Top: The Compost Company utilizes extended aerated static piles, covered with a blanket of finished compost, to process food scraps, carbonaceous feedstocks, and compostable products.
Nora Goldstein
In 2011, Edward Wansing launched The Compost Company in Ashland City, Tennessee, the first organics recycler in the mid-state region around Nashville. Wansing, who grew up on a farm and pursued a career in sustainable architecture, saw a need for recycling of organic waste in the growing Nashville area. “Before I started the company, I spent a number of months talking to area waste haulers and recyclers to gauge local interest,” he told BioCycle in a 2015 article. The facility, located on a 37-acre site, started out composting yard trimmings, wood chips and landclearing debris, and then began taking in preconsumer produce waste.
After a couple years, Wansing began a hauling service, enabling The Compost Company to expand into new areas in the region, as well as new food waste streams. “We are becoming more independent of the larger waste haulers, to better control our supply of incoming feedstock,” he added in the 2015 article. Clients being serviced once collection was launched included the Music City Center convention facility, Nashville office buildings, food processors, and hotels and conference centers that host events producing large amounts of postconsumer food and paper packaging and serving waste, as well as compostable bioplastic serviceware.
Ten years in, The Compost Company has a 25-cubic yard collection truck (it originally started with a Dodge Ram pickup with a dump trailer), as well as accepts food scraps from other haulers that also use compostable liners and accept compostable products. The facility processes about 2,800 tons/year of food scraps along with 4,200 tons/year of yard trimmings and other carbon feedstocks. Clay Ezell, co-owner and Collection and Business Development director, joined the company in 2015. In 2017, a shift was made from windrows to extended aerated static pile composting to improve process controls and optimize utilization of space on the composting pad.
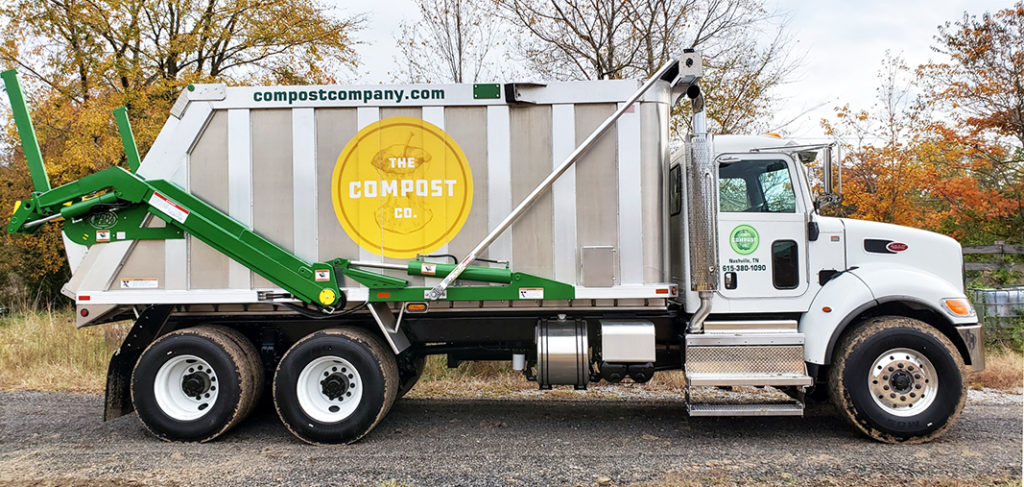
A 25-cubic yard collection vehicle is used to service commercial and institutional accounts. Photos courtesy of The Compost Company
Roughly 40% of the food waste received comes from generators that include BPI-certified compostable products, including liner bags (from back- and front-of-house) and foodservice ware from the front-of-house. “Our willingness to accept compostable products is the reason why some of our largest customers have signed up for collection service,” notes Wansing. “Therefore we would not be able to go ‘food only’ without losing customers.”
The Compost Company is among the compost manufacturers surveyed and interviewed by BioCycle Associates to inform a Decision-Making Guide on acceptance of compostable products being developed for the US Composting Council (USCC). Wansing will be a panelist at the USCC’s Compostable Products Summit on July 15, where a beta-version of the Decision-Making Guide will be presented. This article delves into The Compost Company’s strategies to accept and successfully manage certified compostable products.
Servicing Food Scraps Generators
Compostable products accepted by The Compost Company must meet ASTM D6400 and D6868 standards and be certified by the Biodegradable Products Institute (BPI). In addition to bioplastic and Kraft paper liner bags, the full suite of compostable foodservice ware is accepted, including soiled paper; fiber bowls, plates, carryout containers and wooden-only utensils; and bioplastic cups, paper cups with bioplastic lining, utensils, plates, carryout containers and portion cups. The Compost Company can supply customers with liner bags, or they can procure their own.
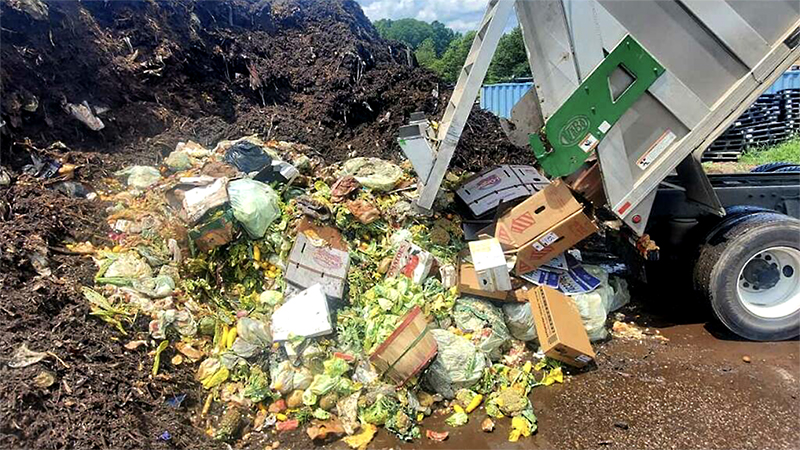
Example of a truckload arriving at The Compost Company includes compostable liner bags.
“Liner bags make everything so much easier,” explains Wansing. “There was a time when the carts were unlined and when customers could empty the food scraps directly into the dumpster. That makes it so much harder to clean the dumpsters. Our truck is equipped with a high-pressure spray washer, and without the liners, cleaning took a lot of time at each stop. With liner bags, we empty the carts and rinse them quickly. It’s faster and cleaner.” Foodservice staff also prefer using liners so the bins are not coming back into the kitchen soiled after being emptied.
Wansing and Ezell see a correlation between the increase in food scraps The Compost Company receives and acceptance of compostable packaging. “It is an incentive to source separate their food scraps, especially when they want to include the front-of-house (FOH) stream,” says Wansing, “With food service establishments, we actually get more food scraps from the FOH versus the back-of-house (BOH), because kitchen staff are trying to waste as little food as possible. For us, postconsumer generates a lot more material, which is due in large part to the inclusion of compostable products. Our clients’ customers are more confident when they can throw everything into one bin so they don’t have to determine what goes where.”
He adds that using all compostables in FOH operations reduces contamination. “When a set up is half compostable products and half single-use disposable, we see a lot more contamination. Not only does it ease decision making on the part of the customer, it eases processing at the facility in terms of sorting.”
The Compost Company still gets contamination in the collected food scraps. Its contracts with customers spell out what is accepted, cart and load rejection policies, and fees that might be levied in the event of contamination. “We want to make sure that they’re not surprised if/when contamination necessitates an upcharge,” notes Ezell. He and Wansing have not seen that acceptance of compostable foodservice ware increases contamination in the food scraps stream from noncompostable lookalikes. “Most of the contamination that we see is due to staff not caring about keeping the contamination out of the bins,” says Wansing. “If we stopped allowing compostable foodservice products we would still have contamination.”
Some compost manufacturers have noted that when taking FOH streams, especially from quick-serve restaurants, they end up with loads that are primarily packaging and little food waste. This can be a disincentive to acceptance of compostable products. “We do have some loads that are a mix of more compostable and paper products than food waste, but it is not frequent enough that it causes a problem,” he adds. “If we had many loads that were more compostable products and paper than food, I can see how it would be an issue.”
Preprocessing And Composting
Initially, a mixer was used to open bags of food scraps and blend in carbonaceous materials, however not all the bags were breaking open. The Compost Company had replaced its original tub grinder with a Rotochopper FP66 horizontal grinder for wood waste and yard trimmings processing because it is better able to handle wet material. It decided to use the Rotochopper to break open the bags and blend the food scraps with the carbon source. “We grind to open the bags about once or twice a week and between those times, mix together carbon with the food waste using a loader, then cover it with more carbon,” explains Wansing. “We run a 6-inch and an 8-inch screen in the grinder when we are grinding the food scraps. We don’t want to grind the feedstock down so small that it inhibits proper airflow in the extended aerated static pile (EASP). This screen combination sufficiently shreds the compostable bags and serviceware to create a homogenous mix without negatively impacting bulk density in the EASP.”
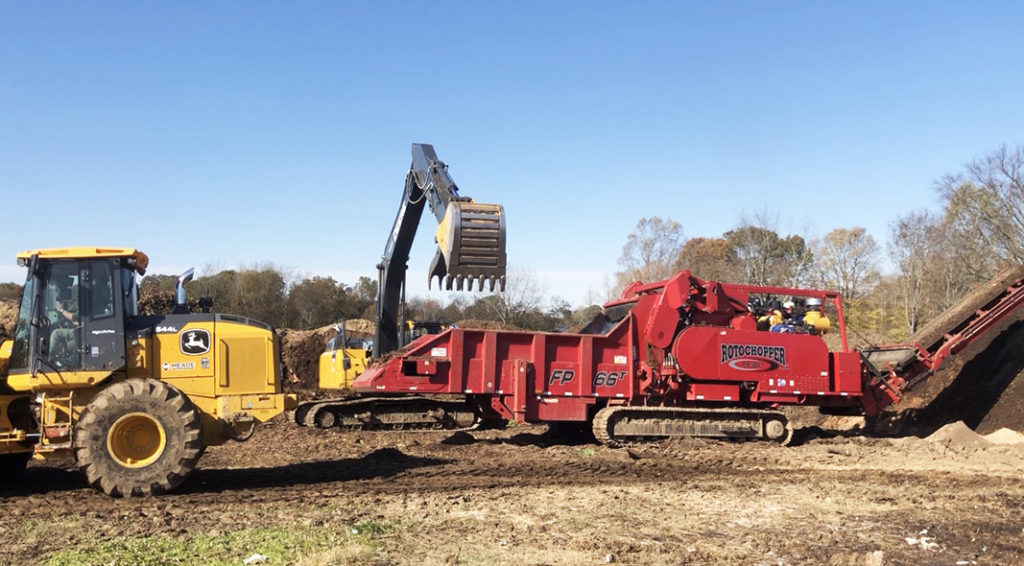
After starting out with a tub grinder, The Compost Company switched to a FP66 Rotochopper horizontal grinder that is better equipped to process wet materials.
He notes that the infeed belt design on the FP66 works well for the wet feedstock, and changing the screens to process different materials is quick and simple. The control system monitors engine load and varies the infeed rate according to parameters set through the control panel for a certain feedstock.
Obvious contamination is hand picked out of the food scraps before and after grinding. Food scraps containing compostable products are composted separately from piles that are yard trimmings only. The separate composting line for yard trimmings is necessary because organic farmers are part of The Compost Company’s end markets and cannot utilize compost that contains bioplastics.
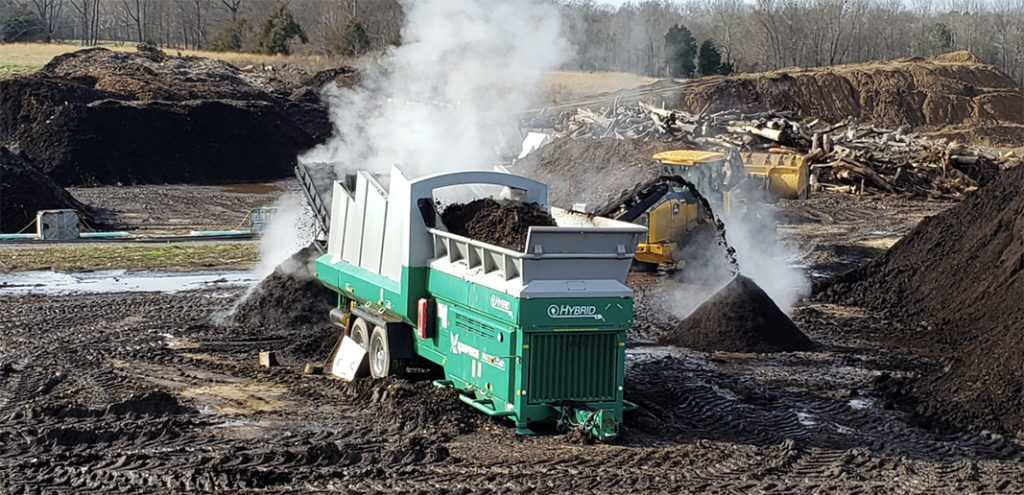
Compost is screened after the active composting phase and again after curing using a Komptech M2 Starscreen.
The active composting phase is 30 to 35 days, with the temperature averaging about 140°F. The piles are capped with a 12-inch layer of finished compost to help control odors and retain moisture. Material is screened before going into the curing phase using a Komptech M2 star screen equipped with variable frequency drives that control the speed. Operators slow the speed down (by reducing the rotations/minute (RPMs) on the drives) to retain the coarser material that aids in aeration during curing. The star screen is paired with a wind sifter that removes film plastic. “We do have quite a bit of contamination from hard plastics and noncompostable film that we didn’t catch on the front-end,” says Wansing.
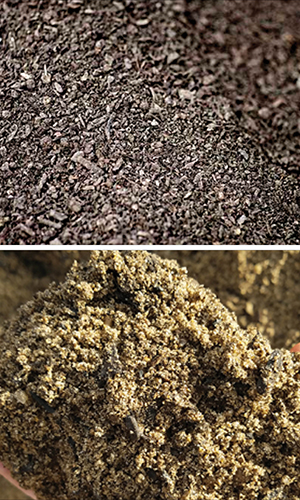
Garden planter blend (top) and bioretention blend (bottom)
Compost is cured for up to six months, then is processed through the Komptech star screen. The RPMs are ramped up to screen the compost to finished particle size. Increasing the speed pushes the material through the screen faster, allowing less material to pass through the stars; small particles fall through first. Up to 98% of material passes through a three-eighth-inch screen and 90% passes through a quarter-inch screen. The site also has a trommel screen. Finished compost may remain at the facility for up to a year, depending on the season. The Compost Company makes a variety of mixes with its compost, including a garden planter blend and a bioretention blend. It utilizes a Rotochopper Go-Bagger 250 to bag compost and a potting soil mix.
Compostable Product Disintegration
The ability to create an optimum mix of food scraps and carbon via grinding and modifying materials handling and composting practices contribute to successful disintegration of compostable products at The Compost Company’s facility. The EASPs usually meet the required PFRP (process to further reduce pathogens) temperature of >130°F for three consecutive days about three to four days into the composting process, notes Wansing. “Typically the piles reach 140° to 150°F and remain there for about 10 days, which may aid in disintegration. For other compost manufacturers that are not getting disintegration, the question may be how quickly the pile is being cooled.”
Compostable products completely disintegrate after the active and curing composting phases. Some are completely disintegrated after the active phase. “We don’t ever see any forks and knives, and rarely see any clam shells or cups after the initial screening,” he adds. “We do see — about 99% of the time — noncompostable products after the initial screening. For example, the base of a disposable cup will be intact and the sides slivered. Every once in a while, we will see a small fragment of a compostable liner bag. What we did learn early on when we tested compostable liner bags is that grinding rips them up enough and breaks them apart to facilitate disintegration. But if they were tied off in a big knot, the knot did not disintegrate.”
The facility had been recycling screened overs back into the active composting phase, but contamination from noncompostable plastics, especially small hard plastic bits, was too high. The Compost Company has been evaluating use of a depackager to remove this type of contamination but is aware that running all food scraps through depackaging would also remove the compostable products. “If we install depack equipment we might reserve that for the exclusive use of the heavily packaged, palletized food goods while running the pre and postconsumer materials as we currently do, and letting the two meet at the time of blending for grinding and EASP composting,” explains Ezell.