A study for the Deer Island treatment plant in Boston Harbor evaluated the feasibility of codigestion, and whether the economic benefits outweigh the costs.
David L. Parry
BioCycle January 2014
Beginning in 1990, the Massachusetts Department of Environmental Protection (MassDEP) banned the disposal of various materials in landfills and waste incinerators, such as yard trimmings, whole tires and electronics. Recently, the agency announced plans to ban source separated commercial organics, with the goal of diverting an additional 1,000 tons/day of SSO by 2020. These materials typically include food waste from supermarkets, institutions, food producers and other large generators. MassDEP expects the ban on disposal of SSO to be in effect by July 1, 2014. Initially the ban will only impact generators of more than one wet ton/week of organic wastes.
MWRA’s residuals processing facilities consist of thickening, digestion and biogas utilization at Deer Island, and dewatering and thermal drying at the biosolids processing facility (BPF) in Quincy, Massachusetts. DITP has twelve, 3-million-gallon mesophilic anaerobic digesters. The egg-shaped digesters have a 90-foot diameter in the middle and a liquid depth of 128 feet. Digested sludge overflows from the digesters to two 3-million-gallon sludge/biogas storage tanks. From the storage tanks, the digested sludge is pumped to the BPF through one of two parallel 14-inch diameter 7-mile-long force mains under Boston Harbor.
At the BPF, the digested sludge is stored in four one-million-gallon storage tanks, then pumped to centrifuges for dewatering. It is then conveyed to the thermal drying portion of the facility and mixed with recycled dried sludge before being fed into the rotary drum dryers. The dried product is screened to produce a pellet. Approximately 75 percent of the product is sold to agricultural users; the balance is utilized in a cement kiln as a coal substitute. A small percentage of the pellets are bagged and sold locally as a fertilizer product. The BPF is operated by the New England Fertilizer Company.
With a 62 percent volatile solids reduction, the anaerobic digesters at Deer Island produce on average approximately 190,000 cubic feet of biogas per hour (cf/h). The biogas is burned in boilers that produce high temperature, high pressure steam that heats high temperature, low pressure water. The hot water is utilized for plant and digester heating, and the remaining steam is used to produce electricity in two steam turbine generators. Approximately 98 percent of the annual heating demands on site are met with the biogas, saving $15-to-$20 million/year in heating costs. Another $2-to-$3 million/year in savings is achieved in electrical production and green energy credits.
Advantages Of Codigestion
More biogas will be produced as a result of the increased food waste load. The beneficial use of the increased biogas will save energy, but the “downstream impacts” of more biosolids and centrate will increase operational costs. The food waste is expected to have an average concentration of 13 percent. It will be blended with the combined primary and secondary sludge at about 5 percent solids for a mixture of 6 to 7 percent solids before feeding to the digesters.
Based on studies conducted by CDM Smith for the Water Environment Research Foundation, the performance of anaerobic digestion is improved when primary and secondary sludge is codigested with food wastes. When food waste is digested separately, a shortage of micronutrients has been observed (see “Codigestion Research Builds Facility Operator Confidence,” Part II, May 2013). However, wastewater sludge provides sufficient micronutrients as well as significant alkalinity to buffer varying organic loads. Feeding a digester both food wastes and wastewater sludge results in stable digester performance and increased volatile solids conversion. Food wastes can have a higher carbon:nitrogen (C: N) ratio than wastewater sludge, which can improve the carbon content of the mixed wastes.
The increase in biogas production can be significant from codigestion of food waste. The increase is greater than the increase in heat demand of the food waste. With this increased biogas production there is an opportunity to focus on power generation first and heat second. As a result, the additional biogas can be fed to an internal combustion (IC) engine or gas-turbine generator instead of the existing steam plant. This kind of combined heat and power (CHP) system can have an electrical efficiency of 38 percent — significantly greater than the electrical efficiency of the existing Rankine steam system in use. Additionally, heat can be recovered from the IC engines or gas turbines. The current electrical efficiency of Deer Island’s Rankine system is approximately only 9 percent.
The value of biogas can be viewed as the difference between the value of the heat and electricity produced minus the cost of generation. The cost of generation includes capital recovery and operation and maintenance of the cogeneration equipment and of the biogas treatment. A new CHP could be designed to operate in conjunction with the existing energy system. For the purposes of evaluating costs in the report, it was assumed that the existing power plant would utilize the biogas generated from the wastewater solids as it does now. This means that all of the DITP thermal needs, as well as some of its electrical needs, would be satisfied by existing facilities. In the economic analysis only the incremental biogas associated with full-scale codigestion of food waste would be fed to the new CHP facilities.
Economic Benefits And Costs
A range of potential quantities of food waste were examined to fully understand the economic benefits and costs of codigestion. The range was 150 to 500 tons/day. It was assumed that these wastes would be collected and preprocessed at an off-site location by the private sector and transported to the DITP. The economic analysis did not include these preprocessing and transport costs. Table 1 shows the amount of additional biogas that would be produced from the incremental increase from codigestion of food waste. The table also shows the equivalent electricity produced by utilizing the additional biogas.
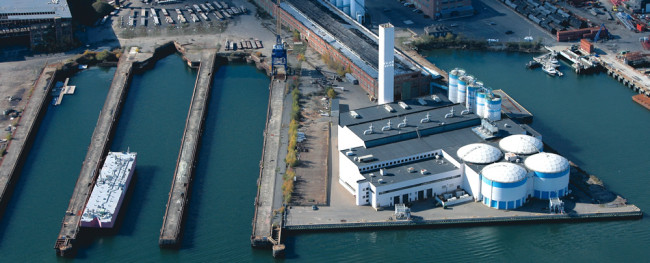
Digested sludge flows over to two sludge/biogas storage tanks, then is pumped to the Biosolids Processing Facility in Quincy where it is dewatered and then thermally dried.
The analysis determined that the monetary benefits from additional biogas production at the DITP are exceeded by the costs for MWRA to process the food waste. Table 2 presents a brief summary of annual costs for the range of food waste considered in the report and an estimate of a “tipping fee” that would be charged to treat these wastes.
The first line shows the monetary value of the additional biogas produced by adding food waste to the DITP digesters. The annual processing costs shown on the second line include all processing costs plus the amortized value of capital costs associated with these operations. The third line shows the amount that MWRA would have to charge private firms that deliver food waste to the DITP to “break even.” The last line in the table shows the tipping fee expressed on a unit cost basis: approximately $9/wet ton or $0.04/gallon of food waste received. These unit costs are in line with fees charged at other facilities.
Based in part on the findings of the CDM Smith codigestion study, MWRA is proceeding with a codigestion pilot program at the DITP. Starting in mid-2014, preprocessed, source separated organics will be transported to DITP, mixed with thickened sludge and fed to existing digesters. Initially, approximately 50 wtpd of the organics will be fed to a single digester. Over time, the quantities will increase to approximately 150 wtpd and two digesters will be utilized. MWRA plans to carefully monitor pilot and control digesters for both normal process parameters and biogas composition and volume. Based on the results of the pilot program, which could have a duration of one to three years, MWRA may increase the volume of source separated organic received at DITP.
David Parry, PhD, PE, BCEE, is a senior vice president with CDM Smith.
Acknowledgements
The basis of the codigestion study is a report for the Massachusetts Water Resources Authority entitled “Assessing Options for Residuals Management.” The principal authors of the report are John F. Donovan PE, BCEE, and Eric M. Spargimino, PE LEED AP, of CDM Smith. The project was overseen by Daniel R. O’Brien, PE, director of the Deer Island Plant and David F. Duest, manager, process control, both with the Massachusetts Water Resource Authority.