How citizens of Missoula, Montana worked with the local health department, consultants and the local treatment plant and composting facility to address nuisance odors.
Katrina Mendrey
BioCycle June 2014
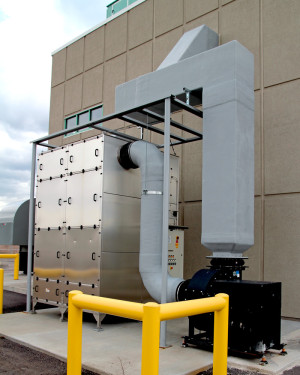
The Missoula wastewater treatment plant installed a photoionization system that uses UV light and carbon filters to treat the air coming from the plant’s headworks and thickened waste activator systems.
Putrid. Barnyard. Dead animal. Outhouse. Within days of moving into her dream home in April 2005, Laura Hall began smelling the foul odors. “It was very distressing because I had no control over it,” recalls Hall. The odors she remembers came nearly every evening, especially in the summer.
Hall and her neighbors in Missoula, Montana couldn’t be sure where the odors were coming from but they suspected the source was the wastewater treatment plant and biosolids composting facility. The facilities were located adjacent to each other across the Clark Fork River approximately a mile away. Matters were complicated by the presence of an animal mortality transfer station and bacon factory located nearby as well.
But in April 2006 complaints started pouring in to the Missoula City-County Health Department (MCCHD) and the City of Missoula Wastewater Treatment Plant. The animal mortality business had long moved elsewhere and it was clear something was amiss. Further development in the area had long ago surrounded the plant and the associated composting facility operated by EKO Compost, but complaints had never been that high.
“It was daily,” notes Starr Sullivan, Missoula’s Wastewater Treatment Superintendent. “Prior to that we would get three or four calls a summer usually from people very close by. But at the peak of things in 2006 we’d get that many daily.”
Odor Characterization Study
In 2008 odors were still persisting and MCCHD eventually sent a Notice of Violation and Order to Take Corrective Action to the City of Missoula requiring that the City, in partnership with EKO Compost, complete an odor characterization study. “The only way to start moving toward a resolution is to have an outside agency make an objective assessment,” says Benjamin Schmidt, Air Quality Specialist at MCCHD.
The comprehensive study was managed by Morrison-Mairele, a Montana-based consulting engineering firm, with technical odor assistance from Bowker and Associates, Inc. in Portland, Maine. Commencing in May 2009, the study included a 20-week community-led survey in which citizen volunteers monitored and recorded odors; a survey of similar length conducted by a trained city staff member who monitored two routes encompassing a one-mile radius of the facilities using a Nasal Ranger and odor wheel; and a three day sampling at both EKO Compost and the wastewater treatment facility during a peak odor period in late July 2009.
“The whole exercise was very practical in terms of identifying what the odor sources were,” says Scott Murphy, Project Manager at Morrison-Mairele. The study determined that the wastewater treatment plant was responsible for 53 percent of odors and EKO Compost was responsible for 47 percent. The odor samples collected at the facilities clearly identified sources of the problem that could be addressed by facility upgrades and operational changes.
Odor Controls
At the wastewater treatment facility, the primary odor sources were the headworks and the thickened waste activated sludge (TWAS) tank. Over 90 percent of odors were attributed to these sources. According to Sullivan, upgrades to the headworks were already in the plans, but the results of the odor study led to some revisions, including additional odor controls. Due to low temperatures in Montana and limited space at the plant, a photoionization system using UV light and carbon filters made by Ambio Biofiltration, Ltd., was chosen to filter air coming from the headworks and TWAS tank.
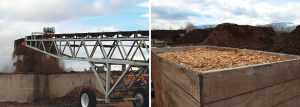
A conveyor belt (left) was installed to transfer dewatered biosolids directly from the treatment plant to the adjacent composting site — which was required to install a biofilter system (right).
Photos by Katrina Mendrey
“I’m pretty conservative when it comes to new technology,” explains Sullivan. “But we piloted it for a year and did the nose test. And the results were remarkable.” He adds this was the first time the system, which originates in Germany, had been used at a wastewater treatment facility in the U.S. The new headworks cost $9.7 million and the odor control upgrades came to around $500,000, according to Sullivan. The facility with these upgrades is designed to treat 12 million gallons day on annual average. Currently approximately 7.5 million gallons are treated.
For EKO Compost, changes were more operational, reports Phil Oakenshield, EKO Compost Plant Manager. Odor sources were attributed to piles of biosolids that were not being composted quickly enough or with adequate bulking agent. Oakenshield estimates the facility receives 29,000 tons of biosolids annually. Previously biosolids were delivered by truck, however because the facilities are directly next to each other, a conveyor belt was installed to transfer dewatered biosolids consisting of approximately 18 percent solids directly from the treatment plant to the EKO Compost site. Once delivered, bulking agent, mostly shredded yard trimmings, is mixed in and biosolids are moved with a front-end loader to aerated static piles.
EKO Compost was required to install a biofilter system as a result of findings from the study. The biofilter is in a plywood box measuring 4-ft by 4-ft by 8-ft; it consists of 4-inch perforated PVC pipe that is covered with approximately 3-feet of straw, followed by 6-inches of charcoal and a thin layer of screened reject material. One biofilter receives air from approximately three aerated piles.
While identifying sources of the odors was central to the study, community involvement was invaluable as well. “In my experience unless you do a lot of community surveys it’s hard to simulate living there,” explains Bob Bowker, owner of Bowker and Associates, Inc. “So that’s why it was good to get input from the neighborhoods. I’ve also seen a lot of people be turned around from an enemy of the city by efforts like this.”
Hall agrees. She was recruited by Schmidt to participate in the citizen volunteer survey. Other volunteers were recruited via mailings to areas with historically high odor complaints. According to Schmidt, around a dozen citizen volunteers submitted complete data sets and ran monitoring equipment for the study.
For her role in the survey, Hall kept a log of when she noticed odors, what she smelled, the intensity of the smell and weather conditions at the time. These were matched to data collected by a weather station at the treatment plant. She also was given a filter that was kept on her front porch and used to collect odor samples. “It felt empowering, like I was doing something to help my neighbors and make a change,” says Hall of helping with the survey. One challenge she had was in describing the smell. While odor wheels that provide descriptions of the smells were used to train some volunteers, Hall does not recall receiving one, “It would have been nice to have a vocabulary.”
But over five years later, Hall doesn’t think it’s necessary anymore. “Things started improving after just a year and now the smells are only occasional,” she notes. “Just a whiff. I’m pleased. Very pleased.”
Katrina Mendrey is a Contributing Editor to BioCycle.