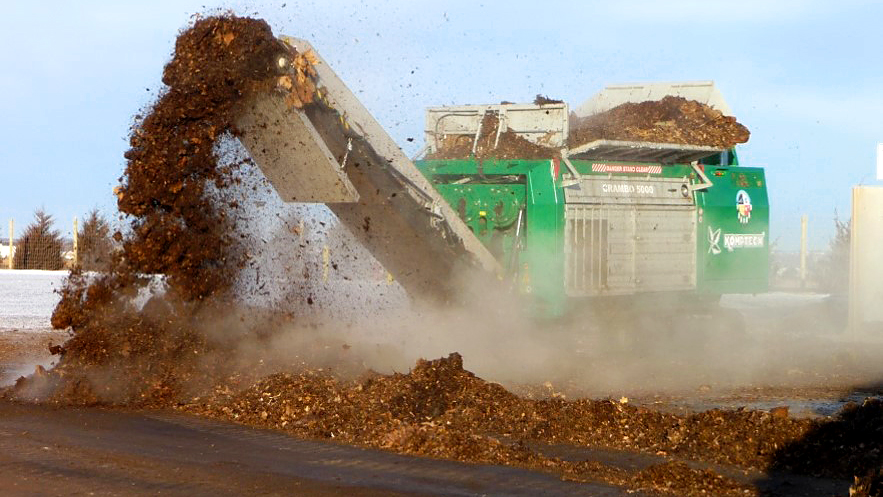
All incoming food scraps and yard trimmings are processed in a Komptech Crambo 5000 with 8-inch and 12-inch screens, and a magnet. Photos courtesy of the SMSC Organics Recycling Facility.
Compost is screened in between the active and curing phases using a Komptech L3 star screen. Availability of the screener is a factor in determining the length of active composting. “It’s more of a materials handling issue than extending the duration of the active composting phase to, for example, aid in disintegration of the compostable products,” explains Dustin Montey, Assistant Biomass Processing Manager at the SMSC. “The fine fraction goes to curing and a portion of the mid-size fraction and overs is recycled back into the active phase. The star screen is equipped with a windsifter, and a large portion of the lighter film plastic contamination is removed before curing. Some of the compostable fraction also gets removed if it hasn’t disintegrated in the active phase.”
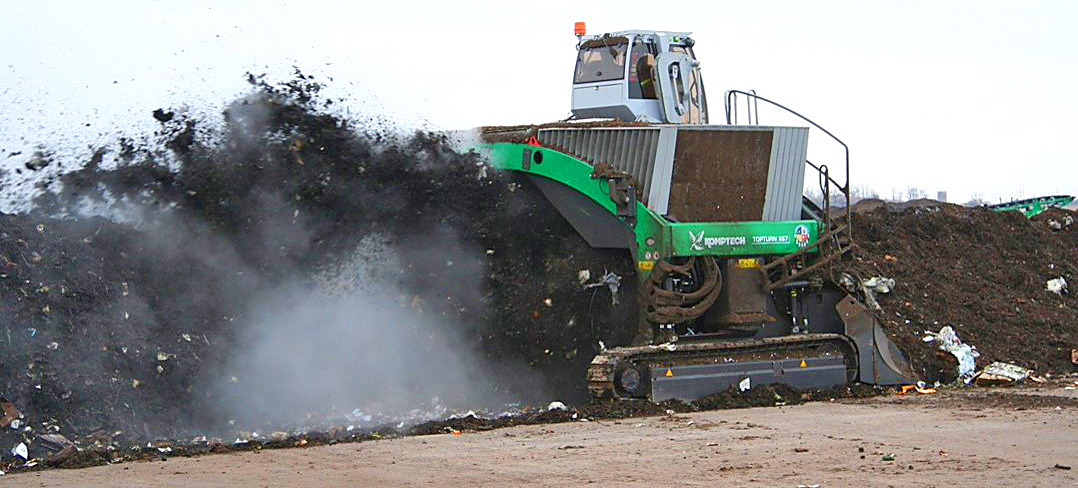
Windrows are turned once a week during active composting. Moisture is added via drip lines when needed.
As the windrows are turned, some of the compostable products end up on the edge of the windrows. To mitigate litter and get the compostable products back into the interior of the windrow, a Bobcat is used to scoop them up after turning and put them at the end of the windrow where they will get turned back into the pile during the once-a-week turning.
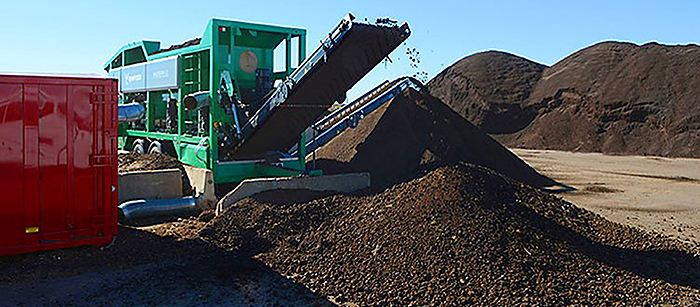
Compost containing food scraps and compostable products is screened in between the active and curing phases using a Komptech L3 star screen equipped with a windsifter.
Compost is cured for about 60 days. Montey notes that the star screen paired with the windsifter is necessary to use with compost manufactured from postconsumer food scraps to optimize removal of plastics. “We get much higher production screening with our trommel, but that is used only for the yard trimmings compost we make. It also costs about 50% less to use the trommel than the star screen with the sifter.” The yard trimmings compost is approved for use in organic agriculture and cannot contain compostable products.
Generally, the SMSC has found that certified compostable bags break down during the active phase of composting; compostable plastic cups usually disintegrate after the active and curing phases. When the finished compost is screened, operators note that compostable utensils and molded fiber are often in the overs fraction that gets landfilled. “We take in a lot of molded fiber, e.g., bowls and trays,” explains Montey. “These typically get stacked by the generator to save room in the dumpster. In turn, the big stacks get stuck together, especially if they are wet and end up forming a big, pulped mass that makes it difficult to fully disintegrate.”
Generally speaking, Skelly and Montey believe that consumer confusion about what is certified compostable and what is a lookalike product result in increased contamination in the postconsumer food scraps loads. They are supportive of compostable product labeling legislation that would help mitigate the confusion. Ultimately, however, allowing compostable products in the postconsumer stream increases the amount of food scraps being diverted to the SMSC. “If we say no, a lot of generators will refuse to participate,” they note. “If we want to increase composting, which we all do, it is a necessary burden.”
Optimizing contaminant removal is critical to the SMSC’s ORF’s bottom line. “We make more money on the compost sales than the tipping fees,” says Skelly, “which is the opposite of how it was in the early days of the ORF,” says Skelly. “Currently, 30% to 40% of our revenue comes from tip fees, and 60% to 70% comes from compost, compost blend and mulch sales.”
Facility Expansion, Switch To Aeration
With their current facility nearing maximum capacity, plus a desire to upgrade its composting process, the SMSC is relocating and expanding its operation elsewhere and will be installing an aerated static pile (ASP) system supplied by Engineered Compost Systems (ECS). The new facility is in the permitting phase with the Minnesota Pollution Control Agency as it is not located on tribal land and falls under the purview of state regulations. “In Phase 1, the SMSC is seeking a permit for 115,000 tons/year of commingled feedstocks,” explains Craig Coker of Coker Composting and Consulting, who is serving as the project manager for the new installation. “In Phase 2, that will increase to 172,500 tons/year. The new process design is for 28 days of active aeration and 30 days of curing (45 in winter). The switch to ASP will make the process easier to manage and control, and reduce the potential for odors.”
Phase I will utilize 16 ECS ASP reinforced concrete wall bunkers (2 fan groups of 8 each) with aeration trenches in the floors. Coker expects that the new composting system will aid in the disintegration of compostable products with the ability to optimize for temperature, airflow and moisture.