Top: Staging the application of Agromin compost on farm fields.
Nora Goldstein
In 2021, Oxnard, California-based Agromin composted and marketed over one million tons of organics. The company, founded over 30 years ago, maintains and manages an infrastructure of 21 processing and composting facilities throughout California. “We got our start by trimming trees for utility companies and then trying to figure out what to do with the trimmings,” recalls Bill Camarillo, Agromin’s CEO. “That quandary became the nucleus of an idea about green waste recycling and the birth of Agromin as a manufacturer of soil products for farms, government sites, major sports arenas, public and private landscapes, and home gardens. We have a client base of over 200 California communities and market compost and mulch in 16 counties.”
On January 1, 2022, compliance with California’s sweeping climate change law related to organic wastes (SB 1383) went into effect. The law, administered and enforced by CalRecycle, requires the reduction of organic waste disposal by 75% by 2025. Additionally, at least 20% of currently disposed surplus food must be rescued for people to eat by 2025. All jurisdictions need to provide organic waste collection services to all residents and businesses and recycle these organic materials via anaerobic digestion facilities that create biofuel (e.g., renewable natural gas (RNG)) and electricity or composting facilities that make soil amendments. SB 1383 also requires local governments to use the products made from recycled organics, including renewable energy, compost, and mulch.
“Agromin is poised to increase its organic waste processing capacity considerably in 2022 to help cities, counties and other jurisdictions throughout California meet the organic waste mandates,” says Camarillo. “We expect to have three new facilities by the end of the year, which expands our service area from San Diego County in southern California, up along the coast and through the Central Valley to Sacramento. Four of our composting facilities also process residential and commercial food waste with green waste — one in Ventura County and three in the Inland Empire. Of the one million tons we composted last year at all of our facilities, about 85% was green and wood waste materials and 15% was food waste. Programs are just getting started in jurisdictions to collect food waste.”
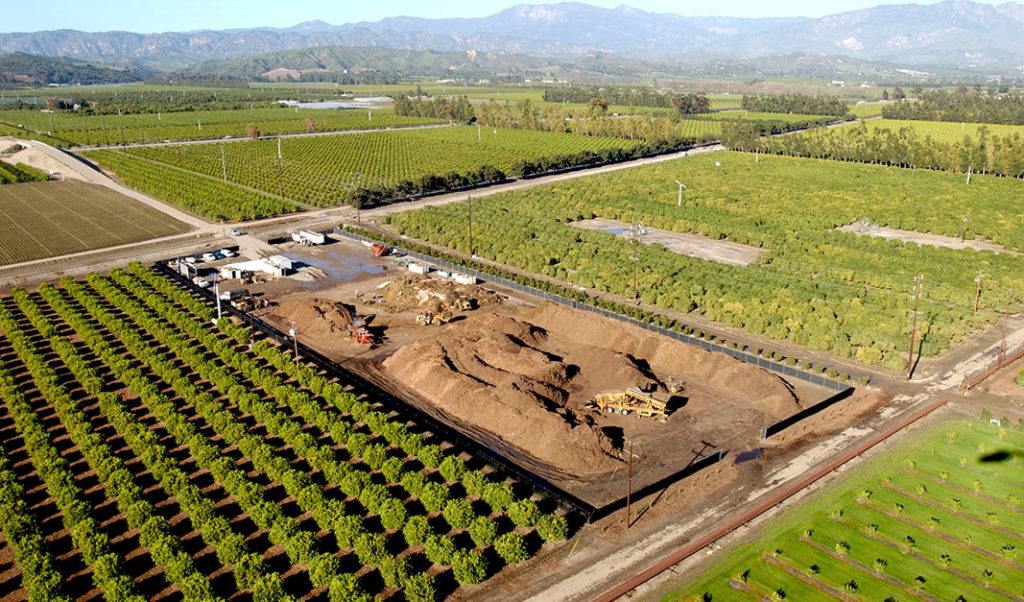
Agromin maintains and manages an infrastructure of 21 processing and composting facilities throughout California, including this site in Limoneira. Photos courtesy of Agromin
The company is venturing into new territory with the opening of a 300 tons/day food waste to animal feed and fertilizer project in Oxnard. Both pre and postconsumer food waste streams will be processed, although Agromin is building the facility primarily for commercial and multifamily streams. “The system is almost fully automated,” explains Camarillo. “Incoming organics go into a stainless steel hopper with augers, followed by a bag breaker, press and multiple screening combinations — all to remove contamination. The facility can handle up to 40% contamination in the incoming material. After contamination is removed, food waste is made into a mash that is rendered. We worked with CP Group for the processing line, and S.A.F.E. (Sustainable Alternative Feed Enterprises, Inc.) for the animal feed production equipment.” He adds that Agromin has been collaborating with one of the largest animal feed manufacturers in the state. Sale of the feed is limited to chickens, pigs, dogs and cats, but no cows (ruminants).
Another market being targeted for the processed food waste is organic fertilizer. “Fertilizer prices have quadrupled, so that is the highest value market right now for our end product from the Oxnard facility,” he notes. “We decant the fats, oils and grease out of the material and sell that separately. Remaining material is dehydrated and then can be sold as fertilizer. A third end market is RNG, where our end product is fed into a digester and the biogas is upgraded into RNG. Once we make the raw material, the market will dictate where it goes.”
Bigger Isn’t Better
When it comes to composting facility design and scale, Agromin has learned that bigger isn’t always better. “You have to understand the community needs and customize the facility to meet market demands,” says Camarillo. “It has nothing to do with the right technology, and everything to do with what is right for the community, feedstock generation, and end market availability. The Achilles heel in composting is transportation cost, so end markets have to be within a reasonable distance.”
Agromin has never entered into the collection end of organics recycling, preferring to partner with waste haulers throughout the state as service providers. It also is “technology agnostic” when it comes to composting systems, having “tried just about everything.” Ultimately, he notes, economics drive the technology along with the regulatory requirements.
The lion’s share of Agromin’s end products — 80% by volume — is sold to agricultural markets. The other 20%, by volume, goes to the landscape and retail markets. By economic value, however, it is more of a 60:40 split (agricultural to landscape and retail). The company, like so many compost manufacturers, still makes the bulk of its revenue on tipping fees. “However, we do see a future of a demand pull, where the market will be pulling the product through the system,” explains Camarillo. “We will get there due to water challenges, the high cost of chemical fertilizers, and carbon credits. Globally, companies are being pressured to be carbon neutral, and you can’t get there without tangible solutions.”
New Business Opportunity
Article 12 of SB 1383 states that “a jurisdiction shall annually procure a quantity of recovered organic waste products that meets or exceeds its current annual recovered organic waste product procurement target as determined by this article. For the purposes of this section, ‘jurisdiction’ means a city, a county or a city and county. … Each jurisdiction’s recovered organic waste product procurement target shall be calculated by multiplying the per capita procurement target by the jurisdiction population where … per capita procurement target = 0.08 tons of organic waste per California resident per year.” For example, a jurisdiction with 100,000 residents is required to reuse 8,000 tons of recovered organic waste annually.
To assist jurisdictions with Article 12 compliance, Agromin created California Compost, an online service that facilitates procurement, recordkeeping, and marketing of recycled organics end products. Notes the website, “California Compost helps you assess your specific needs and tailors a custom compost and mulch procurement plan for compliance.” Factors assessed for a jurisdiction include current recycling and reclamation protocols, population factors and geographical footprint, breakdown of incorporated parks, greenbelts, playing fields, medians, school grounds, etc., compost and mulch application review for maximum water savings, and infrastructure readiness.
“Once the assessment is complete, California Compost prepares a jurisdiction’s specific Article 12 solution,” explains Camarillo. “We integrate with your existing procurement process so your organization can comply with state law while sustainably improving and beautifying its outdoor green spaces. For example, if you enter the City of Ventura into our online calculator, the initial assessment profile shows required procurement of 4,891 tons of compost, 8,433 tons of mulch, 5.5 million kWh of electricity and 177,097 DGE (diesel gallon equivalents) of RNG. Any combination of those is allowed, and CalRecycle has an Xcel workbook to enter the materials purchased to meet Article 12 requirements. A jurisdiction can purchase 50% compost and 50% mulch to be in compliance.”
Jurisdictions are not required to procure recovered organic waste products made from their organic waste to satisfy the procurement requirements, nor do the products need to be produced or consumed within their jurisdiction, according to CalRecycle. They may purchase or acquire products from any entity, or produce it themselves, and use or giveaway these products to count toward their procurement targets, provided the end products meet the definition of “recovered organic waste products.” An additional service offered by California Compost is sourcing recycled organics from elsewhere if they are not available in a specific jurisdiction. “We will help them find the compost to comply,” adds Camarillo.