Norma McDonald
Use of biopolymers for food packaging and serviceware is increasing rapidly, expanding the amount of organic waste collected, recovered and recycled and thus reducing landfill emissions. With growing public outcry and government regulations to increase organics recovery and reduce plastic waste, biodegradable plastics are not just a temporary trend — they will be a bigger part of the future and included in the definition of organic waste (e.g. California’s SB1383).
In order to meet jurisdictional requirements that single use plastics be biologically recyclable, two challenges must be met. First, the terminology and identification of biopolymers suitable for biological recycling must be created and communicated effectively. Second, biological recycling infrastructure must be built, adapted and expanded to recover and recycle the biopolymers.
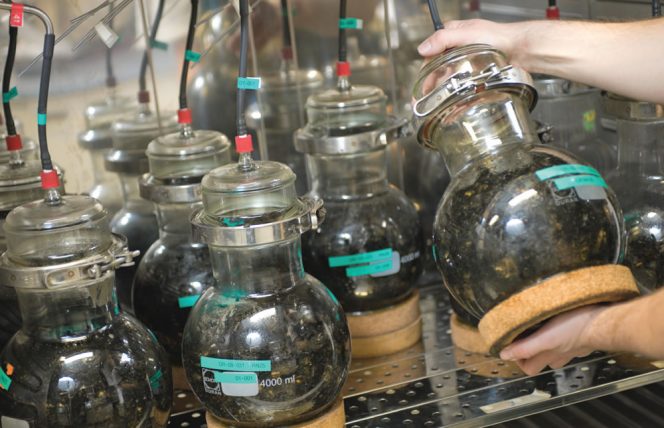
Test for biodegradation of biodegradable polymer molecules being conducted at the OWS, Inc. laboratory. Photo courtesy of OWS, Inc.
Biological recycling of biopolymers — just like food waste — is the recycling of organics using living organisms found in one or more processes, and ultimately in the soil or water. In aerobic composting (AC), the fungi and aerobic bacteria consume the biopolymers for energy, and the by-products are heat, carbon dioxide, and water vapor. In addition, due to the biological process, a portion of the biopolymer’s organic carbon is converted into biomass as humus, part of the compost.
Certification Based On Composting
For the past 25 years in North America, the predominant approach to industrial organic waste processing has been AC. Biopolymers were thus evaluated and certified for “compostability” using consensus-based industry standards (ASTM) for laboratory test methods and pass/fail criteria. The four requirements of compostability are:
- Disintegration: This is the physical fragmentation of the product. Pretreatment processes may accelerate this by shredding or grinding the waste, which also increases surface area and allows for an even distribution of the biopolymer products in the compost pile. The combination of moisture, temperature, mechanical action and microbial activity — during both the active phase and stabilization/maturation phase — continues the disintegration process. The ultimate goal is that the final compost contains no visible fragments of the biopolymer product; the standard also requires that <10 percent of the product’s mass may remain on a 2mm sieve after 12 weeks of AC. Since thickness plays a key role, some products disintegrate far more rapidly than others (analogous to a toothpick and a 2 x 4).
- Biodegradability: Not only must the biopolymer product fully disintegrate, the biopolymer molecules must also truly biodegrade and not accumulate in the environment. For industrial AC, >90 percent of the organic carbon must convert to carbon dioxide within 180 days. This is considered complete biodegradation since the remainder of the carbon has been converted into biomass by the microbes. Some biopolymers completely biodegrade in industrial AC conditions in as little as 28 days. In comparison, Table 1 illustrates the number of days it took various natural materials to reach varying levels of biodegradation.
- Heavy metals and fluorine: In addition to being degradable, the product may not introduce levels of 11 heavy metals or fluorine that exceed regulatory limits.
- Plant toxicity: Finally, the final compost may not contain residuals/byproducts that have harmful effects. The testing standards require the full 12 weeks of AC in order to ensure stable, mature compost is obtained prior to beginning the plant trials. Shorter timeframes have shown negative impacts on both emergence and growth due to immaturity of the compost, so even if the test sample has fully disintegrated much sooner, the AC period is not allowed to be truncated.
The four basic requirements for determining compostability are also relevant to other biological recycling processes (e.g., anaerobic digestion) in order to prevent harm to the environment, but timeframes and specific test methods for degradation will vary. For example, the OK Biodegradable certifications for SOIL, WATER, and MARINE all have pass/fail criteria for the same four parameters with the exception that for SOIL, the disintegration timeframe is not specified.
So far, a minority of existing U.S. industrial-scale yard trimmings composters have adapted their pretreatment, active composting and post-processing to accept food waste and compostable products in order to produce a marketable product. The majority of facilities are reluctant to take on the additional required capital investment, or to risk producing less marketable compost due to either increased contamination or the loss of certification for organic farming.
An additional factor to consider is the operational approach used by the AC facility. Some AC facilities are now operating at very high temperatures (>70°C) and short active phase retention times (4 weeks or less), and little or no stabilization or maturation period. This approach biologically dries and partially degrades organics, but does not produce a true, stable compost since biological activity and odor generation reactivates once the material is rewetted. Along with many natural products, few biopolymer products will sufficiently physically or biologically degrade in these AC facilities.
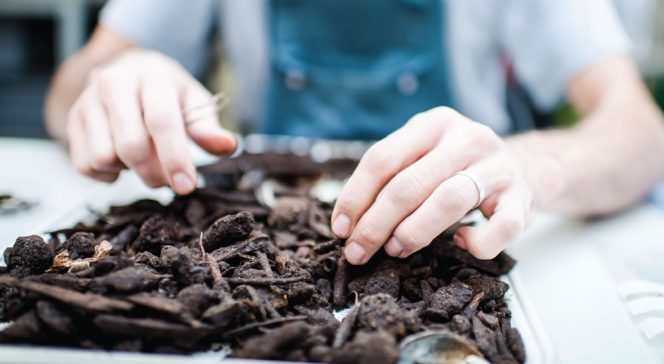
Picking through fraction that remains on sieve following disintegration test to measure mass of product that did not disintegrate. Photo courtesy of OWS, Inc.
Cascaded Combination — AD+AC
A second approach to biological recycling of household organic waste is the “cascaded” combination of anaerobic digestion (AD) with existing or new AC facilities. The AD+AC combination increases percent recovery and recycling of the organics and biopolymers in household organic waste by providing both renewable energy and quality compost. The AD+AC combination thereby increases landfill diversion and reduces associated fugitive GHG emissions. A decision tree (Figure 1) illustrates the behavior of a certified compostable product containing biopolymers in AD systems.
In AD, only anaerobic bacteria are present, which similarly consume (most) biopolymers for energy and the by-product is biogas. Biopolymers that do not fully disintegrate or biodegrade in AD are then consumed during the subsequent AC process required to convert the solid digestate to finished compost.
There are not yet, however, similarly well-recognized industry standards with pass/fail criteria for determining degradability of biopolymers in AD. The most relevant ASTM test method for wet AD is ASTM D5210, “Standard Test Method for Determining the Anaerobic Biodegradation of Plastic Materials in the Presence of Municipal Sewage Sludge”. For higher solids AD, the most frequently used test is ASTM D5511 “Standard Test Method for Determining Anaerobic Biodegradation of Plastic Materials Under High Solids Anaerobic Conditions”. In addition, disintegration in AD can be measured using ISO 15985 “Plastics – Determination of the ultimate anaerobic biodegradation and disintegration under high-solids anaerobic digestion conditions”.
Proposed standards and test methods were recently developed for the AD+AC process as part of the European Open-BIO Work Package 6 measuring the degradation that takes place in the sequential processes. Decades of testing hundreds of biopolymers provides some general guidelines for the degradability of different families of polymers in different biologically active environments and therefore how biopolymers may degrade as they go through each process. One could envisage biopolymer products initially undergoing 25 to 35 days retention time in the AD, and then the solid digestate undergoes an additional 14 to 40 days of AC. Polylactic acid (PLA), for instance, is degradable in thermophilic AD, so at least partial degradation will occur during AD; the high temperature of the subsequent AC phase will complete the degradation process. If PLA is introduced into mesophilic AD, little if any degradation will occur during AD and will be entirely dependent upon the AC phase.
Thermoplastic starch (TP) and polyhydroxyalkanoates (PHA), on the other hand, are readily degradable in both mesophilic and thermophilic AD and may be completely degraded before the AC phase. Some biopolymers, such as polybutylene adipate terephthalate (PBAT), and some natural materials, such as mechanical pulp (natural fibers which have only undergone mechanical pulping and no chemical treatment), require aerobic microorganisms to be degraded and will thus be fully present in the digestate in the AC phase.
Figure 2 illustrates the difference in biodegradability of biopolymers in each environment. The left column is distinguished by conditions where no fungi are present, only bacteria. Chemical pulp (natural fibers that are chemically processed) will biodegrade without fungi present. An aerobic aqueous (water) environment may be the primary phase at a wastewater treatment plant, which may be operated at either high or low temperatures. An anaerobic environment can also be aqueous, as in the secondary or tertiary treatment phase at a wastewater treatment plant or other AD, or a non-aqueous anaerobic environment such as a landfill. The right hand column includes industrial and home composting conditions where not only bacteria are active, but also fungi that are necessary for the biodegradation of mechanical pulp.
Compatibility With AD Processes
In addition to the biological considerations, products which are certified compostable may or may not be compatible with a given AD process primarily due to the significant difference in mechanical process limitations between wet AD and high-solids AD. The need for some pre and postprocessing is required for all AD facilities accepting household organic waste, so the adaptation needed for increased biopolymers in the substrate mix is driven by mechanical limitations of the AD system. Such limitations include susceptibility to formation of a floating layer, entanglement with the mixing equipment, and blockage or sedimentation within the recirculation system. AD systems that cannot readily process green waste, paper or tolerate some amount of plastic contamination are likely to also experience issues inside the digester with biopolymer products. For these facilities, biopolymers and other incompatible natural materials must be presorted and moved directly to AC.
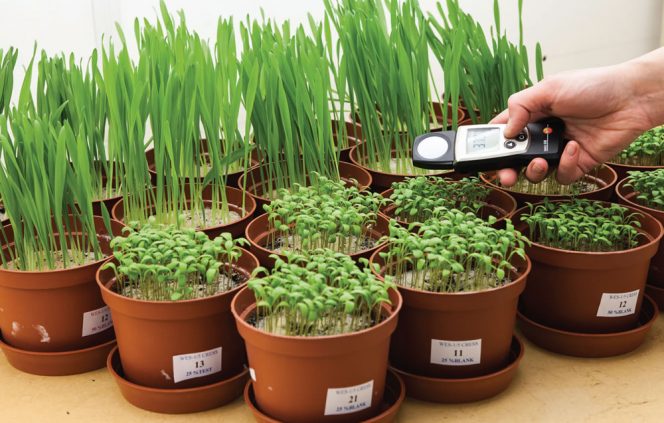
The testing standards require the full 12 weeks of aerobic composting to ensure stable, mature compost is obtained prior to beginning the plant trials. Photo courtesy of OWS, Inc.
For the treatment of household waste organics, dry AD technologies currently represent >75 percent of all installed capacity due to their ability to treat a broader array of materials and tolerate some amount of contamination. For these facilities, the digestate may be dewatered and the solids moved to AC, or if the digestate contains no free liquid, dewatering can be avoided and the digestate may be directly blended with green waste in the AC.
Undegraded biopolymer products and other organic overs are typically screened during the AC process and from the final compost and recycled within the process to allow additional time for degradation to complete. If the overs contain excessive inorganic contamination (nondegradable plastics), the overs may be better suited for isolated stream processing rather than being reintroduced with fresh organics. The specific process used for the isolated stream will depend upon the composition of the overs, but may include isolated additional composting to complete degradation of the biopolymers and other natural materials leaving only nondegradable materials. This remaining, predominantly plastic fraction should then be evaluated for thermal processing where available. At a minimum, the isolated stream processing reduces tonnage sent to landfill.
Terminology Challenge
Development and adoption of terminology for biological recycling of biopolymer products remains challenging for a number of reasons. First, the Federal Trade Commission (FTC) guides for the use of environmental marketing claims (Part 260 and subchapter B of Chapter 1 of Title 16 of the Code of Federal Regulations) restrict the use of claims for biodegradability, compostability and degradability, seeking to ensure that claims are accurate and do not mislead or confuse the public. The ability to make claims is predicated on the availability of infrastructure to properly process the product. This presents a “what comes first” dilemma: a preponderance of biopolymer products suitable for biological recycling, or, biological recycling facilities. Second, the technical terminology and process variations may not translate easily to the public, or fit on package labeling. The FTC requires clear labeling that is not misleading — but does not dictate the level of specificity regarding the process. Third, even when products comply with the standards for compostability and bear a certification logo, they may not be accepted locally due to the specific policies of the processing facility.
These challenges will have to be confronted in light of the growing mandates in coastal communities for products that are frequently littered/blown into the fresh or marine waters to be degradable in those environments as well. Biopolymer products must be re-evaluated in each of these other environments, and an appropriate labeling and identification system must be developed to encompass other biological environments that make it clear that littering is never acceptable, but also to reassure consumers they are using a product that will not accumulate and cause harm to the environment. The constituencies/stakeholders include, but also go well beyond composters. In communities served by composting facilities that do not wish to accept biopolymers, municipalities will have to work with other biological recycling facilities to achieve their goals for landfill diversion of all organics and preventing plastic pollution.
Norma McDonald is North American Sales Manager with Organic Waste Systems (OWS).