Fabric buildings are employed in the organics recycling industry for feedstock receiving and mixing, compost storage and blending, and most recently, to house food waste depackaging.
Nora Goldstein
BioCycle November 2016
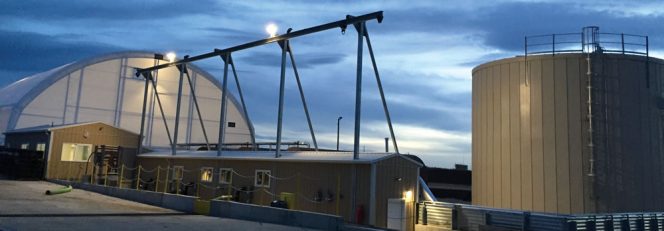
A1 Organics’ Digester Processing System, which includes DODA and Tiger depackagers, is housed in fabric structure near the digester’s feedstock storage tank (top). Photo courtesy of A1 Organics
More recently, anaerobic digestion and composting facilities have been erecting fabric structures to house depackaging and food waste preprocessing systems. Many are fully enclosed and equipped with fast closing doors to enable trucks to enter and leave. Some are designing biofilters to treat the building air. “For facilities that have purchased Ecoverse’s Tiger depackaging systems, we can provide design and specs for the building to enclose them,” explains Kish. “Most are installing concrete floors and anchoring the fabric structure on concrete walls, which can be used as push walls to help load the Tiger, which is 8-feet wide and 20-feet long. We typically create staging areas, e.g., one for unloading source separated organics that can be on the wet side, and another to store feedstocks that are on the dry side, such as cookies, cases of beverages and crates of eggs.”
A1 Organics
A1 Organics, headquartered in Eaton, Colorado, has multiple windrow composting sites and processes a range of feedstocks, including yard trimmings, source separated food waste, manures and biosolids. In 2013, A1 entered into an exclusive substrate procurement agreement with Heartland Biogas, LLC, for Heartland’s anaerobic digester project in Weld County, Colorado. A1 Organics is responsible for sourcing, processing and delivering food waste, fats, oils and grease, and other non-manure substrates to the digester facility. Currently, about 400 to 450 tons/day of food waste and related substrates are received.
When A1 signed the agreement, it already previously purchased a DODA preprocessing system to remove contaminants from source separated organics. The slurry was added to the composting windrows in a ratio of about 80 gallons to 1 cubic yard (cy) of ground yard trimmings, and mixed with a compost turner. Recognizing that it would have to expand into processing a wide range of packaged food waste streams in order to fulfill its agreement with Heartland Biogas, A1 Organics purchased a Tiger depackaging unit. To have the ability to operate the DODA and the Tiger systems year round, A1 solicited bids for a fabric structure at what it calls its Digester Processing System (DPS).
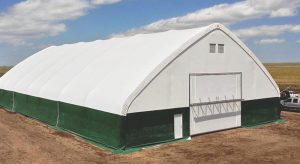
A1 Organics uses a ClearSpan Hercules Truss Arch building at its Rattler Ridge composting facility for equipment storage and Harvest Quest production. Photo courtesy of A1 Organics
A1 chose ClearSpan’s Helical Anchors to support the structure, which do not require concrete or a foundation. It did install a recycled asphalt floor to keep dust levels down in the building. “For the square and cubic footage we were able to acquire, this was a very economical option for A1,” adds Pendley. “Our total cost was about $13-$15/sq. ft., including grading, leveling and running power to it.”
The lowest bid that A1 Organics received for the DPS building was submitted by Fabristructure. The 70-foot by 70-foot structure was installed in June 2016. It sits on 6-feet high and 2-feet thick preformed concrete blocks that raise the building and give it a foundation wall. A concrete floor was laid down inside. “The quality of the concrete blocks was poor so we ended up hiring a concrete company to apply shotcrete directly on the concrete walls to seal them,” explains Bob Yost, A1 Organics’ Vice President and Chief Technical Officer. “They are basically containment walls. We try not to push on them.”
In addition to the DODA and Tiger, the building has a small receiving area for source separated organics, piping that transports the processed feedstocks to the digester’s storage tanks and a boiler room. There are two overhead doors on the south end of the building. Trucks that unload inside are the walking floor type, adds Yost. “We are currently unloading end dumps on the dump pad outside the building,” he explains. “We will be doubling the size of the Fabristructure building in November and are also planning on adding another unloading pad and then covering the unloading pads, control room, pump tram, and in-ground concrete tanks with a Legacy Building. End dumps will be unloading within that building.”
Yost adds that end dump trailers need somewhere between 35-feet to 45-feet clearance to raise the trailer to its total height. “But when dealing with SSO, they don’t need to go up that high,” he says. “The material is so wet, it spills out.” The new Legacy building, which is still being designed (final height hasn’t been determined), has a more conventional structure (versus a hoop frame), with a pitched roof covered in fabric instead of steel. A1 will have the capacity to unload any type of trailer inside.
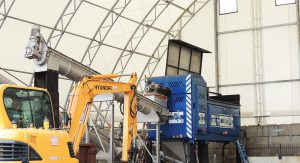
Anaerobic digestion and composting facilities have been erecting fabric structures to house depackaging and food waste preprocessing systems, such as this installation at Staten Island Composting in New York.
As for the expansion of the existing Fabristructure, adding 70-feet is pretty straightforward, he adds. “The end caps of a building like that are not load bearing, so the caps can be removed and the extension can be added very simply.”
Royal Oak Farm
Royal Oak Farm, LLC in Evington, Virginia originally purchased a fabric building to house its hog operation. “We built a 40-foot by 100-foot building with a concrete floor and 5-foot high walls for a very economical price,” recalls Ken Newman, founder of Royal Oak Farm. “The building was supplied by Coverall. We went with this type of structure because the ammonia in the hog manure would rust off the fabric cover — it doesn’t rot like sheet metal. The frame is triple-galvanized, which makes it last a very long time.”
Eventually, Newman phased out the hog raising business and got into composting, soil blending and mulch production. The facility processes yard trimmings, land clearing debris, manures and food waste (primarily from food processors). The original hog barn structure is used for product storage. A newer building, 70-feet by 100-feet and 40-feet high in the center, is Royal Oak’s commodity building. “We can get tractor trailer end dumps in there,” he notes. The company has other fabric structures on the property, used for a variety of purposes.
Maintenance on the structures is minimal. “We are supposed to go around once a year to tighten the straps, but don’t always get that done,” adds Newman. “The only problem we ever had was when a tornado flipped up one of the lean-tos on the side of the building and it ripped the fabric. Otherwise, we’ve never had to replace the covers.”