Top: The footprint of the Dirt Hugger composting facility in Dallesport (WA) illustrates space allocation for all steps of the process. Photo courtesy of Dirt Hugger
Craig Coker
Composting is a biological manufacturing process that involves taking in materials, in some cases preprocessing, then mixing, composting, curing, screening, recycling overs and product storage. As this process can take anywhere from 50 to 120 days to complete, holding all that material for periods of time involves taking up space. How much space will be needed for processing? What about for other things like storm water management and equipment maintenance? A footprint analysis is an initial step in answering those questions. This article offers the author’s insights into how to figure out space needs. Information presented is based on a proposed 17,000 lbs./week aerated static pile (ASP) composting facility the author is designing in Roanoke, Virginia.
Excel spreadsheets are used to do footprint analyses. Excel is an excellent tool for organizing mathematical computations but it implies a degree of precision and accuracy that doesn’t apply to composting. “There is no such thing as a decimal point in composting,” I recall hearing in one of the first compost operator training classes I attended. Another trap to avoid is being too conservative in allocating space in order to acquire less land (and save some money). No composter has ever been heard to say, “I wish I had a smaller site.”
A footprint analysis requires that the mass-based composting recipe for your desired feedstocks has been created and that bulk density data (the weight of something per unit of volume) is known. For the proposed Roanoke facility, the food waste plus carbon amendments will require handling about 17 cubic yards (CY) per day, or about 1,820 tons/year for a facility open 5 days/week (e.g. 260 days/year).
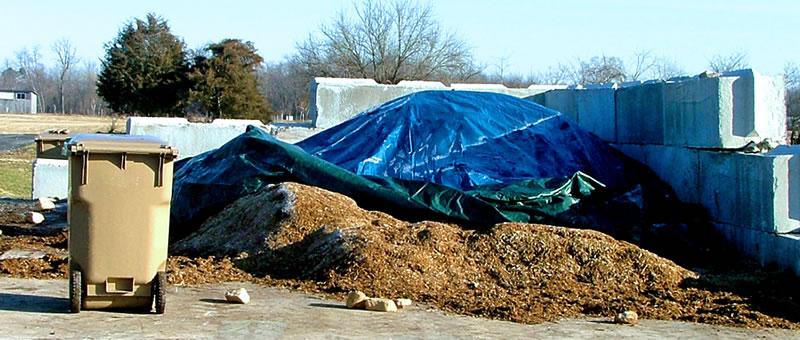
The second step in calculating a facility footprint is space for storage of feedstock such as wood chips (above). Photo by Craig Coker
Materials Flow
The first step is to estimate material flows through the facility. This requires assumptions about residence times in composting and curing, percentage volume reduction in each stage of manufacturing, and screen fines yield versus overs, as shown below:
Assumptions about volume shrinkage in composting (and, by reference, screen yields vs. overs) are based on expected particle size of the carbon amendments. In this example, we are planning to obtain arborist tree chippings from utility line maintenance contractors. Getting an 80% screen yield depends both on particle size and dryness; a moisture content of 40% in the cured compost going to screening is expected.
Sizing The Steps
Let’s start sizing each step in the manufacturing process.
1. Feedstock Receipt
For the proposed Roanoke facility, we are assuming food waste will be delivered daily and that arborist’s chips will come in weekly. We plan on sizing the receiving area for 1.5 times the average weekly volume to account for surges, such as pumpkins following Halloween. Other assumptions include a feedstock storage pile height of 8 feet and an additional 50% space allocation for materials handling. For proposed dimensions of the waste receipt area, the calculation is based on the square root of the projected area, but this will be modified in final design to reflect actual site conditions and the linear layout of the facility.
2. Feedstock Storage
The next step in the process is the space needed for storing feedstocks. For this proposed facility, we plan on short-term storage of carbon amendments in rectangular “eco-block” bunkers, although many may choose to just store them outside in trapezoidal windrow piles. Other assumptions include a storage period of 14 days and assumed material storage depth of 8 feet. For the food wastes, we plan a similar “eco-block” bunker but for only three days’ storage capacity. Note that many states do not allow overnight storage of food waste feedstocks at composting facilities, but some form of short-term storage is advisable to buffer between incoming deliveries and staff mixing and emplacing food wastes in ASP piles or in windrows. For this proposed facility, insofar as the calculation suggests a food waste storage area need of 43 square feet, we are thinking of using a 10-CY roll-off dumpster covered by a tarp for short-term storage.
3. Mixing Feedstocks
For mixing feedstocks together prior to composting, the plan is to blend with the bucket on the tractor using a portion of the waste receipt area concrete pad. If you plan to use a mechanical mixer, use the dimensions on the vendor’s website, and add 15 ft. to 20 ft. on all sides for equipment movement. Mechanical mixers should be sized based on hopper capacity and assume a 15-minute mix cycle. So, for our proposed 17 CY/day mix requirement, we could use a mixer with a 60 cubic-foot hopper and run 9 to 10 mix cycles/day.
4. Active Composting
The active composting phase at the proposed Roanoke facility will be done in aerated compost bins made out of timbers. Assumptions that went into the footprint analysis include: a 28-day (4-week) residence time, loading one ASP every three days, assumed pile height of 6 feet (not counting the 6 to 8-inch compost biolayer over each ASP), and assumed bin width of 6 feet. For the aeration system, the assumed air flow rate was 500 cubic feet/hour/dry ton (Haug, 1993) of bin contents. Another unit of aeration demand is 5 cubic feet per minute (cfm) per cubic yard of mixed compostables in the bin.
5. Curing
Curing (maturation) will be done in bucket-turned windrows. Assumptions that went into the footprint analysis for curing included: windrow dimensions as defined by the Field Guide to On-Farm Composting (NRAES, 1999), 6-ft. high by 12-ft. wide x 125-ft. long windrows, 20 ft. spacing between windrows and 15 ft. turning radius at the end of each windrow.
6. Screening And Storage
The final step in the footprint analysis is product screening and product storage. Assumptions used in this footprint analysis included: a rotating drum (trommel) screen with a 3/8-inch screen mesh, an 80% product yield, a 25-foot space around the screen for equipment access, 3 months winter product storage capacity, and 8-ft. high x 16-ft. wide storage piles. The formula to calculate the volume of a trapezoidal storage pile is in the curing table (above).
Final Total
To sum it all up, this proposed facility will need about 0.5 acre for processing. Plan on another 25% or so for other functions, e.g. access roads, internal equipment paths, equipment storage, etc. In the case of the Roanoke project, a storm water pond is not needed as the site is in an industrial park with its own pond.
Craig Coker is a Senior Editor at BioCycle CONNECT and a Principal in the firm Coker Composting & Consulting, near Roanoke VA. He can be reached at ccoker@cokercompost.com.